Production Supervisor Resume Samples
4.7
(89 votes) for
Production Supervisor Resume Samples
The Guide To Resume Tailoring
Guide the recruiter to the conclusion that you are the best candidate for the production supervisor job. It’s actually very simple. Tailor your resume by picking relevant responsibilities from the examples below and then add your accomplishments. This way, you can position yourself in the best way to get hired.
Craft your perfect resume by picking job responsibilities written by professional recruiters
Pick from the thousands of curated job responsibilities used by the leading companies
Tailor your resume & cover letter with wording that best fits for each job you apply
Resume Builder
Create a Resume in Minutes with Professional Resume Templates
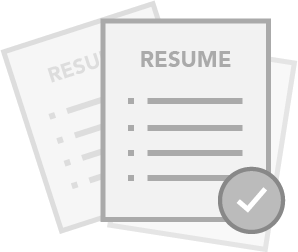
CHOOSE THE BEST TEMPLATE
- Choose from 15 Leading Templates. No need to think about design details.
USE PRE-WRITTEN BULLET POINTS
- Select from thousands of pre-written bullet points.
SAVE YOUR DOCUMENTS IN PDF FILES
- Instantly download in PDF format or share a custom link.
AH
A Hauck
Alana
Hauck
64674 Bennie Stream
Chicago
IL
+1 (555) 790 7707
64674 Bennie Stream
Chicago
IL
Phone
p
+1 (555) 790 7707
Experience
Experience
Phoenix, AZ
Production Supervisor
Phoenix, AZ
Gorczany-Lowe
Phoenix, AZ
Production Supervisor
- Coach/develop and provide feedback to employees and address their issues, to ensure true engagement within the team
- To analyze procedures and recommend/implement measures to improve production methods, equipment performance, quality of product and implement changes to increase efficiency of department or work crew
- To maintain a high level of morale and team-work on the production floor through frequent communication with employees to keep them informed of any new products and/or procedures, and to listen to employee concerns
- Provide support to PCC business for development of new business and support of on-going operations
- Plan, track, and achieve the PCC plant’s safety, environmental, quality, and productivity goals established by company management
- To evaluate employee performance against pre-established standards of performance in accordance with company policy. To provide coaching and counseling to employees which will encourage professional growth as well as meet short and long term goals
- Monitor and assure a safe work environment through process adherence and hazard elimination/mitigation(PPE, Lockout/Tag-out, Machine Guarding, etc.) and hazard elimination/mitigation
present
Dallas, TX
Production Supervisor
Dallas, TX
Ernser, Emard and Sanford
present
Dallas, TX
Production Supervisor
present
- Develop positional rotation to support continuous improvement and operator development
- Improvements- Responsible for continuous improvement for customer concerns, on time delivery through schedule attainment, quality, scrap reduction, safety and moral. Leads teams through problem solving process, documents issues and identifies solutions that prevent recurrence. Develops job breakdown and standardized work processes with team, Performs time studies of operation while developing and performing with the team work sequence, standardized work and takt time charting
- Act as liaison between 3rd party production companies and all internal departments (i.e. Business & Legal, Standards & Practices, Rights & Clearances, On-Air Design, Promos, Network, etc.)
- Performance management
- Communication- Effectively communicates performance in all aspects of the business including, but not limited to Policy, Safety, Quality, Delivery, Productivity during pre-shift meetings and team meetings
- To ensure accurate manufacturing of direct mail as specified by work orders. To ensure that all mailings are in accordance with postal regulations. To manage relationship with the Post Office and respond to postal inquiries
- Work with General Manager and Program Managers to ensure proper resources exist to support the current programs
Education
Education
Bachelor’s Degree in Engineering
Bachelor’s Degree in Engineering
Howard University
Bachelor’s Degree in Engineering
Skills
Skills
- Coordinate with quality engineer and SQE engineer to ensure manufacturing quality under good control. (Quality)
- Working knowledge of MS office products. Ability to perform alpha/numeric data entry in ERP system. Able to use internet and e-mail
- Be knowledgeable of safety, quality and productivity
- Good Manufacturing Practices: Knowledge of basic elements of GMP. This includes understanding all company and regulatory guidelines
- Responsible for establishment of efficient, reliable and profitable manufacturing processes throughout the manufacturing area(s)
- Proficient with MS Word, Excel spreadsheets, Data Analysis, Formatting usable tables and other evaluation documents and Outlook programs
- Good working knowledge of operations, quality standards, policies and procedures as well as FDA guidelines and applications
- Strong computer skills, with working knowledge of factory systems and SAP highly desired
- Maintain professional and technical knowledge by necessary for quality output and team results for customer satisfaction
- Highly organised with excellent ability to manage own and others time
15 Production Supervisor resume templates
Read our complete resume writing guides
1
Production Supervisor Resume Examples & Samples
- Vet various production budgets and schedules submitted by 3rd party production company for pilots, and/or presentations to make sure that our Networks’ needs are met, be it creative, technical, legal, price, and deadline related and make recommendations to senior management as part of the green light process
- Review the cash flow payment schedules submitted by 3rd party production companies and make recommendations to senior management
- Provide necessary information to production operations department to have 3rd party production specifications manuals created and review the manuals for accuracy before distribution
- Explain production and technical standards, show formatting, deal memos, contracts, financial reporting, insurance, production and safety policies, and wrap requirements to various 3rd party production companies and answer questions regarding network requirements
- Act as liaison between 3rd party production companies and all internal departments (i.e. Business & Legal, Standards & Practices, Rights & Clearances, On-Air Design, Promos, Network, etc.)
- Review 3rd party cost reports with production accountants and report any issues to senior management
- Ensure all deliverables are completed accurately and on-time and report any issues to senior management
- Observe all department and company guidelines
- Perform additional tasks as assigned
- Minimum 2-3 years Production Management or related experience required
- Minimum 1-2 years of Media/Entertainment required
- Working Knowledge of Microsoft Office including Word, Excel, PowerPoint, and Outlook
- Has solid understanding of production workflow and hands-on experience in reality/studio-based productions
- Able to review budgets, schedules, and full-scale production plans for a variety of program types, specials, pilots, and presentations
- Has general understanding of accounting principles and procedures, including general ledger, journal entries, account reconciliation, month-end, and cost reporting
- Possesses strong interpersonal and communication skills
- Is an extremely organized and dependable team player, who works well under pressure while handling multiple responsibilities
- Is self-motivated, proactive, flexible, resourceful, and diplomatic
- Can be trusted to keep sensitive information secure
- Ensures accuracy of work
2
Production Supervisor Resume Examples & Samples
- To supervise production of mail projects to meet rigid in-home reliability targets
- To ensure accurate manufacturing of direct mail as specified by work orders. To ensure that all mailings are in accordance with postal regulations. To manage relationship with the Post Office and respond to postal inquiries
- To implement Company policies and procedures in order to ensure fair, consistent, timely and uniform application
- To coordinate maintenance functions with on-site maintenance personnel in order to ensure proper operation of all production equipment and materials. Recommends maintenance and troubleshooting activities to appropriate personnel to ensure equipment is functioning properly
- To maintain a high level of quality for all products produced, and to review the products regularly to ensure that quality standards are maintained
- To analyze procedures and recommend/implement measures to improve production methods, equipment performance, quality of product and implement changes to increase efficiency of department or work crew
- To maintain a high level of morale and team-work on the production floor through frequent communication with employees to keep them informed of any new products and/or procedures, and to listen to employee concerns
- To ensure that all activities and operations are performed in compliance with all local, state and federal regulations
- To recruit, train and supervise a workforce. Approve new hires and recommends or initiates personnel actions such as disciplinary measures or discharges
- To evaluate employee performance against pre-established standards of performance in accordance with company policy. To provide coaching and counseling to employees which will encourage professional growth as well as meet short and long term goals
- To comply with all applicable federal, state and local regulations and company policies affecting employee's health and safety
- Should have a high school diploma or acceptable equivalency. College preferred
- Must have in-depth knowledge of the production and manufacturing
- A plus would be familiarity with mail production equipment including, tiers, pallet jacks and forklifts, letter inserters, labelers and Ink Jet equipment solo mail sorting procedures, distribution logistics, warehousing, and US postal regulations
- Must have the ability to work independently, analyze situations and conditions and implement solutions and work under deadline pressure. Must have effective interpersonal skills and the ability to communicate with all personnel. Must provide on-the-job training and have strong supervisory, planning and scheduling skills
- Typically requires two to four years experience in a production and manufacturing environment
- Position requires working in production areas with fork-lifts, pallet jacks, inserting, inkjets and related equipment is in use. Working in this environment directly results in exposure to paper dust in the air and noise levels from running equipment
3
Production Supervisor Resume Examples & Samples
- Maintain astaff of employees that are effectively trained on executing all procedures,policies and processes by identifying skill requirements for all filling andassembly department positions, implement training plans for each departmentemployee, work directly with the staff and teach any identified training needs,utilize the training coordinator to document completed training, andcommunicate performance expectation and provide constructive feedback
- Eliminateaccidents and continuously improve ergonomics by ensuring employees adhere toestablished safe work practices, and utilize proper ergonomic related equipment
- Produce productthat meets all quality expectations and eliminate rejections by verifying allproduct quality standards are maintained and documented, analyze causes ofquality challenges and institute corrective action as necessary
- Verify routingsand consistently produce to standard cost by providing assistance in startup,operation, changeover and troubleshooting of multiple lines
- Complete allproduction runs on schedule by ensuring accurate production reporting, andinteracting with the temp agency representative regarding staffing needs
4
Production Supervisor Resume Examples & Samples
- Experience of managing in the Food/healthcare/pharmaceutical manufacturing Industry is desirable
- Proven track record in over achieving KPI's and Operational Targets
- Knowledge of international Good Manufacturing Practice and Good Housekeeping Practice standards is essential
- Management of a maintenance and/or engineering function is desirable
- The ability to communicate clear objectives and motivate staff to achieve more is the key to success for this role
5
Production Supervisor Resume Examples & Samples
- Complies with standards and processes such as Hazard Analysis and Critical Control Point (HACCP) and Good Manufacturing Practices (GMP) to ensure product quality
- Monitors production throughput, volume fluctuations and labor utilization to ensure smooth manufacturing operations. Ensures that partners work in accordance with the production schedule to provide product reliability. Ensures appropriate staffing to meet new business requirements and volume fluctuations. Minimizes scrap to control costs
- Manufacturing or related functions
- Strong leadership skills, with the ability to coach and mentor others
6
Production Supervisor Resume Examples & Samples
- Leads the activities of the team members in the production of quality prescription eyewear in accordance with work instructions and company policy to ensure a quality product delivered on time
- Insures the appropriate level of accountability for facility goals and objectives at the team leaders and team member’s levels
- Maintains adherence to company policies, safety standards, and good housekeeping practices
- Leads in the identification of quality, process, workflow, and personnel problems and works to resolve these quickly according to company policy, practice, and guidelines
- Utilizes problem solving techniques, teamwork building strategies, process control, and continuous process improvement tools to meet or exceed the facility key operating statistics
- Facilitates meetings with the shift team members and team leaders at regularly scheduled intervals. The meeting purpose is to communicate the company and facility goals and objectives, successes, process problems, corrective and preventive actions, etc
- Facilitates team leader workflow management, workforce scheduling, and team members’ placement to ensure the facility and company goals are successfully met or exceeded
- Plans and manages innovations to existing processes, implementation of new processes, installation of new equipment, etc
- Assists fellow supervisors and the facility manager in the execution of their duties and in meeting company and facility goals and objectives
- Conducts, leads, or implements the appropriate process audits. The audits will identify the need for the appropriate containment, corrective, and preventive actions, leading to minimizing or eliminating process deviations and non-conforming product root causes
- Interviews, hires, and plans appropriate training for new team members. Instrumental in encouraging team members to elevate their level of technical expertise
- Interacts with associates to establish rapport with team members, to take an interest in the individual and their work and to obtain knowledge of workplace issues
- Supervises team members’ performance and discipline issues in a timely manner. Communicates expectations and behavior changes required in these cases. Follows up with each team member on his or her progress against these expectations
- Conforms to cost center results and budgetary constraints. Analyzes variances and implements action plans to meet or exceed cost per Rx results
- Participates in the team leader’s comprehensive development in areas such as leadership, conflict resolution, communication, process control, problem solving, etc
- Evaluates performance expectation plans with team leaders and team members to meet individual goals and facility objectives
- Communicates business needs, schedules changes, process problems, success stories, etc. This communication takes place top to bottom, to the facility manager, and horizontal across the organization
- Prior Leadership or Technical experience
- 0-7 year of experience in a manufacturing setting
- ISO 9000 and optical training helpful
- LEAN manufacturing experience a plus
- Developed personal computer skills and statistical skills required, as well as, ability to work with peer and upper management personnel
7
Production Supervisor Resume Examples & Samples
- Review production orders or schedules to ascertain product specifications and scheduled delivery dates in order to plan shift operations
- Assist in the preparation of operational schedules and coordinate manufacturing activities to insure the production and quality of products meets specifications
- Assist in the supervision, training and evaluation of staff, spending a minimum of 50% of time on the production floor
- Analyze manufacturing schedule to plan work assignments for group on basis of priority, worker skills, production methods, processes, material, machines and equipment
- Review work orders, product specifications, technical instructions and facility requirements and to facilitate requisition of tools, equipment and supplies with Production Management
- Evaluate equipment and processes to insure personnel safety
- Associates degree in a business or technical discipline OR an equivalent combination of education and experience
- Must possess a minimum of 5 years supervisory/management experience in a manufacturing, warehouse, or operations related environment
- Must possess a minimum of 3 years experience in production or process operations
- Demonstrated strong and effective verbal, written, and interpersonal communication skills
8
Production Supervisor Resume Examples & Samples
- Understand the bottlenecks of your line and allocate resources accordingly to achieve production output
- Establish countermeasures for quality flow out by conducting root cause investigation and implementing corrective actions
- Identify critical risks in the production processes and work with cross functional teams like Manufacturing Process Engineers and Quality Engineers to resolve the issue
- Maintain compliance with all safety regulations
9
Production Supervisor Resume Examples & Samples
- Understand “ Process bottlenecks” or “Gating” items within scope or assigned area of responsibility, take timely action to allocate resources accordingly to achieve stated goals & expectations to ensure production output
- Ensure initial quality standards are developed for new operations & work cells confirming solutions are practical throughout entire production process and support zero defect flow out from station or team area
- Establish effective countermeasures for quality flow out by conducting thorough root cause investigation and analysis … implementing timely corrective actions
- Identify critical risks in Beta/Pilot build processes & work with cross functional teams i.e. Design, Manufacturing, Supplier, Quality & appropriate support group Engineers to resolve issues
- Develop & Support training on Standardized Work Instructions to be used by production associates
- Ensure Teams maintain compliance and adhere to all safety regulations
- Develop training programs and support interviewing / hiring plans for Pilot associates
- Manage and approve timecards for direct report and or assigned Team Members
10
Production Supervisor Resume Examples & Samples
- Build a strong motivated production team capable of consistently delivering high quality products against aggressive production targets
- Empower the production team to collaborate with engineering to improve product manufacturability and line productivity
- Support issue resolution including root cause investigation & corrective action tracking
11
Production Supervisor Resume Examples & Samples
- Coordination of all production aspects for the 2015 World Science Festival, scheduled to take place from May 27 through May 31, 2015 to insure flawless execution of all events at the highest possible level of production
- Meets regularly with the Editorial and Creative Staff to facilitate the development of programs, manages expectations and defines technical parameters required for each program and updates the festival budget and staffing plan as required
- Works directly with Director of Finance and Administration to manage all production elements, programming and staffing requirements to meet budget targets
- Selects and hires Venue Producers as needed to manage the individual venue program development and execution as needed
- With Festival Technical Director develop RFQs for all technical vendors, lighting, audio, video, staging, props etc., based on the ascertained needs from the above meetings
- Manages the bid process for all technical vendors including preparation of bid specification with Festival Technical Director, identification of vendors invited to bid, evaluation of bids and awarding of bids upon final budget approval from the Director of Finance and Administration
- Works with the Technical Director and Venues Producers to determine the production staffing required at each venue and approves all hires in the Production department
- Sourcing and management of all design staff or consultants
- Oversees the development of the overall Festival production schedule and insures that scheduling conforms to budget
- Manages all production staff to insure complete and accurate documentation is maintained of all festival production details including contact/staff lists, schedules, scenic and lighting designs, equipment lists, rental orders and schedules
- Is the festivals primary production contact with all Festival venues and partners and works with the General Manager or Director of Operations on the creation and execution of all venue contracts
- With the Director of Operations (General Manager) supervises on site Venue Managers in the operation and execution of Festival programs at each Venue and Partner Venue
- Works with venue staff and management to insure that all festival production staff working in a venue observe and abide by house rules and best practices
- Insures that any necessary permits or licenses to facilitate festival productions are obtained
- Insures that all production expenses are submitted to accounting and codes all expenses
- Provide a final wrap up of festival production expenses tied back to approved budgets
- Ability to anticipate, identify and resolve complex issues related to production
- Demonstrated oral and written communication skills and ability to work cross functionally
- Demonstrated ability to multi-task, perform in a fast-paced environment & respond quickly to situational needs as
12
Production Supervisor Resume Examples & Samples
- Supervises in their daily work flow of production employees and production operations
- Conducts employee performance assessments and makes recommendations regarding the movement of personnel; works with HR to ensure timely, consistent, and impartial discipline is administered when necessary
- Supports continuous improvement efforts and recommends measures to improve production methods; ensures compliance with standard operating procedures and safety rules and regulations
- Participates on Integrated Product Team to ensure manufacturing needs are addressed by various functional groups
13
Production Supervisor Resume Examples & Samples
- 2+ years of related Production experience
- Degree in a related field
- Computer savvy
14
Production Supervisor Resume Examples & Samples
- Bachelor's degree in Engineering or a related field
- Strongly skill in manpower management
- Experience in welding, assembly, machining or painting process is an advantage
- Ability to work on several working shift
- Good leadership skills
- Effective communication skills both of Thai and English
15
Production Supervisor Resume Examples & Samples
- Quality- Makes quality control decisions based on established quality standards and checks. Applies principles of statistical process control when appropriate. Identifies opportunities for common mistake proofing. Develops and ensures standardized work is followed and maintained. Responsible for process layered audits per the process audit schedule
- Communication- Effectively communicates performance in all aspects of the business including, but not limited to Policy, Safety, Quality, Delivery, Productivity during pre-shift meetings and team meetings
- Safety/5S- Corrects or commends health and safety performance in work area and takes immediate action to correct unsafe conditions or actions. Responsible for proper handling, storage, and disposal of all chemicals, used materials and equipment. Ensures employees are appropriately trained in recognizing hazards associated and specific to their job. Leads accident/incident investigations. Leads 5S activities within the model cell. Assists in conducting risk assessment on new and/or modified equipment and/or processes
- Training- Responsible for new team members orientation on processes, policies and procedures. Development of employees using on-the-job training and training matrices. Has the ability to hire/fire and discipline employees. Provides constructive feedback to all employees regularly through performance reviews
- Improvements- Responsible for continuous improvement for customer concerns, on time delivery through schedule attainment, quality, scrap reduction, safety and moral. Leads teams through problem solving process, documents issues and identifies solutions that prevent recurrence. Develops job breakdown and standardized work processes with team, Performs time studies of operation while developing and performing with the team work sequence, standardized work and takt time charting
- Materials- Leads online schedule attainment. Actively works with materials team to insure accurate inventories and transaction processing. Knowledge and usage of Baan related systems and implements visual controls as required. Respond to inventory variances with corrective action for focus lines. Monitors utilization of kanban – JIT systems. Ensures that the team has proper supplies (gloves, trash cans, blades, trim stands, etc.)
- Upward Communications- Tracks and evaluates performance measurables against quality, cost and delivery goals. Executes appropriate action plans to meet or exceed goals. Alerts management team of significant variations of goals and expectations to prevent surprises through corrective action, desired performance and proactive communication
- Performs other duties as necessary in support of business objectives
- EHS - Performs all work in compliance with Magna and Magna Sealing and Glass Systems Health, Safety and Environmental policies and procedures as well as all federal, State and local laws; promptly report any hazardous condition or workplace injury to immediate supervisor or EHS designate
- Bachelor’s degree or minimum of five years related supervisory work experience
- Two years of supervisory experience with degree or five years if non--degreed
- Experience in the automotive industry
- Demonstrated strong communication skills in order to work with internal and external contacts at all levels within the organization and represent the Company in a professional manner
- Demonstrated strong analytical, troubleshooting, and problem-solving skills for successful performance of job duties. Must have understanding of business issues relevant to job and Company operating procedures and connect these to work priorities and resolve problems
- Demonstrated ability to lead and develop others through support, training, etc. Must be able to manage staff toward departmental goals usually of a short-term focus
- Demonstrated project management and leadership skills to lead, manage, prioritize, and deal with many issues at one time
- Demonstrate ability to motivate team toward goals of a moderate-term focus
- Perform work while seated or standing at work station using a computer (or other office equipment) 30-50% of work day, requiring frequent fingering on keyboard
- Walk to and from various locations 50-70% of work day
- Occasional reaching above and below waist height and above shoulder height
- Occasional lifting and carrying of items weighing up to 25 lbs
16
Production Supervisor Resume Examples & Samples
- Bachelor's Degree in Food Science or a related discipline
- 6+ years' experience in a food manufacturing environment, with at least 4 years supervisory experience
- Proven experience in working within a similar role in a fast paced manufacturing environment, ideally a GMP environment
- Experience in Lean Manufacturing or Six Sigma principles is highly desirable
- Excellent interpersonal skills, can work on own initiative & also as part of a team
- Good organisational skills and a strong ability to follow procedures
- Good work ethic & time management skills
- Pro-active approach to problem solving
17
Production Supervisor Resume Examples & Samples
- Manage the plant budget and production objectives
- Develop and oversee proficient operations in production planning, materials control, quality control, safety and maintenance
- Plan and direct the efficient use of facilities, equipment, materials and production staff to meet production needs
- Monitor plant performance against established safety, quality, delivery and budget standards
- Forecast people and facilities requirements meet corporate and plant objectives
- Manage all in plant set-up resources to ensure that goals are met efficiently and effectively
- Ensure that the company conforms to all customer requirements related to part quality
- Ensure that appropriate corrective action is in place where non-conforming part issue arise in house or at customer locations
- Maximize plant utilization of human resources and equipment
- Meet budgetary spending targets for the departmental cost centre
- Ensure that established OEE Quality, Availability & Performance standards are communicated and achieved within the division
- Ensure that safety standards are identified, communicated and achieved within the division
- Where an established OEE or safety standard is not being met, it is the manager’s responsibility to identify the root cause and take the appropriate action
- Ensure that operators use standard work and associated tools to meet standards
- Ensure that all OEE and 5S measures are in place and updated as required
- Maintain 5-S standards within the department
- Participate in employee counseling and disciplinary action as required
- Ensure the efficient execution of responsibilities as outlined in the job descriptions for the Production and Production Quality departments in the plant
- Perform a minimum of one yearly performance appraisal for each direct report
- Ensure that training requirements for each departmental employee are identified and plans are in place to close any gaps
- Ensure that environmental standards are identified, communicated and enforced within the department
- Ensure supervisors perform a minimum of one yearly performance evaluation for each departmental employee
- Ensure the fair administration of all company policies including wage and benefit packages
- Maintain communication and utilize the expertise of other departments as required
- Ensure compliance with defined Business Management and Environmental Management Systems requirements
- Work in compliance with all health, safety and environmental legislation and ensure that departmental employees are trained appropriately
- Provide support for the continuous improvement initiatives within Techform
- Provide support in the attainment of Techform's "Quality Operating System" goals as outlined be the key graphs
- Carry out all duties focusing on the goal of internal and external customer satisfaction
- Superior organizational and communication skills
- Complete knowledge of the Occupational Health and Safety Act
- Must possess a post secondary degree, diploma or equivalent in a management related field
- A minimum of seven (7) years experience in a management position within a manufacturing environment is required
- A general knowledge of employment law would be an asset
18
Production Supervisor Resume Examples & Samples
- Provide technical support for the qualification and validation of new product introductions to ensure all aspects of performance, manufacturability and quality are achieved
- Provide technical support for the qualification and validation of new equipment and processes; and identify and implement new technologies to continuously improve processes
- Develops and coordinates programs to recognize and reward groups or individuals for suggestions and actions related to process improvement
- Lead and support root cause analysis investigations, recommend and execute corrective actions and preventative actions
- Conduct investigations and tests pertaining to the development of new manufacturing methods, materials or processes, and investigate possible applications of results
- Strong Interpersonal and communication skills with the ability to communicate and listen at all levels
- Self-motivated with high sense of urgency, resourcefulness and adaptability
- Position requirements include a Bachelor’s Degree or equivalent with a minimum of five years experience in a manufacturing setting
19
Production Supervisor Resume Examples & Samples
- Meet or exceed productivity, efficiency and quality standards on a daily basis
- Maintains and promotes adherence to all Health Safety & Environment policies and procedures
- Develop and maintain a team oriented atmosphere at all times
- Provide a high level of communication with all Employees
- Interact with all support functions to ensure smooth operation of activities
- Enforce all divisional policies and procedures
- Work with continuous improvement, 5S and cost reduction initiatives for the department
- Accurately maintain payroll and overtime tracking
- Consistently apply all elements of the Employee Charter and Collective Agreement
- Provide ongoing training to new employees, line transfer employees, and existing employees
- Investigate all employee complaints of unfair treatment in a timely manner. Respond to employee issues, concerns, suggestions and complaints within 48 hours
20
Production Supervisor Resume Examples & Samples
- Promote company culture and ensure discipline to all company policies and procedures
- Supervises hourly employees in the performance of their job
- Coordinates the training of new employees on respective lines to perform all operations and to follow safety requirements
- Maintains time and attendance for all hourly employees as directed
- Ensures equipment is properly set-up on respective line(s)
- Schedules daily line production to meet customer demand and plots productivity changes weekly
- Ensures Magna Production System (MPS) principles of standardization and one piece flow are established and enforced
- Assist in the process of Job Task Analysis and Hazard Identification for machinery in their area
- Ensure employees' do pre-start inspections and co-sign checklist to verify completion
- Perform daily unplanned inspections. Ensure that inspection is appropriately documented
- Responsible to ensure Employee Development Plans are in place for the department, if applicable
- Responsible and accountable to manage, support and provide direction to all staff within the department – including Performance Reviews and Employee
- Development Plans, if applicable
- Communication through line/department meetings
- Responsible for collecting Business Center data related to the overall measureables of the unit; bench marking and analyzing these trends and establishing related action plans
- Ensures confidentiality of all company personnel data
- Overtime and travel may be required to support achievement of objectives
- Conduct planned workplace inspections, as scheduled by the Environmental, Health and Safety Department
- Ensures visibility and accessibility to employees, by practicing Management By Walking Around (MBWA)
- Completion of high school or equivalent
- 5 to less than 7 years of work related experience
- Minimum 2 years supervisory experience preferred
- Sound Computer Knowledge
- Sound knowledge of Magna Production Systems
21
Production Supervisor Resume Examples & Samples
- Enforce and encourage both standardized work and one piece flow
- Lead, mentor and coach Team Leader(s) on processes, training and development and employee relations
- Participate in the daily scrap walk
- Review scrap daily and sign off with the Team addressing areas, where needed
- Ensure that employees are conducting proper pre-shift inspections of their workstations
- Maintain safe work practices according to regulations under the Occupational Health and Safety Act (i.e. perform regular workplace inspections, involved in SEWO, correct in safe acts or conditions, training of new employees)
- Initiate SEWO and assist with back to work plan with Modified Work Employees
- Directs the utilization and use of all machinery and equipment involved in assembly production activities
- Ensure materials are delivered on time to the work centre to meet production requirements
- Maintain records of availability of components/ parts and movement/ storage of work process
- Monitor inventory levels finished and purchased components
- Review key resets at end of shift and reconcile to number of parts rejected
- Maintain employee records to include time keeping, absenteeism, overtime records and performance reviews
- Work with Human Resources to create a performance improvement plans as required
- Oversee distribution of overtime in a fair manner
- Analyze Overall Availability (OA) of work centre and plans necessary actions to improve
- Maintain communication with assembly operators and listen to any improvement suggestions
- Encourage Assembly Operators to submit suggestions into the GROW Program
- Maintain up-to-date CPR and First Aid Entrapment Procedure, Fire evacuation training for use in emergency response
- Ensure the Escalation Process is being followed
- Follow through with engineering changes in production
- Perform yearly performance reviews
- Monitor floor layout & organization
- Track non-standard hours to try to isolate reduction actions
- Assist in the implementation of continuous improvement objectives
- Provide input and makes recommendations for approval regarding disciplinary action and employee counselling. Keeps all comments documented and escalate to Human Resources when needed
- Implement and coordinate 5S activities with Team (zone champions) delegated
- Complete any quality and NCR Dispositions as required
- Ensure NCR Procedure is followed and that it includes Quarantine Cage Procedure
- Must fill out sensor By-Pass log as applicable
- Cross reference E-time to time sheets and the attendance log
- Approve vacation as per policy
- Investigate stock loss terms when required
- Comply with TS 16949 and MAFACT Policies and Procedures
- Must comply with all ISO 14001 (Environmental) and OHSAS 18001 (Health and Safety) systems and standards as it pertains to their work
- Abide by all AODA and C-TPAT procedures that apply to their position
22
Production Supervisor Resume Examples & Samples
- Implements production schedule in the most efficient and effective manner
- Ensures that the work instructions are followed and that Team Associates receive all required training
- Maintains production efficiency without sacrificing safety, quality, and cost standards
- Facilitate continuous improvement activities, as necessary
- Respond to Team Associate concerns/issues in a timely manner
- Conduct employee performance reviews in a timely manner
- Conduct pre-shift meetings and communicate all pertinent information to Associates
- Ensure that shift production reporting is processed accurately and in a timely fashion
- Ensure that all company policies are adhered to at all times
- Administer employee discipline, when necessary
- Reduce and/or eliminate the number of recordable injuries on the respective shift
- Member of safety committee – drives safety improvements through monthly safety inspections
- Follow all health/safety rules
- Maintains safe working procedures and good housekeeping practices; responsible for participating in the investigation and resolution of safety incidents/accidents
- Performs daily health and safety audits
- At least 3 years of supervisory experience in an automotive, manufacturing environment
- Excellent communication skills, including ability to effectively discipline, reward and coach employees
- Working knowledge of safety standards and OSHA guidelines
- Skills and Competencies
23
Production Supervisor Resume Examples & Samples
- Monitor and improve shop floor safety, aggressively eliminating unsafe processes
- Determines priorities and sequences jobs
- Increases production efficiency through continuous improvement and waste elimination
- Ensures preventive maintenance is performed according to schedule
- Good language, communication, interpersonal and teamwork skills
24
Production Supervisor Resume Examples & Samples
- 1)Maintain work areas to meet and exceed customer requirements
- 2)Visually monitor housekeeping and plant organization
- 3)Monitor and address safety & environmental concerns on the shop floor
- 4)Monitor quality issues toward our goal of zero defects
- 5)Control overtime to achieve a goal of 0 hours
- 6)Improve efficiency by reducing down time and set-up time
- 7)Perform daily scrap reviews
- 8)Enforce company policies as outlined in Handbook
- 9)Create and implement Continuous Improvement suggestions
- 10)Housekeeping and other activities as assigned
- 11)Provide a safe and healthful work environment that is free of recognized hazards for all associates, contractors and visitors
- 12)Advise associates, contractors and visitors of any actual or potential danger to their safety or health, and ensure the necessary training and/or Personal Protective Equipment (PPE) is provided and used
- 13)Cooperate with all local, state and federal agencies, such as OSHA or the EPA, in the event of an inspection
- 14)Know, follow and enforce all applicable TS 16949, ISO 14001 and Safety Policies and Procedures
- 15)Investigate all injuries (Immediately) and ensure corrective action is taken and maintained
- 16)Perform hourly production board walks
- 17)All other requirement as directed by Management
25
Production Supervisor Resume Examples & Samples
- Bachelor’s degree or equivalent experience is required
- 4 plus years’ experience in Investment Management Industry preferred
- Minimum 3 years sales support, or client service experience preferred
- Experience managing production teams for large scale client reporting needs
- General knowledge of the institutional investment management and mutual fund business
- Global team management experience
- Team mentoring and development experience
- Experience working in a large, complex global investment firm
- Operational team management experience
- Ability to self-manage
- Strong team management and development skills
- Excellent relationship building skills
- Manage a large team of production staff
- Able to represent team within region with local senior leadership
26
Production Supervisor Resume Examples & Samples
- Ensure productivity, efficiency and quality standards are achieved on daily basis
- Plan, coordinate and notify employees of their daily tasks
- Take appropriate corrective action when substandard performance is observed
- Interact with all support functions to ensure smooth operation of Production activities in their assigned areas
- Champion continuous improvement and cost reduction efforts for the their assigned areas
- Maintain 5S in areas of responsibility and maintain all MaFact Communication Boards
- Provide ongoing training to new employees, line transfer employees, and existing employees; and
- Assist in weekly workplace inspections, including the completion of work orders and related actions to correct substandard conditions and behaviors
- Perform daily inspections of the work area and document the existence of any hazards
- Communicate to employees the importance of adherence to established health & safety policies and procedures through safety talks, departmental meetings and or work center briefings
- Communicate and enforce all company health & safety policies, practices and rules, and readily correct unsafe conditions or behaviors of which you become aware
- Adhere to and follow all company health & safety policies, practices and rules for the workplace
- Investigate workplace accidents/incidents of which you are aware and/or within the work area(s) under your responsibility, which may include but is not limited to conducting interviews with employees, investigating the incident scene, preparing incident investigation reports, and implementing corrective actions. In the event of a critical injury, ensure a worker representative of the Joint Health & Safety Committee is notified and assists with the investigation
- Support employees impaired through injury or illness to safely return to work (Return to Work program)
- Comply with legislative requirements of the Occupational Health & Safety Act and Workplace Safety & Insurance Act, including the Duties of a Supervisor and Duties of the Employer as outlined in the Occupational Health & Safety Act, s. 27 and 28
- Administer progressive discipline when warranted and complete of required documentation and disciplinary meetings
- Ensure that all elements of the Collective Bargaining Agreement are followed; and
- Maintain proper records and backup documentation
- Follow the Principles of the Employee’s Charter and the Corporate Constitution
- Attend all scheduled training sessions, and complete related course materials
- Suggest systems, processes, and activities that increase productivity by improving integration of people, materials, equipment and finance
- Must be able to travel overseas for business reasons
- Other Duties as required
27
Production Supervisor Resume Examples & Samples
- Supervises Team Leader(s) and Production Team Associates including but not limited to planning, assigning, directing and coordinating their day-to-day activities
- Assists the Production Manager in determining and managing appropriate manpower requirements
- Trains new and transferred employees on their job duties and responsibilities; and cross trains as necessary
- Tracks and reports daily production; and drives improvements where necessary
- Works to improve first run capabilities by identifying repeat offender(s) and developing corrective action
- Participates and leads process improvement projects: productivity, quality, ergonomics, etc
- Monitors, maintains and records employees’ time related to the Attendance and Time-Off Policies (e.g. vacation, medical day, bereavement, jury duty, etc). Records approved time-off requests in E-Time; and ensures required time-off requests with supporting documentation are processed completely and timely
- Ensures all employees and visitors have a safe environment in that safety and housekeeping standards are maintained; and all hazards, unsafe actions, or unsafe conditions have been identified, corrected, and/or eliminated
- Responds to and investigates all reports of injuries, accidents, illnesses, near misses and property damage immediately
28
Production Supervisor Resume Examples & Samples
- Quality- Makes quality control decisions based on established quality standards and checks. Identifies opportunities for common mistake proofing. Understands quality control plans. Accurately tracks and measures defects and performs a defect analysis. Ensures standardized work is followed and maintained
- Communication- Effectively communicates performance in all aspects of the business including, but not limited to Policy, Safety, Quality, Delivery, Equity, Productivity and General Focus Factory Communications, during pre-shift meetings and team meetings
- Safety/5S- Corrects or commends health and safety performance in work area and takes immediate action to correct unsafe conditions or actions. Ensures employees are appropriately trained in recognizing hazards associated and specific to their job. Completes safety inspections on a routine basis, and ensures compliance with all Health and Safety as well as ISO14001 policies and procedures. Leads accident/incident investigations. Assists in conducting risk assessment on new and/or modified equipment and/or processes
- Staffing- Responsible for weekly staffing of work cells based on customer demand / weekly schedule in accordance with materials team. Staffs work cells with trained personnel to meet “takt time”. Maintains vacation, overtime, off-line training and relief schedules
- HR/Training- Development of employees using Training Within Industry and training matrices. Presents new information to large and small groups. Administers and applies company policy consistently and fairly. Has the ability to hire/fire and discipline employees. Provides constructive feedback to all employees regularly through performance reviews. Establishes individual development plans by determining needed skills and knowledge. Participates in the hiring of new employees by interviewing candidates effectively and legally. Develops team competence using E.O.S improvement activities. Responsible for maintaining and developing team morale
- Improvements- Responsible for continuous improvement for customer concerns, on time delivery through schedule attainment, quality, scrap reduction, safety and morale. Leads teams through problem solving process, documents issues and identifies solutions that prevent recurrence. Supports Continuous Improvement team in the performance and completion of time studies of operation while developing and performing, with the team, work sequence, standardized work and takt time charting
- Materials- Leads on-line schedule attainment. Knowledge and usage of Baan related systems and implements visual controls as required. Responds to inventory variances with corrective action for manufacturing shift. Monitors utilization of kanban – JIT systems
- Upward Communications- Tracks and evaluates performance measurables against safety, quality, cost and delivery goals. Executes appropriate action plans to meet or exceed goals. Alerts management team of significant variations of goals and expectations to prevent surprises through corrective action, desired performance and proactive communication
- General- Performs other duties as necessary in support of business objectives
- With Bachelor's: Two (2) years of automotive or related manufacturing industry experience
- Without Bachelor's: minimum of five years related supervisory work experience
- Prior financial experience
- Previous work experience with an automotive manufacturing company
29
Production Supervisor Resume Examples & Samples
- TECHNICAL
- Address any downtime related to inadequate equipment and make recommendations for enhancement
- Specific technical skills as required for area (i.e.: CNC, tool and die, fine blanking, Grob, and assembly)
- Engineering Technologist designation or equivalent
- Excellent knowledge of TS16949/ Workwell/ISO14001 systems
- Previous Supervisor (approx. 5 years) experience necessary or equivalent manufacturing exposure
- Excellent English language communication skills (both verbal and written)
30
Production Supervisor Resume Examples & Samples
- Responsible for the day to day supervision of Foam Production employees
- Establish a professional relationship with the employees in production
- Encourage the work force to be quality driven, and motivated to achieve the goals and objectives of the company
- Handle issues in a manner that will resolve them before they escalate to the grievance stage
- Practice principles that are fair, firm and consistent. Take action only after all the facts are known
- Monitor, maintain and record all variables that relate to the company attendance policy in an expedient manner. Those of which would include, but are not limited to, absenteeism, tardiness, vacation etc
- Strive to improve first run capability by identifying repeat offenders and developing corrective action to eliminate issues
- Be proactive and take responsibility as a change agent
- Work towards achieving continuous improvement goals established by management. Implement ideas that force trends upward. Key factors in production include direct labor efficiency, first run capability, as well as reduced supplier issues. Document results on a daily basis
- Maintain a clean, safe and professional place for employees to work by utilizing them during downtime or agreed upon contractual time
- Ensures that the principles of the Magna Employee Charter, Corporate Constitution and the Operating Principles are practiced, supported, and reinforced
- Responsible and accountable for the Employee Opinion Survey (EOS) results
- Ensure all employees have a safe environment in that all hazards, unsafe actions, or unsafe conditions have been identified, corrected, and/or eliminated
- Enforce safety rules, policies, and procedures consistently, and respond to and investigate all reports of accidents or injuries in a timely manner
- Thoroughly train new employees, correct or commend employee’s health and safety performance, and conduct adequate performance appraisals by evaluating an employee’s safety performance
- Display a positive attitude towards safety and lead by example that will result in a safe and healthful workplace for all who work at Louisville Seating Systems
- Ensure that Health, Safety and Environmental standards are adhered to in accordance to the Magna Employee Charter and the Occupational Health & Safety Act
- Administers and ensures compliance with the Quality and Material Management System requirements as outlined in the policy manuals
- 2-6 years supervisory experience
31
Production Supervisor Resume Examples & Samples
- Implements production schedule and related goals with the operators available, in the most efficient and effective manner
- Ensures that the work instructions are followed and that the operators have received the proper training with regard to work instructions, quality and safety procedures
- Ensures that plant efficiency is maintained at the highest possible level, without sacrificing safety, quality and cost standards
- Maintains consistent communication and shift reports with Engineering, Maintenance, Shift Supervisors and Management utilizing all available and appropriate communication tools
- Exercises supervisory control over assigned personnel, and provide guidance and assistance to them to resolve non-routine problems
- Reviews work performance of plant personnel and makes recommendations regarding future work assignments
- Ensures that Shift Production and related reports are processed accurately and on time
- Responsible for completing Layered Process Audits on a weekly basis and closing and/or elevating issues as required
- Ensures that all employees’ concerns are handled by appropriate personnel in a timely and constructive manner
- Ensure confidentiality in all respects towards the Company and its Personnel, Customers and Suppliers
- Technical knowledge of the manufacturing process. (CNC machining & assembly operation)
- Must be very familiar with TS16949/QS-9000 and ISO14000 Procedures
- Must have working knowledge of Industrial Equipment Risk Assessment, Transportation and Handling of Dangerous Goods, Workplace Inspection
- 5 years experience in a manufacturing environment as a Production Supervisor preferably in automotive
- Must be able to communicate fluently in both written and spoken English
- Highly engaged and proactive in the area of health and safety with fundamental knowledge of safety standards (O.H.S.A. and Industrial Accident Investigation Report)
- Must be able to relate/communicate well with people at all levels
- Able to positively motivate and lead
- Must have good organizational skills, be a self starter and a team player
32
Production Supervisor Resume Examples & Samples
- Supervision of production teams to ensure targets for quality/service/costs are achieved. This will be achieved through the application of an empowering style of leadership which draws fully on resources and capabilities of the team coupled with a positive employee relations approach
- Providing timely feedback and review, and ensuring all performance issues are dealt with in a constructive and prompt manner
- Consistently applying the company's policies
- Ensuring that all employees are treated with the fairness and respect due to them
- Facilitating open two-way communications regarding individual, team and company performance through weekly team meetings, daily interaction on the line and updating of on-line notice-board
- Liaising with line trainer to develop a training program to ensure smooth operation of department, the development of product builders and the health & safety of personnel
- Employee selection and hiring
- Planning - including developing /maintaining a viable plan incorporating hiring, training, capacity-modelling, efficiency/yield assumptions, ramp-rate, learning-curve etc
- Liaising with warehousing, quality assurance, bulk-packaging and other relevant parties to ensure prompt shipment of product
- Maintaining GMP / Housekeeping at a high level within the department through the involvement of all team members
- Interacting and liaising with the other manufacturing teams and Materials team to prioritise backorders
- Managing process and material flows, space management, and working with the Engineering group to maximise utilisation of space designated for specific operations area
- Administration duties which include Time and Attendance system, Holiday planning etc
- Provide leadership and direction for the advancement of Lean Manufacturing
- Establish and support a work environment of continuous improvement that supports the company's Quality Policy, Quality System and the appropriate regulations for the area they support
- Ensure employees are trained to do their work and their training is documented
33
Production Supervisor Resume Examples & Samples
- Supervise daily work activities
- Work closely with supervisor aides, manager, and other shift leadership in prioritizing and directing department work flow
- Adjust department manpower availability to production requirements
- Ensure assembly integrity through continuous monitoring of departmental processes, including layered standard work and 5S audits
- Verify Supervisor Aides are executing the duties of their position
- Maintain appropriate levels of supplies to meet production requirements
- Monitor issues and receipts for work orders
- Fill in for other area supervisors as needed
- Administer department personnel functions
- Initiate performance reviews and recommend salary changes or promotions when appropriate
- Evaluate and recommend employees for hire, as required
- Using Labor Tracking program, record daily hours and schedule employee time off
- Establish open lines of communication with the production floor
- Enforce the company policies as documented in the Employee Policy Manual and promptly execute formal disciplinary action when required
- Represent corporate policy and communicate to employees as required
- Ensure training and skills matrix are in compliance with training policy
- Work to further develop skills and knowledge for department leadership
- Work toward continuous improvement using the ACE Operating System
- Monitor work order efficiencies and improve wherever possible
- Implement cost reductions where possible
- Write or update processes as necessary, or review processes written or updated by engineering
- Interact with other support departments as required
- Record and interpret production related metrics, recommending corrective action when necessary
34
Production Supervisor Resume Examples & Samples
- Understanding & application of the Magna Charter Principles & Core Values
- Morale – treat everyone with dignity and respect
- Support and assure daily meetings are happening
- Assure proper communication across shifts
- Coach & consult employees
- Provides constructive feedback to all employee regularly
- Coach and counsel Team Leaders
- Administer employee discipline – time and attendance, performance
- Review and audit standardized work instructions
- Ensure that only trained operators are assigned to jobs and that standardized work instructions are being followed
- Ensures that products meet the customer needs in the areas of cost, quality and delivery
- Analyzes hourly production numbers ensuring that efficiency, uptime, attainment goals are being met. Must react accordingly if the metrics are not in line with the targets
- Participates in the hiring of new operators and responsible for maintaining team morale
- Safety
- Complete Accident Investigation reports as necessary
- Assure a safe work area and that safety policies are practiced
- Anticipates safety, quality and productivity problems in work area and takes immediate action to correct unsafe conditions or actions
- Review active Quality Alerts and ensure the team is aware of the issues
- Assists manufacturing engineering and quality control in establishing quality standards and checks
- Audit the Process Centers to assure parts are cleared that don’t belong - line purging
- Review & approve All Suspect Tags – insure they are completely filled out as prescribed
- Promotes 5S activities in all work areas
- Involvement and following up of the different continuous improvement and Corporative Programs: LPA’s, Fast Response, Quality System & Magna Quality systems (MQS), EHS, ISO 14001, Ergonomics, ISO TS, Problem Solving, Lean & MAFACT, Magna Charter & Core Values
- Active participation in the process of the “5 whys” & 8 D’s in order to solve problems
- Assign and manage personnel and equipment resources to meet daily production requirement and shipments to customers
- Conduct employee appraisals as required on time
- Respond to Associate concerns or issues in a timely manner
- Ensure communication occurs with other Production Supervisors
- Must have a positive attitude and be able to handle changing conditions
- Associates or Bachelor’s degree in a related field with general knowledge and or equivalent experience in a manufacturing environment
- Experience in manufacturing processes (mechanical, assembly & machining)
- Demonstrated experience in communications, negotiations, leadership & teamwork
- Ability to lead and develop others through support, training, etc
- Conflict resolutions skills
- Strong analytical, troubleshooting and problem-solving for successful performance of job duties
- Knowledge of ISO/TS 16949 requirements
- Understand written and verbal instructions
35
Production Supervisor Resume Examples & Samples
- Lead production team development and departmental activities around Safety, People, Quality, Delivery and Cost
- Reduce OSHA Incident Rate and attain compliance through weekly safety audits, monthly safety meetings, required safety training, implementation of 5S practices, identification of chemicals and containers, root cause correction, and enforcement of all regulatory and management policies and procedures
- Improve product quality through assurance of operator capability and compliance to specifications. Candidate must manage time constraints, availability of technical resources and various operator skill levels
- Decrease product cost through continuous improvement activities, effective utilization of manpower, machines, materials, and methods. Candidate must manage material availability, labor resources, and capital resources
- Ensure compliance with environmental requirements through control of hazardous waste by training and directing designated employees to handle hazardous waste generated in the department, and compliance with applicable environmental permits, regulations, policies and procedures
- Achieve Production schedule through scheduling of material, manpower, and equipment. Candidate must manage material availability, manpower resources, and multiple sources of information
- Apply employee feedback and develop team associates
36
Production Supervisor Resume Examples & Samples
- Achieve daily attainment requirements
- Maintain and update training matrices
- Record downtime, scraps, and determine team efficiency
- Understand and administer HR policies
- Coach and counsel employees with performance concerns
- Independently administer corrective actions through the written level
- Approve all vacation and appointment time requests
- Document and deliver employee performance appraisals as issued
- Determine allocation of overtime, submit requests for OT approval
- Assign employees to work cells/machines daily
- Ensure cross training for your area of responsibility
- Maintain 5S checklist and ensure 5S performance
- Perform LPA’s
- Maintain Kanban cards, make replacements, and enforce their use
- Perform pre-shift meetings
- Be able to perform Customer Specific Recommendations
- Complete their portion of incident/accident reports
- Understand your responsibility to the environmental programs, including ISO14001. Understand the importance of conformance with all environmental procedures of the environmental management system, including emergency response. Understand the EMS consequences, actual or potential, of their work activities and/or their behaviors from specified work instructions
- Notifies Department Manager and Business Unit Manager on non-conforming issues
37
Production Supervisor Resume Examples & Samples
- Perform all duties and promote themselves in a manner that reflects the P&F expectations, P&F’s vision/
- Grade 12
- Must demonstrate effective oral and written communication skills
- Fluent in English, spoken and written
- Must have good organizational, leadership, interpersonal and problem solving skills
- Able to be flexible in hours of work in order to meet internal/external customer requirements.(scheduled and non-scheduled overtime shifts, etc)
- Must demonstrate the ability to work in a team environment
- Microsoft Office Product experience preferred
- Must be able to work in a strictly confidential manner
- Min 3 years experience in Team Leader role in manufacturing preferable automotive industry
38
Production Supervisor Resume Examples & Samples
- Provide leadership and direction with emphasis on team building through daily toolbox meetings, effective communications, and in developing an efficient team that is responsive to production requirements
- Establish maintenance work schedules taking into account customer requirements, resource availability, and other priorities
- Control quality, productivity and process flow to meet customer requirements while ensuring a high level of customer satisfaction
39
Production Supervisor Resume Examples & Samples
- Experience in a production plant supervisory position in the Chemical Industry
- Experience in implementing & using continuous improvement tools and techniques
- Experience supervising plant preventive maintenance programmes & implementing SHE policies & procedures
- Good Communication, Reporting, Presentation and analytical skills
- Excellent IT skills, experience with MRP systems - planning and scheduling of work
- Supervision of manufacturing personnel: This includes attendance, performance appraisal & role function management. Developing training plans for the manufacturing personnel. Recruitment & probation management. Supervise & support the day to day tasks of the manufacturing department
- Production order fulfilment: Implementing a master production schedule system and achieve efficient production plans
- Performance monitoring: Establish key performance indicators. Provide feedback & reports to the manufacturing department & other key personnel. Use continuous improvement tools to instigate actions for improvements. This includes feedback from Quality, Customer Service, Environmental & H&S audits
- Process improvement: Drive process improvements to impact costs and improve competitive advantage, using key tools and techniques to enable success. Implement a Total Productive Maintenance program to improve plant and tool availability and support H&S improvement targets
- Stock accuracy: Supervise the accurate storage, usage and clear down of raw materials and packaging used in the production process. Maintains inventory accuracy by conducting organised cycle counts as required
- Month End: Introduce a Clear down procedure & Analysis of Production Route cards & Reports, introducing improvement projects from findings
- Governance: Actively manage the requirements of the Health & Safety & environmental policy within the manufacturing department
- ITC Integration: Develop, integrate & use all of our IT structures to strengthen our business intelligence & communication
- Branding: Ensure within the manufacturing department that the essence, integrity & growth of our brand is delivered in line with the brand strategy
- New business integration: Work in a multi-disciplinary team of people to manage the process of integrating new products or procedures arising from the acquisition of new business
40
Production Supervisor Resume Examples & Samples
- Strong planning, organizational, problem solving, professional verbal & written communication, and relationship building skills are essential
- A desire to be the hands-on collaborator in a manufacturing facility
- Experience and passion for working in a lean manufacturing environment
41
Production Supervisor Resume Examples & Samples
- Organisation and co-ordination of a production team to manufacture quality product on schedule and in a safe and efficient manner in compliance with GMP
- Initiate and drive production and quality improvement projects in line with the Company requirements
- Communicate with other shifts and key stakeholders through effective shift handovers
- Escalate issues as they occur to appropriate team members in a timely manner
- Develop and execute training plans for reportees to ensure adequate cover is always available for all processes on shift
- Drive elimination of waste projects with an emphasis on yield improvement
- Collaborate with interdepartmental colleagues on lean manufacturing projects to improve productivity, efficiency and quality standards
- Responsible for the planning and scheduling of multiple products in accordance with customer lead times
- Demonstrate strong problem solving abilities
- Management of production resources for example people, equipment, time, etc
- Communicate with other teams on production related issues
- Maintain positive employee relations
- Completion of timely performance reviews and appraisals
- Recruitment of production employees in conjunction with HR
- Implement company policies in conjunction with HR
- Formulate and implement training plans to meet compliance, versatility and development needs
- Maintain a very high standard of housekeeping and GMP compliance
- Develop a strong team culture through communications and team leadership
- Perform operations in accordance with established safe working procedures, regulations, standards and general safety rules, ensuring that attention is given to special hazards associated with the particular area of work
- Provide information on environmental, health and safety issues to all team members
- Report and document all incidents / accidents which may occur during the course of work and carry out and assist in al investigations and follow-up
- To take on other duties which the Company may assign you from time to time
- Minimum of 3 years' experience as a production supervisor or similar role
- Demonstrated organisational and planning abilities
- Production Supervisor - Evening Shift
- Experience of Quality Systems, Lean Manufacturing or six sigma an advantage
- Strong leadership, inter-personal and team skills
- Technical aptitude
- Ability to work on own initiative
- A relevant qualification is desirable (manufacturing management / or production /
- Engineering related discipline)
- Medical device background a distinct advantage
42
Production Supervisor Resume Examples & Samples
- Liaising with line trainer to develop a training program to ensure smooth operation of department, development of product builders, health & safety of personnel
- Interacting and liaising with the other manufacturing teams and Logistics to prioritise backorders
- Establish and support a work environment of continuous improvement that supports the internal Quality Policy, Quality System and the appropriate regulations for the area they support. Ensure employees are trained to do their work and their training is documented
43
Production Supervisor Resume Examples & Samples
- First AID/ AED certification
- Auto components manufacturing experience with a minimal of 3 years’ experience as a Team Leader
- A minimum of 2 years’ experience in production management/ supervising
- Demonstrated interpersonal conflict resolution and leadership skills
- Demonstrated ability to lead by example and be fair and consistent
44
Production Supervisor Resume Examples & Samples
- Reduce OSHA Incident Rate and attain compliance through weekly safety audits, monthly safety meetings, required safety training, implementation of 5S practices, identification of chemicals and containers, root cause correction, and enforcement of all regulatory and management policies and procedures
- Improve product quality through assurance of operator capability and compliance to specifications
- Candidate must manage time constraints, availability of technical resources and various operator skill levels
- Decrease product cost through continuous improvement activities, effective utilization of manpower, machines, materials, and methods
- Candidate must manage material availability, labor resources, and capital resources
- Ensure compliance with environmental requirements through control of hazardous waste by training and directing designated employees to handle hazardous waste generated in the department, and compliance with applicable environmental permits, regulations, policies and procedures
- Achieve Production schedule through scheduling of material, manpower, and equipment
- Candidate must manage material availability, manpower resources, and multiple sources of information
- Effectively communicate with associate team: accomplishments, short term plans, issues, and training, via shift start-up meetings
- Apply effective feedback and develop team associates
- Effectively plan, contribute, and execute plans to accomplish yearly cell objectives
45
Production Supervisor Resume Examples & Samples
- Develops and implements action plans to meet department goals in the areas of labor efficiency, labor utilization, housekeeping, and productivity improvements
- Supervises the job performance of employees on assigned shift, making sure their work runs on schedule and meets company standards for safety, quality, production, and waste
- Works on continuous improvement projects
- Works with engineering and maintenance departments relative to modification of processes and equipment in order to improve production and quality of products
- Perform regular daily audits of key processes to ensure optimum process performance
- Measures and evaluates employee performance according to company standards for quality, productivity, and career advancement
- Ensure that there is an adequate distribution of skills to enable production plan to be achieved effectively
- Actively builds leads and production employee skill set to create a cross functional workforce and increase efficiencies
- Stimulate teamwork within his/her departments. Creates a fair and positive environment that fosters a solid work ethic and maintains a good team attitude within the group
- Ensure his/her departments are a safe work environment
- Leads activities to communicate and maintain adherence to company policies, safety standards, and good housekeeping practices
46
Production Supervisor Resume Examples & Samples
- 5+ years of experience as a Production Coordinator
- Demonstrated ability to effectively foster relationships
- Ability to create and manage department specific production schedules
- Demonstrated ability to multitask in a fast-paced production environment
- Software requirements: Microsoft Word and Excel, Gmail and knowledge of production tracking databases such as Shotgun is preferred
47
Production Supervisor Resume Examples & Samples
- Fully accountable for Health & Safety and responsible for the development and continuous evolution of the Health &Safety culture
- Ensuring a consistently high quality product is produced on time in full
- Fully responsible for the staffing plan and ensuring team optimisation and the control of fixed costs
- Lead and develop the team and ensure ongoing coaching and mentoring is provided in order to continually enhance skills and knowledge to meet the demands of the business now and in the future
- Fully accountable for performance management of team including carrying out performance reviews and corrective action meetings
- Oversee the execution of the CBP on a continuous basis
- Ensure efficiency and scrap targets are met
- Responsible for training adherence and ensuring absence and overtime targets are met
- Positively interacts with internal and external customers at all times
- Ensure there is a comprehensive program of continuous improvement in place to improve quality, performance, efficiency and reduce costs through kaizens
- Continuously strive to improve employee engagement and ensure efficient and effective communication at all times
- Drive and promote our core values and behaviours
- Previous experience of leading and managing teams in a manufacturing environment is essential
- Must be able to demonstrate personal leadership experience and understand the importance of positive employee engagement
- Have excellent working knowledge of manufacturing and industry "best practice"
- Have a high level of business awareness, be action oriented complemented by the resilience to achieve challenging objectives
- Strong interpersonal skills, an innate ability to influence and build relationships at all levels and a driving vision to create an inclusive culture of performance, continuous improvement and development
- Must be a pro-active self-starter and an excellent communicator with exceptional problem solving skills
- Honours level degree required (FETAC Level 8)
- Should have evidence of continuing professional development
48
Production Supervisor Resume Examples & Samples
- The Production Supervisor is responsible to oversee the Associates and ensure safety, productivity and quality for the facility on their shift
- Continually monitor inventory and staffing levels to ensure that production schedules can be met
- Give direction and support to the Cell Leaders as required
- Ensure that all Cell Leaders have and understand applicable procedures, equipment and check fixtures
- With Cell Leaders, conduct performance reviews on all employees
- Work with Cell Leaders to co-ordinate activities within the team in accordance with daily production schedules and initiate changes to the production schedules as necessary
- Ensure that all departments are co-operative in ensuring accordance of plant safety rules
- Work with Cell Leaders to resolve any quality problems that arise effectively and efficiently
- Ensure containment of any non conforming product and initiate the NCMR process and involve Quality Engineering where required
- Assume the Operation Manager’s responsibilities and duties in his/her absence
- Any reasonable request by other levels of management. Perform other duties as assigned
- Make sure all necessary departmental communication is passed on to the Production Supervisor coming on duty
- Understand the current status of all processes and equipment throughout the facility and involve the proper disciplines in problem resolution
- Focus on, and drive the mindset of Continuous Improvement throughout the operation
- Responsibilities for standardized work; including: lead the development of SW and buy-off, incorporate appropriate product quality standards into standardized work, post and maintain SW at the job, audit SW to ensure adherence, train Cell Leaders and Associates in SW, analyze recommendations for improvements, improve SW (eliminate waste), review changes in SW with Production Manager and interface with support people to accomplish changes in SW
- Monitor and maintain production levels according to schedule
- Conduct bi-weekly team meetings
- Ongoing understanding of key factor results such as scrap rates, downtime and efficiencies
- Ensure housekeeping, 5S standards are maintained throughout the facility
- Ensure that all equipment and process capacities are being maximized to achieve peak efficiencies and give direction in this area as required
- Conduct daily meetings with Cell Leaders to understand and set priorities based on the needs of the business
- Make decisions regarding the operation based on a combination of customer’s needs, needs of the business and the needs of the employees
- Assume Cell Leader responsibilities for assigned workcell
- Comply with and ensure all employees adhere to all policies and procedures as outlined in the Employee Handbook
- Comply with and ensure all employees adhere to QS9000 Operating Procedures
- Completion of Secondary School is required
- Completion of Post-Secondary Diploma is an asset
- 2 - 4 years’ experience in a supervisory role or demonstrated equivalent required
- Must have excellent interpersonal skills
- Must have excellent oral and written communication skills
- Must be able to work flexible hours and be willing to work overtime, as required
- Strong understanding of the manufacturing process
- Strong computer skills, including Microsoft Excel and Word
- Strong leadership skills to support the business needs
- Strong trouble shooting and reasoning ability
- Strong organizational, self- starter and prioritizing abilities
49
Production Supervisor Resume Examples & Samples
- 1) Maintain production to meet planned output
- 2) Identify and implement manufacturing process improvements within Oakley
- 3) Lead teams to participate in manufacturing quality initiatives
- 4) Establish production order and material inventory accuracy
- 5) Resolve production and quality issues by using root cause and corrective action strategy
- 6) Provide departmental leadership and direction to build a high performing team and a world-class operation
- Work closely with Planning, Operations, Manufacturing, Tech Support, and Quality teams to keep informed about their business issues and needs, in order to create processes that support those needs
- Provide leadership, direction, and development opportunities for team(s)
- Measure and report team performance through the use of computer and system tools and resources
- Manage and/or develop and/or maintain the systems and process infrastructure supporting the manufacturing process, involving appropriate departments as required
- Process auditing to eliminate non-value add activities
- Set priorities based on work order schedules
- Foster positive and effective interdepartmental communication and teamwork
- Give appropriate and timely feedback to team members, peers, and management
- Collect and optimize standard work
- Effectively coach team(s) to continuously improve processes
- Ability to understand, monitor, and react to analysis of cost/scrap data
- Initiate changes and improvements as opportunities are identified
- Produces daily performance reports, and explain root cause(s) of short production occurrences
- Ensure that team members are cross-trained in multiple job functions
- Maintain 5s principles and an ergonomically safe work environment for team(s)
- Promote clean, safe work areas throughout plant by continuously checking for hazardous conditions
- Consistently administer and hold your team accountable to company policies and practices regarding attendance, performance etc
50
Production Supervisor Resume Examples & Samples
- Health and Safety
- Technical College/University education Engineering or Certified Machinist
- Knowledge of safety standards (OHSA and Industrial Accident Investigation Report)
- Must have working knowledge of Industrial Equipment Risk Assessment and Workplace Inspection
- Strong working knowledge of lean manufacturing principles
- Knowledge of GD&T and SPC
- Capable of troubleshooting processes and tooling
- Computer literacy and software applications (ie., Microsoft Office)
- At least 3-5 years supervisory experience in a manufacturing environment, preferably automotive
- Must be a team player, communicate well with others. Interact with people at all levels and departments
- Must have good organizational skills, and display a positive attitude towards new ideas
- Proven team player with good leadership skills to ensure Company’s objectives are achieved by personnel assigned under his/her care
- Must be familiar with TS16949 and ISO14001 procedures
- Must be quality/cost conscious
51
Production Supervisor Resume Examples & Samples
- 1) Follow and enforce all plant safety rules and policies
- 2) Ensure daily pre-shift inspections are completed, conduct unplanned inspection audits on a weekly basis and planned inspection audits once a month
- 3) Routinely make visual inspections of emergency evacuations routes correcting any safety concerns immediately
- 4) Within 24 hours of an accident/incident complete accident investigations identifying root cause and corrective action
- 5) Ensure weekly safety talks in pre-shift meetings are being conducted with team members signing safety training roster
- 6) Understand and promote Magna’s philosophies and Employee’s Charter
- 7) Schedule, supervise, coordinate, and direct the activities of team members to ensure that production levels and quality standards are met
- 8) Establish and maintain effective communications with all other departments as well as conduct all business activities in a professional manner
- 9) Plan and direct the utilization and use of all equipment and manpower to achieve the most effective results
- 10) Supervise team members in accordance with the principles of the Employee Charter and the policies and procedures set out in the BGM Team Member Handbook
- 11) Promote continuous improvement and capitalize cost reduction opportunities
- 12) Act on behalf of the Department Leader and/or Assistant Department Leader in their absence and assume the responsibilities of Team Leader in their absence
- 13) Immediately attend to all accidents and injuries and initiate the accident and injury investigation program, while following up to ensure procedure implementation and completion
- 14) Supervise Team Leaders in their job performance and ensure fulfillment of policies, practices and procedures
- 15) Utilize interactive management principles when implementing corrective discipline procedures in dealing with team members, encourage professional development to enhance team performance, and cross train to maximize flexibility and coverage to accommodate vacations and absences
- 16) Provide timely coaching, counseling, and feedback to employees through one-on-one sessions, performance evaluations, and regular team meetings
- 17) Follow and comply with all operational procedures/policies as stated in the employee Environmental Health and Safety programs and conduct Team Safety Talks as required
- 18) Promote good housekeeping
- 19) Perform other duties as required
- Computer skills; Basic knowledge of Microsoft Word and Excel
- Must possess working knowledge and understanding of the assembly process
- Must possess working knowledge and understanding of quality systems, standards, and procedures
- Must have strong team-focused, interpersonal and leadership abilities
- Must be willing to work extended or flexible hours as required to meet external and internal customer requirements
- Must be willing to work in various locations within and outside the facility
- Must be able to pay good attention to detail
- Must possess good human relations, leadership skills, and a maturity of judgment
- Must have good organizational and problem-solving skills
- Ability to operate and maintain all machinery and equipment in his/her assigned area
52
Production Supervisor Resume Examples & Samples
- Managing people, building effective teams and developing direct reports
- Drive to achieve operational excellence, consistently meeting manufacturing sales, quality, delivery goals and driving productivity and cost of sales improvements
- Driving a culture of safety in a production environment
- Production planning, scheduling and management
- Commitment to leading continuous improvement
- Ability to effectively influence others
- Accountability and Teamwork
- Strong communications skills
- Responsible for several components of a project or a complex component of a larger project
- Contributes to their team or department by applying their knowledge of one or more functional areas
- Fully developed professional able to work without direct guidance or direction from others
- Has in depth knowledge of the discipline and role
53
Production Supervisor Resume Examples & Samples
- Lead production employees to perform in a proficient manner, providing motivation through personal example and interpersonal skills
- Ensure employees are following all safety and operating procedures
- One plus years supervisory experience preferred
54
Production Supervisor Resume Examples & Samples
- Effectively communicate with employees and other shift key personnel
- Oversee workflow based on weekly schedule and collaborate with the scheduler in determining both staffing requirements and the finite schedule
- Develop, implement and manage departmental goals and objectives
- Maintain Inventory Accuracy and address discrepancies
- Increase productivity, labour variance and quality through Process Improvement based on current acceptable standards
- Complete performance reviews
- Resolve manufacturing issues resulting from human error, equipment failure, product/component quality, and schedule changes
- Daily attendance, employee information forms, vacation planning, payroll exception reports, weekly production reports
- Performs other related duties as assigned by Management
- Education: College Diploma (minimum), University Degree preferred
- Experience: Previous Supervisory experience preferred
- Competencies: Experience in cosmetics, pharmaceuticals or food industries
55
Production Supervisor Resume Examples & Samples
- Coordinate and supervise department to achieve the production objectives of work plans and continuous improvement
- Regulate and manage overtime, annual leave and training ensuring that all regulations and plans are adhered to
- Support operators in minimising equipment downtime
- Ensure appropriate risk assessment and 'Permit to Work' procedures are in place and adhered to
- Participate actively in all operational and continuous improvement meetings scheduled
- Collaborate in internal and external audits
- Liaise with shipping/warehousing/quality and other departments as necessary
- Assimilate, co-ordinate and share appropriately all information relating to production & QHSE objectives
- Ensure general production office administration and documentation is correctly completed
- Develop alternative measures and contingency plans to support the production process
- 3rd level degree (or equivalent) in related field
- This role requires a demonstrated aptitude for decision making and the ability to delegate responsibility appropriately
- Knowledge of ISO/HACCP and Safety Systems
- Demonstrated accuracy and attention to detail in work
- Commitment, persistence and ability to overcome setbacks and get the job done
- Effective communication skills
- Ability to work under pressure and to tight deadlines
- Ability to communicate effectively both written and verbal with a variety of internal / external contacts
- Demonstrated aptitude for decision making and delegate's responsibility appropriately
56
Production Supervisor Resume Examples & Samples
- Ensures MPS principles of standardization and one piece flow are established and enforced
- Responsible and accountable to manage, support and provide direction to all staff within the department – including Performance Reviews and Employee Development Plans, if applicable
- Holds Others Accountable
- Resolves Conflict
- Trains Others
- Evaluates
- Focuses on Continuous Improvement
- Responds Appropriately to Crisis Situations
- Approachable
- Assertive
- Tactful
57
Production Supervisor Resume Examples & Samples
- Facilitate Continuous Improvement
- Continuously improve standards set by facilitating and executing Problem Solving/Problem Solving Group (PSG) activity within the area. Conduct training and periodic assessments to ensure process is being followed
- Short Interval Management (SIM) Process
- Check that standards set within the shift (Spray Drying and Packing technologies) are adhered to through SIM Process - layered confirmation
- Manage Labour
- Schedule and plan resource requirements for the Spray Drying and Packaging Areas based on the production plan and schedule and plan labour accordingly. Optimise labour allocation through continual communication internally
- Cover essential elements of Production Manager and Team Leader Role in the event of unplanned absence
- Manage process reliability
- Monitor & Improve OE through companies System. Identification of bottlenecks within the process, report and conduct problem solving with relevant team members
- Manage Quality
- Maintain product quality and adherence to Quality Systems through management of the team and process to deliver agreed product specifications as defined in quality standards and policies
- Manage Health and Safety
- Protect the health and safety of all employees through instituting and adherence to site 'Safety First' culture. Utilise the SAT (Safety Action Team) and SIM (Short Internal Management) Process to proactively improve safety within the production area
- Analyse & report conversion performance metrics
- Through analysis of Performance Data, identify performance gaps, trends and improvement opportunities and communicate internally using visual management standards in the areas
- Build Sustainability through people
- Exhibit passion for people growth, engage and align all team members to achieve individual roles, function and optimal company performance
58
Production Supervisor Resume Examples & Samples
- Quality Control
- EH&S Coordinator, (Communicate and administer EH&S Policy as required)
- First Pass Yields
- EH&S and 5S Checklists
- Turnbacks
59
Production Supervisor Resume Examples & Samples
- Manage & coordinate Production Studio workload in recording and producing
- Liaise daily with the Creative Department to ensure communication and workflow are at maximum efficiently
- Oversee and maintain all equipment in both the recording and production studios
- Communicate with the Production Manager on any issues or situations concerning your department
- Other duties as assigned by Production Manager
- Must have a minimum of 10 years Production experience
- Display a genuine interest and knowledge of our brands. (Virgin/BOB/TSN)
- Bell Media is Music First – so music production experience is an asset
- Imaging experience in CHR, Classic Hits, Sports Talk, and Country music formats
- Jingle Music Production an asset
- Must love working in a team environment
- Must be a quick-learner and over-achiever
- Ability to work under pressure with initiative and problem-solving capabilities
- Computer literacy is mandatory
- Computer Network/IT knowledge is an asset
- Must be a wizard of Wide Orbit Automation
- Proficient at both Pro Tools, and Adobe Audition
- Working understanding of mixers and production equipment
60
Production Supervisor Resume Examples & Samples
- Directly supervise subordinates to perform day-to-day tasks to provide timely and quality production in efficient manner
- Coordinates with employees to meet projected schedules; monitors progress and updates management; resolves day-to-day conflicts that could jeopardize the work
- Oversees work performance to assure specifications are met; and generally keeps production running in a timely manner
- Maintains close surveillance to assure scheduled work flow and best utilization of people, skills, and equipment
- Works to continually improve quality and output
- Requires dedication and focused concentration for extended time periods
- Satisfactory performance requires broad skills and abilities and good knowledge of manual assembly high volume production technology and methodology as well as good understanding of company products and operating concepts
- Stays abreast of the latest production techniques and company products by reading trade journals, attending training sessions and seminars, business meeting, and trade association meetings. Spends the majority of time in the assigned production work area resolving work issues
- Training of employees is an on-going responsibility and requires coaching, cross-training, and continuing assistance
- Sometimes works with confidential data requiring care to protect
- 2 - 3 years of direct industry experience (Inserting)
- 1 - 2 years direct supervisory experence
- An associate degree in industrial management or related is preferred
- Requires broad skills/abilities and very good knowledge of manual/assembly production tech. and methods
- Good skills in communications/writing; professional manner/tact dealing with others
- Requires good organizational skills/ability to stay in control and maintain even handed approach while working with continually changing multi tasks in a deadline work environment
61
Production Supervisor Resume Examples & Samples
- 4 - 6 years of direct mail experience
- 1-3 years management/supervisory experience
- Scheduling and planning skills and abilities and
- Strong knowledge of production control technology and methodology
- Professional manner/tact dealing with others
- Strong organizational skills and ability to stay in control while working in a continually changing, deadline driven work environment
- Strong PC skills
- Associates Degree in Industrial Technology, Material Management, or related field
- Knowledge of mail insertion procedures and postal regulations
62
Production Supervisor Resume Examples & Samples
- To evaluate and improve bottlenecks in manufacturing areas as internal leader of capital projects and capacity maximization
- To implement opportunities identified in their areas through root cause problem solving tools
- To manage the manufacturing process to ensure work standards and KORE requirements
- To ensure optimal execution of production schedule by reducing scrap and increasing productivity
- To evaluate and monitor the process performance on real-time (OEE)
- To live OE culture by implementing and sustaining OE tools
- To lead routines of process performance review
- To manage operators’ development and performance and to ensure they are properly scheduled according to their skills and competences
- Knowledge of Good Manufacturing Practices (GMP’s)
- Concepts of Quality and safety
- Continuous improvement (Analytical problem solving tools)
- Concepts of Lean Manufacturing
- Statistical Process Control
- HACCP
- MRP II
- Volume of Production Costs and Logistics
- Spanish
- Internal & External Communication
- COMPETENCIES
- Balances Immediate and Long Term Priorities
- Deliver Results
- Develops and Inspires Others
- Drives Innovative Business Improvement
- Imports and Export Good Ideas
- Lives the Values
- Networking
- Use of Technology
- Self-Management
- Boundary Management
63
Production Supervisor Resume Examples & Samples
- Instil an attitude of a fair and happy working environment
- Facilitating open two-way communications regarding individual, team and company performance through weekly team meetings,
- Employee selection as well as being in charge of dismissals
- Planning - including developing training for staff
- Cross functional communications to ensure prompt shipment of product
- Administration duties which include Time and Attendance system
- Establish and support a work environment of continuous improvement that supports BSC's Quality Policy, Quality System and the appropriate regulations for the area they support
64
Production Supervisor Resume Examples & Samples
- Direct the functions of the department including job assignments, goal setting, and maintaining consistent job standards
- Promote and support continuous improvement initiatives that focus on safety, quality, delivery and cost
- Implement production schedules as provided by cell schedulers for the shift to assure adequate throughput and maintain on-time deliveries
- Manage labor approval process with emphasis on appropriate approvals and system accuracy
- Communicate and enforce the company policies and/or the union contract relative to all associates
- Assist in identifying and implementing irreversible corrective action strategies with Lead Supervisor, Manufacturing Engineering and Quality and assure flow-down to all affected associates
- Participate in the development and improvement of new processes, tools, fixtures and designs
- Assure good departmental housekeeping and a safe work environment. Meet or exceed OSHA and EPA standards and requirements
- Maintain a cost effective department through continuous communications with all associates
65
Production Supervisor Resume Examples & Samples
- Production
- Planning & Scheduling
- Tool & Die
- Design and sequence of operations
- Industrial Engineering
66
Production Supervisor Resume Examples & Samples
- Responsible for raw material receipt, production & shipment of high quality medical devices
- Ensure that all Quality system procedures and manufacturing procedures are adhered to in order to produce quality product
- Ensure that output targets based on capacity plans are attained
- Ensure that a high standard of compliance with GMP is maintained in the manufacturing areas
- Ensure that changes to relevant procedures/instructions are relayed to those affected in production
- Ensure that training needs of employees in the manufacturing area are constantly reviewed and that required training is given as appropriate
- Ensure that all LMS training is up to date within the MBU
- Monitor employee performance and carry out performance appraisals with employees
- Maintain excellent communication channels with the production & distribution teams and with other departments through regular updates
- Work closely with other functions to meet delivery requirements
- Work on actions from assigned customer complaints, NCR's, actions from internal/external audits and CAPA's and determine root cause
- Monitornon conformances and rework to ensure they are kept to a minimum
- Highlight vendor issues, process issues, compliance issues to the relevant departments
- Participate in Product Transfer and Product Development cross functional teams to ensure production readiness to implement new products into manufacturing, this will involve preparing/reviewing manufacturing instructions and Bills of Materials (BOM's)
- Ensure adherence to all environmental, health & safety requirements in accordance with company policy
- Act as designee for Production Manager as appropriate
- Ensure that Code of Conduct is considered in all business matters carried out on Cook's behalf
- Formal production/engineering qualification and/or relevant manufacturing experience (medical devices, plastics, etc.)
- Minimum 5 years previous experience in a supervisory position
- Knowledge of medical device quality standards ISO13485/FDA practices and GMP or similar regulated industry standards
- Good computer skills including knowledge of Microsoft® Office
- Excellent organisational and team building skills
- High self-motivation
67
Production Supervisor Resume Examples & Samples
- Manage production control of high speed inserting equipment and mail meter machines
- Review through-put records of staff to monitor individual performance and increase the business unit’s productivity
- Manage Quality Control staff. Oversee inventory control for 200+ clients
- Perform duties and manage production control activities for production scheduling, production expediting, and control operations to achieve production goals and conformance with delivery date commitments
- Participate in planning meetings to assist in determining the scope and objectives for production control
- May be assigned responsibility for preparing a master schedule to conform with delivery dates, production capacities, available personnel, etc
- Maintain surveillance over orders in process to keep informed of production status and, when needed initiate necessary steps to correct
- Personally supervise and expedite rush orders and material shortages and revise schedules to offset delays
- Utilize trade journals, trade association business meetings and seminars to stay abreast of latest technologies and methodologies
- Perform independently without supervision except for difficult assignments
- Problem solve through research, investigation, inquiry, analysis, and evaluation. Develop and/or assemble all necessary work information
68
Production Supervisor Resume Examples & Samples
- Work with the CG Supervisor, Production Manager, Producer(s) and Studio Executives to measure and manage creative scope and technical processes within schedule and budget parameters while evaluating available resources, performance priorities, and schedule implications for all sets
- Directly manage the personnel, inventory, and process for the Assembly/Set Dressing Dept in partnership with the Assembly Supervisor
- Manage and drive the Enviro Group set building process, working with character leads from each discipline to determine creative and technical requirements as well as holding individuals and teams to deadlines
- Oversee and manage schedules for the confluence of deliverables, mediating between departments when necessary
- Provide continual awareness of opportunities for efficiency through asset reuse and variation. Evaluate Designs and Layout at the earliest opportunity to ensure feasibility
- Work with all relevant departments to establish standards of deliverables, mediating between departments when necessary
- Work with relevant depts. to ensure feasibility of set execution through Final Rendering
- Track, analyze, and report on department trends regarding productivity, hitting of deadlines, long range planning, heavy multi-tasking, and schedule coordination responsibilities
- Work with artistic and technical leadership on coaching and managing the team(s) towards production and individual performance expectations. This could include participation in yearly performance reviews
- Must possess the experience and proper judgment for the dissemination of information. Understand the proper forum for the dissemination of information and is skilled at determining which information is acceptable for wider publication and when
- This candidate has on-going contact with the Producers, Directors, and studio executives and must be skilled at the quick analysis and reporting required to explain daily/weekly challenges and solutions
- Position may require offset or extra hours depending upon the demands of production
69
Production Supervisor Resume Examples & Samples
- Manage and supervise an assembly team to meet objectives for Safety, Quality, Cost, Yield, and Output. Direct management and supervision of production staff and contingent assembly staff
- Manage hiring, orienting, and training of production employees and staff
- Establish and promote a positive work environment that drives high quality, safe operations, and dependable output. Work with process and manufacturing engineering to maintain work flow, and monitoring steps of the process
- Collaborate with cross functional groups for production planning and scheduling
- Monitor progress, revise schedules, resolve problems, and report results of shift production. Maintain quality by promoting and enforcing organization standards
- Maximize uptime of equipment and facility by following operation and maintenance protocols
- Measure, collect, analyze, maintain, and report on all production metrics and key performance indicators. Contribute to continuous improvements in all areas of production
70
Production Supervisor Resume Examples & Samples
- Ensure that production is efficient and effective with high level of employee engagement
- Actively participate in day to day leadership of the business unit, and positively contribute to the business unit team, driving engagement activities
- Lead / participate in continuous improvement activities, e.g. Lean/Cost Reduction initiatives
- A minimum of two/three years supervisory/people management experience in a high volume manufacturing environment is desirable
- Third level technical qualification or extensive experience in a technical environment an advantage
- Production process troubleshooting experience required
- Dynamic "hands-on" individual prepared to take responsibility
- Knowledge of ISO/QS9000 and FDA Quality standards
- Good working knowledge of MRP
- High level of PC skills required
- Self starter with demonstrated efficient work methods, analytical & problem solving skills and ability to handle multiple tasks in a fast paced environment
- Capable of working as part of a multi-disciplined team
71
Production Supervisor Resume Examples & Samples
- Lead and direct the Company health and safety objectives and support the company’s health and safety directives to provide a safe and healthful workplace for all employees, this includes
- Regulatory compliance with local, state and federal legislations
- Establishing plant-wide measurable and goals that meet or exceed industry standards, and are monitored, tracked and audited on a regular basis and communicated to employees
- Recognition of accomplishments/milestone in the areas of safety, environmental, ergonomics and employee wellness
- Development of effective programs that increase employee awareness and involvement in the areas of safety, environmental, ergonomics and employee wellness
- Accountability of supervisors for enforcing safety rules and implementing the necessary training and corrective actions to ensure proper focus on established objectives
- Lead and direct Just-In-Time assembly and other operations for health and safety, quality, customer satisfaction, cost, productivity, environmental and ergonomic issues through to resolution utilizing problem solving processes (e.g. 8D, 5Y,etc.)
- Maintain effective communication with assembly operators via pre-shift and individual meetings regarding company policies, procedures, work instruction, company rules, process documentation and environmental regulations
- Review all production objectives and coordinate objectives with production procedures in cooperation with other management/supervision personnel to maximize product reliability and minimize costs
- Lead by example with safety including utilizing appropriate Personal Protective Equipment (PPE) at all times
- Supervise AIM Systems-Warren direct labor to include training and development, communication, enforcement of company policies and procedures, performance coaching and evaluation and written documentation of performance issues in a timely manner. (e.g. performance reviews, performance improvement plans, etc.)
- Schedule and assign appropriate tasks to achieve daily production, quality and housekeeping goals
- Maintain an open and honest relationship with dignity and respect with all employees in accordance with the Employee Charter Open Door Process
- Recommend plant measurables and continuous improvement of quality, equipment performance and productivity
- React and follow through with all quality issues to ensure that no defective products are shipped to the customer
- Immediately attend to all accidents and injuries, and initiate the accident/incident investigation process. Facilitate the determining root cause(s), corrective action(s) and follow up to ensure implementation and completion of corrective actions
- Correct unsafe acts and conditions
- Coordinate and/or deliver training to current and new employee Just-In-Time operations following established operating procedures
- Manage and coordinate cross-training activities to improve ergonomics and employee skill development
- Maintain and promote good housekeeping utilizing (5S)
- Liaise with other shifts to communicate quality, production, safety and/or supplier problems/issues
- Minimum of 5 years of automotive manufacturing environment
- Minimum of 3 years of supervisory experience desired
- Demonstrated oral and written communication skills, as well as, strong organization skills
- Personal computer skills
- Understanding of manufacturing, assembly, sequencing and equipment principles
- PC Training
- Forklift Training (not required)
- Employee Charter
- Bailer Training
- Interpersonal Communication
- ISO/TS16949:2002
- Personal Protective Equipment
- Ergonomics
- Safety Signs
- Lockout/Tagout
- Bond Cell Training
- Normal amount of sitting
- May be required to stand in excess of 6 hours
- May be required to lift, push and/or pull 60 pounds
- Able to conduct normal amount of work at a computer
- May require travel
72
Production Supervisor Resume Examples & Samples
- 5 years work related experience in a manufacturing environment
- Minimum 3 years supervisory experience preferred
- Sound knowledge of Health and Safety and the legal requirements of a Supervisor
73
Production Supervisor Resume Examples & Samples
- Responsible for the day to day supervision of production associates
- Establish a professional relationship with the associates in production
- Practice open and honest dialogue with the union when administering the UAW contract. Handle issues in a manner that will resolve them before they escalate to the grievance stage
- Ensure all associates have a safe environment in that all hazards, unsafe actions, or unsafe conditions have been identified, corrected, and/or eliminated
74
Production Supervisor Resume Examples & Samples
- Monitor and on occurrences; Be the first responder as secondary support
- Create a conducive work environment for the team(s) to complete their assigned responsibilities / tasks
- Basic administration of supervisory responsibilities and documents
75
Production Supervisor Resume Examples & Samples
- Reviews and negotiates on production goals and determines the most efficient way to achieve them through analyzing scenarios and collaborating with senior Production Management
- Develop procedures and methodologies to track, organize, improve and manage all aspects of their production process and methodology, responding as needs change. In partnership with the Production Manager, makes recommendations for improvement of the production process
- Day to Day operations/tasks within the department; Supervisor reviews, Director Reviews, etc
- Work with artistic and/or technical leadership on coaching/managing the team(s) towards meeting/exceeding production and individual performance expectations. This includes but is not limited to annual performance reviews
- Break-down production pipeline steps as they relate to the department with emphasis on the impact both up and down stream in the pipeline
- Communicate with leads & technical directors regarding deadlines and prepping shots for daily rounds
- Ensure that the correct processes are being followed and meetings are scheduled (handoffs, kickoffs, reviews, etc)
- Negotiate production solutions across departments up to and including the Director(s) and/or Studio Executives
- Track, analyze and report on department trends regarding productivity, quotas and long range planning
- Onboard new hires: Organize workstations, ensure proper training for studio processes (timesheets, vacation requests, lighting notes, etc.)
- PA/APM management, coaching and delegation, as appropriate
76
Production Supervisor Resume Examples & Samples
- 1+ years’ experience in Microsoft Office knowledge (Word/Excel/Outlook)
- 1+ years’ experience in a manufacturing environment
- Body shop /stamping / subassembly experience
77
Production Supervisor Resume Examples & Samples
- 1+ years’ experience in Microsoft products
- Body shop/stamping/Paint/subassembly experience preferred
- CNC machining experience (PTO specific
- Helium leak stand experience (PTO specific)
78
Production Supervisor Resume Examples & Samples
- 1 or more years of experience in Manufacturing
- Ability to work with limited supervision
- Ideal candidates should be able to demonstrate leadership in One FORD (leadership) behaviors combined with outstanding interpersonal, teambuilding, and communication skills
- Body shop/stamping/paint/subassembly experience preferred
79
Production Supervisor Resume Examples & Samples
- 3-5 years supervisory experience in manufacturing, preferably in the jewelry industry
- Computer skills including excel, word, powerpoint and database knowledge
- Experience with material review planning (MRP) systems
- Results-driven approach to manufacturing with demonstrated quality and cost improvements
- Saturdays and overtime as needed
- JD Edwards software
- Lean manufacturing principles and/or six-sigma experience
80
Production Supervisor Resume Examples & Samples
- Improve product quality through assurance of operator capability and compliance to specifications
- Manage time constraints, availability of technical resources and various operator skill levels
- Decrease product cost through continuous improvement activities, effective utilization of manpower, machines, materials, and methods
- Manage material availability, labor resources, and capital resources
81
Production Supervisor Resume Examples & Samples
- Production Supervisors participate in the day to day responsibilities of filming TV commercials for assigned clients within their area
- They will be responsible for capturing all necessary footage and audio as it relates to live shoots and may assist with the coordination of all logistics
- The Supervisor will have face to face time with clients and must manage shoots as needed on a per project basis at various budget levels across multiple categories
- At times the Producers will assist in interacting with TWCM’s most premier production clients to discuss creative concepts and other aspects of production relevant to the client
- This position will help or lead other Producers or Production Account Managers with routine assistance and guidance. They will provide coaching and performance Management, and they will perform work scheduling and determine project assignments. They will also oversee the quality of the work being performed by the team members to ensure the highest standards are being met. At times, they will also provide training to direct reports and other team members
- Responsible for collaborating on best practices and be able to bring capital expense needs/ideas to the table for their regions and enterprise ideas
- The Supervisor will serve as a backup to the Regional Production Director to help with TWC’s most advanced Production needs or clients
- The ideal candidate has 5-7 years of previous experience as a videographer and assisting in bringing creative concepts to life
- The Production Supervisor must have a proven track record of excellent filming/videography skills and the ability to assist in the development of high quality, creative and compelling concepts for advertising
- This position must coordinate with various internal and/or external partners to schedule and execute various types of productions while adhering to project deadlines and budgets
- Proven ability to manage several projects simultaneously
- Solid people management capabilities and must be well rounded in various aspect of Production. Previous experience managing others is preferred
- Strong understanding of production equipment
- Strong understanding of current process with an eye towards collaborating to improve and share best practices
- Strong understanding of production techniques in filming, time needed for projects and best practices for execution related to production services is essential
82
Production Supervisor Resume Examples & Samples
- Establishes and maintains effective communications/interaction with all other departments, including but not limited to engineering, quality assurance, maintenance, human resources. and material control support groups in order to achieve established targets
- Conducts all business activity in a professional manner consistent with the positive leadership practices of building trust, empowerment, and competitiveness, with emphasis on personal responsibility
- Plans and directs the utilization and use of all equipment and manpower to achieve the most effective results
- Understands, compiles and organizes operational data; using that data to implement improvements by working with teams and using lean tools and problem solving methods
- Responsible and accountable for meeting Presstran and departmental targets and goals
- Monitors and adjusts inventory balances as required, investigates inventory problems and implements solutions to source
- Participates in personnel requirements planning, overtime scheduling, etc
- Co-ordinates preventative maintenance with toolroom/maintenance depts. and production planner
- Promotes and recommends continuous improvement suggestions including environment, people, processes and equipment/machinery and ensures departmental CI's are implemented
- Monitors and completes required Layered Process Audits (LPA)
- Co-ordinates the movement of quarantine material/parts/scrap upon disposition by material buyer/quality assurance
- Follows and adheres to requirements of current customer quality and environmental management systems standards
- Supports other Area Leaders and Lead Hands in compliance with: the Presstran Health and Safety/Ergonomic/Environmental program/procedures; the Occupational Health and Safety Act and Regulation for Industrial Establishments and other relevant Codes and Standards; and participates in performing regular workplace inspections; ensures corrective actions; leads investigation in serious/critical incident/accidents
- Participates in the Return-to-Work program and ensures employees work within their RTW plan
- Proficient with Microsoft Office
- Ensures fairness to direct reports, and encourages and participates in the Open Door Resolution Process for employee relation issues
- Teach, coach and mentor Lead Hands for succession planning and enhancement of leadership knowledge and skills
- Effectively builds and fosters teamwork within the department
- Performance Management - teaches, coaches and mentors employees to meet company expectations
- Conducts performance appraisals informally or formally as required and ensures performance appraisals are completed for all employees
- Ensures employees are trained or certified, as required and participates in training programs as required
- Participates in the monthly departmental meetings
- Develops and maintains peer relationships
- Approaches each day and each challenge with a positive attitude
- Conducts themselves in a professional manner when receiving or giving feedback/information, whether it is positive or constructive
- Post-secondary education in a related field (e.g. Industrial Relations/Production Management/Manufacturing Engineering) and/or related work experience
- 3-5 years leadership experience
- Experience in operational improvements using Lean methods and techniques
- Must have a thorough knowledge of general office procedures including PC and LAN computer use. Must be proficient in relevant computer software and program use
- Experienced in Lean Implementation (standardized work), 5S, value stream mapping, A3 Method, etc.)
- Must possess human relations skills and maturity of judgement
- Demonstrated ability to motivate, mentor, and drive team to reach targets
- Must possess time management, leadership, strong communication, organizational and presentation skills (present to groups of up to 100 employees)
- Familiarity with weld assemblies and press operations
- Experience with recognized problem solving techniques (i.e. black belt)
83
Production Supervisor Resume Examples & Samples
- Work any shift as well as rotating shifts and weekends
- 3 or more months experience in Body shop/stamping/paint/subassembly
- 1+ years’ experience in Body shop/stamping/paint/subassembly
84
Production Supervisor Resume Examples & Samples
- A minimum of 5 years’ experience working in a production team within an Animation or VFX production. Additional experience in high-end television and/or related fields will be taken into consideration
- Specific experience in Animation, Assets and Layout will be an advantage
- Excellent scheduling, reporting, administrative and organisational skills
- Advanced knowledge of Microsoft office, and strong experience and database software and tracking
- Experience managing production staff
- Energy and enthusiasm for facilitating the work of artists in high pressure environments
- A passion for seeing the best possible pictures come to screen
- Ability to multi-task, prioritize and problem solve
- Highly developed written and oral communication skills and the ability to connect with a wide variety of personalities
- An ability to remain focused on the big picture without losing track of the details
85
Production Supervisor Resume Examples & Samples
- The Production Supervisor is responsible for the supervision of all processes, procedures, outputs and deliverables for their respective department(s) and ensuring the outputs and interactions of those departments are aligned with production needs
- A Production Supervisor is assigned to a specific department or group of departments and is an integral part of the management structure of that team or teams
- Assists the Production Manager and Associate Producer in assigning appropriate manpower and scheduling to ensure completion of their respective departments goals
- Responsible for the day to day running of their department(s), managing established schedules through production planning, coordination and troubleshooting
- Provides the department supervisors and artists with support to enable them to complete their work
- Supervises Production Coordinators within their department(s)
- Will work closely with other Production Supervisors to ensure that inventory moves smoothly from one department to the next
- Uses and contributes to the ongoing development of tracking/reporting documentation and in house tracking systems
- Completes special projects as needed or requested
- A minimum of 5 years experience working within a production team on VFX or Animated productions
- Exceptional scheduling skills
- Technical knowledge/experience of film formats, digital media and film techniques
- Advanced knowledge of Microsoft office, and strong experience with database and tracking software
- Sincere enthusiasm for facilitating the work of artists in high pressure environments
- A passion for Animated projects
- Strong administrative and organisational skills
86
Production Supervisor Resume Examples & Samples
- Monitor ANDON occurrences
- Verify that the line is running safely, smoothly, and producing quality parts
- Support Continuous Improvement and coach problem resolution to the lowest level
- Responsible for the daily material handling functions for the facility and for the department
- Provide direction and support in the allocation of resources in order to appropriately cover material handling responsibilities
- Support Production System and synchronous material flow through lean manufacturing practices
- 1+ years’ experience in Microsoft Office (Word/Excel/Outlook)
- 1+ years of experience in Body shop /stamping / subassembly, or manufacturing assembly and machining experience
- 1+ years of Safety and MP&L experience
87
Production Supervisor Resume Examples & Samples
- Perform all duties and promote themselves in a manner that reflects the P&F expectations, P&F’s vision/values through Magna’s Employee Charter
- Follow and abide by all government, legal, Magna and P&F rules and regulations
- Contribute to continuous improvement and cost reduction activities
- Participate in the monthly Team Member meetings and provide timely feedback on issues and concerns
- Report and Ensure accuracy of inventory and production
- Take over Accountability
- Initiate and follow up on delegated tasks
- Assist with dock audits
- Participate with inventory control
- Complete weekly “Layered Audits”
- Record downtime and analyze root cause
- Provide training and work instructions in the areas of, but not limited to, Health & Safety, TS 16949, ISO 14001, job specific etc
- Ensure that both OHSA and environmental legislative requirements are being met through regular workplace inspections and correcting all unsafe acts/conditions and environmental hazards
- Participate and deliver formal team member evaluation (Performance Appraisals) on time
- Manage Attendance Policy
- Involvement in Performance management of Team Members up to applying the Progressive Disciplinary Process effective, constructively, consistently and fairly
- Supervise, identify and recommend team member training i.e. on the job, formal to comply with job specific and legal requirements
- Active involvement in Manpower planning to meet production requirements i.e. overtime, new hires, temporary staff
- Promote fair and honest effort through teamwork
- Guide and encourage your team in improving uptime/productivity/throughput
- Provide the team with the right tools and knowledge to effectively build a quality product
- Promote, participate in and support Continuous Improvements
- Motivate and encourage positive, two-way friendly attitudes at all times
- Treat all team members equally, fairly, with dignity and respect
- Promote open, honest communication amongst one another
- Set a positive example for the Team at all times
- Answer Team Member questions as soon as possible
- Maintain Team Member confidentiality
- Provide each Team Member with performance feedback on a regular basis
- Encourage Team Members to discuss their questions, concerns and suggestions in a positive manner
- Have authority to stop production for quality reasons
- Have the right to refuse work based on safety or health concerns
- Ensure that safe and healthy conditions are met at area of responsibility
- Deliver Training of new hires, temporary staff and refresher training to existing employees utilizing P&F training standards by area
- Ensure high Quality Performance of all team members
- Maintain competency through training of employees including new employee training in department specific health and safety policies and procedures including emergencies, lockout, safe operation of equipment and personal protective equipment
- Delegation and follow up of tasks and responsibilities
- Develop Team Leads for possible succession
- Provide accountability for enforcing quality procedures, productivity expectations and safety rules and implementing the necessary training and corrective actions to ensure proper focus on established objectives
- Perform workplace audits of documentation, checklists and deficiencies to ensure pre-start up inspections are completed
- Min 5 years experience in Team Leader/Supervisor role in manufacturing preferable automotive industry
- Able to be flexible in hours of work in order to meet internal/external customer requirements. (scheduled and non-scheduled overtime shifts, etc)
- Able to rotate shifts
- BEST Supervisor Training or equivalent an asset
- Microsoft Office Systems
- Policy and Procedure administration
- Performance Feedback
- Emergency First Aid
- Compliance to all legal requirements
- S.H.A
- Lockout Training
- ISO-14001
- Accident Investigation
- Hazard Identification
- M.S
- Lean Manufacturing
- TS-16949
- Able to work effectively within a team environment
- Plans work and carries out task without detailed instructions
- Analyzes problems skillfully
- Shares critical information with everybody as needed
- Maintains high standards despite pressing deadlines
- Regularly produces accurate, thorough and professional work
- Completes work in a consistent and timely manner
- Takes personal responsibility for safety
- Treats all people with respect
- Seeks and considers diverse perspectives and ideas
- Provides a supportive work environment
- Demonstrates excellent knowledge of techniques, skills, equipment, procedures and materials
- Able to manage multiple projects
- Works to improve the performance of oneself and other by pursuing opportunities for continuous improvement and learning
- Prioritizing customer needs and demands
- Writes and speaks effectively using all necessary tools available
- Respects all external and internal customers
- Anticipates problems and sees through how a problem may affect others
- Is alert in a high risk environment
- Ability to read blue prints and drawings
- Able to work with others; build and maintain positive employee relations
- Must be dependable and organized including ability to prioritize and multi-task
- Able to interpret written report, correspondence, instructions, procedures and guidelines
- Able to communicate effectively
- Able to manage and schedule multiple priorities and meet deadlines
- Excellent knowledge and adherence to P&F Quality Standards and Processes
88
Production Supervisor Resume Examples & Samples
- Lead teams of Team Leaders and Production/Skilled Team Members in an automotive manufacturing environment to meet and exceed company goals and objectives
- Supervise/Manage the production process to ensure processes meet safety standards, quality standards, environmental, and OSHA regulations
- Allocate and mange staff and production resources
- Guiding, evaluation and supporting employees
- Optimizing production, production quality and the cost situation by recognizing the potential for rationalization as well as by improving workplace design and safety
- Recognizing and rectifying bottleneck situations
- Instructing the team in what the company’s objectives are
- Providing instruction and guidance about required techniques and regulations
- Controlling the deployment of personnel in unusual production situations
- Recording absence and presence of employees and teams
- Cooperation with Health & Safety and audit teams
- 4-7 years of experience in series production / lead employees
- Skilled worker in auto technology
- BS degree in business or related field
- Positive employee relations / team building
- Responsibility for personnel in technical industry
89
Production Supervisor Resume Examples & Samples
- Ability to work weekends as required by the manager or supervisor
- Excellent interpersonal skills needed for working in a team environment
- Ability to work all scheduled shifts, on time
- Numeracy skills
- Bi-lingual preferred
90
Production Supervisor Resume Examples & Samples
- Maintaining a safe work place
- Ensure production meets quality standards
- Maintaining an environment of continuous improvement
- Ensures necessary parts and materials are ordered and distributed in a timely and efficient manner
- Works to improve processes, timeliness and reduce costs by eliminating non-value added activities
- Implements various corporate initiatives such as 5S, Lean Manufacturing, 6 Sigma, Internal Certification, etc
- Accountability for value stream mapping
- Leads efforts to develop and deploy standard work for each work area
- Degree or diploma in Engineering or manufacturing related discipline
- 3- 10 yrs of experience in manufacturing plant with experience in production
- Thorough knowledge of Welding processes
- Good interpersonal and collaboration skills
- The desire to be part of a World Class Team
- Good communication in English
- Familiar with Engineering Drawing
- Experienced on lead and interaction directly with people
91
Production Supervisor Resume Examples & Samples
- Bachelor's Degree from an accredited college or university
- Minimum of 2 years of leadership / supervisory experience
- Bachelor's Degree in Engineering (Mechanical, Industrial, Chemical, Electrical or Aerospace) from an accredited college or university
- Experience working with Unions in a production environment Desire to work in a challenging and dynamic manufacturing environment
- Strong interpersonal and leadership skills Strong oral and written communication skills
- Supervisory / leadership experience in a manufacturing environment
- Ability to identify and implement cost reduction strategies based upon measurement data and technical expertise
- Ability to develop credibility with employees, manager and peers Strong technical, analytical, and diagnostic skills
- Ability to plan, communicate, and execute
- Ability to deal fairly and equitably with all employees Strong organizational skills
- Demonstrated integrity – accept and adhere to high ethical, moral, and personal values in decisions, communications, and actions when dealing with others
92
Production Supervisor Resume Examples & Samples
- Associates Degree from an accredited technical school or college (or a high school diploma / GED with at least 4 years of experience in Manufacturing)
- Minimum of 3 years of related manufacturing experience, specialist knowledge of a specific department or experience in a similar position
- Minimum of 2 years of prior leadership experience in production and supervision
- Bachelor's degree from an accredited university or college
- Minimum of 5 years of related manufacturing experience
- Knowledge of high-voltage transformer manufacturing
- Prior experience using Kronos Time and Attendance software
- Basic Microsoft Office software utilization skills
- Basic knowledge of Lean Manufacturing principles
- Strong analytical, problem solving, and project management skills
- Ability to manage contract resources
93
Production Supervisor Resume Examples & Samples
- Ensure team compliance to Quality Management System. Identify opportunities for improvement and create action items for gap closure
- Work with support functions to review processing schedules or production orders to make decisions concerning inventory requirements, staffing requirements, work procedures , or duty assignments, considering budgetary limitations and time constraints
- Maintain a safe and clean work environment by educating and directing personnel on the use of all control points, equipment, and resources; maintaining compliance with established policies and procedures
- Support and follow all rules/guidelines/standards set by EHS, Quality, and CI functions as set by leader and position
- All other duties as assigned including working extended shifts/overtime as required by the business
94
Production Supervisor Resume Examples & Samples
- Allocating work and assigning manpower
- Strong leadership focus on continuous improvement, FOD, Quality, and EH&S initiatives
- Provide leadership and direction with emphasis on team building through weekly toolbox meetings, monthly All Hands meetings, effective communications, and in developing an efficient team that is responsive to production requirements and change
- Control quality, productivity and process flow to meet COPQ requirements while ensuring a high level of customer satisfaction
95
Production Supervisor Resume Examples & Samples
- Ensuring a safe working environment through modeling safe behaviors, leading audits/inspections, correcting unsafe behaviors, conducting safety meetings, and utilizing proper work methods, procedures and equipment
- Providing direct supervision to production and/or hourly employees
- Driving continuous improvement in safety, productivity, quality and spending
- Planning daily work schedules, determine priorities, allocate work assignments, and regulate production processes in order to meet specific daily production requirements
- Championing lean manufacturing efforts and projects
- Reports to a General Supervisor with responsibility for operations and employees
- High School diploma/GED or higher from an accredited institution
- Minimum of one (1) combined year of supervisory and/or leadership experience
- Bachelor’s degree or higher from an accredited university
- Minimum three (3) years of supervisory experience in a manufacturing environment
- Experience working with hazardous materials
- Experience leading cross functional teams
- Self-directed and detail oriented
- Ability to create, lead and work in a team atmosphere
- Ability to drive and influence positive change
96
Production Supervisor Resume Examples & Samples
- Ensuring a safe working environment through modeling safe behaviors, leading audits and inspections, correcting unsafe behaviors, conducting safety meetings, and utilizing proper work methods, procedures and equipment
- Providing direct supervision to production hourly employees
- Handling shift administrative activities such as time and absence reporting, attendance control, vacation planning, overtime, etc
- Driving continuous improvement in safety, productivity, quality and cost
- High School Diploma/GED equivalent or higher from an accredited institution
- Minimum of one (1) year of combined supervisory and/or leadership experience
- Bachelors or Associates degree from an accredited university
- Proficiency in Microsoft Office Software Tools
- Experience in medical, pharmaceutical, or food manufacturing (cGMP, ISO 13485)
- Ability to drive and influence change and lead cross functional teams
- Training and/or experience with SixSigma and Lean Manufacturing
97
Production Supervisor Resume Examples & Samples
- Responsibe for the EBL and Bumpon production areas
- Responsible for holding Tier 2 meetings each morning in the departments
- Reports to a Product Manager with responsibility for operations and employees in the same plant areas
- Minimum of two (2) years of experience in a manufacturing environment
- Background in Lean Manufacturing
98
Production Supervisor Resume Examples & Samples
- Chemical or Mechanical Engineering Degree or equivalent experience OR minimum of 3 years of production or operations management, including supervision, crew leadership, or coordination or equivalent and completion of secondary level education
- Minimum of 2 years (in addition to above) production management, engineering or operations experience
- Advanced computer skills utilizing MicroSoft programs, Outlook, Word, Excel
- Must be able to learn computer software programs such as maintenance database (i.e. Maximo) and Project database software
- Ability to develop and manage good working relationships with internal departments (maintenance, sales, logistics, accounting), contractors, suppliers, inspectors and customers
- Demonstrated ability to develop staff accountability
- Strong execution skills
- Demonstrated ability to coach others for high performance and high engagement; motivates, inspires, and engages others to excel and work towards the vision
- Demonstrated respect, candor, and commitment
- Must be able to manage priorities; sees what needs to be done, assesses degree of urgency and importance, and takes appropriate action
- Demonstrated expertise in managing multiple tasks, projects, and deadlines in a highly dynamic environment
- Practical business acumen
- Relentless determination and courage to get things done; demonstrates tenacious and unrelenting drive for results
- Demonstrated teamwork and the ability to effectively collaborate with others
- Ability to influence others outside of formal reporting relationships
- Must be able and willing to work in an outdoor environment with exposure to grain dust
99
Production Supervisor Resume Examples & Samples
- 40% Planning and implementation of processes to create a safe work environment and effective use of the work force
- Must be able and willing to work from heights (i.e. ladders, catwalks, etc.) and in an indoor/outdoor environment
- Experience managing an effective EHS program
- Expectation to balance work schedules with other Supervisors to accommodate shuttle train loading
- Ability to influence decision-making
100
Production Supervisor Resume Examples & Samples
- 20% Maintain a system that evaluates process improvement sheets and model reports daily for accuracy and changes in trends, and act on any adverse trends or lack of accuracy
- 10% Utilize a tool (activity schedule) to help manage and execute the numerous requirements for which you are accountable
- Coordinating the logistics for the shipping and receiving of 12,000 tons of animal feed monthly
- Lead a group of highly engaged employees in this environment
- Oversee loading and unloading of trucks
- Daily paperwork review
- 2+ year's supervisory experience in a production/industrial environment
- Ability to work 2nd shift - (2:00pm-10:30pm)
- Customer Solutions Approach. Holds self and others accountable
- Experience in a feed or manufacturing industry
- Inventory management experience
- Forklift experience
101
Production Supervisor Resume Examples & Samples
- 40% - Plant Operation and Risk Management
- Supervise, lead and engage production team on a daily basis
- Plan and implement our Operational Excellence processes with the Operational staff to create a safe environment and effective use of the asset to achieve production goals
- Conduct regular plant inspections and assist in a variety of location specific audits
- Hold monthly safety meetings with staff to review procedures and safety awareness issues to ensure the Plant and yard are clean and safe for customers and employees
- 20% - Operational Effectiveness
- Perform physical operational duties which include receiving of grain and/or crop input products, operating grain cleaners and dryers, and any other operational activities
- Meet all rail car and truck loading requirements to ensure that customers receive the products and services they require in an efficient and timely manner
- Assist Plant management in managing the location grain or crop inputs inventory to minimize inventory loss
- Communicate and coordinate with the staff and central logistics to ensure efficient meshing of buying and shipping programs and effective elevator space management
- 20% - Talent Management
- Ensure optimum performance of staff through coaching, development, and training
- Assist with planning and scheduling of the operations staff to ensure staffing levels are appropriate to meet customer needs, along with proper training and direction of seasonal staff
- 20% - Capital Effectiveness and Reliability Excellence
- Organize and plan an assigned area of the facility within operating budget and assist with preparing capital budgets
- Supervise onsite contractors that perform work at the location to meet safety and quality guidelines
- Ensure operations staff are trained to operate plant equipment efficiently and effectively
- Minimum 2 years’ experience in an agricultural service business environment
- Proven supervisory experience with the ability to effectively lead and manage a team of diverse employees
- Proven problem solving, decision-making and organizational skills
- Ability to manage compliance with Environment, Health & Safety and Operations standards and regulations
- Proven ability to facilitate training
102
Production Supervisor Resume Examples & Samples
- 20% - Maintain a system that evaluates process improvement sheets and models reports daily for accuracy and changes in trends and acts on any adverse trends or lack of accuracy
- 20% - Understand the plant flow and what restrictions or bottlenecks cost vs the cost to remove those restrictions or bottlenecks
- 20% - Employees must be educated and trained to perform their jobs safely and to accept responsibility for their own safety performance
- 20% - Maintain physical condition and appearance that reflect the standards of quality and service of our business. Ensure that the character of our people professionally represent the brand image
- 10% - Maintain a system that sets standards on each delivery
- 10% - Utilize a tool (activity schedule) to help manage and execute the numerous requirements you are accountable for
103
Production Supervisor Resume Examples & Samples
- Solid background of production and engineering management, Honest, Righteous, Diligent, Carefully, Studious
- Technical or finance Universities with English, MBA qualifications is an advantage
- 5-10 years’ Experience in manufacturing management, at big FDI manufacturing is an advantage
- Interpersonal skill to production people and other depts
- Hand-on experiences in production management and engineering skills
- Experiences in FDI manufacturing environment: Benchmarks, safety, performance management and interpersonal skills
104
Production Supervisor Resume Examples & Samples
- Bachelor technical or technological degree
- 3+ years experience in a highly automated plant operation
- Proven record of leading a team
- Knowledge of products and production processes
- General knowledge in food production & HACCP
- Communication/presentation skills
- Managerial skills
- Broad orientation/knowledge on technical issues
- Dutch and English language
- Bachelor/Master technical or technological degree
- 5+ years supervisory experience in a highly automated plant operation
- Knowledge of products and production processes of the specific plant area
105
Production Supervisor Resume Examples & Samples
- 30% Coaching development, training and management support to employees within the facilities such that goals of the organization are achieved
- 30% Assist in management of all aspects of State/Federal Regulatory and Cargill compliance programs including: EH&S, Inventory Control, Warehousing, Security, Housekeeping, Food Safety, etc
- Expectation to balance work schedule with other supervisors to accommodate flexibility in scheduling based on fluctuating business needs
- Grain operations or personnel management experience preferred
- Capable of delivering innovation
- Ability to work effectively as part of a team
106
Production Supervisor Resume Examples & Samples
- Monitor production to ensure that quality, productivity, and cost standards are maintained
- Provide employee training to ensure that employees are performing job responsibilities effectively
- Oversee department specific sanitation operations as necessary to promote and maintain a clean and food-safe environment
- Maintain and enforce GMP standards
- Evaluate subordinate performance, communicate with employees, and provide information for work performance improvement
- Participate in the support of plant and company safety programs, promoting and maintaining a high level of awareness and adherence to defined employee safety requirements such as lock-out/tag-out, personal protective equipment, confined space entry, etc
- Provides leadership and direction for plant continuous improvement
- Attend and Lead production meetings
- Lead and manage cross functional Line Structure Teams
- Respond to employee grievances
- Ensure operation of manufacturing lines will meet performance standards for each product
- Ensure all daily manufacturing documents are completed and accurate
- Functions with limited direct supervision
- Exhibits the desired ConAgra Behaviors for the Ways We Win - Teach and Trust, Push for Personal Excellence, Constructively Challenge, See the Big Picture, Think two steps ahead
- Applies ConAgra’s Operating Principles of Simplicity, Accountability, Collaboration, and Imagination to deliver results
- A self-motivated individual that is able to motivate, mentor, and train others
- Excellent communication, interpersonal, problem solving, organizational, and follow through skills that can achieve results by working through others
- Ability to develop rapport across the organization and draw people together to create winning teams
- Strong PC skills with MS office programs
- Previous experience with SAP preferred
- Ability to multi-task and set priorities within the department
- Good mechanical aptitude to operate and troubleshoot manufacturing equipment
- Previous experience with continuous improvement, lean manufacturing, six sigma preferred
- Ability to work weekends and/or shift work (flexible to switch between 1st, 2nd or 3rd shift according to production schedule) with a strong work ethic and employment history
- A four year degree in Business, Food Science, Chemistry, Biology, Agricultural Sciences, or Engineering preferred. Other degrees will be considered
- Bilingual, Spanish preferred
- Three to four years supervisory experience in food-processing or food packaging, preferred
107
Production Supervisor Resume Examples & Samples
- Direct and coach production operators in the execution of daily/weekly production schedules for multiple packaging
- Drive the continuous improvement agenda in area of responsibility through teamwork, skills and capability
- 3 years experience in food, beverage, pharmaceutical or chemical industry
- 2 years previous management/supervisory experience
- Work flexible shifts, weekend and overtime as business needs
108
Production Supervisor Resume Examples & Samples
- Meet the productivity, quality, safety, health, environmental and morale goals established for the site
- Complete and update all necessary production paperwork and record
- Experience in food, beverage, pharmaceutical or chemical industry
- Experience in a fast paced manufacturing environment
109
Production Supervisor Resume Examples & Samples
- Continuous Improvement and Management – 35%
- 3 years of experience in high speed manufacturing environment with 1 year of management/supervisory experience OR a Bachelor’s degree in Business Management, Engineering, Supply Chain or related field
- 1 year of mechanical/electrical experience
- 2 years of Microsoft Word, Excel, and PowerPoint experience
- Prior experience with Kronos 6.2 or a similar timekeeping system
- Prior experience with SAP or a similar production planning application
- Must be able to work flexible shifts, hours, weekends and overtime as business needs arise
110
Production Supervisor Resume Examples & Samples
- Drive the continuous improvement agenda in area of responsibility. Maintain/develop lean daily management tools
- Incorporate and maintain safety, including use of all personal protective equipment by employees, ensuring equipment guards and safety features are working, and promoting good daily safety practices and habits
- Ensure team understands roles and responsibilities as it relates to core accountabilities, including safety, quality, productivity and delivery
- Communicate goals and objectives, apply company policy, staffs train, coach, recommend salary increases, administer discipline, insure positive employee relations and review the performance of employees. Build bench strength through active development of direct reports
- Manage all operating budgets with regards to labor, over time and temporary employees
- Complete and update all necessary production paperwork and records
- Manage and facilitate employee and management relationship within the guidelines of a labor contract and/or company policy
- Assist Plant Manager and Operations Manager as needed
- Bachelor's degree in Business, Supply Chain Management, Chemistry, Engineering, or related field
- Know
111
Production Supervisor Resume Examples & Samples
- Responsible for establishment of efficient, reliable and profitable manufacturing processes throughout the manufacturing areas
- Coordinates activities of manufacturing to enhance operational effectiveness using forecast, capacity planning and internal metrics
- Directs and manages the activities of the direct operators leads area in the consistent application of discipline and control of people and processes
- Responsible for attainment of operational, quality and functional goals as defined by facility management including execution of ISO standards
- Develop and train the personnel in the operational areas, to assure the adequate supply of capable personnel in the growing stages of the company utilizing the policies established by Human Resources and work instructions defined by manufacturing and industrial engineers
- Apply a proactive focus in the formal communication exercises established by the company in order to obtain a dynamic response to the constant changes in the market
- Daily production reports according his area results and daily review with his team
- Daily time and attendance input in to the KRONOS system, daily production master plan review and following
- Responsible to apply all the requirements related to EMS, ISO9000/14000 requirements according to the position
- Responsible for establishment of efficient, reliable and profitable manufacturing processes throughout the manufacturing area(s)
- Coordinates activities of manufacturing areas to enhance operational effectiveness using forecast, capacity planning and internal metrics. Also leads communication efforts of customer reliability issues or concerns addressed by use of ECNs (Engineering Change Notifications)
- Directs and manages the activities of the manufacturing supervisors and their respective staffs
- Develop and train the personnel in the operational and technical areas, to assure the adequate supply of capable personnel in the growing stages of the company utilizing the policies established by Human Resources and work instructions defined by manufacturing engineers
- Apply a proactive focus in the formal communication exercises established by the company (Daily Operative meeting, CFT, CSI, Quarterly Manufacturing Unit meetings) in order to obtain a dynamic response to the constant changes in the market
112
Production Supervisor Resume Examples & Samples
- Responsible for establishment of efficient, reliable and profitable manufacturing processes in all areas
- Coordinate manufacturing activities to enhance operational effectiveness using forecast, capacity planning and internal metrics
- Direct and manage the activities of operators and lead them the consistent application of discipline and control of people and processes
- Responsible for the attainment of operational, quality and functional goals as defined by facility management including execution of ISO standards
- Develop and train personnel in operational areas, to ensure that the policies and company defined work instructions are followed
- Daily production reports according area results and daily review with team’s efforts in areas such as DFP, Scrap, FTQ, absenteeism, turn over and safety
- Input of time and attendance information into the appropriate system
- Review of daily production master plan
- Everything concerning about ISO 9001 & ISO 14001
- Administration of human material and technical resources
- Hands on & proactive personality
- Consistent and stable leadership
- Superb communication skills at all levels
- Problem analysis and decision making
- Team building
- Capability to handling different tasks in the same time
- Planning and organization
- Interpretation of BOM
- Lean manufacturing knowledge
113
Production Supervisor Resume Examples & Samples
- Direct, supervise and coordinate all aspects of proper methodology in the fabrication, assembly and packaging of production units
- Effective communication of department, plant, and EMA objectives to the work force as well as effective communication of their feedback to the company
- Daily direction of work assignments, ensure proper material flow and equipment usage
- Train and maintain a flexible work force that is safety, quality, and production oriented
- Address staffing needs based on department labor maps
- Communicate, coordinate and cooperate with other departments to maximize efficient productivity
- Administer time and attendance for all direct reports using the Kronos time management system
- Ensure direct reports are paid correctly and in a timely manner
- Utilize EMS principles to conduct root cause problem solving; research and implement process flow improvements, production methods, production throughput and improved product quality
- Maintain effective employee relations; ensure compliance with company policies/procedures and legal guidelines; foster a positive workplace environment
- Stay current on all aspects of hazardous waste and handling
- Be available prior and after shift so as to ensure a timely shift transition
- This is a fast paced, high volume production environment which requires an aggressive, self-starting individual able to work both independently and as a team in a manufacturing environment to meet customer requirements
- Willingness to work all shifts and extended hours is required
- Experience using Microsoft Office tools including MS Word, Excel, and PowerPoint
- Three years previous supervisory/management experience in a manufacturing setting
- Prior experience utilizing lean manufacturing tools and techniques
- Knowledge of Kronos timekeeping systems
114
Production Supervisor Resume Examples & Samples
- Assure that all quality criteria are met in accordance with ISO9000 requirements
- Maximize first pass yield in all product lines without sacrificing HSE or Quality
- Ensure procedures are in place and followed in compliance with all HON, state, and federal regulations and guidelines
- Ensure shifts are adequately staffed to best assist in increased productivity
- Recommend improvements to production methods, equipment performance and quality of product
- Serve as resource for Leads and team members to drive improvement opportunities
- Analyze and resolve work problems, or assist workers in solving work problems
- 1 year of experience in manufacturing concepts including Lean, Six Sigma, TQM, ISO
- 3 Years of leadership experience in a manufacturing environment
- Bachelors or Masters
115
Production Supervisor Resume Examples & Samples
- Directing all activities for all production lines across shifts in accordance with plan and line goals, product standards, costs, budgets, manpower and established procedures
- Mechanical, Mechatronic & Food Engineer, Industrial Engineer, Chemist Degree
- Experience as manager of operative personnel
- Experience in line production processes
- Ability to communicate effectively in both, Spanish and English
- Operational understanding of warehouse/logistics processes
- Demonstrated knowledge of managing safety and quality programs & processes
116
Production Supervisor Resume Examples & Samples
- Bachelor's Degree and at least five (5) years of supervisory experience, preferred. High School diploma and five or more years of manufacturing experience required or equivalent combination of education and experience
- Consistent work history and experience
- Ability to lead in a production environment
- Requires tact and good judgment
117
Production Supervisor Resume Examples & Samples
- Plans and reviews production operations, establishing priorities and sequences for manufacturing products
- Resolves operational, manufacturing, and maintenance problems to ensure minimum costs and prevent delays
- Schedules and assigns work to meet production requirements. Utilizes the appropriate personnel based on skill sets
- Involved in the hiring process for hourly employees. Responsible for employee counseling and disciplinary actions, including recommendations for termination
- Maintains and adheres to the operational budget for departments supervised
- Maintain shift reports and records. Verify employee’s time in KRONOS
- Work with Supervisors in other departments to coordinate activities
118
Production Supervisor Resume Examples & Samples
- University degree in Manufacturing, Chemistry, or Engineering (concentration in Food Industry is preferred)
- Excellent knowledge of English language
- Has knowledge of manufacturing systems (SA, Mfg Pro), good PC literacy (MS Office)
- Must have 3 - 4 years experience in Manufacturing (Production, Maintenance, and Engineering preferred)
- Experience in managing / supervising team leaders / blue collar workers
119
Production Supervisor Resume Examples & Samples
- Manage daily line operations in Mixing, Baking, and Packaging. Insures line is running properly, identifies the need for, arranges for and coordinates maintenance repair, replacement, or upgrades
- Directs personnel and activities to achieve consistent, highest quality products at the lowest possible cost
- Attends POG meeting daily
- Insures compliance with GMPs and all regulatory requirements
- Insures proper allocation of direct labor to lines on a daily basis through KRONOS
- Closes line cost centers on a daily basis
- Enters shift units, downtime, and carton weight data into Supervisor audit
- Enters Mixing data into Pansophic
- Utilizes SAP to manage maintenance of line equipment
- Maintains good labor relations and resolves all verbal grievances and other labor related issues in a timely manner
- Participates in evaluation/training of hourly personnel
- Insures employees follow all Atlanta Bakery, Local, State, and Federal Health and Safety rules and regulations including EPA and OSHA
- Insure compliance with safe operating procedures by line personnel
- Plan and coordinate Safety Meetings
- Coordinate and follow up on all reportable and near miss accidents
- Coordinate and follow up on all Safety violations
- Conduct monthly Safety Inspections of line and follow up on observed issues
- Complies with Bakery Affirmative Action policy
- Maintain all line related system and regulatory documentation on their shift
- Provides Production Manager input on budget issues
- BA/BS degree in operations management, business or a related field or equivalent experience
- A minimum of one year prior supervisory or leadership experience
- Prior sanitation experience preferred
- Excellent analytical and computer skills
120
Production Supervisor Resume Examples & Samples
- Direct activities of hourly associates in assigned areas to ensure department production goals are met
- Ensure line operations meet established standards, specifications, efficiency and quality requirements to affect favorable production results
- Communicate and collaborate with other production front line leaders and cross-functional teams on a regular basis concerning production goals and all operation activity
- Foster team building & collaboration across functional areas at all levels
- Responsible for coaching, counseling and training hourly associates to foster a high performance work team
- Maintain employee relations activities including safety, labor relations and grievance response and/or avoidance
- Ensure compliance with all company policies, safety guidelines and state and federal regulations
- Partner with the master labor planner to understand and optimize staffing needs
- Seeks and understand financials about the business and the various trade-offs to control costs end-to-end
- Fosters a high performance work systems by learning and teaching Lean concepts, TPM, Six Sigma and/or Integrated Lean and 6S
- Manages SAP/LIS on a daily basis for packing employees to ensure each record is accurate for payroll to effectively run
- Strong in labor relations and fluently understands contract labor rules to work well with shop stewards and union leadership
- Responsible for hiring and training hour associates
- Challenges the status quo
- Bachelor’s Degree in Operations Management, Supply Chain, Engineering, Food Sciences or related discipline
- Leadership skills, comfort level with change, and the ability to lead change
- Solid interpersonal skills and team orientation
- Willingness to work different shifts, including overnights, and weekends
- Previous manufacturing experience through internships or co-ops is highly desirable
- Demonstrated leadership skills
- Ability to multi task and enjoy a dynamic and fast paced environment
- Working Knowledge of Computer-Related Systems (Excel, Word, and Microsoft)
121
Production Supervisor Resume Examples & Samples
- Direct, delegate and assign tasks to employees
- Train employees on production duties
- Motivate employees and promote a positive work environment
- Identify, prevent and address health and safety issues, such as dress code, personal hygiene, working conditions, etc
- Assure all product is produced and packaged according to standards
- Maintain employee absence and tardy records
- Report and document accidents and incidents immediately following proper procedures
- Ensure all company rules and regulations are followed
- Administer progressive disciplinary actions as appropriate
- Demonstrate strong commitment to GMP’s and the production of outstanding quality products
- Ability to demonstrate safe working habits
- Ability to demonstrate excellent work habits in line with Good Manufacturing Practices (GMPs)
- Ability to speak, read, and write in both English and Spanish
- Ability to understand, follow, and provide detailed oral and written work instructions
- Excellent motivational, interpersonal and communication skills
- Computer literacy, especially with Microsoft Office Suite
- Ability to follow and enforce all company policies and procedures
- Ability to stand and walk for long periods of time
- Ability to lift/carry up to 25 lbs. and push/pull up to 40 lbs
- Ability to meet all other physical requirements of work in a manufacturing environment
- Ability to work any shift, nights, weekends, holidays and extended hours as required
- Ability to pass job related, computer based testing
122
Production Supervisor Resume Examples & Samples
- Adhere to all safety procedures and policies. Lead Safety meetings and conduct required safety walks utilizing the DuPont STOP auditing program, communicate issues in an efficient and effective manner
- Responsible for monitoring quality levels, reporting, and minimizing scrap. If problems arise takes the necessary corrective action
- Responsible for monitoring production levels through O.E.E. (Overall Equipment Effectiveness) tracking. Motivate and ensuring daily goals are being met
- Responsible for the general housekeeping condition of the manufacturing area through 5S methodology. Report any equipment problems promptly to maintenance and/or engineering
- Prepare detailed plans and schedules to ensure efficient product flow and that shop orders are completed on time. Ensure all material transfers are handled within the prescribed procedures and checks all materials for correct specifications. Effective communication to oncoming supervision of any safety issues, change of schedules and other critical issues
- Maintain appropriate levels of labor in accordance with skill requirements, work levels and schedules. Maintain conformance with employee safety rules, issue violation warnings, and administer approved disciplinary measures when necessary. Maintain employee vacation and attendance records
- Reports to management all discrepancies of policies and procedures
- Requires a minimum of an Associate’s degree in Business, Operations Management or a related field
- Must have minimum of one year of supervisory experience
- Must have mechanical ability and basic knowledge of machinery operations
- Must have the ability to work in a team environment
- Must be computer literate with basic knowledge of Word, Excel, and Windows. (SAP knowledge preferred)
123
Production Supervisor Resume Examples & Samples
- Organize and facilitate work team meetings (examples: pre-shift, roundtables, etc.)
- Improve team communication and engagement
- Think quickly, creatively and challenge team to do the same
- Desired Knowledge, Skills, and Abilities
- Demonstrated ability to work in a results oriented, challenging environment
- Authorized to work in United States on a permanent basis
- Technical Background preferred
- Degree in Engineering, Operations Management, or related Technical major preferred
- Must pass a drug screen and background investigation
124
Production Supervisor Resume Examples & Samples
- Ability to address employee concerns in a timely manner and if required provide the necessary feedback through Coach and Counseling and the use of the progressive discipline system
- Apply policies and procedures fairly and consistently throughout the department, according to the Employee Handbook and Departmental Operating Procedures
- Facilitate performance reviews of Wage Associates
- Knowledge of all policies and procedures of the incumbent’s areas of responsibility
- ERT Membership
125
Production Supervisor Resume Examples & Samples
- BA/BS Degree in Business, Food Science, Engineering or related field is preferred
- 1-5 years of experience in a manufacturing environment is required
- Ability to lead, motivate and mentor large teams of hourly associates is required
- Strong analytical/critical thinking
- Strong accountability, consistency and follow-through skills
- Ability to work effectively with a wide array of plant personnel ranging from hourly employees to senior management
126
Production Supervisor Resume Examples & Samples
- 35%- Lead operational functions performed at this facility. Coordinate with the Assistant Logistic Superintendent to meet the goals of our vessel loading and barge/rail unloading programs which are key drivers to the profitability of this location. Develop daily crew schedules with the unionized staff (ILWU) to meet our customer’s needs. Train in the control room to obtain an understanding of the Federal Grain Inspection Service grading standards and use this knowledge to make informed decisions on binning & inventory management
- 30%- Ensure the Environmental Health & Safety Programs are being followed and provides a safe working environment to our employees, customers and community. Ensure product quality standards and customer needs are met through execution of the Food & Feed Safety programs. Perform daily sanitation inspections to ensure the facility is meeting Cargill & OSHA standards
- 20%- Provide training on critical safety programs such as confined space entry, burning and welding, lock-out/tag-out, standard operating procedures, etc. Participate in the hiring of production personnel as needed to meet staffing needs. Manage the training of newly hired employees utilizing the on-boarding checklist. Provide on-going training to current employees to learn new tasks
- 15%- Perform daily inspections of the facility noting any mechanical defects & reporting them both directly to the Maintenance Leadership Team and through the Computerized Maintenance Management System. Assist in maintenance activities when working second shift or week-end duty
- Four year degree [industrial or agricultural technology or equivalent] OR four or more years’ experience in industrial plant environment
- Minimum 2+ years maintenance management, engineering, or production management
- Ability to develop and manage good working relationships with internal departments, contractors, suppliers, inspectors and customers
- Ability to take off-hour calls and rotate weekend coverage with facility staff as needed
- Advanced computer skills (MS Word, Excel, Access, CMMS, etc)
- Ability to effectively manage change
- Task oriented
- Effective Communication [verbal, written, presentation, numeric] skills for multiple levels of Cargill and customer organizations
- Working knowledge with Environmental Health and Safety
- Willingness/ability to work rotating shifts
127
Production Supervisor Resume Examples & Samples
- Directs the resolution of highly complex or unusual business problems that cross functional lines
- Develops business plans to achieve functional or cross-functional objectives
- Leverages the performance management cycle to motivate employees and support achievement of objectives
- Typically has 7 to 25+ years relevant experience
128
Production Supervisor Resume Examples & Samples
- As our Production Supervisor there is never a dull moment – you will face new production challenges every day on the manufacturing floor, leading a team of mixers or materials handlers, making strategic decisions on the fly, which will determine whether you meet production goals by the end of the shift and how you will do so without compromising the safety of your employees or the quality customers require
- Rely on operator wisdom and experience to guide you in finding solutions to immediate problems and long term changes to enhance safety, quality and productivity. Work with the Lean Manager and a cross functional team to achieve cultural transformation
- Mentor others early in their manufacturing career, helping them understand team dynamics in manufacturing and how to lead seasoned employees effectively, to ensure that your shift exceeds metric targets
- Previous leadership or supervisory experience
- 3+ years’ production experience in a in a food, chemical, beverage or related batch manufacturing environment
- 3+ years’ manufacturing experience
- Previous experience leading coaching and mentoring conversations with direct reports
129
Production Supervisor Resume Examples & Samples
- Manage new production challenges every day on the manufacturing floor as you coach a team of mixers or materials handlers and make strategic decisions on the fly. Your ability to effectively engage your team will determine whether you are able to meet safety and production goals
- Mentor other Production Supervisors early in their manufacturing career, helping them understand team dynamics in manufacturing and how to lead seasoned employees effectively, to ensure that your shift exceeds metric targets
- Bachelor’s degree in engineering, science or technology
- 3+ years production experience in a food, chemical, beverage or related batch manufacturing environment
- 1+ years production supervisory experience in a food, chemical, beverage or related batch manufacturing environment
- Bachelor’s degree in Chemical or Mechanical Engineering
- 1+ years Project Management experience
- 1+ production experience with the implementation of Lean systems in a in a food, chemical, beverage or related batch manufacturing environment
- Experience with Total Productive Maintenance (TPM) and/or High Performing Work Systems (HPWS)
130
Production Supervisor Resume Examples & Samples
- Plan and manage the day-to-day operations of 25 to 30 hourly teammates in order to safely, efficiently, and cost effectively achieve performance targets
- Coach, develop, and mentor teammates to meet current and future business demands
- Act as a change agent and champion change initiatives and continuous improvement efforts, driving the TPM cultural transformation to high performing work teams
- Execute plant labor and overhead budget while achieving all dish machine remanufacturing metrics, ensuring the safety of all teammates
- Work closely with other supervisors and the cross-functional team to encourage collaboration to work efficiently to exceed metric targets
- Conducting and owning root cause analyses, 5 why’s, and corrective and preventive actions
- Bachelor’s degree in engineering, science, business, or related field
- 2+ years manufacturing experience
- 2+ years previous leadership experience
- Bachelor’s degree in Mechanical Engineering or Industrial Engineer strongly preferred
- Experience working in an assembly environment; evidence of a mechanical aptitude
- 2+ years’ experience applying TPM in a lean manufacturing environment
- Strong computer skills including Microsoft Suite applications
131
Production Supervisor Resume Examples & Samples
- Reviews daily production schedule, makes work assignments, and work schedule for the Production Technicians
- Conduct routine safety and communication meeting with the technicians
- Provide supervision to Production Technicians to insure that all safety, procedures, and work practices are being followed; assist in mechanical problems; mentor, coach, and develop production technicians
- Issue safe work permits, hot work permits, confined space entry permits and close out the permits on a daily basis
- Conduct employee performance reviews, document performance management, and manage Operations Technicians goals
- Complete or assure accurate completion of production paperwork and reports as necessary
- HS diploma/GED required
- Minimum 5 years chemical plant experience
- No immigration sponsorship offered for this role
- 7 years’ experience as Lead Operator or step-up Supervisor
132
Production Supervisor Resume Examples & Samples
- Identify all issues in team and provide continuous support to all members according to operating standard on everyday basis
- Supervise effective working of production personnel and in accordance with the decided production schedules and ensure compliance to all company policies
- Administer all work according to QRQC principles and recommend strategies to improve processes and achieve goals
- Coordinate with equipment and process teams and ensure compliance to all protocols and maintain product quality
- Manage and prioritize all production processes and implement all production plans
- Ensure compliance to all local policies to achieve all production objectives and provide appropriate feedback
- Prepare necessary paperwork and administer all information and maintain records of all documents related to production and quality
- Direct the company’s manufacturing activities to ensure maximum effectiveness is obtained for the production of quality products within specified time and budgetary guidelines
- Directs manufacturing engineering efforts to ensure company facilities and equipment are adequately designed, built and maintained. The emphasis will be on robust equipment/processes utilizing poke yoke techniques and quick change over
- Interface with Development Engineering and Sales/Marketing to coordinate the production process for the introduction of new products
- Problem-Solving skills -must be able to quickly ascertain a situation and be decisive in solving it
- People
133
Production Supervisor Resume Examples & Samples
- 10+ year's offshore facility production and maintenance experience with 5+ years in a supervisory position
- Deepwater and subsea experience desirable
- Experience working on a floating facility desirable
- Formal training with Command of Major Emergencies competency
- Excellent interpersonal skills and the ability to work in a team oriented environment
134
Production Supervisor Resume Examples & Samples
- 50% Organize, Plan, Lead and control daily production
- 20% Ensure administrative functions are being met for employees
- 10% Compliance with all Corp/BU, State and Federal statues as it relates to the operation
- 10% Safety and proper job training of all employees
- 10% Maintain communication of availability of operating supplies
- Periodically attend training outside the work site that may include travel and/or overnight stay
- 3 or more years industrial experience and high school equivalency or 2 - 4 year college degree plus 1+ years of industrial experience
135
Production Supervisor Resume Examples & Samples
- 40% - Lead specific operational accountabilities: control room operations [vessel loading and inventory received marine operations [stevedoring and coordinating barge handling], or house operations [rail, truck, dryers, sanitation]
- 25% - Employees: Schedule, motivate and train employees to perform specific tasks
- 10% - Special projects and initiatives
- Four year degree [industrial, electrical, agricultural technology or similar technical discipline] OR four years experience in industrial plant environment OR equivalent service as commissioned or noncommissioned military officer
- Successful applicants will be required to pass basic math test required of union control room console operators
136
Production Supervisor Resume Examples & Samples
- Provide leadership and direction to shift personnel in order to meet the desired output. Review work-in-process levels in all production areas and make recommendations and adjustments to maintain efficient balance. Adjustments include decisions concerning equipment downtime, manning levels and material quality
- Uniformly enforce and apply company policies and procedures to maintain fair and consistent work practices. Provide input and seek clarification where necessary to ensure that adequate communication and understanding is occurring. Provide honest, objective and specific feedback to enable the subordinate to clearly understand the shortcomings and the means for improvement. Serve as facilitator, when needed, to maintain the group's focus and provide the necessary resources
- Manage shift activities so as to meet the plant's scrap, rework, and defect goals. Facilitate decision making and problem solving process for crew leaders and their crews to foster a more participative and committed approach to the operations. Provide the necessary feedback and coaching to review results with crews so as to obtain the desired continuous improvement. Monitor defect and downtime causes and provides feedback and recommendations to Value Stream Manager to assist with first pass yield and other targets within their area
- Provide clear, consistent direction relative to maintaining and enhancing the plant's safety goals. Maintain shift records relative to on-the-job training status for all department personnel. Initiate manning assignments to address shortcomings to ensure that production goals can be met with qualified personnel
- Contribute towards the plant's cost reduction goals through fostering a continuous shift awareness. Coach and encourage crews to identify and implement cost savings. Understand the concepts behind lean manufacturing and supports them in the workplace. Provide the necessary leadership to obtain the data, acceptance, and details necessary for an effective project justification. Control usage of supply items and recommends changes to maintain control or reduce costs where appropriate. Support major cost reduction efforts relative to materials and/or formulations by actively obtaining the information that can be communicated to department personnel to heighten their awareness, understanding and support
137
Production Supervisor Resume Examples & Samples
- Train and develop and direct reports in order to efficiently complete work
- Works with Human Resources in disciplinary situations
- Maintain a safe and efficient working environment emphasizing neat, orderly housekeeping, daily equipment maintenance and attention to specific problems
- Enforce the work rules as they apply to direct reports
- Adhere to schedules and make sound decisions when deviation from such schedules is necessary
- Support and promote cost improvement ideas
- Promote good labor relations through consistency of action, fairness, effective communications and respect to all employees
- Recommend labor force manning levels/changes and overtime requirements
- Maintain such records as overtime, Kronos, data collection, vacation, personal days, etc
- Practice and instill safety adherence as a first priority to achieve accident-free work performance
- Works with and directs the storeroom to coordinate requirements as needed
- Functioning as a team player, coordinate requirements with Machine Shop, Quality, Paint, Shipping, and Test departments
- May serve as a backup Supervisor to peer departments in Test, Quality Control, Plant Air, Machine Shop and Shipping areas
- BS Degree in a Technical field preferred with five (5) years experience in heavy industry assembly or an equivalent combination or education and experience
- Mechanical aptitude are necessary
- Ability to work midnight to 8am
- Some weekends required
138
Production Supervisor Resume Examples & Samples
- Supervises the activities of production associates to achieve objectives with regard to quality, cost and time. Evaluates the performance of associates and completes necessary reports. Recommends training and development needs
- Inspects and monitors production quality and equipment. Ensures quality procedures/practices are applied to the process, tooling, and equipment to achieve expected quality improvements
- Promotes and supports the company's efforts in associate involvement concepts, and "open door" communications through the development and or implementation of various programs
- Promotes commitment to quality through attitude, behavior, communication, and development/implementation of programs and activities
- Communicates/updates shift management of daily problems and concerns, identifying areas needing attention to ensure the continuity of the operation
- Engineering Degree required
- Personnel Management, Lean Manufacturing, Welding and Assembly processes Knowledge
- English 70%
139
Production Supervisor Resume Examples & Samples
- Provide daily supervision and support of employees in the respective work cell(s); which includes assignment of work, managing employee performance issues, maintaining staffing levels,
- Maintain a cross-training matrix and identify and provide training for employees as needed to ensure adequate skills coverage
- Responsible for carrying out daily production schedule of orders through the work cell
- Identify issues that cause schedule interruptions and work with support departments to solve problems proactively
- Coach employee performance to improve productivity, manage attendance, ensure compliance with work procedures
- Utilize performance correction counseling to ensure fair and consistent expectations for all employees
- Work closely with inventory management, sourcing, Lean, Quality, Human Resources / Safety to identify and solve problems that interfere with the daily achievement of the production
- Manage the work cell(s) 5S and other Lean initiatives. Participate in Kaizen events
- Responsible for communicating safety expectations in work cell and work proactively to minimize safety hazards
- Perform near miss and accident investigations. Communicate hazards to others to prevent repeat incidents and raise the issue with maintenance or management. Complete safety cross and other reports as needed
- Drive quality assurance program in accordance with ISO 9000. Identify and respond to corrective actions
- Ensure department is following all company policies and procedures
- Proactively respond to employee concerns and ensure timely follow up to questions
- Maintain daily / weekly /monthly production reports. Carry out standard work expectations
- Significant emphasis and expectation to use Lean tools to improve business results and coach subordinates
- Monitor Kanban, WIP and Plan for Every Part and notify Inventory Control to control variation while ensuring employees execute inventory transactions properly
- Execute Safety, Quality, Delivery and Cost metric charts impeccably while soliciting input from the workforce
140
Production Supervisor Resume Examples & Samples
- 4 years of Lead operator / supervisory experience in manufacturing
- Must be able to manage and lead change
- Strong leadership skills with a focus on team building
- Must have a solid working knowledge of Manufacturing and Quality
- Knowledge of ISO 9001 or QS 9000 procedures
- Must be capable of resolving complex problems
- Knowledge of Lean Manufacturing skills, 5S visual factory and JIT manufacturing techniques
- Must have good computer skills with Window, Word, Excel
- Ability to develop high levels of credibility and forge solid and positive professional relationships with subordinates peers and upper management
- Provide leadership and direction for the manufacturing floor by setting priorities to meet the business objectives and to provide the training and guidance necessary to enable the employees to improve their own abilities and skill levels
- Coordinate all manufacturing related activities for the shift to ensure that all are driving toward the common goals established in the strategic plan
- Lead the shift efforts to establish a lean operation utilizing PPI and the 5S programs to identify and remove waste and focus on the customer
- Focus all manufacturing associates on (4) priorities: Safety, Quality, Customer Service and Productivity
- Maintain clean and safe facilities to support the overall business requirements
- Provide continuous feedback to associates to assure all are using best practices and are striving for continuous improvement and alignment with the business objectives
- Train direct reports to improve the employee’s skill sets and overall effectiveness through the PMD process
- Assist and support other leadership team members as required
141
Production Supervisor Resume Examples & Samples
- 40% Leadership:Manage day-to-day operations, including supervision and development of direct reports to include: full human resource management responsibilities for operators, such as hiring, scheduling, motivating, handling employee relations issues, and processing employee related paperwork. Develops and coaches employees using Cargill’s Performance Management Process (PMP) as well as managing the disciplinary process
- 25% Operational Efficiency: Drives customer solutions and services, product quality, quality notifications, and food safety. Reviews, monitors, and follows up on area results to ensure quality, food safety, and efficiency goals are met. Troubleshoots causes of customer issues or production problems and collaborates with other functions to provide efficient and effective resolution. Ensures availability of consumable supplies and provides communications to ensure the procurement of necessary supplies. Recommends and implements operating efficiencies within plant
- Bachelors Degree in Engineering, Sciences, or Business); may substitute degree with a minimum of 5 years of manufacturing experience
- Occasionally requires light work outside in a plant environment. On-call required
- Light physical activity including standing, walking, climbing and lifting
- One year of supervisory experience or demonstrated leadership experience, such as crew leadership, project leadership or equivalent
- Ability to develop and maintain good working relationships with internal functions (maintenance, sales, logistics, accounting), contractors, suppliers, auditors and customers
- Demonstrated leadership skills including ability to build highly effective teams
- Basic understanding and knowledge of HR practices, including EEO, Guiding Principles, etc
- General knowledge of production management with ability to develop understanding of plant processes and operational needs
- Demonstrated ability to develop employee accountability and engagement
- Demonstrated ability to appropriately set priorities
142
Production Supervisor Resume Examples & Samples
- Builds people capability through effective employee relations, hiring, training, and communication for frontline hourly personnel
- Demonstrates ability to function successfully in a fast paced, changing work environment
- Bachelor's Degree and/or equivalent experience in consumer packaged goods or a related industry
- Demonstrated frontline supervisory skills
143
Production Supervisor Resume Examples & Samples
- Administration or Management diploma
- Diploma in Operations Management or in a similar field
- 3 to 5 years’ experience in People Management between union groups
- Manufacturing experience between the food industries
- High Production Volume (FMCG) experience required
- Fluent in French (Oral-writing)
- Intermediate level of English required (Oral-writing)
- Microsoft Office knowledge (Word, Excel)
- Human Resources tool knowledge is a plus
- Manufacturing equipment knowledge (Mechanical, electrical and pneumatics among others)
- Management of resource allocations
- Understands, applies and manages the overtime policies
- Ensures the relations between colleagues
- Ensures the efficiency of his/her production line and engages in the conflict and problem solving solutions
- Writes the performance evaluations of his/her direct employees
- Direct the performance improvements and the disciplinary measures of his/her direct employees
- Understands and respects the systems and methods about food security
- Focuses on the results of his/her sector and explains the performances when is needed
- Time, stress and priorities management is required
- Integrates and applies the security rules
- Ensures that the production is aligned with the Best Production Practices
- SMED, Kaizen 5S, etc. knowledge
- Good interpersonal relations and communication skills
- Focused in team work and cooperation
- Health and security oriented
- Focused on the quality of the product
- Able to adapt to different work environments and changes
- Able to apply plans in concrete actions
144
Production Supervisor Resume Examples & Samples
- BS degree in the industrial sector, electrical, mechanical engineering
- 3-5 years experience in similar position
- Bilingual English/Spanish
- Communication and Leadership skills
145
Production Supervisor Resume Examples & Samples
- Supervise daily activities in rotor, assembly, and test
- Participate or Lead Key Projects aligned to plants goals and objectives as directed
- Leads daily Tier II meeting
- Control direct labor costs by driving efficiency to reduce premium time
- Analyze, recommend, and monitor training needs for subordinate and new personnel
- Support and drive Zero Incident Culture
- 2 year of experience in Operations or Manufacturing
- Minimum 1 year of Supervisory experience with direct reports
- Must be legally authorized to work in the United States without sponsorship
- 5 years of experience in manufacturing or operations
- Six Sigma Green/Black Belt
- 3-5 years of experience managing a team
- Engineering experience
- Previous experience in the Automotive industry
- Prior machining experience
146
Production Supervisor Resume Examples & Samples
- Optimize the functions of one’s department to effectively meet customer needs while minimizing costs
- Maintain daily statistics on customer demand, production, and overdue orders
- Communicate production metrics to management and other functional supervisors and maintain active communications between all levels of plant personnel
- Serve as a central point of contact for management in regards to production issues in one’s functional area
- Promote a Zero Incident Safety Culture enforcing safety standards that include housekeeping objectives, following all safety rules and procedures including PPE standards and buddy checks, and addressing unsafe conditions
- Understand and meet all department safety goals
- Ensure that department work areas are kept clean, organized, and orderly per 5S standards
- Champion continuous improvement efforts throughout the facility
- Lead in the coaching, counseling, and disciplinary activities surrounding one’s employees while simultaneously administering and maintaining Eaton Corporation policies and plant policies
- Explain the necessities of new policies, technologies, and processes as they are implemented
- Evaluate workload requirements to ensure proper and adequate manning to support production requirements
- Delegate tasks and responsibilities accordingly as governed by customer demand
- Investigate and solve quality issues and/or serve as a point of contact through which quality
- Minimum three years of experience supporting Manufacturing, Operations or Technical processes
- Minimum one year of leadership experience managing people or project teams
- Bachelor's Degree in Engineering from an accredited institution
- Three years of leadership experience
- Lean manufacturing / Operational Excellence skills in 5S+, Value Stream Mapping, Standard Work, Visual Management, etc
- Demonstrated effective communication and leadership skills
- Process focused
147
Production Supervisor Resume Examples & Samples
- Promotes customer satisfaction
- Ensures all functional areas have accurate, timely information
- Bachelor’s degree from an accredited institution is required
- 3 years of experience in a supervisory role
- 1 year of manufacturing experience
- Bachelor's degree in Engineering or Business
- Experience working in an assembly environment
148
Production Supervisor Resume Examples & Samples
- Minimum 1 year of experience in a supervisory role is required
- Must be legally authorized to work in the United States without company sponsorship now and in the future
- 3 plus years of experience in a supervisory role
- Experience with lean, six sigma, CI
- MS Office, Excel
149
Production Supervisor Resume Examples & Samples
- Assist the manufacturing manager in setting department goals and fulfillment of those goals
- Supervises work activities of personnel in the production area
- Directs operators to obtain maximum productivity and efficiency, ensures availability of materials and equipment to accomplish to meet production schedule and commitments
- Ensures that products assembled conform to established specifications and quality standards
- Ensures that methods, practices and production processes developed and approved for implementation conform to international standards
- Keeps wastage of materials, labor and power of his area is within approved limits
- Ensures that all machines and equipment, tools are in good running condition
- Plan manpower allocation, machine set-up and materials needed in manufacturing operations
- Checks and follows up the availability of indirect and direct materials affecting the plan
- Monitors quality trends and reworks rates to determine the causes of problems and recommends corrective actions
- Interfaces with Engineering, Quality Assurance and other support groups regarding manufacturing related problems
- Coordinates with personnel of Production Planning and Control regarding line balancing, commitment and control priorities
- Implements new methods that will ensure effective and smooth flow of production
- Ensures that safety program of the company are properly implemented in the section
- Maintains good housekeeping and efficient operating within the area of responsibility
- Prepares weekly, monthly, and other periodic reports of production activities
- Ensure application of Quality Policy of the company in his/her area of responsibility
- Performs other duties as maybe assigned from time to time
- Bachelor’s degree holder in engineering or any related courses
- Minimum of 5 years of production supervisor experience is required
- Knowledgeable in quality/ improvement systems/ ISO 9000
- Familiarity with UPS product manufacturing processes is preferred
- Excellent leadership, people management and communication skill
- Focused, analytical, organized, systematic, with high tolerance for stress, pleasant. disposition and excellent judgment skills
- Computer literate, able to use the Internet and email
150
Production Supervisor Resume Examples & Samples
- Conduct Daily Visual Management stand-up meeting with all department personnel in area of responsibility focusing on safety, quality, delivery, cost/productivity, and inventory
- Additional related duties as required
- Minimum of 1 year of supervisor experience
- Relocation is not being offered for this position. Only candidate residing within a 50 mile radius of Reno, NV will be considered
- Bachelor’s Degree in Operations, Engineering, or related field of study
- 3 + years of related experience including increasing responsibility and leadership of projects and teams of considerable size, scope and complexity in a manufacturing environment
151
Production Supervisor Resume Examples & Samples
- Carrera professional terminada
- Experiencia minima de 3 años en posicion similar
- Dominio de SAP
- Habilidades de liderazgo y comunicacion a todos los niveles
- Experiencia en procesos manuals de ensamble
152
Production Supervisor Resume Examples & Samples
- PRODUCTION MANAGEMENT IN ORDER TO ACHIEVE THE TARGET OF
- TO ENSURE ALL WORKS ORDERS / OUTPUT ARE MET ON TIME AS PLANNED WITHIN ACCEPTABLE
- TO SUPERVISE AND INSPECT HIS/HER SUBORDINATES TO ENSURE THE BEHAVIOR AND
- Bachelor’s Degree in rubber technology, materials, polymer sciences or related fields
- At least 5 year experiences in combining advance materials, product structure and material design, and manufacturing technologies to achieve technical performance
- A strong technical professional to develop and apply state-of-the art materials technology to highly engineered technical products
- Demonstrate strong initiative and drive for results as well as good interpersonal and teaming behavior
- Good command of English both spoken and written skills
- Computer literate ( Microsoft Office & CAD a plus)
- Able work in Nakhonratchasima and can work night shift, work on Saturday (2 Saturday / Month)
153
Production Supervisor Resume Examples & Samples
- Safely insures all phases of manufacturing are being performed efficiently and effectively
- Recommends and drives formula improvements, equipment and engineering revisions
- Coordinates publishing of process condition set up sheets; updating these conditions and maintaining the process conditions database
- Produces all shop floor paperwork as required for process order production
- Coordinates and administers all aspects of training for new hires as well as long term associates
- Complies with and enforces all company policies and procedures
- Reviews and corrects information in E-Time for time-keeping of production associates’ hours
- Coordinates with other Production Supervisors to provide seamless shift turnover and appropriate staffing
- Ensures plant production area housekeeping is maintained in “Tour Ready” conditions at all times in accordance with housekeeping guidelines
- Other projects/duties as assigned
- 2-5 years experience
154
Production Supervisor Resume Examples & Samples
- Bachelor’s degree in Mechanical Engineering preferred
- Other engineering disciplines with related experience can be substituted
- Or at least eight to ten years experience in manufacturing/maintenance engineering & supervision/quality control & environment and a minimum of two years supervisory experience
155
Production Supervisor Resume Examples & Samples
- Ability to take initiative along with decision making skills
- Due to ITAR, US citizenship or permanent resident status is required
- Must be able to communicate clearly both verbally and in writing
- Previous experience with SAP business management software a plus
- Must have basic capability with MS Word and Excel software
156
Production Supervisor Resume Examples & Samples
- Ability to work with all levels of management and communicate effectively with peers, customers and clients
- Demonstrated leadership skills; direct supervisory experience
- Highly motivated individual who enjoys operating in a dynamic environment and who enjoys the challenges of process improvement and "lean" manufacturing initiatives
- Candidates should be highly self-directed and able to learn quickly with a strong ability to drive and deliver results
157
Production Supervisor Resume Examples & Samples
- Ability to plan projects and to use written/verbal/analytical/organizational skills to influence business objectives
- Turbine engine overhaul and repair or related experience is desired, as well as, logistical, materials management, and financial experience
- MS Office programs proficiency
158
Production Supervisor Resume Examples & Samples
- General awareness of production processes, quality control, costs and other techniques for maximizing the effective manufacture and distribution of goods
- General awareness of business and management principles involved in strategic planning, resource allocation, leadership, production methods, and coordination of people and resources
- Ability to read, write, and speak fluently in English
- Ability to work off-shift hours, during company designated holidays, and extended shifts/overtime as the business requires
159
Production Supervisor Resume Examples & Samples
- Maintain effective communication with team members via pre-shift and individual meetings regarding company policies, procedures, work rules, process documentation and environmental regulations
- Follow the principles of the Magna Team member Charter
- Lead by example by wearing PPE at all times
- Uphold confidentiality and build trust in Management
- Maintain an open and honest relationship with fellow team members and help develop this attitude; treat all team members with dignity and respect without favoritism
- Conduct yearly performance reviews in timely manner
- Schedule team member vacation and personal days per department guidelines and company policies
- Promote and practice “safety first” policy by addressing all hazards, defective equipment and unsafe conditions immediately
- Discipline team members per company policies and procedures
- Provide accurate daily reports on machine uptime, pieces per hour, scrap percentage and accidents
- Promote and facilitate Open Door process without reprisal, effective communication and Fair Treatment
- Supervision training preferred
- Forklift training
- Able to work well with others; build and maintain positive team member relations
- Able to prepare, read and interpret written reports, instructions, procedures and guidelines
- Able to maintain confidentiality, and use discretion and tact
- Able to calculate figures and amounts, such as percentages and proportions
- Able to use computer and software as required
- A review of this description has excluded the marginal functions of the position that are incidental to the performance of fundamental job duties. All duties and requirements are essential job functions
- Some requirements may exclude individuals who pose a direct threat or significant risk to the health and safety of themselves or other team members
- Requirements are representative of minimum levels of knowledge, skills and/or abilities. To perform this job successfully, the incumbent will possess the abilities or aptitudes to perform each duty proficiently
- This document does not create an employment contract, implied or otherwise
160
Production Supervisor Resume Examples & Samples
- People management - supervision of production teams to ensure targets for quality/service/costs are achieved. This will be achieved through the application of an empowering style of leadership which draws fully on resources and capabilities of the team coupled with a positive Employee Relations approach. Essentially this will embrace the following
- Consistently applying BSC policies
- Establish and support a work environment of continuous improvement that supports BSC’s Quality Policy, Quality System and the appropriate regulations for the area they support. Ensure employees are trained to do their work and their training is documented
161
Production Supervisor Resume Examples & Samples
- Schedule and monitor staff and day to day workflow. Develop employee’s skills, evaluate performance and provide feedback
- Oversees resolution of employee relations. Conducts hiring, training, and evaluation of staff
- Work with Pharmacy Manager to analyze operations and overall efficiencies of the pharmacy
- Strong knowledge of current pharmacy regulations
- Experience training and coaching less experienced staff – patience to explain details and processes repeatedly
- Ability to adapt in a dynamic work environment and make independent decision
- Willingness to work a flexible schedule for peak times
- LI-HN1
162
Production Supervisor Resume Examples & Samples
- 2-3 year experience in manufacturing and materials area
- Engineering’s Degree or Industrial Engineering or similar
- Personnel Management skills
- Conversational English (85%)
- The ability to offer and promote a continuous and effective communication at all levels of the organization
- Knowledge desirable Quality (ISO, TS) systems
- Knowledge of standards of safety and environmental (ISO 14001) or ESP (Eaton Security Process)
- Extra: Knowledge of Internal enterprise systems such The Eaton Business System (EBS), Eaton Lean Six Sigma (ELSS), Eaton Environmental Safety & health system MESH and appropriate quality systems EQS
163
Production Supervisor Resume Examples & Samples
- To repeatedly and consistently deliver a fully compliant product to the correct quality requirements at a rate that satisfies the demands of the production schedule
- Ensure that all staff under the team leaders jurisdiction can continuously and competently execute their tasks according to all work instructions, weld procedures, sequences, drawings and weld maps without deviation
- Responsible for the overall quality of the product on completion of their scope of work. Perform defined in process inspection
- Task allocation-ensure that welders and metal worker know what to do, how to do and how long they need to complete specific tasks-in strict accordance to drawing and documentation requirements
- Implement & Smoothly followed takt time on line and highlight takt time disturbances in time. Follow actions to reduce disturbances with use of tools
- Initiate line improvement activities. Use statistical tools for root cause analysis and follow actions for improvement
- Should have good understanding of tools like 7 QC tools, TQM like 5S, Kaizen, Takt Line, ISO 9000 & other statistical tools practical use
164
Production Supervisor Resume Examples & Samples
- Plan work schedules and assignments to ensure that equipment is being serviced within the maintenance guidelines
- Monitor work order completion using Maximo and the employees timekeeping using Kronos
- You cumulate a minimum of three (3) to four (4) years of railway experience in a similar role
165
Production Supervisor Resume Examples & Samples
- Plan, implement and control functional activities in order to achieve the Operations Unit and/or Product Quality performance targets including goals set forth for the Achieving Excellence System
- Must be able to provide leadership and coaching to all employees in the department and provide feedback to employees
- Ensure functional role of support organizations are integrated into Operations Unit resulting in a one-team approach
- Ensure the right resources are available on a shift by shift basis to meet projected workload delivery on quality, cost and schedule
- Maintain housekeeping standards to ensure a safe working environment
- You must possess post-secondary degree/diploma in technical discipline and a minimum of three (3) years’ experience in a Supervisory role in a Manufacturing environment
- Ethics, integrity and honesty; respect for others; cooperation; be motivated to get things done; be able to express ideas logically and coherently; possess a positive attitude; be able to overcome obstacles; assume full responsibility; utilize the appropriate resources to solve day-to-day problems; react quickly to unforeseen events
- You must have in depth knowledge and experience in budgeting control, manufacturing and scheduling
- You must have previous experience working in a unionized environment
- You have experience in developing both long-range strategic goals and short-term tactical plans
166
Production Supervisor Resume Examples & Samples
- Directs and supervises the daily activities of the production, shipping and maintenance functions of facility, delegating responsibilities as necessary, to attain goals and objectives in each area. Ensures personnel are trained to perform standard work
- Schedules production by reviewing shop drawings in detail to determine ship date commitments, labor and material requirements
- Perform administrative tasks such as: payroll, writing and giving performance reviews, creating and maintaining performance measurement reports with accuracy
- Ensures compliance with the company’s safety programs through leading by example, performing audits and conducting and monitoring training
- Ensures effective employee relations by providing employee coaching and development
- Work with the Operations Management and Human Resources to make employment decisions, and resolve employee issues
- Works in team with other management to continually improve processes such as production flow, safety and quality standards and utilization of materials
- Conducts periodic cycle counts and physical inventories to maintain accurate inventory levels
- Responsible for quality assurance ensuring both results and associated documentation are maintained. Point of contact for third-party quality control organizations for quarterly audits
167
Production Supervisor Resume Examples & Samples
- Directs and supervises the daily activities of the production work centers, delegating responsibilities as necessary, to attain goals and objectives in each area. Trains personnel to perform standard work, conduct process audits, and participate in production directly as appropriate to crew size, scope of operations, and number of lead workers
- Works with operations management to determine labor requirements by reviewing production schedules and hires personnel according to budgeting plans set by operations management
- Perform administrative tasks such as: writing and giving performance reviews and creating and maintaining performance measurement reports with accuracy
- Assures proper PPE is used per plant requirements. Conveys and enforces company policies to employees and enforces safety regulations
- Ensures effective employee relations by providing employee coaching and development. Works with the operations management and human resources to make employment decisions and resolve employee issues
- Lead the production floor effort to reduce waste through the use of CIS, the SQDC boards, and corrective action sheets
- Leads special projects as needed and stands in as back up for operations management during vacations/absences
- Maintains time and attendance records
- Education: Bachelor’s Degree in operations, manufacturing, engineering, business, or other technical area strongly preferred
- Previous supervisory/management experience in a manufacturing setting
- Prior experience in operations research/process flow and scheduling department work
- Strong problem analysis and resolution skills
- Experience using SAP and Microsoft Office applications
- Strong communication skills and proven ability to lead people and get results from others
- Prior experience with Lean Manufacturing and 5s
- Knowledge of safety procedures such as lock out, tag out
- Able to identify possible quality defects and causes and knowledgeable of corrective actions
- Understand fundamentals of coaching, counseling, and feedback
- Comprehension/understanding of reading, speaking, and math skills
- Ability to measure performance of standards and goals
- Efficient problem solving skills and ability to work in stressful work situations
168
Production Supervisor Resume Examples & Samples
- Receives instructions from Production Supervisor/Manager for Machining/Final Lines-Assembly/Blend schedules and requirements for meeting Production requirements
- Computes amounts of stock and supplies required for operations, based on production schedules and requisitions materials from storage area
- Interprets job orders to employees and assigns duties
- Plans flow of materials through the department and coordinates with Operations and Maintenance for physical layout of assembly/machines according to work orders
- Responsible for setup and operation of equipment in support of department’s objectives
- Interfaces with other departments within and outside the ARO facilities to determine resource needs and scheduling
- Oversees and performs tests as needed to ensure accurate results
- Prepares appropriate charts/reports to communicate information to appropriate departments
- Trains Leads and Operators in Safety, production procedures, proper equipment operation and routine record keeping
- Assists with program of continual improvement within the Operations area
- Reports various manufacturing problems as they occur, compiles pertinent data and discusses with appropriate supervisor
- Coordinates with appropriate departments on various segments of the manufacturing process to identify and/or prevent potential problems
- Assists in evaluating proposed process changes and their impact on quality and productivity prior to implementation
- Generates and updates equations used in the adjustment of out-of-spec batches to meet spec requirements
- Assists as required in the training of manufacturing personnel to achieve their highest level of proficiency
- Coordinates with Quality on laboratory analyses results and reports
- Maintains the highest ethical standards, even when challenged from above
- Understands and lives by Esterline’s ethics and business conduct policies
- Must be proficient with MS Word, Excel Spreadsheets, Data Analysis, formatting of usable tables and other evaluation documents and Outlook programs
- Experience with Syteline and DOT regulation knowledge
- Working knowledge of Statistical Process Control and associated data analysis
- Proficient at reading and generating charts and graphs (pareto, bar, control, flow, fishbone, Cause and Effect, etc.)
- Must possess an outstanding degree of judgment, organization, planning, initiative, flexibility and creativity
- Must be able to perform calmly and reasonably under pressure from demand for production and other exigencies
- Physical capabilities include lifting materials up to 50 pounds, walking up and down steps, and to various programs as the situation warrants
- Plans movement of 100-500 pounds of material to draw out exact quantities required for formulation
- Must possess teamwork capabilities and Leadership skills
- Associate’s degree or equivalent with a written plan toward a Bachelor’s degree with 2 – 3 years related experience and/or training
- Self motivated starter demonstrating maturity in responsibilities and analytical skills
- Good communication skills and high degree of integrity
- Established team skills in interfacing with all employees
- Proficient with MS Word, Excel spreadsheets, Data Analysis, Formatting usable tables and other evaluation documents and Outlook programs
- Knowledge of computer systems and DOT regulations
- Ability to read and write English and compute college level mathematics, including statistics
- Strong interest in pure and applied research to improve product quality and reduce operational costs in all stages of manufacturing
169
Production Supervisor Resume Examples & Samples
- Directly supervises employees on either swing (2nd) or graveyard (3rd) shift
- Ensure that proper resources are available to meet the job schedule, including cross-training development, department staffing structure and skills gap training plans for operator positions
- Ensure that all employees are properly trained to produce high quality work and to understand Hytek’s Quality System and its specifications
- Ensure that all employees are properly trained in the company rules, policies and safety issues
- Ensure accuracy of all timecards and attendance issues (e.g. – overtime approval, vacation requests, unexcused absences, etc.)
- Conduct performance reviews, skill assessments and performance planning for each employee that reports directly to you
- Responsible for addressing and accurately documenting performance and/or disciplinary issues for direct reports including performance improvement plans as necessary
- Communicate important issues and concerns to production management on a timely basis and proactively when possible. Work closely with manager(s) on disciplinary and documentation issues
- Provide leadership for root cause analysis and corrective action investigations to safety, quality and policy related issues utilizing Real Time Problem Resolution (RTPR)
- Fully support Hytek’s Quality System and participate as required in OEM/Customer audits
- Perform basic recruiting, interviewing, and hiring practices for shift openings
- Responsible for the hiring, training, employee motivation, counseling, and discipline of employees supervised for the shift
- Lead and participate in continuous improvement activities, including 5S, visual management and execution of Kaizen workshops as necessary to serve the needs of our customers, both internal and external
- Actively support and participate in Hytek and Esterline’s continuous improvement. efforts (EOS playbook) to serve the needs of our customers
- Report and document all WISHA accidents and lead/support investigation for corrective actions and future prevention
- Crossover communication with Value Stream Supervisor/s to ensure department cohesiveness and consistency
- Generally assigned to more complex production operations with greater independent authority and broader spans of control in terms of functions directed, operational difficulties encountered, or number of employees directly and indirectly supervised
- Maintain the highest ethical standards, even when challenged from above
- Understand and live by Esterline’s ethics and code of business conduct policies
- Assist others as requested or needed
- Attention to detail, ability to read and follow directions, proficient with Microsoft office (Word & Excel)
- Work closely with employees throughout the shop, with timely response to employee needs and support
- Ability to lead, coach and mentor others for increasing abilities including skill development and position expectations
- Work successfully with different personalities and individuals with varying abilities
- Successfully address substandard effort or performance and implement improvement plan to achieve necessary expectations
- Must have strong customer service skills, be flexible, reliable and consistent with meeting task completion dates
- Knowledge of specifications, tools and equipment used throughout the shop and the ability to read and interpret work orders and purchase orders is preferred
- Must be able to work effectively in a team environment, while providing leadership and achieving department expectations
- Excellent responsiveness and customer focus
- Must be dependable and able to maintain good attendance track record
- Approachability
- Directing Others
- Interpersonal Savvy
- Motivating Others
- Sizing Up People
- Organizing
- Planning
- Building Effective teams
- Fairness to Direct Reports
- Drive for Results
- 3-5 years of relevant experience, preferably in a supervisory or leadership role
- Manufacturing or Finishing industry experience highly preferred
- ERP experience required; MRP experience a plus
- Six Sigma or Lean Certification a plus
- Experience with Oracle Syteline a plus
170
Production Supervisor Resume Examples & Samples
- Provides direction and defines activities to the personnel of the assigned manufacturing area through production leads to attain production goals consistent with delivery, quality and cost requirements
- Reviews and establishes department standards and practices
- Responsible for assuring that product quality is maintained at assigned standards
- Responsible for training, employee motivation, performance evaluations and disciplinary actions of assigned personnel
- Assists with implementation of Lean Manufacturing concepts and 5S activities
- Confirms that the maintenance of machines and equipment, including calibration is complete and up to date
- Ensures daily production activities are entered into IQMS system accurately
- Prepares daily work status updates for the Production Manager and Director of Manufacturing
- Implements, coordinates, contributes and assists with other projects as assigned, including team participation
- Understands and live by Esterline’s ethics and business conduct policies
- High school diploma/GED or equivalent work experience. Bachelor’s desired
- 5 years’ experience with troubleshooting injection molding process and machines, compression molding processes, or assembly processes
- Minimum 5 years of leadership/supervisor experience in manufacturing operations; preferably in an injection molding environment
- Strong verbal/written communication, organizational and interpersonal skills
- Leadership skills as effective communication, conflict management, persuasive, team player, people focus
- Bilingual in English desired
- The Production Supervisor is capable to effectively communicate clear and specific instructions to all personnel he interacts with
- The Production Supervisor is an active listener such that is able understand other people’s views and create, propose and reach agreements that will foster team work in order to achieve the desired results
- Possess Supervisory and leadership experience in a manufacturing environment
- Proficient with Outlook email, Microsoft Office (Word, Excel) and IQMS system or similar MRP system
- Knowledge of AS9100 procedures and policies
- Ability to write and comprehensive reading of Spanish
- Ability to read, write and speak English at a basic level. (Preferable)
171
Production Supervisor Resume Examples & Samples
- Min Bachelor Degree in Food/Agricultural processing technology or equivalent
- At least having 5 years experience in food manufacturing with know how in food processing, GMP and HACCP, ISO and project management
- Experience in leading a team with minimum size of 150 people
- Good knowledge on Food Safety System and Safety Management
- Strong analytical to solve processing issues
- English proficiency, both of oral and written
- Familiar with SAP Production
172
Production Supervisor Resume Examples & Samples
- Be a change agent and drive out waste throughout the manufacturing operation through the deployment of the Lean methodology
- Drive a continuous improvement culture by involving employees in problem solving and decision making as well as recognizing them for exceptional work
- Leading the day-to-day production activities within the value stream(s) to ensure that current commitments are achieved while improvements are being made
- Track daily performance through the use of process center communication boards on a daily basis
- Assures a clean and safe working environment for all employees, emphasizing prevention of potential problems and hazardous conditions, and supports Pentair’s safety programs
- Responsible for requisitioning, placing, training, directing, appraising, disciplining, or other actions relating to the manufacturing operations employees assigned to the Production Area / Value Streams
- Assist with the development of current and future state value stream maps and continuous improvement plans, as well as the implementation of those plans
- Support new process and product development and implementation
- Be highly visible to associates and promote hands-on, high involvement approaches to problem solving
- Develops key improvement projects and performs other related duties as needed
- Ability to move about within the facility in the facilitation of work teams, problem solving, and communication with employees and management
- People management in the areas of: performance management, time and attendance, and progressive discipline
- 2 year degree required, 4 year degree preferred
- 5-7 years manufacturing experience, with a preference for manufacturing leadership experience
- 1-3 years’ experience in leadership
- Experience managing automated manufacturing systems preferred
- Experienced with operating computers specifically Windows platform, Work and Excel, Lotus Notes, JD Edwards and Internet
- Demonstrated understanding of Lean Manufacturing concepts
- Knowledge of process improvement concepts and methods along with the flexibility and adaptability to accept, support, and deploy new processes in a changing business environment
- Skilled at effective communications at both technical and leadership levels. Skills must include good interpersonal skills, as well as verbal communication skills and ability to understand information and ideas as presented
- Skill in conflict resolution including the ability to address difference of opinions or facts and use the most appropriate method to reach an effective solution
- Ability to build and maintain effective working relationships, both internal and external, and establish credibility with business partners
- Ability to effectively coach and foster staff growth and development
- Ability to evaluate and motivate personnel
- Ability to adapt to rapidly changing business circumstances; must be able to thrive in a constantly changing business environment
173
Production Supervisor Resume Examples & Samples
- This position requires a Bachelor's Degree in a Manufacturing, related discipline, and/or three to five years of progressively more responsible supervisory experience in medical devices or equivalency
- This position also requires demonstrated communication and human relation skills
- Excellent leadership and communication skills both written and oral
- Lean Manufacturing experience is required ( 5S, Kanban, One piece flow, waste elimination, visual management)
- Analytical and administrative ability
- Knowledge of MFG/PRO and word, outlook and excel skills are required
- Experience working within an FDA regulated environment
- Experience managing a departmental budget
- Experience working to environmental health and safety regulations
- Black belt Certification or Six Sigma a plus
174
Production Supervisor Resume Examples & Samples
- Must have prior supervisory experience in a manufacturing environment for at least 10 direct reports
- Demonstrated leadership qualities and the ability to coach/mentor others
- Experience in successfully driving production of quality products in a way that meets business goals and operations metrics
- Demonstrated understanding of business budget for ones area
- Bachelor’s Degree required. Preferred disciplines: Engineering; Business
- Minimum of 3+ years supervisory experience in a manufacturing environment for at least 10 direct reports
175
Production Supervisor Resume Examples & Samples
- Technical proficiency in troubleshooting mechanical and repair issues
- Assists Production Manager in establishing production, quality and cost control standards, production, product and staffing scheduling,
- Plan and execute production activities and established production priorities for products in keeping with effective operations and cost factors
- Coordinate production activities with purchasing, maintenance, engineering and quality control activities to optimize team members and equipment
- Assist Production Manager by providing data and analysis on production, quality control, maintenance, and operational issues to determine causes of nonconformity with product specifications, operating or production problems
- Identify and implement business improvement processes to achieve results
- Partner cross functionally and with operators to review production activity, waste/scrap, and quality reports to identify and implement improvements
- Provide coaching and development of operators and leads
- Assist in implementing and coordinating organizational policies and goals
- Enforce compliance to quality systems including FDA, ISO and GMP and partner with Quality function
- Support an environment of open communication and employee involvement
- Manage time and attendance system
- Ensure effective transfer of information between shifts
- Minimum of High School Diploma, Secondary education degree preferred
- Minimum of 2+ years of relevant experience in a highly regulated industry. Medical Device preferred
176
Production Supervisor Resume Examples & Samples
- Directs the activities of employees engaged in manufacturing activities including but not limited to training and supervising, maintaining a positive work environment, ensuring compliance with safety standards and established policies and procedures
- Supervises production line set-up including but not limited to testing and adjusting line equipment prior to operation and ensuring production line starts on schedule
- Supervises all production activities performed by employees; maintains a high degree of visibility and access to employees throughout the shift
- Establishes and maintains department standards for productivity, reliability, and accuracy
- Monitors and reports daily production results, material usage, waste, and downtime
- Coordinates with quality control to maintain quality standards; takes appropriate corrective measures to resolve deficiencies
- Forecasts staffing needs to meet peak demands of the business and staff team accordingly; trains, motivates, coaches, rewards, and disciplines employees being supervised; resolves personnel issues
- Coordinates with the production manager to manage personnel issues including but not limited to vacation approvals, time card approval, daily and weekly overtime, hiring, and training
- Assists production manager with development and implementation of policies and procedures; ensures all established policies and procedures are followed by employees
- Inspects for proper sanitation of equipment and facilities; takes corrective action to resolve deficiencies
- Resolves production-related issues with representatives from other department throughout the company
- Maintains safety programs and all required safety training for employees
- Has the independence and authority to perform required tasks to ensure all provisions of the quality system are met
- Able to routinely make a decision which may affect immediate operation and have a company- wide impact
- Knowledge of production practices and procedures
- Demonstrated proficiency in supervising and motivating subordinates
- Basic competence in subordinates’ duties and tasks
- Strong organizational, problem-solving, and analytical skills
- Proficient on Microsoft applications
- Good judgment with the ability to make timely and sound decisions
- Bilingual skills a plus
- Ability to effectively communicate with people at all levels and from various backgrounds
- Must be able to speak, read, write, and understand the primary language(s) used in the workplace
- Bachelor’s Degree in Engineer or related field required
177
Production Supervisor Resume Examples & Samples
- Provide strong people leadership with a focus on creating/maintaining a positive work environment through effective communication, performance management, accountability, etc. This includes time and attendance review and maintenance for all department employees
- Ensure all SOPs are current, and training on SOPs and processes remains current
- Analyze Production efficiencies downtime and waste. Lead teams to improve the results. Participate in finding a ‘better way”
- Write investigations and CAPA actions for non-conformances in the department. Work with QA to quickly resolve any variance or document errors so that product may be released on time. Lead Problem Solving activities
- Manage staffing levels and budget spending
178
Production Supervisor Resume Examples & Samples
- Time and attendance review and maintenance for department employees
- Ensure all process training and SOP training is up to date
- Provide supervisory support across three shifts. This includes administering disciplinary actions. Manage the work environment by providing a conduit for employee concerns and issues
- Write investigations and CAPA actions for non-conformances for Bulk and Gamma departments. Write and maintain SOPs and other manufacturing specifications and Manage the department budgets
- Monitor and take action to improve department metrics including scrap, non-conformance, batch record errors and plant efficiency
- Order indirect materials and equipment to support the process
179
Production Supervisor Resume Examples & Samples
- High School Diploma or Equivalency required
- Demonstrated leadership experience with at least 1 year of previous supervisory experience
- Must be able to work flexible hours, including some weekend work as assigned
- Basic computer skills required, including ability to use Microsoft Outlook for e-mail
- Experience in a manufacturing/production environment
180
Production Supervisor Resume Examples & Samples
- Implements a staffing plan by identifying resource requirements, writing justifications for additional personnel, obtaining approval for changes, and co-ordinating the selection process with Human Resources (HR)
- Monitors daily work operations and provides direction to predominantly non-exempt and entry level staff to achieve unit or departmental goals
- Interacts with internal and external customers, by meeting regularly, responding to requests and explaining procedures
- Interprets and executes policies that affect individuals within the assigned organisational unit or department
- Monitors compliance with company policies and procedures (for example (e.g.) compliance with Food and Drug Administration (FDA), British Standards Institution (BSI), Equal Employment Opportunities regulations etcetera (etc.))
- Develops direct reports by securing appropriate training, assigning progressively challenging tasks, applying progressive disciplinary action as appropriate and conducting formal written and verbal performance reviews
- Develops work schedules for department by assessing priorities, workload and available resources
- Maintains personnel records (e.g., work schedules, vacation schedules/leaves and makes or directs modifications in the database to reflect actual changes
- (Experience/Education) National Framework of Qualifications (NFQ) level 7 qualification in a relevant discipline and 2+ years of related work experience, or an equivalent combination of education and work experience
- (Technical/Business Knowledge (Job Skills)) Monitors progress of non-exempt employees toward departmental goals; monitors costs of projects and human and material resources within a department or unit. Will perform this job in a quality system environment. Failure to adequately perform tasks can result in non-compliance with governmental regulations
- (Cognitive Skills) Develops and/or identifies new work processes and the improved utilisation of human and material resources within the assigned area or related departments; facilitates other’s participation in the continuous improvement programme; investigates and solves basic problems that impact work processes and personnel within a unit or department
- (Influence/Leadership) Promotes department goals by selecting, motivating, and training capable staff. Leads the activities of assigned staff by communicating and providing guidance towards achieving department objectives
- (Planning/Organisation) Schedules human and material resources within a department or section in conjunction with near-term plans to ensure their availability; carries out operations within an established budget
- (Decision Making/Impact) Assignments are expressed in the form of tasks; generally makes day-to-day decisions within established policies, procedures and guidelines in order to carry out the operations and processes selected at higher levels; consequences of erroneous decisions or recommendations might include delays in programme schedules and result in the allocation of more resources
- (Supervision Received) Works under general supervision. Receives limited supervision on standard issues, and detailed instructions on new assignments. Work is reviewed for soundness of judgement, overall adequacy and accuracy
- (Supervision Provided) Provides direction and guidance to predominantly non-exempt and entry level exempt personnel; evaluates performance of and assists in career development planning for subordinates; often responsible for a local functional or process activity
181
Production Supervisor Resume Examples & Samples
- SPECIFIC KNOWLEDGE
- Practical knowledge of pharmaceutical manufacturing processes
- Knowledge of pharmaceutical standards and quality systems
- Managing team
- BUSINESS UNDERSTANDING
- Basic understanding of cGMP requirements (Indonesia/ASEAN)
- Managerial Competence
182
Production Supervisor Resume Examples & Samples
- Monitors, organizes and performs all functions associated with packaging of clinical trial supplies and assures compliance to GMPs, SOPs, FDA, DEA and OSHA rules and regulations
- Implements procedures to increase productivity and decrease downtime
- Works closely with Project Management to establish manufacturing and packaging protocol section of batch record for ongoing and future studies
- Oversees both primary and secondary production areas equipped with various pharmaceutical packaging equipment including but not limted to: automated bottle line, form, fill and seal equipment, card sealing, vial and ampoule labelers, pouch equipment and medical device tray sealing
- Responsible for production involving manual and automated application of randomized labels on bottles, cards, cartons, kits, vials, syringes and ampoules
- Responsible for insuring correct placement of multiple look-alike product combinations in blister units, cards and bottles
- Employee performance evaluations, new employee hiring, disciplinary notices, employee termination, according to company guidelines and performance requirements as established in the union contact
- Develops, reviews and edits related production SOP’s (operational, maintenance, cleaning) in Documentum program
- Responsible for maintaining and ordering personnel, safety, disposable and support packaging supplies
- Review and approval of production staff vacation and personal days, along with leave of absence requests
- Responsible for entering data accurately in batch records and logbooks
- Must review completed manufacturing and packaging batch records in a timely manner
- Investigate and prepare out of specification reports and customer complaints related to production in Trackwise program
- Responsible for handling the packaging of refrigerated and frozen clinical trial material
- Security, accountability and reconciliation of controlled substance in clinical production
- Staging, reconciliation and inventory label generation in ERP system (JD Edwards)
- Data entry required for production rates, labor hours and downtime
- Responsible for daily employee assignment training
- A high-school diploma is required
- Bachelor of Science Degree in Health/Chemistry/Pharmacy related field is preferred
- Clinical Trial Manufacturing and Packaging experience is preferred
- Completed Clinical Trial training course is preferred
- Computer literate (Microsoft Suite, Word, Outlook, etc) is required
- JD Edwards experience or similar ERP systems experience is required
- Working knowledge of cGMPs, DEA and OSHA rules and regulations is required
- Leadership and team building skills are preferred
- Demonstrate ability to train, motivate, direct and supervise production personnel are required
- Knowledge of packaging equipment in a Just-in-Time environment is required
- Proven ability to develop Standard Operating Procedures is preferred
- This is Second Shift, 4:00 pm to 12:30 am. Selected incumbent must be willing and able to work these core hours
- 5+ years Clinical, contract or production experience
183
Production Supervisor Resume Examples & Samples
- Manage and organise Operators to meet agreed Production schedules and targets and to make efficient use of available resources, monitoring their work to ensure they achieve a right first time approach
- Liaise with relevant departments to ensure work proceeds to schedule within company GMP/SHE standards as detailed in SOPs
- Monitor Operators time keeping and absence and take appropriate action where necessary ensuring that relevant targets are met
- Take appropriate investigative and/or disciplinary action necessary in misconduct/poor performance situations
- Monitor the performance and potential of Operators and provide the direction, training
- As a member of the collective team, attend regular production meetings
- Any other duties which may properly be assigned to this post
184
Production Supervisor Resume Examples & Samples
- Lead production staff to ensure timely supply of product
- Schedule personnel, raw materials and equipment in line with the agreed commercial demands
- Communicate and escalate schedule conflicts & propose effective resolution
- Drive & model behaviours in alignment with company principles with a particular emphasis on speaking up for safety & quality
- Implement equipment & processes that improve productivity or safety in the facility
- Ensure staff training & development is aligned with company expectations. Coach, mentor & performance manage staff as necessary. Build an effective succession plan to support ongoing human resource needs
- Ensure that production equipment remains in an appropriate state of maintenance, calibration & validation. Liaise effectively with relevant support groups to ensure compliance
- Ensure batch documentation is completed accurately for each batch according to the outline of production
- Other duties identified & required by management
185
Production Supervisor Resume Examples & Samples
- Proficiency with computers, including the Microsoft Office (Excel, PowerPoint & Word)
- Ability to effectively work cross functionally with various groups including, Materials, Purchasing, Supply Management, Engineering, Contract Logistics Center, Finance, HR, EH&S, and IT
- Flexibility to cross training across several product lines and possibly 2nd shift
- Understand sheet metal machining and have experience with TRUMPF punch press and brake press machines preferred
- Be a voice for ACE (our business operating system) and train team members while completing daily tasks
186
Production Supervisor Resume Examples & Samples
- Supervises the activities of production associates to achieve objectives with regard to quality, cost and time. Evaluates the performance of associates and completes necessary reports. Recommends merit increases and training/development needs
- 5-7 years Operations/Supply Chain or related equivalent experience
- Investigates the Root Cause of defects and scrap, implementing corrective action
- Work requires periodic stooping/bending and frequent walking/standing throughout day
- Requires occasional lifting of objects less than 25 pounds as well as occasional lifting of objects 25 to 50 pounds
- May on occasion require lifting, with assistance, of objects weighing 50 to 75 pounds
- Requires use of protective clothing
187
Production Supervisor Resume Examples & Samples
- Work with HR and Production Manager to recruit and hire new technicians with the appropriate skill sets
- Conduct daily standup meetings, review priorities, assign tasks, identify barriers and communicate as required
- Create and maintains staffing schedules, shift plans and production schedules for production teams
- Train technicians as required on assembly processes, test operations and documentation requirements
- Identify and communicate Non Conformances to Engineering and Quality
- Oversee the resolution of Non Conformances and Implementation of corrective action as required
- Work with Production Manager and Test department to share labor resources as necessary to ensure internal deliveries support test need dates and test completion
- Identify and Coordinate the implementation of process improvements
- Direct 5S and Area Compliance activities
- Work with Facilities and Maintenance to ensure that production equipment is maintained and repaired in a timely manner
- Support audits and work with cross functional teams and quality to resolve audit findings
- Lead hardware safety tabletop meetings and pre task crew briefings
- Maintain technician training certifications and coordinate/conduct training classes as required to ensure compliance with company standards
- Work with Manufacturing Engineering to optimize Manufacturing Orders and ensure process instructions are understood
- Work with Production Planning to ensure Manufacturing Orders are released to the factory floor as required to support the production schedules
- Work with Engineering Liaison, Tool Designer and machinist to ensure tooling and equipment incorporate design for manufacturability enhancements
- Manage the creation of manufacturing process instructions and training materials required for production employees
- Interpret and communicate technical requirements to assembly and test technicians
188
Production Supervisor Resume Examples & Samples
- Bachelors’ degree in Business, Engineering or other related degree
- Minimum 5 years of manufacturing or Supply Chain experience
- Demonstrated ability to implement OSHA/EPA/NFPA programs a must
- Demonstrated verbal and written communication skills are a must
- Experience in Chemical Piping Systems and /or Electronics Automation
- SAP Experience desired
189
Production Supervisor Resume Examples & Samples
- Engage and direct employees to ensure departmental/plant goals and objectives are met
- Motivate associates to ensure that predetermined productivity, cost and quality standards are achieved or exceeded
- Determine priorities, set up schedules, assign employees to scheduled jobs, and ensure compliance with SOPs, cGMPs, company policies, work rules, and safety procedures
- Ensure availability of materials, equipment, and other supplies or resources
- Strong knowledge of Good Documentation Practices to review/audit required documents and ensure accurate completion of all paperwork
- Improve the overall department efficiency and processes by implementing improvement projects. Partner with functional leaders to drive improvement in production quality and yields
- Deliver training to new and current employees as required and update training records
- Mentor, counsel, and follow-up on employees through two-way engagement on their performance, attendance, etc
- Responsible for handling exceptions, incident reports and grievances. Investigate abnormalities and implement corrective and preventive actions for these abnormalities
- Communicate to functional leaders on departmental issues, activities, and accomplishments. Interact with a wide range of individuals at all levels
- Attend, participate, and conduct meetings as required, including cross-functional meetings when needed
- Perform safety audits and inspections, lead performance huddles and drive engagement and involvement at shop floor level
- Drive safety/quality improvement ideas and performance. Participate on Safety/Quality Teams
- Perform the functions of arithmetic: add, subtract, multiply and divide all units of measure; compute ratio, rate and percent; calculate variables and formulas
- Ability to apply logical thinking to define problems, collect data, establish facts and draw valid conclusions, to interpret an extensive variety of technical instructions in mathematical or diagrammatic form and to deal with abstract and concrete variables
- Knowledge of pharmaceutical manufacturing and plant support systems
- Experience and training in Six Sigma, Lean Manufacturing or similar programs is a plus
- Experience in driving efficiency improvements and cost savings in a manufacturing or similar environment
- Willingness to obtain required Bachelor’s degree if not already graduated
- Must be willing to work a variety of shifts if required which may include rotating shifts
- Intermediate to advanced computer skills including Microsoft Office Suite and various database software
- Attention to detail and good organizational skills
- Strong interpersonal, communication, and writing skills
- Understand and working knowledge of cGMPs
- Demonstrate initiative and ability to perform as part of a team
- Knowledge of pharmaceutical processes and equipment
190
Production Supervisor Resume Examples & Samples
- Reviews production orders or schedules to ascertain product data, such as types, quantities, and specifications of products and scheduled delivery dates in order to plan department operations
- Plans for production operations
- Reviews and recommends priority sequences for manufacturing products by utilizing knowledge of production processes, machinery and equipment capabilities
- Prepares operational schedules, and coordinates manufacturing activities to insure production and quality of products meets specifications
- Inspects production processes and methods to insure proper handling of products and equipment
- Supervises direct reports and ensures training needs are met
- Arranges for the maintenance of equipment when needed
- Ensure proper staffing of all line operations and provide employee training
- Propose, develop and justify annual operating and expense budgets
- Investigate and resolve employee complaints and production problems
- Inform plant manager regarding production activities and mechanical problems and conduct meetings with supervisory staff to review production issues
- Develop, communicate and ensure compliance with all policies and procedures
- Performs other work related duties as assigned
- Associates degree in related field and 3 years of related work experience; or High School Diploma/GED and 5 years of related work experience
- Excellent interpersonal and communication skills; and demonstrated successful ability to build positive partnerships, while work collaboratively with cross-functional business teams
- Demonstrated successful ability to organize and prioritize work to ensure timely deadlines
- Self-motivated and driven for results with the ability to work in a fast paced environment and continually striving for improvement
- Excellent problem solving, critical thinking and decision making skills
- Experience with measurement of performance to goals and standards
- Quality orientation and attention to detail
- Ability to define, prepare and analyze production reports
- Ability to perform basic IT troubleshooting
- Excellent Communication and interpersonal skills
- Prior experience and knowledge in the plumbing industry
- 3-5 years of prior supervisory experience
- Experience with manufacturing software systems
- IT Knowledge desired
- Knowledge of safety procedures, OSHA and environmental rules and regulations desired
191
Production Supervisor Resume Examples & Samples
- Assign and coordinate work, assist with employee selection, review employee performance, resolve employee issues and administer company policies in assigned department
- Recommend equipment upgrades, staffing adjustments, and process modifications
- Manage and drive departmental performance measures articulated in the Manufacturing Operating System (MOS), including visual controls and provide regular progress reports to management
- Participate in continuous improvement projects to reduce material and labor costs
- Accountable for all aspects of ISO 14001/QMS compliance within assigned area
- Demonstrated successful ability to build positive partnerships and work collaboratively with cross-functional business teams
- Must be able to remain in a stationary position 50% of the time
- Green Belt Certification or comparable problem solving certification
192
Production Supervisor Resume Examples & Samples
- Responsible for assigned department functions and all associated personnel
- Responsible for planning departmental operations by establishing priorities and sequences for manufacturing products
- Observes and coaches personnel on work related issues
- Incorporates Milgard’s vision and values into day-to-day activities and behaviors; guides and motivates others to remain committed to the Milgard philosophy
- Participates in the Leadership Development Program (LDP) for the location
- Creates and executes Milgard Preformance System objectives, meeting MPS commitments and working within the guidelines of MPS; reflects Milgard business values and the Milgard philosophy in all business interactions
- Actively develops Succession Candidates
- Minimum three (3) to five (5) years production supervision experience
- Sense of urgency and self-motivation; ability to work independently
- Ability to work under pressure and meet deadlines
193
Production Supervisor Resume Examples & Samples
- 40%- Safety/Risk Management
- Partners/collaborates with Environment, Health and Safety (EHS) and Food Safety, Quality and Regulatory (FSQR) experts to implement the most effective approach for complying with corporate safety policies and procedures
- Health & Safety: Enforces a culture of zero injury and illness
- Environmental: Understands and proactively avoid environmental impact and potential risk to the businesses
- Food Safety: Directly monitors risks associated with products. Ensures HACCP/FDA requirements are met in all food and feed processes
- Educates workforce in the food safety fundamentals and completes safety inspections and housekeeping audits
- Documents and investigates EHS/Food Safety incident data compiled by Production Supervisors to identify risks and recommend mitigation actions (i.e. safety index, RIFR, food safety index, CFSRA and FDA audits)
- Maintains direct relationship with regulatory agencies (i.e. supervisors work side-by-side with FSQR and psoosibly MDEQ)
- 25%- Customer Focus/Product Innovation/Quality Management
- Directly monitors production outcomes, quantity, and quality to ensure customer and food safety requirements are within specifications. Works with other Production Supervisors to meet customer specifications and timeline
- Documents and investigates quality data issues that occur and compiles information and provides recommendations for improvement for review by FSQR, and other Production/Operations Supervisors
- Within defined area of scope, identifies risks and recommends areas of improvement and innovation. Measures quality performance in areas that impact the customers
- Supports BU/Plant customer relationship by meeting businesses objectives and by understanding how operational performance impacts internal/external customers
- 15%- Production Financial Performance / Capital Planning Effectiveness
- Administers production budget for a department, process, or shift
- Executes purchase orders and ensures timely payment of invoices
- Accountable for compliance with department non-base capital investment plans
- 10%- Operational/Reliability Excellence / Continuous Improvement
- Executes and monitors day-to-day operations for all production processes for defined departments, process, or shift
- Implements and supports common reliability processes and ensures the reliability culture is foundational to operations (i.e. deploys common reliability processes and metrics; focus on eliminating the root-cause of reliability problems, etc.)
- Assists in planning for future production workforce needs and participates in selection of employees
- Responsible for training and on boarding new/transferred employees as well as workforce engagement, recognition, development and coaching
- 4 year degree or equivalent years in manufacturing environment
- Previous experience in a supervisory role, directly supervising and developing others
- Strong problem solving and decision making
194
Production Supervisor Resume Examples & Samples
- Supervise a team of unionized employees
- Act as a leader in health and safety management
- Participate in the progress of your department in health and safety, quality, service, productivity and continuous improvement
- Participate in the planning of the production
- Lead team meetings with employees
- Participate to the development of employees and team work
195
Production Supervisor Resume Examples & Samples
- Supervises hourly employees performing various production operations
- Administers all rules, programs and procedures that pertain to direct reports
- Responsible for on-the-job training of employees including back up operators and completing the required documentation
- Instructs new or reassigned employees in the safe and efficient operation of equipment
- Responsible for promoting and enforcing safety rules and policies. Adhering to company safety standards as they relate to daily operations
- Responsible for the production, quality, and performance of the employees
- Evaluates employees based on performance set forth in the evaluation guidelines and completes the require documentation
- Recommends candidates for hire, promotion, demotion, transfer, or release
- Responsible for maintaining labor within an assigned department levels
- Reassigns labor on idle equipment to eliminate unfavorable labor variance
- Observes production operation within area of control to ascertain compliance with safety, quality, production standards, work rules,
- Reports potential production downtime, scrap production and quality of each machine under the supervisor’s responsibility and
- A bachelor’s degree is preferred
- Job related experience for 3 - 5 year minimum
- Required on-the-job and classroom training both internally and externally
- Ability to understanding of the operating principles of all assigned equipment
- Ability to identify product defects using appropriate inspection procedures and test equipment
- Ability to learn customer specifications
- Ability to maintain inspection equipment
- Ability to effectively instruct and train other employees
- Ability to operate and functionally use a computer
- Must be able to organize, plan and prioritize
- Ability to meet deadlines and to concentrate and pay attention to detail
- Must have sufficient endurance to perform tasks over long periods of time
- Must be able to handle sensitive related and proprietary information in a confidential manner
- Must follow company policies, procedures, practices, and standards of conduct as outlined in the Amcor Corporation manuals
- Maintains an awareness of and complies with hazardous waste management and other environmental management requirements in the workplace by attending scheduled training sessions
- Must maintain professional competence, ethical integrity, knowledge, and skills
- Action Oriented. Works hard; is action oriented and full of energy; not fearful of acting with a minimum of direction or planning
- Customer Focus. Is dedicated to meeting the quality expectations and requirements of internal and external customers; acts with customers in mind; establishes and maintains effective relationships with internal and external customers and gains their trust and respects
- Decision Quality. Makes good decisions based upon a mixture of analysis, wisdom, experience, and judgment; most of his/her solutions and suggestions turn out to be correct and accurate
- Functional and Technical Skills. Has the functional and technical knowledge and skills to do the job
- Learning on the Fly. Learns quickly when facing new problems; a relentless and versatile learner; open to change; analyzes both successes and failures for clues to improvement; experiments and will try anything to find solutions; enjoys the challenge of unfamiliar tasks; quickly grasps the essence and the underlying structure of anything
- Building Effective Teams. Creates strong morale and spirit in his/her team; shares wins and successes; fosters open dialogue; defines success in terms of the whole team; creates a feeling of belonging in the team
- Drive for Results. Can be counted on; very bottom-line oriented; steadfastly pushes self and others for results
196
Production Supervisor Resume Examples & Samples
- Supervises the hourly employees performing various production operations on the shift. Administers all rules, programs, policies and procedures that pertain to the direct reports
- Ensures proper on-the-job training and development of employees. Instructs or directs the instruction of new and reassigned employees on the safe and efficient operation of equipment
- Evaluates employees based on performance set forth in the evaluation guidelines. Recommends candidates for hire, promotion, transfer or release
- Coaches and counsels employees as required by performance and rewards and/or disciplines employees as necessary to ensure safe and efficient operation of production shift
- Maintains labor within assigned departmental levels. Reassigns labor on idle equipment as necessary to eliminate unfavorable labor variance
- Observes production operation within area of control to ascertain compliance with quality, safety, and production standards, observance of work rules and the efficient operation of equipment. Takes corrective action as necessary to eliminate deviations
- Reports potential production downtime, scrap production and quality of each machine under the supervisor’s responsibility and summarizes shift data
- Follow and enforce product safety and packaging safety rules, procedures, and/or guidelines. Ensure our products are safe for intermediate and end users
- May carry out other projects and tasks as assigned
197
Production Supervisor Resume Examples & Samples
- Supervises and coordinates the employees and activities of the department/production function to ensure safety, quality, productivity, and housekeeping standards are met or exceeded
- Facilitates the on-the-job training and development of subordinates’ skills to ensure a continued high level of production and morale
- Facilitates communications and dissemination of information between crew operations
- Responsible for monitoring machine parts and supplies for production equipment as needed to maintain their good working order
- Reviews production schedules to ensure an optimization of set up changes
- Furnishes work orders and schedules for maintenance corrective action
- Required to work assigned schedule of 12-hour shifts, rotating days and nights, Monday through Sunday, working hours may vary as specified by management. Incumbent must be able to work overtime on a regular basis and/or be on call as directed by management
198
Production Supervisor Resume Examples & Samples
- Consolidate and analyze the production data to support the development of strategy and annual budget to ensure that production development is able to meet company objectives
- Plan, implement and check current and future operation requirements and production process. Coordinate and arrange monthly/weekly/daily production activities, material flow/ inventory to achieve production target in schedule and meet customer expectations including trial production
- Review and analyze production, quality control, maintenance, and operational reports to determine causes of non-conformity with product specification, and operating or production problems. Develop and implement operating methods and procedures designed to eliminate operating problems and improve product quality
- Interface and consult with engineering personnel relative to maintenance and repairing schedules, actions, including modification of machines and equipment in order to improve production and quality of products
- Interface and coordinate with relevant departments (e.g. production control, technical/process, logistics, purchasing, utility supply, etc.) to ensure sufficient supply of raw materials and to obtain optimum production and utilization of human resources, machines and equipment
- Implement the relevant safety and environment protection policies and procedures in coordination with Country EHS. Enforce all company operations, safety, ecology and housekeeping guidelines to maintain a working environment that supports work safety
- Responsible for the general management of manufacturing personnel in coordination with Human Resources
199
Production Supervisor Resume Examples & Samples
- Provide guidance of daily operations for (5) Production and (2) Shipping Supervisors in Polyol
- Seek compliance with all environmental, safety, and health requirements, and promotes a safe working environment, and ensures accountability of shift personnel for safety performance
- Provide daily support to shift supervisors in the production and shipping facilities in performance of their own duties in a Union environment
- Coordinate, communicate, and monitor daily operations activities across the shifts, and provides daily operating instructions, and provides conflict management as required
- Ensure consistency and accountability on shift regarding discipline, procedures, and grievances
- Provide Tier 2 troubleshooting of operational problems (including DCS/SISI) and safety issues that last more than one shift
- Work with Unit Production Engineers and Technologists and Supply Chain using LIMS/PIMS and other tools to monitor production performance including plant yields, quality and waste generation
- Ensure that content of operating instructions and parameters is accurate and current
- Assist other operations personnel in the Maintenance process and in obtaining guidance and training for shift personnel to promote proper operation and maintenance of the plants
- Participate in reliability performance by supporting Asset Effectiveness through root cause failure analyses and in corrective actions for bad actors
- Work with staff engineers to brainstorm Operational Excellence and capital investment ideas for a 5-year plan
- Develop detailed plans for capital project implementations by scope and model reviews, construction package review, commissioning
- Will work as manufacturing representative for some lower budget capital projects
- Support continuous improvement by working with the Lean shift teams, staff engineers and the site continuous improvement team
- Facilitate accident report investigations and action item follow-up, coordinates acceptance of new installations, participates in process hazard analyses (PHAs), and is responsible for generating and approving some Management of Change MOC documents
- Maintain weekly and daily alignment with the cluster maintenance coordinator regarding work priorities and schedule, and ensures continuity of on-going work between shifts by tracking progress and communicating status with operations personnel, and recommending appropriate actions
- Assure compliance with standard production trends and conformance with Quality process in coordination with Analytical Services
- Prepare detailed plans for operational changes such as startups, shutdowns, product changes, plant tests, bi-annual turnarounds, and outages
200
Production Supervisor Resume Examples & Samples
- Manage operators and oversee shift operation
- Manage daily job order and distribute it to each working area
- Verify daily production activity and performance
- Oversee the operation of plant and process equipment to meet customer demands
- Identify the opportunities for continuous improvement and lead action items
- Work with other teams to handle operational issues
- Drive a customer first and fast mindset throughout the Operations team as well as the rest of the organization
- BS/MS Engineering degree in Mechanical or Industrial engineering requested
- Experience in a manufacturing environment; preferably with exposure to plastics or film industry
- Computer skills to include such programs as Word, Excel, Access, PowerPoint, and Project desired
- Experienced in problem solving techniques, such as Six Sigma, Lean certification is a plus
- Excellent verbal and written communications skills in native language and English
201
Production Supervisor Resume Examples & Samples
- Manage daily production schedules, continuously ensure quality production, and realize the effects throughout the shop when these are not met
- Improve the operations effectiveness, as measured by productivity, quality, safety and communications goals, by working with various departments
- Oversee the proper training of the department workforce
- Complete production reports and safety forms
- A vocational or high school degree, with post high school courses on supervision usually obtained through the RAMAC Supervisor's Training course or another approved program and minimum 5 years of manufacturing plant experience OR a Bachelor's degree and 1-3 years of manufacturing plant experience
- Position may require handling or oversight of employees handling hazardous waste. Employee required to receive annual training on the proper handling and accumulation of hazardous waste in accordance with the applicable regulatory requirements and lnSinkErator procedures
202
Production Supervisor Resume Examples & Samples
- Ensures that employees’ training requirements are met and maintains associated records
- Reviews employees’ performance and coordinates wage progression with Human Resources
- Administers discipline as needed and maintains associated records
- Communicates any production issues or changes involving procedures, fixtures, drawings, specifications, etc. to Operations Manager
- Leads toolbox meetings with employees and daily communication meetings with other Production Supervisors and Production Coordinator
- Monitors status of orders for daily shipment
- Identifies the root cause of late orders and reoccurring quality issues and implements corrective action as needed
- Responsible for Request Date Service Level, backlog reduction, safety, scrap, rework, reject rate, and warranty related issues
- Insures safety requirements are met for assigned area and personnel
- Provides coordination and liaison between production groups and other manufacturing, division and corporate groups
- Communicates and implements company goals, policies and procedures
- All other tasks or projects as assigned
203
Production Supervisor Resume Examples & Samples
- Minimum 3 years supervisory production experience in a manufacturing/automotive environment
- Demonstrated ability to coach/mentor employee team members
- Proficient in all MS Office products
204
Production Supervisor Resume Examples & Samples
- Participate in Production System Efficiency and Quality System Efficiency workshops to support continuous improvement: propose and implement continuous productivity, efficiency and quality improvement actions for all facilities
- Facilitate equipment and process moves
- Recommend safety policies and assure safety controls are tested and reliable
- Keep up to date documentation related to process
- Be responsible for the computer aided process management system
- Manage a team of Process technicians
- Bachelor's degree in engineering, preferably with a specialisation in Maintenance and Process
- Strong people management skills, interpersonal and communication skills
- Ability to work in a matrix organisation
205
Production Supervisor Resume Examples & Samples
- Drive actions for improvement: communicate with the Autonomous Production Unit Manager, Production Supervisors of other shifts, and support functions to ensure a transparent information flow, collaborate to define improvement areas and precise action plans
- Manage team performance: know team problems, define areas for performance improvements with team members, drive teamwork, lead problem solving groups, lead workshops on quality improvement methods (5S, TPM, 6M…)
- Ensure daily team management: assure appropriate headcount, ensure the respect of standardised work methods, assure presence on the floor to answer questions or address problems
- Ability to work 2nd shift hours
206
Production Supervisor Resume Examples & Samples
- 2-5 years experience with leading others to achieve results
- Willingness to work a 12-hour rotating shift schedule
- Demonstrated ability to isolate and solve problems
- Proven ability to build cooperative relationships across various functions / crews / areas
207
Production Supervisor Resume Examples & Samples
- Must maintain safe work environment by consistently wearing proper PPE, performing safe work behaviors and by communicating any and all safety concerns through appropriate channels
- Responsible for communicating information to the hourly crew members
- Ensures effective employee relations. Provides employee training, coaching and development
- Assists with incident investigations
- Tracks absenteeism and time-keeping
- Performs other functions as required
- Balances quality, productivity, cost, safety and morale to achieve positive results in all performance measures. Works to continuously improve in all areas
- Participates in hiring process, retention, performance review and discipline
208
Production Supervisor Resume Examples & Samples
- Minimum of 4 years of related work experience in production / manufacturing / operations or similar environments
- Previous leadership experience in manufacturing / planning / scheduling / operations or similar environments
- Experience with Lean manufacturing / Six Sigma concepts or similar process improvement methodologies
- Ability to obtain a Security clearance
- BA or BS degree
- Previous experience supervising bargaining unit employees
- Manufacturing, Industrial Engineering, and Supervisory experience in the aerospace/defense industry
- Ability to leverage technology
- Ability to lead in a team-based manufacturing environment and make decisions with minimal supervision
- Supervisory skills with ability to use good judgment to resolve conflict
209
Production Supervisor Resume Examples & Samples
- Schedule and cost accountability
- Effectively manage day to day assignments for 15-20 represented
- 4 plus years of work experience in production / manufacturing /
- BS/BA in Operations/Manufacturing, Business, Engineering or any major
- Experience with semi-conductor fabrication
- Experience utilizing lean manufacturing and six sigma principles
- Manufacturing experience in the aerospace/defense industry
- Excellent communication (written and verbal)
- Self-directed individual
- Experience working with Microsoft Office Tools (Excel, PowerPoint, Project,
210
Production Supervisor Resume Examples & Samples
- Minimum of 4 years of experience utilizing business systems and tools that aid in manufacturing and financial management
- Minimum of 4 years leadership experience in a manufacturing environment with knowledge of manufacturing planning/scheduling and operations
- At least 1-2 years utilizing lean manufacturing concepts with a proven track record of lean / six sigma implementation projects
- High computer literacy and proficiency working with Microsoft Office Tools (Excel, PowerPoint, Project, Access) and familiarity with paperless Shop Floor Control Systems
- Able to obtain a DOD government clearance
- BA or BS degree in business field, technical field, or in industrial engineering with demonstrated applicable work experience in production/manufacturing environments
- Previous experience utilizing a shop floor data management system
211
Production Supervisor Resume Examples & Samples
- Execution of schedule and cost
- Workforce planning and forecasting
- Employee hiring and training
- Time and attendance tracking
- Area layout and flow management
- Capital identification and control of overhead expenses
- Ensuring the enforcement of company policies and procedures
- 4 plus years of work experience in production / manufacturing / operations or similar environments
- Previous leadership and management experience in manufacturing or similar environments
- Experience with Lean manufacturing and/or Six Sigma or other similar process improvement methodologies
- Experience utilizing business systems and tools that aid in managing labor, processes, and budgets
- Ability to obtain a classified security clearance
- Experience in an electrical assembly/ cables environment
- Experience utilizing lean manufacturing concepts with a proven track record of lean / six sigma implementation projects
- Basic knowledge/understanding of theory of constraints
- Manufacturing or Industrial Engineering experience in the aerospace/defense industry
- Solid people management and interpersonal skills; uses good judgment to resolve conflict
- Experience working with Microsoft Office Tools (Excel, PowerPoint, Project, and Access)
212
Production Supervisor Resume Examples & Samples
- Responsible for the day-to-day operations for the manufacturing functions. Defines goals, improves technologies, and determines best course of action to meet schedules and/or resolve technical issues. Translates customer requirements into state-of-the-art manufacturing strategies and process, resulting in cost-effective processing and profitable manufacturing of company products
- Owner of the plant escalation process to ensure schedules are maintained. Works closely with other plant support functions, communicating the status of operations and requesting assistance from them when required
- Determine that labor resources are sufficient for successfully meeting production requirements and assure that these resources are properly trained and being used to achieve maximum capacity. Labor flexibility is a key initiative that is being driven in the plant. You will monitor operations in conjunction with the EHS Coordinator assuring that we are following all safety and environmental regulations and specifications
- Drive plant continuous improvement efforts and lean concepts with team. Supporting them through the PIM and tier processes
- Rapho Park is going digital (implementing a shop floor system) in the next fiscal year and this position will be integral in the success of the implementation, providing communication throughout the process
- Bachelor's degree, preferably in an engineering related discipline
- Prior supervisory or leadership experience is strongly preferred
- Experience in the use of Six Sigma tools and lean manufacturing techniques
- Experience in lead time reduction and cost savings activities
- Prior experience in a plant lean transformation is a plus
- Effective written and verbal communications/interpersonal skills
- Ability to multi-task and react decisively to changing priorities
- Skilled in the use PC and software applications ( MS Word, Excel, Power Point, Project)
- Experience with MRP and CRP manufacturing applications a plus
- US Citizen or Green Card Holder
213
Production Supervisor Resume Examples & Samples
- Perform various administrative tasks such as training, resolving customer complaints, holding weekly communication meetings with associates and awareness of team goals
- Prepares employee job performance evaluations and conducts reviews
- Administers company policies concerning hiring, promotions, disciplining and other related areas requiring guidance in conjunction with the manager and human resources
- Keeps Operations Manager and Plant Administrator informed of unusual or anticipated problems
- Ensures that safety standards are followed and safety remains top priority
- Prior experience in manufacturing environment in a supervisory or managerial role
- Working knowledge of quality systems and manufacturing processes required
- Proven ability to lead/drive change using lean manufacturing techniques required
- Ability to communicate effectively - verbal and written
- Ability to demonstrate strong leadership capabilities
- Must possess strong mechanical troubleshooting skills and be able to train associates in the team
- SAP experience highly desirable
- US Citizen or Perm Legal Resident Required
214
Production Supervisor Resume Examples & Samples
- Direct supervision of cells as required. Communicate all vital information to cell members; direct duties and work assignments; track, approve and address attendance issues; administer discipline and monitor performance [1 to 5 cells]
- Coordinate daily manpower moves within the cell to achieve maximum production output at lowest cost and schedule overtime as required
- Monitor, and control OME usage for production cell(s) to meet budget requirements
- Monitor, recommend and implement new processes and process improvements to improve labor costs
- Monitor and maintain the quality system for the production cell
- Investigate, review and implement new salvage methods to maintain and improve new material usage costs
- Investigate and implement corrective actions on accident reports and maintain a safe and ergonomically sound working environment
- Maintain the Environmental standard
- Manage/facilitate the principles of the Volvo Production System (VPS)
- High School diploma and minimum of 2 years experience in manufacturing or remanufacturing of engines and components
- 5 years supervisory level experience in a manufacturing environment (preferably in a union shop)
- Knowledge of the principles of Total Quality Management (TQM)
- Basic knowledge of remanufacturing concepts/processes
- Demonstrated experience in lean manufacturing implementation
215
Production Supervisor Resume Examples & Samples
- Assembles and installs a variety of hardware and electronic components to standard build and customized specifications using state-of-the-art technology and processes
- Produces customer approved 1st article semiconductor devices
- Integrates, configures and tests a variety of PC hardware, operating system software and peripherals
- Plans, develops and/or implements quality assurance procedures. Evaluates quality deviations to determine cause, effect, and corrective measures to remedy such deviations. Surveys customers periodically regarding accuracy of shipments, quality of product, efficiency of process, adherence to specifications and overall customer experience
- Ensures work area is well maintained and in compliance with all safety regulations and department policies including Electro Static Discharge (ESD) requirements
- Ensures equipment is safe, in good repair, functioning appropriately and calibrated to be in full compliance with required military, ISO and other quality standards. Participates in the evaluation, recommendation and implementation of new equipment or equipment enhancements
- Creates, reviews, updates, presents, manages and/or contributes to a variety of statistical, narrative, financial regularly scheduled and ad hoc written and oral reports and presentations
- Assesses productivity measures, identifies trends and monitors department activity
- Typically 5+ years relevant work experience
216
Production Supervisor Resume Examples & Samples
- To supervise the production line in order to finish the production requirement by using the minimum resources
- Carry out orders and company policy and implement with production operators
- Ensure that the operators do work right the first time and work according to TQC and work instructions
- Co-ordinate with related departments to solve day to day production problems
- Improve productivity and reduce the cycle time
- Train line leader and operators
- Work with the project team members to have the continuous improvement to the project yield and quality
- Control the production equipment properly to prevent any damage and lost
- Manage day to day production work
- Support other dept. To solve the related problems
- Keep the discipline and factory cleanliness according to company policy and ensure the operators work in a safe environment
- Education Qualification : College
- Be able to write and speak English and Mandarin
- 2-3 years management experience in HMLV manufacturing mode
- Good team work
- Be able to work under pressure
217
Production Supervisor Resume Examples & Samples
- Day to day management and technical direction to a team of up to 30 personnel
- Lead and give support, advice and technical direction to a Business unit team which will support manufacturing operations
- Recommends and implements measures to improve production methods, equipment performance, production flow, floor layout, process yields, and product quality
- Understands and deploys the use of Lean Manufacturing (5S) and Process Excellence (Six Sigma) methods
- Understands and uses data, key metrics and statistical information to improve process (SPC)
- Expedites production, maximising efficiencies in all areas including support functions and meeting KPI's
- Responsible for maintaining training records to the required standards for all internal and external auditing including ISO 13485 and FDA
- Ensure that the monthly build schedule is met and disposition all material for work orders on Oracle
- Provide production plan updating for daily production meetings
- Materials must be effectively managed and accounted for using the MRP system
- Eight - Ten (8-10) years supervisory/people management experience
- A minimum of 5 years manufacturing experience preferably in medical device field
- Third Level Qualification in relevant discipline and/or certification in supervisory management course
218
Production Supervisor Resume Examples & Samples
- 20% Develop strategies for operations of assigned area to include technical optimization of processes
- 10% Oversee product quality to ensure total customer satisfaction
- 5% Perform miscellaneous duties as assigned
- 5% Additional Responsibilities
- 4 year degree OR 2+ years operations leadership experience
- Experience in food operation/processing and/or manufacturing environments
- Ability to handle flexible and varying hours. Must be willing to work on all shifts
- Computer literacy and eagerness to learn SAP
- Positive attitude and problem solving mentality
- Excellent verbal and written communication skills
- Acquire and maintain knowledge of HACCP/OPRP/PRP (GMP) policies and requirements to complete all monitoring and/or verifications tasks as outlined in the policies and procedures and ensure that corrections and corrective actions, if needed, are taken per said requirements
219
Production Supervisor Resume Examples & Samples
- Demonstrate a primary commitment to patient safety, product quality and compliance with the Stryker, Quality Manual and its governing regulations
- Lead a production team to achieve plant and business objectives by creating a self-directed team environment
- Modify daily schedule according to needs
- A minimum of 3 years professional experience and previous people management experience; or equivalent combination of education and/or experience
- Demonstrate strong leadership skills with a history of driving performance
- Knowledge of ERP systems; knowledge of Oracle is a plus
- Computer literacy and use of Windows and Microsoft Office required
- Ability to instruct and train subordinates in manufacturing procedures, quality guidelines and safety requirements
220
Production Supervisor Resume Examples & Samples
- Assuring that employees perform their duties in a safe manner according to safety rules, policies and procedures AND ensure that all operations areas are in compliance with specified safety rules, polices and procedures
- Plan and supervise and be responsible for all production activities in assigned plant
- Coordinate with Supervisors of other shops to insure efficient flow of materials into and through shop
- Obtain help from staff departments for such things as tooling, equipment selection, plant layout, labor relations, cost data, safety and quality control to effectively carryout duties
- Plan and schedule work to meet completion date through Production Control Expeditors and department schedulers
- Inspect quality of work performed within the department to insure quality standards and accurate counts
- Search constantly for better ways to reduce costs by improving production techniques, tools, jigs and fixtures
- Instill in employees the desire to reduce costs
- Maintain discipline and efficiency in department
- Maintain accurate records as required for the efficient operations of the shop
- Candidate will need to be able to work any shift (1st, 2nd or 3rd); shift has yet to be determined
- 1-3 Years knowledge and experience in production manufacturing processes preferred
- Prior Supervisory experience a plus, but will consider individuals with supervisory interests and extensive knowledge of manufacturing processes
- Ability to work under pressure of time and resource constraints
- Must possess workflow and organizational skills; be self-motivated problem solver; and effectively direct, supervise and motivate assigned employees
- Strong commitment to quality/safety/efficiency
221
Production Supervisor Resume Examples & Samples
- Four years food service and/or retail experience
- Ability to perform all duties in the kitchen
- Stable work or education history with good attendance record
- Required competencies for this position are work standards and productivity, communication, interpersonal and intercultural relations, decision making, and dependability
- Additional required competencies may include financial, coaching, delegation, and planning
- Must be able to demonstrate ability to master high quality batch cooking techniques, must have the ability to develop and test recipes for quantity preparation. Provide leadership to hourly staff
- Dependability/accountability, multi-tasking, flexibility, initiative and planning/organizing are highly desirable to be successful in this position
- The ability to delegate authority and responsibility with follow up to achieve positive results
- Perform basic math and have the ability to understand and trouble shoot standardized recipes
- Lift up to 40 pounds, stand, walk, reach and stoop extensively. Knowledge of sanitation requirements
- Ability to meet daily deadlines
- Computer skills in word processing, spreadsheets, processing orders and e-mail
- Must be ServSafe certified or become certified within first year
- Ability to work effectively with individuals from different viewpoints and backgrounds
222
Production Supervisor Resume Examples & Samples
- Supervise, motivating and drive production team workers to meet production goals
- Increase operators' productivity though flexible work force project
- Guide & lead leader/ operator to carry out daily output, cycletime & problem solving
- To ensure production run according to production plan schedule and meeting delivery schedule
- To manage and control the production material inventory in production line and cost down activities
- Generate reports in OSIR, CIP for improvement
- Maintain good housekeeping and discipline foster a conductive and effective working environment as well as perform other duties as and when assigned or requested
223
Production Supervisor Resume Examples & Samples
- Degree in Engineering, Supply Chain, Business, Operations Management or related major
- Highly motivated self-starters
- Demonstrated ability to work in a fast passed results-oriented, changing work environment
- Effective coaching, facilitation, presentation and team building skills
- Bachelor's degree in Engineering, Supply Chain, Business, Operations Management or related major
- Eligible to work in United States without work authorization sponsorship
- Must pass a drug and background screen
224
Production Supervisor Resume Examples & Samples
- Participates in Environmental, Health and Safety initiatives as set forth by the company
- Bachelor's Degree in a Technical field with 5 years general experience or 5+ years operations/supervisory experience in lieu of degree
- Must have a level of proficiency with Internet, Email, and Microsoft programs
- Must be able to use excel spreadsheets and word processing programs
225
Production Supervisor Resume Examples & Samples
- Facilitate resolution to system malfunctions
- Train new employees on all procedures and old employees on new procedures
- Clean and maintain work area
- Retrieve, aliquot, and bar-code specimens for confirmation analysis
- Adherence to all established guidelines outlined in Alere’s Employee Handbook
226
Production Supervisor Resume Examples & Samples
- Plan and direct the manufacturing of orders
- Remain knowledgeable of required Eaton policies and guidelines
- Minimum of one (1) year of leadership experience working in an engineering and/or manufacturing environment
- Must be legally authorized to work in the United States without Company sponsorship
- Previous manufacturing or engineering related work experience in a manufacturing environment
- Lean/CI experience a plus – Green Belt preferred
- Prior experience working in Fabrication or Assembly
- Prior experience working in an Engineered to Order environment
- Prior experience directly supervising/managing a team
- 5 years of experience in leadership in an engineering/manufacturing environment
227
Production Supervisor Resume Examples & Samples
- Manage an excellent team of 11 production employees. Improve knowledge base matrix of team to ensure cross training and job satisfaction of the team is a priority
- Drive Zero Incident Safety culture in the facility, Safety champion for the facility leading safety stand downs and communication. Conduct appropriate training and area audits to ensure that safe work practices are consistently and constantly employed throughout the facility. Lead the elimination of safety hazards.(MESH)
- Manage 5S program and implement cycles of improvement
- Drive employee engagement culture and reward and recognition program. Fosters an environment that promotes Eaton’s goals, philosophies, and encourages continuous improvement
- Lead daily Gemba meeting and keep minutes and owners
- Ensure solid understanding of supplier’s capacity/load and adjust accordingly
- Executes cycle count program, receiving process
- Manage the daily productions schedule, issues, needs, and align staffing to optimize productivity and output
- Disciplined adherence to standard work and testing/quality procedures are followed and continuously improved upon
- Support the Eaton Quality (EQS)program in the facility, and live the Eaton Business System (EBS)
- Clearly communicate expectations and consistently hold self and employees accountable for performance. Assume personal accountability for achieving targets despite a challenging environment
- Manage the performance and development of direct reports. Effectively and swiftly recognize, coach, counsel & correct employees to support/maintain Eaton’s Values and Philosophy. Utilize leadership skills & techniques that support high levels of satisfaction, productivity and quality
- Minimum of two years of manufacturing operations, engineering, or distribution center experience
- Minimum one year of professional supervisory experience
- Required working knowledge and experience with computers
- Knowledge of manufacturing processes and systems and engineering processes
- Six Sigma experience/certification
- Proficient in Microsoft Office Suite
228
Production Supervisor Resume Examples & Samples
- Schedule production work order releases and work in progress to meet stated goals for capacity utilization, on time delivery, and cost
- Work closely with appropriate functions to ensure smooth production of Machine Shop operations. Collaborate with Accounting, Engineering, Manufacturing Engineering, Maintenance, and other plant groups, as necessary to obtain or provide assistance, coordinate efforts, expedite resolution of problem situations, etc
- Provide and maintain effective communication within the organization
- Maintain and administer Overtime boards to ensure accuracy and consistency
- Experience in the Aerospace Industry
- Experience working in a Machine Shop Operations Environment
- Knowledge of or ability to quickly learn hydraulics products and processes
- Ability to quickly analyze, identify and implement opportunities and corporate initiatives for improvement that have measurable dollar impact each year
- Customer oriented
229
Production Supervisor Resume Examples & Samples
- Establish and maintain a working environment conducive to high employee morale and productivity
- Drive and support continuous improvement initiatives to include safety, cost, service and quality
- Administer and enforce company policies, guidelines and work rules
- Review and approve all daily time allocations
- Interface with supply chain planning team on MRP requirements and develop schedules in respective areas of responsibility to meet requirements
- Support management and Leadership team to achieve monthly and annual objectives
- Implement / support 6S to maintain a standardized work area across all departments
- Manage Department budgets, overhead and training costs
- Manage the daily assignments for multiple departments and ensure appropriate execution of those assignments. Instill ownership and accountability in team members
- Clearly and effectively communicate production goals. Serve as a catalyst in employee engagement and productivity. Use data to drive action and engage employee in contributing to a continuous improvement culture
- Ensure materials are appropriately assigned to the designated cell based on customer demand and forecast requirements. Monitor and coordinate the flow of materials into the cell as needed and report; anticipate and address concerns, inefficiencies, and shortages
- Actively develop effective relationships with supporting staff members and use supporting staff members as a resource as well as serve as an effective resource to supporting staff members
- Identify and implement measures that improve production methods, performance, product quality, cell efficiency, and staff engagement of assigned cell
- Collect, maintain, and distribute scrap reporting documents daily. Manage the collection and delivery process of scrap materials daily
- Enforce performance against key metrics including the 6S Program, production levels, down time, and the integrity of the buffer system
- Ensure operator training to ensure training is complete and concerns have been addressed or reported to leadership
- Partner with leadership and the training team to execute cross training and certified operator programs
- Understand, communicate, and enforce safety regulations and requirements applicable to the cell environment
- Serve as an employer advocate (role model), positively promoting the company image and appropriately identifying, addressing or directing concerns that may have a negative impact on the company image
- Perform job duties in a manner that maintains compliance with environmental, health and safety regulations, policies and procedures
- Bachelors degree or equivalent of 10 years of relevant experience, in lieu of degree required. Bachelors in Engineering strongly preferred
- Five years minimum related experience
230
Production Supervisor Resume Examples & Samples
- Everyday coaching to engage team and develop ownership for sustainable targets achievements
- Ensure the Production Department achieves targeted results
- Responsible for factory business of global brands
- Become a front-line leader in the NCE (Nestle Continuous Excellence) continuous improvement process
- Initiate process improvements by leading the plant production group to identify potential savings and assist with their implementation
- Actively participate in the development and execution of initiatives towards achieving operating plan objectives
- Promote and enhance a positive labor management relationship including efforts to continuously improve teamwork and establish high levels of employee involvement
- Deliver effective training and performance management of Production workforce
- Coordinate with all Departments to maximize overall effectiveness and efficiency of the Production operation
- Undertake other functions as required
- Continually review existing processes and procedures in order to implement improvements
- A minimum of three (3) years’ experience as a Supervisor in a food processing operation, preferably within a unionized environment
- A university degree or college diploma in a related discipline. Can thoroughly understand company policies and procedures
- Strong computer skills, with working knowledge of factory systems and SAP highly desired
- Must be able to respond to changing demands with short notice, and be proactive in managing the needs of a 24/7 operation
- Strong interpersonal and communication skills, and excel at working within a team environment
- Demonstrated problem solving and leadership skills, and can deliver results through people
231
Production Supervisor Resume Examples & Samples
- Communicate, discuss and resolve reconditioning goals, results and problems with the Operations Manager
- Use PT Scanner, VCF and any management tool to track production and post charges
- Monitor and aide in ensuring established guidelines for a safe work environment are met to achieve compliance with OSHA and EPA regulations
232
Production Supervisor Resume Examples & Samples
- Investigate and solve quality issues and/or serve as a point of contact through which qualityissues can be resolved
- Ensure that employees know the importance of quality and enforce follow through. Work with quality control team to resolve issues and regularly review quality trends in the market
- Experience within an Engineered to Order environment
233
Production Supervisor Resume Examples & Samples
- Reports to a Manufacturing Operations Supervisor with responsibility for operations and employees in the same plant areas
- Minimum two (2) years of leadership experience in a manufacturing environment
- Knowledge of Lean and/or Six Sigma Methodologies
234
Production Supervisor Resume Examples & Samples
- Provides leadership and direction to assigned manufacturing team by leading and communicating job expectations; planning, monitoring, and appraising job results; coaching, counseling, and disciplining employees; initiating, coordinating, and enforcing systems, policies, and procedures
- Assure the development of weekly/monthly capacity plan to support master schedule with Production Planning & Manufacturing Engineering
- Accomplishes master schedule by scheduling and assigning personnel; establishing priorities; monitoring progress; revising schedules; resolving problems; and reporting results
- Work with support functions to achieve area goals, continual improve processes, and/or reduce costs. (i.e. - Planning, Quality, Supply Chain, Engineering, & Program Management)
- Lead daily stand up & weekly cross-functional team meetings
- Generate metrics & presents during monthly operations review
- Operates within limits of expense budget
- Communicate issues to operations management team
- Responsible to drive continuous improvement in all manufacturing activities
- Responsible for cost controls, quality and delivery while ensuring integrity of in process hardware and delivered products while meeting program requirements
- Approves time and attendance, including overtime, vacation, and personal time off
- Ensures assigned area is maintained in a clean and orderly fashion
- Minimum Associates' Degree in Engineering, Manufacturing, or Business or equivalent experience. Bachelor's preferred
- Minimum of 5 years previous experience in product development or manufacturing environment of a high technology product
- Minimum 2 years of supervisory experience required. 3-5 years experience preferred
- Required to have knowledge in manufacturing with a creative ability to resolve challenging technical issues
- Ability to communicate technical issues verbally and in writing to all levels of management
- Must demonstrate intimate knowledge of Six Sigma, continuous improvement, Lean and statistical methodologies
- Attention to detail very important
- May require moderate to heavy lifting usually not exceeding 40lbs
- May require working extended hours, weekends, and off shifts as required
235
Production Supervisor Resume Examples & Samples
- Direct all manufacturing personnel to ensure completion of customer requirements
- Assess performance indicators, and take appropriate actions, to ensure schedule, cost, and quality goals are met
- Ensure that required documentation and/or system transactions are executed to meet customer, manufacturing system, and financial reporting requirements
- Assure that policies, procedures, and other documentation are followed to ensure consistent and compliant manufactured product
- Provide leadership and commitment in support of continuing improvements in quality, productivity and delivery performance
- Assure that Environmental, Health, and Safety issues are addressed considering local regulations, Eaton policy, and good corporate citizenship
- Evaluate operational performance of the group in order to facilitate performance management, commendations, and improvements
- Specify job assignments for manufacturing personnel, and monitor performance, to achieve product delivery and cost requirements
- Coordinate and assist with manufacturing initiatives, participate on teams in order to drive best practices across manufacturing
- Identify critical machine for set-up reduction and reduce set-up times
- Develop and implement standardized work for all critical processes in the machining, assembly, and test areas
- Bachelor’s Degree from an accredited institution preferred
- A minimum three (3) years of supervisory experience in a Manufacturing or Operations environment
- Must be able to work 2nd Shift hours
- Relocation assistance is not available for this position. Only candidates located within a 50 miles radius of Euclid, OH will be considered
- Five (5) years of supervisory experience
- Supervision in an unionized environment
- Thorough understanding of lean manufacturing technologies and processes
236
Production Supervisor Resume Examples & Samples
- Knowledge of lean manufacturing / six sigma techniques
- Experience with food safety and general labor regulations
- Knowledge of SAP or similar production planning applications
- Prior experience operating forklifts and pallet moving equipment
- Lift, push and pull a minimum of 60lbs repeatedly
237
Production Supervisor Resume Examples & Samples
- Bachelor Degree in related field or a minimum of 3 years of experience and/ or training or equivalent combination of education and experience
- Knowledge of Good Manufacturing Practices (GMP’s), must be production oriented and have knowledge of food processing equipment
- Understanding of OSHA/USDA/ FDA requirements
- Demonstrate the ability to drive continuous improvement and manage cost out of operations in previous assignments
- Ability to work in a team oriented fast-paced environment
- Ability to identify and solve problems
- Detail and process oriented
- Planning skills
- Written and verbal communication skills
- Presentation and facilitation skills
- Must have the ability to exercise considerable judgment and strategic planning
- Must be able to work flexible hours; days, afternoons, midnights, overtime and weekend work
- Infrequent travel requirements
238
Production Supervisor Resume Examples & Samples
- Plan and lead the activities of production processes and personnel during the manufacturing/assembly of products
- Partner with the Manufacturing Manager, Production Planning, and Materials departments to establish production priorities and plans
- Meet or exceed goals established for safety, schedule attainment, labor efficiencies, scrap, rework, training, and any other production related goals
- Supervise and assist in the setup, operation, troubleshooting and maintenance of various assembly equipment and machining centers
239
Production Supervisor Resume Examples & Samples
- Established ability to work with people, both within the team and cross functionally
- Experience in developing and executing environmental and product specification verification testing
- Experience with Real Time networks/GSM is a plus
- Strong analytical, problem solving and troubleshooting skills
240
Production Supervisor Resume Examples & Samples
- Develops and implements plans for effective use of manpower, machine and material utilization
- Insures compliance with all company policies and procedures
- Understands and participates in the development of department budgets, staffing plans and obligations
- Establishes and promotes teamwork atmosphere between departments, Associates and Supervisors to accomplish company mission
- Interviews (when applicable), hires, trains, coaches and disciplines subordinates
- Participates in team projects or activities as assigned by direct Supervisor
- Monitors and maintains performance to schedule and develops plans to complete by the required delivery times
- Travel up to two weeks in duration as required
- Ability to work in a team environment & maintain regular attendance
241
Production Supervisor Resume Examples & Samples
- Is responsible for managing people: staffing, worked hours, flexibility, capabilities, feedback, coaching, performance, development, recognition, disciplinary measures
- Ensures the team is safe and all safety procedures are followed
- Ensures that the finished product is always produced in time and at the correct quality in a sustainable manner
- Ensures a strong leadership, on a daily basis, in achieving results and in improving applied practices and/or processes; is on the floor, coaches the team members and quickly implements corrective or preventive actions
- Communicates with various internal/external customers or partners in order to achieve the planned objectives and to improve business results or processes
- Education: Bachelor Degree in Manufacturing Management, Engineering or equivalent
- Minimum of 3 to 5 years experience in a manufacturing environment (Experience in a Food Industry and People Management position considered as assets)
- Knowledge: Manufacturing processes and technologies (SAP, an asset); Lean Manufacturing tools and practices (Six Sigma, an asset); fully computerized
- Is able to work with a flexible schedule in order to cover the shifts overlap and to go on shifts, if necessary
- Fluently bilingual: French and English, orally and written
- Key competencies: Strong leadership, results driven, coaching, involvement and empowerment, change management
242
Production Supervisor Resume Examples & Samples
- Coach and lead production teams in the achievement of Safety, Quality, Delivery, Cost, People, Maintenance, Environment and Productivity objectives by following standardized work
- Provide communication and recognition
- 1+ year experience in Microsoft Office products
243
Production Supervisor Resume Examples & Samples
- Manage the human, capital and material resources of the departments in such a manner to achieve continuous improvements in product and process quality, delivery and productivity
- Create a safe and healthy work environment, where open communications, positive employee relations, creativity, productivity and participation are encouraged and employees are respected, recognized and rewarded
- Select, assign, develop and manage human resources to enhance and support the company posture on positive employee relations and work force diversity, both morally and legally - responsible for hiring and retention of highly qualified staff
- Provide effective leadership such as coaching, teaching, role modeling, enabling, and empowering, to build the capabilities and contributions of all employees within the supervised areas
- Must communicate effectively through a variety of channels in a multiple shift operation, to assure that the information moves quickly and smoothly to all parts of the Sensor Fab
- Will provide organization, instruction and motivation to the team, giving general business direction to enable team members to be responsible for day-to-day decision making
- Will teach listening, conflict resolution, communication and teaming skills to direct labor employees
- Demonstrate functional knowledge and understanding of fab operations and the use of Statistical Process Control (SPC)
- Will utilize project management skills and multi-tasking to drive cycle time, cost and operations productivity
- Administrative duties such as corrective action/problem solving, time & attendance, report preparation and delivery, resource allocation
- A minimum of 7 years of experience in a Wafer Fabrication factory
- A minimum of 5 years in the semiconductor industry as a Supervisor or Lead
- Lean Manufacturing Methodology proficiency
- Working knowledge of SPC charts
- Proficiency with the following Microsoft office applications: Word, Excel, Powerpoint, Outlook and Access
- Experience driving process improvements – Greenbelt Teams
- Experience with e-charge, e-traveler, e-trac, R&M database, etc
- Experience in pulling data and creating reports for management
- Experience coaching teams to identify and improve process effectiveness
- Must be proficient leading cross-functional teams
- Project management experience handling multiple tasks driving to successful conclusion
244
Production Supervisor Resume Examples & Samples
- Ensure a safe and ergonomic work environment for the team and encourage suggestions, actions and ownership for improvement to meet desired Zero Harm environment
- Drive processes to create a standardized work environment and reduce/eliminate errors
- Oversee tactical and strategic activities, maintain accurate timekeeping records, schedule vacations, and ensure team support of company policies and procedures for the assembly and injection molding teams
- Responsible for training the team and improving flow within the cells to ensure that customer demand is met
- Establish and maintain tactical and strategic activities required to meet and improve departmental Key Performance Indicators (KPI’s)
- Conduct regular audits to verify process sustainability and identify improvement opportunities
- Communicate and escalate as necessary to get adequate support to achieve the highest results
- Ensure inventory accuracy through established depletion/replenishment systems and cycle counting processes
- Lead the training and cross training of all department team members.This includes coaching and development of all personnel assigned to assembly and injection molding
- Teach, coach and mentor process owners and leaders on how to sustain results
- Establish and maintain team schedules and staffing to ensure proper manpower coverage to meet daily demand and cost goals
- Participate directly and indirectly in kaizen events
- Minimum of a Bachelors Degree with a major in Engineering, Supply Chain or Business preferred
- 2 - 5 years of experience in a manufacturing environment
- Minimum of 1 years of prior supervisory experience in a manufacturing facility
- Lean environment and implementation experience a plus
- Able to communicate effectively (both written and oral) in English; Spanish is a plus
- Computer skills (MS Office, MS windows, Email, ERP System)
- Enjoy a challenging and fast-paced environment
- Strong analytical problem solving skills
- Strong coaching, facilitation and organizational skills
- Can demonstrate team building and rapid execution abilities
- High performance, reward for results
- Respect for the individual and the environment
- Absolute integrity
- Pragmatic, open style, candor
- Clear goals; engaged leadership
- Accountable operations
245
Production Supervisor Resume Examples & Samples
- Oversee setup and adjustment of process and production equipment
- Assist in scheduling and coordinating manufacturing operations with the site management; implement production and maintenance schedules, estimates worker hour requirements and assigned duties for job assignment completion
- Maintain time, production and maintenance records in written or electronic form
- Investigate raw material requirements and alert Quality of raw material shortage before commencing production
- Maintain appropriate inventories of basic plant and safety supplies
- May be required to cover for other department or shift supervisors as needed
- Coordinates development and skills training of department personnel
- Ensure appropriate housekeeping of regular work areas and storage areas
- Essential functions require presence in the workplace on a regular basis and an ability to work extra hours if needed. If applicable, ability to work overtime may be needed to ensure required staffing capacity to meet daily production objectives
- A minimum of a High School Diploma or equivalent with 2+ years general experience
- One (1) years supervisor experience in a manufacturing setting; OR a combination of education and experience will be considered
- Good mathematical reasoning, computer skills and mechanical aptitude
246
Production Supervisor Resume Examples & Samples
- Provide direct supervision for production employees in assigned area
- Participate in employment, staffing decisions, performance management decisions
- Drive plant wide Continuous Improvement with a special focus on making people, materials, and information flow
- Maintain all departmental work, vacation, overtime and related schedules
- Develop and implement schedules and manpower requirements to meet or exceed production plan
- Plans and prioritizes departmental production schedules based on customer delivery dates, efficiencies, and material supplies
- Monitor departmental productivity to ensure that established quality and production levels are met or exceeded
- Champion use of Eaton systems and tools to ensure appropriate execution within assigned areas
- Engage direct reports in manufacturing LEAN initiatives including but not limited to operator standard work, 5S, pull systems, empowered work teams, and structured problem solving
- Develop employees within areas of responsibility to work as a team to accomplish goals as set forth by the company
- Assesses and develops processes to adhere to FIFO and PFEP requirements
- Define, develop, and lead short and long-term strategies for PQDO logistics to deliver world-class logistics driving optimization, standardization, and overall efficiency
- Build organizational capability of logistics function including providing direction and coaching to direct reports
- Work directly with the Supply Chain Function to align logistics operations to existing supply chain and businesses processes
- Implement and support behavioral based zero incident safety culture
- Ability to communicate effectively with other departments to expedite the workflow and ensure the established quality expectations
- Minimum of 3 years of experience in a manufacturing environment
- Minimum 2 years of direct supervisory experience
- Relocation assistance is not available for this position. Only candidates in the immediate geographic area of 50 miles will be considered
- Bachelor’s Degree in Engineering
- Materials Flow Experience
- Six Sigma/Green Belt
- Employee relations investigation experience
- PMP Certification
- Proven sponsor of change
- Interpersonal savvy; ability to influence up, down, and across the organization
- Knowledge of logistics and materials flow processes
- Proficient in Microsoft Office products
247
Production Supervisor Resume Examples & Samples
- Direct daily activities related to the coordination all associates, environment and materials in the final assembly area
- Ensures individuals and teams meet customer requirements and expectations
- Schedule all present priorities to the shop floor associates and follow up through completion
- Planning and supervisory skills
- Supervisor must have excellent interpersonal skills, facilitating skills, and problem solving abilities
- 3 – 5 years combined experienced as supervisor in the present line of work
- English 90%
248
Production Supervisor Resume Examples & Samples
- Participate in the QRMP audit and assist in the development of procedures and corrective actions
- Oversee and lead the implementation of the QRMP (Quality Risk Management Process) system and operational standards as outlined in the plant accountability list
- Adhere to Kraft Heinz quality standards to ensure product quality and Food Safety by following Good Manufacturing Practices (GMP’s), standard operating procedures (SOP’s) and Kraft Heinz specifications
- Prepare departmental costs and variances with regard to productivity, short and long-range planning, labor scheduling, product scheduling, raw materials, packaging supplies, product weights, sanitation and housekeeping
- Organize and facilitate production line activities to ensure conformance to establish requirements regarding quality, safety, employee- relations, productivity and cost scheduled volume outputs
- Work with Product Development, Suppliers, Engineering, Quality, and Factory Employees in finding innovative ways to improve the Quality and productivity of our Products
- Support Employee involvement in Safety, Analytical Problem Solving, Project Planning, Vendor and Customer Relations, fostering a Team atmosphere
- Monitor and update all area practices and policies for compliance
- Work with Product Supply Group in weekly scheduling of the Packaging and Processing Area to optimize productivity
- Prepare, distribute, and follow-up with regard to all established records, reports and/or forms
- Ensure strong, effective communication across functions and with employees, vendors and government regulators
- Monitor productivity data and help develop corrective action plans necessary to achieve annual productivity improvements
- Implement safety measures for accident prevention through monthly departmental safety meetings and working with salaried Supervisors to ensure hourly employee compliance
- Report on quality defect issues and help determine necessary corrective actions to eliminate repetitive failures
- Manage operations to achieve daily efficiencies in keeping with established standards
- Manage budget of assigned department, in accordance with annual productivity improvement targets
- Suggesting new solutions to production problems and ways to improve the efficiency of an operation
- Interprets company policies to workers and enforces policies and safety regulations
- Oversee development of high performing work teams within department through coaching, training and engaging team members through effective cascading of goals, visual performance boards and ongoing communications of factory changes and performance. Embrace the KHGPS principles necessary to accomplish these objectives and support the change management techniques to develop the culture of continuous improvement and engagement
- Assist with the supervision of the Production staff including but not limited to performance management and employee development, etc
- Bachelor degree in Business, Food Technology, or related degree is strongly preferred
- 10 years of experience in a manufacturing environment is required
- 5 years of progressive leadership experience in a manufacturing environment is required
249
Production Supervisor Resume Examples & Samples
- Coordinate production requirements
- Coordinate staffing
- Serve as first line of communication on all issues
- Utilize performance management to improve employee performance
- Coordinate with other functional areas (materials, quality, engineering, techs, etc.) to resolve issues
- Participate in the implementation of business initiatives
- Maintain complete safety & environmental compliance
- Ensure completion of on the job training for new operators and technicians; ensure re-certification of continuing operators and technicians.�
- Maintain all operator and technician pay systems paperwork/documentation
- Understand and manage fundamental business –production, quality, scrap, downtime, etc
- Lead problem solving efforts (CAR, ESAR, Accident Investigations, issues on line, etc.)
- Initiate problem solving efforts
- Lead department or cross-functional projects
- Facilitate or co-facilitate formal training
- Focus on launch activities
- Maintain safety and environmental compliance
250
Production Supervisor Resume Examples & Samples
- Warehousing and Inventory Control
- SOX Experience
- Continuously Improvement Knowledge / Six Sigma
- Proficient in Microsoft Word, Excel, PowerPoint a must
- Knowledge on Statically Control and Use
- 8D Investigation Methodology
- Chemical Knowledge and Handling Experience
- Understanding of Drawings, Work Instructions and P&ID’s
- EH&S: Perpetuate the spirit of safety. Anticipate and rectify unsafe conditions or practices. Celebrate safety compliance and innovation. Enforce safety violations. Lead or participate in Hazard and Operability studies, Operational Readiness Investigations, Product Risk Reviews, Hazard Reviews, and Near Miss investigation and closure
- Quality: Ensure department compliance and participation with quality programs, processes, and events. Solicit quality improvement suggestions and respond with feedback and implementation as appropriate. Lead and participate in quality improvement projects and other related efforts. Lead quality investigations and respond to issues with appropriate safety and quality solutions
- Operations: Ensure manufacturing objectives and schedules are being met. Initiate and participate in Continuous Improvement initiatives. Ensure product meets quality specifications and investigate when it does not. Initiate and support development of engineering projects
- Supervision: Develop production employee skills and performance. Write and conduct employee performance reviews. Publicly celebrate outstanding individual and group performance. Counsel employees as required. Train and oversee training. Interview departmental candidates. Conduct written, verbal and functional qualification tests. Cultivate safety and quality oriented individual and group performance
- Administration: Write, revise and audit operational procedures. Respond to customer complaints. Conduct Root Cause Analysis Investigations. Present at site meetings. Monitor work area performance (safety, quality, throughput), SAP transactions, record keeping, inventory management, expenditures, attendance, and other items necessary to track production unit performance