Maintenance Supervisor Resume Samples
4.9
(107 votes) for
Maintenance Supervisor Resume Samples
The Guide To Resume Tailoring
Guide the recruiter to the conclusion that you are the best candidate for the maintenance supervisor job. It’s actually very simple. Tailor your resume by picking relevant responsibilities from the examples below and then add your accomplishments. This way, you can position yourself in the best way to get hired.
Craft your perfect resume by picking job responsibilities written by professional recruiters
Pick from the thousands of curated job responsibilities used by the leading companies
Tailor your resume & cover letter with wording that best fits for each job you apply
Resume Builder
Create a Resume in Minutes with Professional Resume Templates
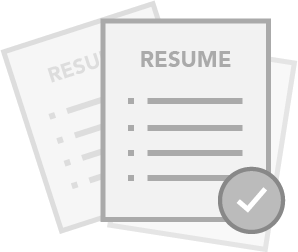
CHOOSE THE BEST TEMPLATE
- Choose from 15 Leading Templates. No need to think about design details.
USE PRE-WRITTEN BULLET POINTS
- Select from thousands of pre-written bullet points.
SAVE YOUR DOCUMENTS IN PDF FILES
- Instantly download in PDF format or share a custom link.
MK
M Kerluke
Marcus
Kerluke
64172 Misty Land
San Francisco
CA
+1 (555) 861 9752
64172 Misty Land
San Francisco
CA
Phone
p
+1 (555) 861 9752
Experience
Experience
Houston, TX
Maintenance Supervisor
Houston, TX
Hand, Botsford and Feest
Houston, TX
Maintenance Supervisor
- Work with Maintenance Manager on training and indoctrination of workers to improve work performance and acquaint workers with company policies and procedures
- Provides construction oversight on work performed by outside contractors ensuring work performed meets industry standards and related codes
- Provide leadership in support of the Site Manager and Assistant Site Manager in overseeing operational performance
- Assist in overseeing construction workers and vendors working at center, including contractors performing capital work
- Provide accurate and timely progress updates on managed work on a daily basis including contractor managed work in areas of responsibility
- Develops work teams and improve individual performance by providing training and feedback
- Under the direction of the manager, plan, monitor and evaluate employee job performance, and assist manager in conducting performance appraisals
Boston, MA
Plant Maintenance Supervisor
Boston, MA
Farrell, Bahringer and Jast
Boston, MA
Plant Maintenance Supervisor
- Supports development, implementation, maintenance, and ongoing improvement of the food safety system
- Performs or assists with difficult field jobs and handles customer service complaints related to installation, repair, or disconnection of all TWC services
- Performs such individual assignments as management may direct
- Implements corrective actions identified by key maintenance performance indicators as a means to create overall equipment effectiveness
- Effectively manage UPTIME performance
- Provides daily logs including daily scheduled and nonscheduled work sheets and equipment PMs
- Evaluate down-day performance to find opportunities for improvement
present
Chicago, IL
Senior Maintenance Supervisor
Chicago, IL
Romaguera and Sons
present
Chicago, IL
Senior Maintenance Supervisor
present
- Handle all aspects of maintenance for one or more communities and/or 500 units
- Supervise maintenance associates providing training, motivation, and performance feedback
- Monitor and direct scheduling of all maintenance personnel and vendors, and ensure staff adheres to company policies and procedures
- Track inventory for repairs and maintenance
- Assist with planning and execution of all preventative maintenance programs such as mechanical, electrical, HVAC, plumbing, fire and life-safety systems
- Ensure the knowledge of, and enforcement of, company safety policies
- Responsible for operating within the property budgetary guidelines
Education
Education
Bachelor’s Degree in Engineering
Bachelor’s Degree in Engineering
University of Memphis
Bachelor’s Degree in Engineering
Skills
Skills
- Strong interpersonal skills and ability to adapt and flex styles in a quickly changing team environment
- Excellent knowledge of electrical, general maintenance, HVAC knowledge, and repair skills
- Strong ability to effectively develop and lead a team, grasp concepts quickly, and articulate ideas effectively
- Strong planning and organizational skills -- Ability to prioritize and organize work/jobs with eye towards completion speed and general usability
- Specific course work that is highly desirable – Maintenance Planning, Reliability Centered Maintenance
- Proficient in Microsoft Office including Word, Outlook and Excel or ability to quickly learn
- Ability to use and program personal computers and programmable machine controls with demonstrated knowledge of existing/new machine programming languages
- Professional demeanor and the ability to interact with internal/external customers in a positive and professional manner at all times
- Proficient reading design drawings and blue prints, including a basic knowledge of GD&T
- Strong interpersonal skills with ability to interact with all levels of personnel in a professional manner
15 Maintenance Supervisor resume templates
Read our complete resume writing guides
1
Maintenance Supervisor Resume Examples & Samples
- Equipment Maintenance – Oversee maintenance of facility equipment to achieve key performance goals with regard to uptime, cost per unit, and utilization. Provide regular feedback on performance. Assist in development of preventative and predictive maintenance program. Oversee effectiveness and schedule work. Insure proper recording of all work orders in CMMS system, and utilize data to identify trends in repairs, evaluate equipment performance, and update business partners on work schedules and accomplishments
- Builds trust with direct and indirect business partners by explaining rationale behind processes and approach taken to decision making
- Understand computer applications
- 2) Minimum educational level
2
Maintenance Supervisor Resume Examples & Samples
- Supervise the mechanics in mechanical and electrical troubleshooting and repair of all the plant equipment including as a minimum conveyors, motors, pneumatic and hydraulics systems
- Follow guidelines, HAZMAT, PM's, CMMS (Sprocket)
- Train maintenance teams and other plant personnel in quality/safety processes and new job processes to department performance standards
- Serve as technical "go to" as point of contact for maintenance management to keep plant running at peak efficiency
- Coordinate/communicate with site personnel to identify and prevent problems that affect plant performance
- Supervise your team with established priorities related to work order completion rates
- Develop and stimulate improvement processes, techniques
- Contribute to continuous improvement of maintenance methods and
- Be responsible for monitoring and maintaining the Sprocket work order system, analyze and produce reports
- Ensure that work is performed safely and in accordance with VF Outdoor standards
- Work in a consistent and harmonious way with other shop supervisors, inspectors, stores personnel and engineers to achieve satisfactory job completion
- Specify work assignments, maintaining daily status of shop work
- Establish maintenance schedules and repair estimates
- Enforce safety regulations and conformance of company policies
- Maintains reports established as critical departmental matrices
- Maintain work schedule compliance records, PMs, work orders, and maintenance programs
- Maintain equipment and safety records
- In sure equipment repair records are maintained in Sprocket
- Regular and dependable attendance and punctuality is an essential function of this position
- May need to start shift early and stay as long as necessary to pass on all essential information to all shifts
- Maintain knowledge, understanding and adherence to Safety policies, Maintenance process. Standard Operating Procedures (SOP’s), Sanitation Rules, regulations and company policies
- All other duties, as assigned
- Mechanical/ Electrical background necessary and tech school background desired
- Exhibits a high sense of urgency when necessary
- Good delegation skills, willing to give team members the opportunity to grow
- Understand maintenance purchasing and planning practices
- Good planning and organizational skills
- Frequently works off shifts to interface with those mechanics
- Ability to direct, coach, support, and delegate as the individual team may require
- Minimum of 5 years of experience in the manufacturing environment and excellent knowledge of hydraulics, pneumatics, electrical, electronic, PLC’s, mechanical equipment, and facilities
- Ability to calculate figures and amounts, percentages, area, circumference and volume
3
Fulfillment Maintenance Supervisor Resume Examples & Samples
- Plans, assigns, supervises, and coordinates projects performed by outside vendors or staff in the performance of a variety of semi-skilled craft related work in the facility
- Accountable for the preventive maintenance program, and maintenance of production equipment and facilities
- Develop, maintain and administer an organization qualified to maintain all equipment and facilities in a safe and efficient working condition. Execute an effective preventive maintenance program to minimize unscheduled down time
- Maintain all operating equipment in satisfactory condition. Schedule needed repair to have minimum interference
- Assure that equipment is capable of operating within the specifications and tolerances established
- Consult with Plant and Maintenance Management regarding desirable modifications of existing equipment and facilities and the possible replacement of existing equipment which will improve operations and reduce maintenance cost
- Compiles reports, keeps service and work records, and order supplies and equipment as needed
- Develop objectives and standards of performance for projects within the Maintenance department required to meet departmental, divisional and corporate goals and objectives
- Plan and provide for an adequate supply and ensure control over spare parts and maintenance supplies
- May supervise custodial and grounds maintenance functions
4
Maintenance Supervisor Resume Examples & Samples
- Must be Degree/Trades Qualified in a relevant Engineering Discipline
- Must be competent in both Mechanical and Electrical Maintenance issues
- Experience of computerized maintenance systems
- Experience of working in a regulated high volume manufacturing environment
- Must have experience in supervising a group of technicians
- Must be flexible to work shift patterns
5
Maintenance Supervisor Resume Examples & Samples
- Provide effective supervision, training and coaching to assigned shift/employees to achieve the required equipment up time, equipment repairs, and production goals. Maintain department records and inventories
- Ensure that standard operating procedures and engineering procedures are current, accurate and that all work is done in compliance to ensure maximum quality
- Work with employees to resolve technical and machine problems. Schedule preventive maintenance to effectively meet production needs
- Provide the shift to shift communication link in order to keep all team members working toward the same goals. Communicate to employees all issues that affect the plant
- Maintain ongoing preventive maintenance program to ensure optimum equipment performance
- Oversee equipment upgrades and refurbishment projects, effectively coordinating with vendor support
- Ensure accurate spare parts inventory and on-site availability to support equipment repairs and upgrades
- Three years or more of industrial supervisory or similar leadership experience preferred
- Strong preventive maintenance development experience, familiarity with reliability centered maintenance principles preferred
- Able to manage multiple tasks with competing priorities, establish and achieve goals
- Able to work a night schedule, including weekday and weekend overtime
- Good computer skills, experience with Microsoft Office a must. Familiarity with CMMS preferred
6
Maintenance Supervisor Resume Examples & Samples
- Provide effective supervision, training and coaching to assigned maintenance employees to achieve the required equipment up time, equipment repairs, and production goals. Maintain department records and inventories
- Four years or more of industrial maintenance supervisory or similar leadership experience preferred
- CNC Machining Equipment experience highly preferred, high volume manufacturing also highly preferred
- Familiarity with CMMS preferred
7
Maintenance Supervisor Resume Examples & Samples
- Field education training
- Quality assurance to both Otis and the customer
- Callback reduction
- Technical support
- Expenditure of labor, materials, and other assets
8
Maintenance Supervisor Resume Examples & Samples
- Ensures proper supervision and direction of assigned maintenance shop functions and develops, trains and motivates staff capable of performing skilled crafts. Provides technical support to diagnose and resolve maintenance/repair problems
- Supervise a support group responsible for providing technical assistance and required craft services to support manufacturing and plant operations
- Implementation of preventive maintenance plant and update the timely & monitor effectiveness
- Machine History & analysis
- Identify, Procure & stock necessary spares. Identify supplier source. Commit to reduce the maintenance cost
- Writes practices and procedures for maintenance related activities and provides a source of expertise in areas that are necessary in completion of objectives
- Continuous Improvement, Equipment Accuracy, Increase Operational Efficiency, Cost Savings,
- Regulations, system, standard & process - drive & compliance i.e CPS, TPM, EOHS. Adheres to established standards, policies and practices relating to quality, cost reduction, safety, ergonomics
- Expense budgets, capital forecasts and expenditures. Planing, Monitoring & Reporting
- Experience of systems, Tools & techniques like 5S, EOHS, TPM, MTBFT, MTTR, OEE, SAP
- Experience of Hydraulic & Pneumatic system & components. Mechanical power transmission systems & components, Knowledge of Electrical & Electronic controls. Calibration, Torque Tools
- Provides miscellaneous administrative support including reportiing, manpower data, and timekeeping
- Caterpillar’s Maintenance Supervisors provide direction to both Caterpillar and non-Caterpillar resources
- Diploma/Degree in Mechanical Engg
- No. of yrs of work Experience - 7 - 14 Year
- No. of yrs of Relevant work Experience - 7 - 9 Years
- Thorough knowledge of various engineering, manufacturing and / or maintenance standards and practices and manufacturing systems
9
Maintenance Supervisor Resume Examples & Samples
- Supports production in reducing and eliminating equipment/tooling downtime and scrap utilizing good analytical methodologies (solid experience in preventive/predictive maintenance, spare parts inventory, plc upgrades, electrical)
- Supervises maintenance employees across all shifts ensuring that they are trained as required and performing satisfactorily and mechanical troubleshooting
- Maintains and issues daily job assignments; records and evaluates the results of Preventive Maintenance
- Establishes project plans and spare parts inventory to ensure equipment and tooling is operating in a safe manner and maintained properly
- Establishes and maintains a disaster recovery plan for current equipment, tooling and projects
- Participates as a member of the division’s safety committee
- Responds to safety work orders and action items in a timely manner
- Monitors, maintains and records employee’ time related to the Attendance and Time-Off Policies (e.g. vacation, medical day, bereavement, jury duty, etc). Records approved time-off requests in E-Time; and ensures required time-off requests with supporting documentation are processed completely and timely
10
Maintenance Supervisor Resume Examples & Samples
- Contributes to a cohesive, positive and clean work environment by providing guidance, performance feedback and coaching to leads and partners. Serves as the technical expert and resource for plant maintenance partners
- Creates and sustains a cohesive, positive and clean work environment
- Operates within established budgets, forecasts, cost objectives and service levels to control expenses. Supports implementation of cost, quality and service improvement initiatives
- Maintenance (5 years)
- Ability to coach and mentor others
- Proficient in safety procedures
11
Maintenance Supervisor Resume Examples & Samples
- Supervises the work in short, long and planned term maintenance of the production equipment
- Secures that the government’s rules and regulations regarding maintenance is followed
- In production equipment maintenance includes: Maintenance of forklifts, all lifting and rolling equipment, conveyors, racks, bins, compressor systems etc
- Represents the company in contact with the authorities for all the permissions, inspections, and tests that are needed for the production equipment
- Supervises the work in short, long and planned term maintenance of the premises. Premises maintenance includes: Electricity (high and low voltage), water, sewage, ventilation, telephony, heating, build and reconstruction of the facilities, yards, gates, fences, parking lots etc
- Reads and understands the machine maintenance manuals and electrical diagrams
- Communicates with equipment vendors or service department to clarify the subject for machine breakdown
- Supervises employees and gives direction and assignments to non-Caterpillar employees as needed to accommodate special circumstances and complete projects on schedule
- Provides evaluation and recommendation of contractor’s services for use in selecting contractors for future projects
- Provides professional training for technicians continuously and a guidance to support maintenance activities in both electrical and mechanical equipment repairs
- Ensures the implementation of preventive maintenance (PM) and update the PM plan timely
- Commits to reduce the maintenance cost and spare parts management
- Collaborates with technical department engineers, Section Managers, Team Members, and others
- Supervises or manages a work unit of primarily salaried or hourly employees where planning, scheduling, monitoring, and reviewing work of subordinates is required
- Responsible for expense budgets, capital forecasts and expenditures, and all personnel issues in the area including performance evaluations of subordinates
- Establishes and then monitors general policies and guidelines for projects under his/her control, to ensure specific management goals are met and desired results are achieved
- Knowledge of various engineering, manufacturing and/or maintenance standards and practices
- At least a four year degree OR 5 years of job related experience
- At least 1 year of previous supervisory role, preferably in maintenance
- Jobholder initiates communication with others outside immediate work group to work on new ideas or to counsel others, etc
- 3 to 5 years of prior relevant experience
- Experience in a metal cutting (CNC - PLC) environment
12
Maintenance Supervisor Resume Examples & Samples
- Utilize Total Preventative Maintenance System to maintain and support current the current Preventative Maintenance Program for all manufacturing equipment
- Participate, and support in WCM Maintenance best practice
- Oversee installation of new equipment by contractors
- Insure daily standardized work procedures are performed and followed
- Oversea proper repair of manufacturing equipment in the event of failure
- Maintain spare parts inventory for all manufacturing equipment
- Perform necessary in-house projects. Keep an up-to-date log of the timing of these projects
- Identify and correct any safety issues
- Contact outside companies to perform any required projects that are not completed with internal resources
- Exhibit a fair and consistent approach in supervising maintenance technicians, which follows the principles outlined in Magna’s Employee Charter to ensure a satisfied and productive workplace
- Perform the requirements of this position in such a way that will maximize the return to the Magna shareholders, while maintaining ethical business practices
- Follow company policies and business objectives in the daily management of facility operations
- Maintain technician/ employee time and vacations
- Associates Degree in a Maintenance Technician field; or equivalent combination of education and work experience
- Minimum of 5 years of maintenance experience in a manufacturing environment
- Extensive demonstrated knowledge beyond troubleshooting of Allen Bradley programmable logic controls
- Injection Molding Experience Preferred
- Demonstrated experience with Fanuc six axis robotics
- Average mobility to move around a manufacturing environment
- May require local travel
13
Maintenance Supervisor Resume Examples & Samples
- Plan, prioritize, coordinate and monitor on site construction and facility maintenance activities of outside contractors
- Supervise employees and outside contractors, including job assignment, workload monitoring, providing material, equipment and assistance to determine work flow
- Provide Product Groups with project status updates
- Assign resources as needed ensuring good resource utilization
- Develops and motivates resources to ensure objectives are achieved
- Evaluates and recommends external vendors
- Plans, implements and controls facility maintenance budget
- Manages project portfolio for facility in coordination with other functional areas
- Processes and coordinates special work orders
- College or university degree in an operations maintenance-related discipline or equivalent
- 3 to 5 years of work-related experience
- Prior supervisory experience in a manufacturing related environment
- Knowledge of Caterpillar products, policies, and procedures
14
Maintenance Supervisor Resume Examples & Samples
- Supervises employees and outside contractors' work force including assigning jobs, monitoring work load, providing material and equipment and assistance in determining when, where and how work is to be completed
- Provides Section Managers with project status updates, discusses priorities, determines overtime needs and shifts manpower to meet scheduling needs
- Ensures proper supervision and direction of assigned operations for effective utilization of personnel
- Develops and motivates contractors' supervisors and employees to assure desired standards and objectives are met / achieved
- Supervises employees and gives direction and assignments to non-Caterpillar employees as needed to accommodate special circumstances and complete projects on schedule."
- Plans, implements and controls site alterations budget with approval of Manager
- Performs various miscellaneous such as providing monthly reports on machine location and classification master, report of significant events, manpower list for upcoming month, contractors report, machine delivery dates, closed/cancel report, charges to each Value Stream Group and approves monthly time cards and charges
- Supervises employees and gives direction and assignments to non-Caterpillar employees as needed to accommodate special circumstances and complete projects on schedule. Provides evaluation and recommendation of contractor’s services for use in selecting contractors for future projects
- Lead and drive the TPM Program & Culture
15
Maintenance Supervisor Otis , Inc Resume Examples & Samples
- Improving efficiencies
- Safety auditing
- Co-Ops/Interns
- Other
16
Maintenance Supervisor Resume Examples & Samples
- Organize the Maintenance/ Mold Maintenance teams, complete paperwork (performance reviews, ordering, work orders etc.), and be active in equipment, molding and building repairs as much as possible
- Provide daily operational guidance and direction to staff on work assignments and priorities based on input from operations
- Attend the daily Production Meeting at your plant
- Assist stores keeper in ordering components for stores and repairs. Ensure proper level of spare parts and what is kept in stores
- Complete performance reviews annually
- Update the Training Flexibility Matrix and Job Description to keep them current
- Work towards attaining a 100% rating on all items in the PM program
- Ensure your Maintenance area is clean and safe
- Ensure the Maintenance Team is following all work instructions. Maintain and monitor all procedures and documentation in accordance with TS16949
- Assist with first inspections on all new equipment
- Help develop and maintain our Equipment Build Standard and standardizing components
- Actively pursue opportunities to reduce cost and improve cycle times
- Support other teams with new installations and cost reduction implementations
- Support Production by resolving all equipment/ molding related issues in a timely matter
- Support the other Maintenance teams as required during holidays
- Maintain KPI's for departments
- Help develop and maintain build standards and EOAT standards
- Secondary School Diploma required, as well as 3 year Technologist diploma in Mechanical or Electrical Engineering, or
- Leadership skills in order to coordinate the activities and communicate the requirements of the company to both internal support and external vendors required
- Experience in machine shop techniques required
- Sound knowledge in operation and maintenance of manufacturing processes required (i.e. injection molding, painting, robotics and assembly techniques); including water cooling/chilling systems and boilers; compressed air systems; security and fire protection systems; refrigeration and air handling systems; environmental control systems, rules and regulations and electrical control systems, hydraulics and schematic drawings
- Aptitude for working with numbers and a high degree of accuracy
- Effective trouble shooting for a variety of different situations/issues effectively
- Strength and ability to troubleshoot and solve problems
- Able to problem solve effectively
- Aptitude for working with numbers with a high degree of accuracy
- Proficient with Microsoft Office and AutoCAD or similar design software
- Proficient reading design drawings and blue prints, including a basic knowledge of GD&T
- Ability to work flexible work hours, including unscheduled overtime, when necessary
- Ability to appreciate and maintain the appropriate level of confidentiality
17
Maintenance Supervisor Resume Examples & Samples
- Performance management of maintenance staff, mechanical and electirical
- 10 years' experience in a solid dosage pharmacetuical enviroment
- Experience in process and packaging machinery
- Have a trade qualification and a level 7
- People managemnet skills
- Good understanding of World Class Maintenance practices and expectations
- Knowledge of maintenance systems and work practices for both electrical and mechanical crafts
- Knowledge and experience of CMMS systems is essential
- Good understanding of equipment reliability techniques such as RCM, FMECA & Root Cause Failure Analysis
- Knowledge and understanding of Lean Six Sigma DMAIC methodology
18
Maintenance Supervisor Resume Examples & Samples
- Accomplishes maintenance objectives by selecting, orienting, training, assigning, scheduling, coaching, counseling, and disciplining employees; communicating job expectations; planning, monitoring, appraising job contributions; recommending compensation actions; adhering to policies and procedures
- Meets maintenance operational standards by contributing maintenance information to strategic plans and reviews; implementing production, productivity, quality, and customer-service standards; adhering to problems
- Meets maintenance financial standards by providing annual budget information; monitoring expenditures; identifying variances; implementing corrective actions
- Evaluates and maintains functionality and reliability of equipment and machinery through preventative maintenance, operating and testing systems and equipment; restoring, repairing, rebuilding, or replacing faulty or inoperative components and parts
- Improves function and reliability of equipment and machinery by studying performance results; identifying, recommending, and implementing changes, expansions, and additions
- Accomplishes maintenance and organization mission by completing related results as needed
- Performs all work in compliance with Magna and Magna Sealing and Glass Systems Health, Safety and Environmental policies and procedures as well as all federal, State and local laws; promptly reports any hazardous conditions or workplace injury to immediate supervisor or EHS designate
- Minimum 3 years of technical leadership experience
- 5 years experience working with automated equipment in a manufacturing environment
- PLC programming
- Solid understanding of principles used in multi-axis robotic systems
- Strong “hands-on” capability in the installation and programming robotic and PLC controls systems in a manufacturing environment
- Experience working in a molding or stamping environment
- Demonstrated leadership with the ability to lead, mentor, develop, train and support technical staff members
- Strong organizational, project management, and leadership skills to prioritize, coordinate projects, manage conflicting needs, and deal with many issues at one time
- Demonstrated strong written and verbal communication skills
- Must have excellent interpersonal skills to exercise influence at various levels and functions
- Must be able to operate standard and specialized equipment/tools related to the job
- Ability to calculate and analyze data, generate reports, present information, etc
- Demonstrated ability to research and recommend new products and processes. Must be able to initiate implementation of continuous improvement processes
- Demonstrated ability to troubleshoot, update, and work on all equipment in designated area of responsibility. Must have current knowledge of electrical codes and electricity and be able to apply it to the job. Machine rebuilding and mechanical knowledge including hydraulics required
- Computer Aided Design skills required to create, update, read, understand, and work using mechanical, machine, and/or equipment documents
- Ability to use and program personal computers and programmable machine controls with demonstrated knowledge of existing/new machine programming languages
- Demonstrated good interpersonal and written/verbal communication skills to communicate with internal and external contacts and work in a team environment
19
Maintenance Supervisor A/s Resume Examples & Samples
- Provides instruction, guidance and leadership to employees by assisting in solving day to day problems
- Establish and maintain effective communications with engineering, quality assurance, production and material control support groups
- Setting and achieving priorities according to production schedules
- Maintain Top 3 issue list and develop action plan to close and prevent from reoccurrence
- Working actively with production (operators, supervisors and managers) to support schedules
- Conduct all business activity in a professional manner consistent with the positive leadership practices of building trust, empowerment, and personal responsibility
- Setting up, carrying and following up of appropriate PM Schedules for Weld Lines
- External Contact with Contractors, Suppliers – follow through and follow up on work orders and outside work
- Utilize interactive management principles when implementing progressive discipline procedures in dealing with unsatisfactory employees. Encourage professional development to enhance team performance. Cross train team members to maximize flexibility and coverage to accommodate vacations and absences
- Supervises an average of 5 - 60 employees in accordance with the principles of the Employee Charter and the policies and procedures set out in the P&F Handbook
- To communicate with and motivate all employees in the spirit of continuous improvement
- Provide appropriate safety training to personnel that operate or maintain equipment
- Promote and practice our “Safety First” policy by addressing any hazards, defective equipment or unsafe situation
- Contain, report and have safety hazards fixed by the qualified people immediately
- Know how to perform your team’s assigned tasks in a safe manner
- In your area, know how to properly lockout all energy sources, including stored energy
- Instruct and monitor your team to ensure they are following the safety rules, standard and procedure at all time
- Know what type of Personal Protective Equipment is required for the jobs in your area and ensure that your team uses personal Protective Equipment properly
- Ensure work areas are keep clean, promote and practice good housekeeping along with all fellow Team Members
- Ensure Quality Workmanship through continuous improvement and training
- Help to exceed Customer Quality Expectations with a focus on zero defects
- Ensure the Standard Operating Procedures are followed
- Participate in making and communicating improvements to existing procedures
- Ensure quality checks are performed with the correct equipment at the required frequency
- Communicate Problem Reports to other Team Members
- Report Quality issues or concerns immediately – assist in containment and corrective actions
- Be familiar with and follow all regulatory compliance with Magna, Local, State and Federal Legislations including OSHA and ANSI standards
- Additional duties (job description to be provided)
- C of Q in Industrial Electrician and/or Industrial Millwright
- 5 years hands on work related experience in Maintenance Department (auto environment)
- Strong capability and experience (5 yrs) to design, integrate and program new welding equipment using PLC (RSLOGIX 5000) and Robots (FANUC, ABB and Motoman)
- Strong capability and experience (5 yrs) to set up or modify programs of existing, new and older, using PLC (RSLOGIX 5000) and Robots (Fanuc & ABB and Motoman)
- Strong knowledge about manufacturing equipment to assist in choosing proper equipment for P&F’s requirements
- Strong capability and experience (5 yrs) to set up new equipment i.e. weld lines
- Strong knowledge and experience (5 yrs) in Hydraulics and Pneumatics
- Strong knowledge of machine safety devices
- Excellent presentation, motivation and Team building skills
- Excellent organizational, leadership, interpersonal and problem solving skills
- Ability to work effectively within team environment
- Good mathematical and communication skills
- Human resource skills and maturity in judgement required
- Prepares for problems or opportunities in advance
- Responds to situations as they rise with minimal supervision
- Makes sound decisions; bases decisions on fact rather than emotions
- Works harmoniously with others to get a job done
- Is committed to doing the best job possible; keeps commitments
- Understands, encourages and carries out the principles of integrated safety management, complies with or oversees the compliance with Company safety policies and procedures; completes all required ES & H training; takes personal responsibility for safety
- Treats all people with respect; provides a supportive work environment for the multicultural workforce
- Demonstrates knowledge of techniques, skills, equipment, procedures and materials Applies knowledge to identify issues and internal problems
- Writes and speaks effectively, using conventions proper to the situation; listens well during meetings and feedback; asks others for their opinion and feedback
- Listen and responds effectively to customer questions; respects all internal and external customers
- Anticipates problems, sees how a problem and its solution will affect other units; adapts well to changing priorities, deadlines and directions; notifies supervisor of problems in a timely manner
- Able to manage multiple projects; able to determine project urgency in a practical way; uses goals to guide actions
- Constructively helps and coaches others in their professional development; exhibits a “can-do” approach and inspires associates to excel
- Is able to maintain high standards despite pressing deadlines; does work the first time and inspects work for flaws
- Does what is necessary to ensure customer satisfaction; prioritizes customer needs
- Able to challenge conventional practices
20
Maintenance Supervisor Resume Examples & Samples
- Provide supervision and direction to the Maintenance Technicians
- Communicating daily job assignments to ensure that all equipment is maintained and serviced
- Record and evaluate the results of preventative maintenance information
- Provide assistance to Engineering and Quality as it relates to fixtures and gages that are used in the manufacture of assemblies or products
- Provide design assistance to the manufacture of fixtures, machines, tools and seat assembles. Including the use of AutoCad to perform tolerance stacks along with design of required manufacturing hardware
- Responsibile for OSHA programs related to maintenance, SDS management and Environmental regulations
- Enforcement of safety rules, policies and procedures consistently and respond to and investigate all reports of accidents or injuries in a timely manner
- Ensure all employees have a safe environment in that all hazards, unsafe actions, or unsafe conditions have been identified, corrected and/or eliminated
- Assists with safety inspections and audits including follow up action plans. Assists in the compliance of all ISO 14001 regulations
21
Maintenance Supervisor Resume Examples & Samples
- Manage a team of facility technicians
- Oversee the activity of the Press Maintenance crew
- Price, prioritize and recommend parts and supply purchases
- Review and analyze daily activity reports to organize and direct equipment repair and/or maintenance (including preventive work)
22
Maintenance Supervisor, Toledo Resume Examples & Samples
- Leading and directing the field operations in the Toledo area for maintenance, repair, and open order activities
- Provide open order sales support, scheduling and quality assurance
- Review of estimates for accurate labor and material costs
23
Maintenance Supervisor Resume Examples & Samples
- Oversees and directs maintenances employees, about daily workload, on all shifts in a safe, quality minded, and productive manner with a sense of urgency to attain production priorities as scheduled
- Fill in for the maintenance manager in his/her absence
- Hold daily pre-shift meetings on assigned shift with employees. Visits other pre-shift meetings in the department to provide feedback and support
- Communicates with maintenance manager and other plant personnel about maintenance concerns, providing status reports as appropriate
- Assists in the implementations and improvement of effective preventive maintenance programs for all plant equipment
- Follows and supports Victor Manufacturing’s and Magna’s operating principles, including
- May be required to adjust shifts as necessary
- Must have high school diploma or GED
- Prefer a two year degree or higher in a related field
- Knowledge of PLC, ladder logic, robotic interfaces and programming
- Two years industrial electrician
- Two years maintenance tech
- Prefer three years of supervisor experience
- Must have good organizational and managerial skills to attend to multiple tasks simultaneously
- Must be proficient in computer operations
- Must exhibit high integrity and honesty
- Ability to read, write, analyze, and interpret technical procedures, diagrams, requirements and business correspondences
- Ability to effectively and appropriately present information and respond to questions from various groups
- Ability to apply advanced mathematical concepts as appropriate
- Ability to define problems, collect data, establish facts, and draw valid conclusions
24
Maintenance Supervisor Resume Examples & Samples
- Oversee and direct team members in a safe, quality-minded and productive manner to attain production priorities as scheduled
- Monitors work areas and enforces safety and cleanliness
- Supervision of team members to include training and development, communication and enforcement of company policies and procedures, performance coaching and evaluation, and written documentation of team member performance issues
- Aligns with Business Unit Production Supervisors and Tech Support Leads to establish priorities for Emergency Maintenance, Preventive Maintenance (PM’s) and Planned Corrective Maintenance Work
- Provide input to PM Coordinator’s to improve PM task lists and develop planned work
- Reviews weekly maintenance plan and aligns with Production team on achieving the plan
- Perform quality audits of technician’s performed work for PM’s, planned corrective work, and emergency work
- Escalate major breakdowns to Tech Support Manager and develop Root Cause Failure Analysis with corrective actions
- Reviews with Tech Support Manager production, quality control, and maintenance reports and statistics to plan and modify maintenance activities
- Reads and analyzes work orders, records and performance metrics and generate management updates as needed
- Demonstrates equipment operations or work procedures to new employees or assigns employees to experienced workers for training
- Responsible for suggesting methods to improve area operations, processes, efficiency, and service level for all internal customers
- Fosters a positive and effective interdepartmental communication and teamwork
- Communicates clearly and directly with employees concerning performance expectations, productivity, and accountability
- Other duties and responsibilities
25
Maintenance Supervisor Resume Examples & Samples
- Job Functions
- Facility Maintenance - Direct responsibility for the maintenance department. Responsible for hiring, evaluating and supervising maintenance staff
- Department Safety - Responsible for implementing and enforcing proper safety practices by all mechanic personnel
- Maintenance Supply Management – Direct responsibility for management of maintenance supplies and overseeing maintenance budget. Ensure maintenance supplies on hand are accurate and contain an economically balanced level of spare parts, tools and materials
- Budget Control - Responsible for ensuring spare part and service purchases fall within budget guidelines
- Distribution Systems - Maintain existing material handling equipment to maximize product warranties and the productivity of the distribution center. Ensure implementation of functional equipment and minimizes down time during start up
- Interpersonal Skills
- Ability to coach, provide direct feedback, promote teamwork and develop employees
- Technical and Business Skills
- Mechanical and electrical abilities to support any facility or material handling systems equipment
- Mechanical/Electrical Engineering Degree preferred
- Project and time management, strong written and oral communication skills
- Material handling and facility management experience
- 5 years practical experience as a mechanic
- 3 to 5 years direct supervision experience
26
Maintenance Supervisor Resume Examples & Samples
- Responsible for the operating efficiencies of all plant equipment
- Responsible for controlling and maintaining the cost of repair and replacement of the existing plant equipment
- Accountable for the development of discipline and safety procedures of all maintenance associates
- Responsible for implementation of good, preventive maintenance
- Responsible for scheduling the manpower, availability, and spare parts to meet the operating objective as planned
- Responsible for maintaining a good working relationship with all departments and all shifts
27
Seasonal Maintenance Supervisor Resume Examples & Samples
- Develop People – Direct reporting responsibility for shift Maintenance personnel. Establish clear performance objectives for direct reports. Complete performance appraisals and provide regular feedback to associates. Schedule training for associates according to development needs. Participate in hiring process for department personnel
- Facilities Maintenance – Oversee upkeep of facility according to calendar and quality guidelines. Provide clean and safe work environment. Support janitorial staff by providing tools and supplies necessary to perform work. Complete facility improvement projects, such as painting, striping, etc
- Department Safety – Implement and enforce proper safety practices by all department personnel. Insure all equipment safety devices are intact and in working condition
- Budgeting and Purchasing – Provide input on Maintenance expense budget for facility. Allocate resources to complete work with minimal overtime. Secure parts, tools, and services within budget guidelines. Manage parts inventory to balance availability and monetary investment. Maintain accurate record of inventory in CMMS by establishing and overseeing procedures for parts usage. Interface with vendors to build business partnerships
- Project Management – Maintain current project list for facility and provide status updates to business partners. Allocate resources to insure completion within schedule guidelines. Assist with implementation of new equipment and technologies. Participate in commissioning process and make recommendations for improvement
- The Seasonal Maintenance Supervisor is a temporary assignment created to assist the campus during peak season. Upon the conclusion of the peak season, the Seasonal Maintenance Supervisor will return to his/her previous building, shift, and department
- Material handling equipment
- Electrical, mechanical, pneumatics, PLC
- Safety regulations and codes
- Strong interpersonal and human relation skills
- Ability to analyze problems, create solutions, and multi-task with attention to detail
- Associates degree in technical or business field preferred
- 5 years practical experience as a technician
- 3 to 5 years Maintenance lead role
- Material handling, facilities maintenance
28
Maintenance Supervisor Resume Examples & Samples
- Provide leadership (supervision, guidance, coaching, training and technical support) to assigned teams
- Plan, organize and manage activities of team/s and communicate clear expectations regarding department and individual goals
- Coach and develop Maintenance Lead position in support of day to day operations
- Complete Performance Reviews, Development Plans, and counselling of maintenance technicians
- Must be flexible to work any shift as assigned on an exception basis
- Manage workforce selection, placement and retention
- Develop and Implement processes and procedures working with the Maintenance manager or cross-functionally with other supervisors to improve efficiency across Value Streams
- Background in manufacturing/packaging maintenance and Lean implementation
- Advanced knowledge of computer software including Microsoft Office Suite and CMMS (Manager +)
- Knowledge of safety regulations and equipment troubleshooting
- Ability to effectively train, coach and provide performance feedback
- Ability to analyze moderately complex data (maintenance KPI metrics)
29
Reliability Maintenance Supervisor Resume Examples & Samples
- Understand, initiate, and maintain the preventive and planned maintenance system, interpret data, identify problems and trends, and formulate proper decisions to focus maintenance activities
- Utilize various computer software including, but not limited to, the Microsoft Office suite, SAP, CMMS etc. to develop and maintain maintenance KPI data
- Oversee and control Stock room inventories and efficient operations to ensure parts availability at the minimum cost
- Conduct daily communication meetings with maintenance teams to provide feedback on performance, goal progression, safety topics, operational results and business updates and seek input from maintenance technicians on methods to impact efficiency, accuracy and safety
- Identify barriers to performance and assist Maintenance Manager in identifying/analyzing root cause and effect and develop action plans to resolve
- Complete Performance Reviews, Development Plans, and counselling of maintenance technicians under his/her supervision
- Develop “continual training” strategy for maintenance workforce within area and provide the time required for training
- Lead Maintenance KPI efficiency projects
- Additional responsibilities as needed
- Background in manufacturing/packaging maintenance and Lean manufacturing environment
- Advanced knowledge of computer software including Microsoft Office Suite and Computerized Maintenance Management Systems (CMMS)
- Knowledge and experience in inventory control and stock room optimization
- Knowledge of manufacturing safety regulations and equipment troubleshooting
- Strong project management skills (planning, organizing, and resource allocation)
- Strong analytical, reasoning and problem solving skills (A3, PDCA, BDA)
- Strong training and facilitation skills
- Ability to work with and tactically influence all levels of the organization to establish best practices and standards in maintenance and execution
- Ability to motivate, foster teamwork and provide positive reinforcement to a team/s
- Ability to understand and use technical documents and OEM manuals on complex equipment
- Ability to define problems, collects data, establish facts, and draw valid conclusions (Root Cause Problem Elimination)
- Organized in Action
- Constructive Networker
30
Plant Maintenance Supervisor Resume Examples & Samples
- May be required or called upon to assist in on-the-job training of other Supervisors, Field Technicians, or vendors as necessary
- Previous cable/telecommunications experience as Field or Maintenance Technician level or higher is required
- Strong interpersonal skills required. Must be able to project a positive company image, interact professionally with customers, subordinates, vendors, and all levels of company management and maintain confidentially at all times
31
Maintenance Supervisor Resume Examples & Samples
- Oversight of GFB Maintenance Operations and Personnel by meeting business metrics goals as defined the department
- Responsible for trending/forecasting equipment efficiency and downtime utilizing SAP
- Responsible for prioritizing daily job assignments and scheduling of shutdowns
- Maintain and update PM’s in SAP
- Implement ACE and Lean Strategies to improve Quality, reduce process time and reduce operational costs
- Ensure that all assigned employees adhere to Environmental, Health and Safety procedures
- Administer GFB’s policies and procedures to ensure compliance and equitable treatment for all employees
- Perform staffing requirements and conduct performance and skill review processes for assigned employees
- Identify and resolve process improvement opportunities to enhance quality, decrease process cycle time and reduce operational costs
32
Maintenance Supervisor Resume Examples & Samples
- Ability to coach, lead and develop team of Maintenance Technicians with varying levels of proficiency and skills
- Responsible for supervision of any contractors and vendors operating within the facility on assigned shift
- 3 to 5 years’ experience in facilities / maintenance / building services management supervision preferred
33
Maintenance Supervisor Resume Examples & Samples
- Perform general maintenance and repair
- Perform and document routine preventative maintenance on equipment and systems
- Maintain comfortable building temperature
- Perform basic maintenance on H.V.A.C. equipment
- Stay within budget and tracks monthly expenses
- Responsible for planning and estimating maintenance and repair projects, as needed
- Identify and report to the Assistant to the Publisher/President repair needs and safety discrepancies when observed at the facilities. Also inform Human Resources of safety issues
- Correct all building safety issues when they arise
- Oversee and ensure the proper completion of work when performed by assigned Laborers/Contractors
- Maintain records and inventory of custodial equipment and supplies to be sure accurate reporting by vendors
- Initiate requisitions for supplies and equipment when required
- Responsible for coordination of duties of custodians and/or cleaning services to ensure an optimum level of housekeeping and cleanliness
- Perform minor plumbing repairs as needed
- Paint as directed
- Move furniture, equipment etc. as directed
- Complete required daily, weekly and/or monthly fire inspections
- Work with other Maintenance Supervisors/Managers to back one another up at their facilities as needed
- Knowledge of basic mechanical and technical applications as related to specific job functions
- Proficiency in the use of custodial equipment and cleaning materials
- Proficient use of hand tools
- Ability to perform the essential physical job functions/responsibilities of the position
- Good communication skills with the ability to relate to a diverse work community
- Exercise independent judgement and initiative
- High School Diploma or equivalence
- Five (5) years of combined basic experience in carpentry, electrical, plumbing, and other building maintenance trades
34
Maintenance Supervisor Resume Examples & Samples
- Train and evaluate Maintenance staff in venue
- Combination of 1-2 years experience in a role similar to this position
- Strong computer skills in Outlook, Excel, Word, PowerPoint and other related computer programs
- Good communication and interpersonal skills
35
Maintenance Supervisor Resume Examples & Samples
- Direct and supervise maintenance staff and other employees performing maintenance services as directed by the Maintenance Manager
- Provides customer services by greeting and assisting customers
- Respond to customer inquiries, complaints and needs
- On an ongoing basis leads and trains staff to include assisting in staffing positions to ensure that all staff members are well-informed on event specific details
- Assist the Maintenance Manager to ensure compliance with all maintenance department and venue policies ad procedures to include all safety regulations, alarm systems and fire systems
- Oversee productivity and work assignments of the maintenance staff
- Lead shift teams to clean all areas of facility and grounds before, during and after shows/events
- Communicate with the Maintenance Manager any challenges and status of all assignments prior to the conclusion of the shift
- Other tasks as assigned by the Maintenance Manager
- Handle multiple tasks simultaneously
- Remain flexible and adjust to situations as they occur
- Follow oral and written instructions and communicate effectively with others in both oral and written form
- Basic knowledge of Microsoft office programs (Outlook, Excel, Word)
36
Maintenance Supervisor Resume Examples & Samples
- Assess, prioritize, and recommend maintenance projects
- Maintain electrical equipment and lights, including bulb and ballast changes
- Perform scheduled maintenance inspections and repairs as needed
- Perform light landscaping tasks
- Perform exterior building maintenance
- Perform light construction and carpentry duties as needed
- Assist Maintenance Manager and Operations Manager with coordinating vendors and third party contractors
- Ensure that the property and facility is in good working condition
- Ensure that all maintenance tools are in good working condition and stored neatly and securely
- Ensure that rented or owned equipment is stored safely and securely
- Ensure that the exterior gates, entrances, and all buildings on property are locked and secure
- Maintain work area in a clean and safe manner
- Recruit, train, and supervise seasonal operations and maintenance employees
- All other maintenance duties as assigned
- High School diploma or equivalent required. 4-year degree preferred
- Combination of 1-2 years experience in a similar role
- Working knowledge of carpentry, plumbing, and electrical preferred
- Overall handyman skill set
- Good trouble shooting ability and problem solving skills
- Solid written and oral communication skills
- Must be able to communicate via email and utilize common Microsoft Office Suite software
- Must be punctual, reliable, works well under pressure and detail oriented
- Must be fluent in English in both written and verbal communications
- Must be able to work a varied schedule, including some nights and weekends, and every show at the facility
37
Maintenance Supervisor Resume Examples & Samples
- Safe installation and repair of equipment
- Assist Production Manager with planning of resources both human and equipment
- Assist maintenance in the diagnosis and repair of production equipment
- Understand the gauging methods to be utilized in high volume manufacturing of powertrain components
- Maintain and consult the operating and repair manuals for all plant equipment
- Ensure that an effective preventive and predictive maintenance system is in place and is clearly understood by the members of the Maintenance team
- Coach, train, develop and inspire maintenance staff
- Maintain documentation on all equipment, building infrastructure, etc. such as machine manuals, electric circuit diagrams, hydraulic-pneumatic circuit diagrams, assembly drawings, spare part lists, preventative / predictive and emergency breakdown work orders / instructions
- Maintain and develop work instructions regarding the maintenance area
- Provide equipment downtime and equipment related cost reports in order to focus on cost reduction
- Select reliable and quality suppliers for spare parts. Select reliable and quality contractors for building modifications, major machine repair work, etc
- Schedule all necessary work activities under consideration of production requirement and maintenance staff skills
- Assist management in the development of strategic short and long term maintenance plans
- Ensure work instructions are followed and millwrights, electricians and apprentices have received the proper training
- Ensure effective, non-repetitive problem solving and machine repair occurs shift to shift
- Ensure that shift maintenance reporting is processed accurately and on time
- Ensure full compliance with relevant trade standards of best practice in all work carried out by the team improvements
- Allocate jobs to employees ensuring they are trained to carry out job tasks and functions in an efficient manner, including the use of hand and power tools, safety devices and required personal protective equipment
- Ensure that plant efficiency is maintained at the highest possible level, without sacrificing safety, quality or cost standards
- Support Environmental initiatives related to ISO 14001
- Support CI initiatives of the manufacturing team
- Responsible to protect own health and safety by working in compliance with established safe work practices and procedures
- Enforce high standard of quality, integrity, teamwork and safety in all work performed by the members of the team
- Pass on information, experiences, knowledge and best practices to other maintenance employees with regards to equipment repair, preventative maintenance, problem solving, etc
- Manpower planning & scheduling including overtime planning/scheduling & Performance & Attendance management
- Ensure company policies are adhered to at all times
- May be required to perform other duties as assigned by Production Manager or his/her designees
- Initiate and embrace company change
- Pursues relative personal training for continual knowledge growth
- Grade 12 or equivalent, Technical College/University Engineering degree
- Able to use all equipment related to trade, including milling, lathe, grinder, knowledge of welding, brazing, soldering, resistance welding and knowledge of CNC programming and operating knowledge of computers, PLC programming
- Microsoft Office
- Five years related experience in an automotive manufacturing environment
- Previous supervisory experience in a manufacturing environment preferred
- Must be comfortable with heights
- Ability to use Mig, Tig and Arc welding equipment
- Ability to read and understand electrical schematics
- Working knowledge of CNC control systems
- Basic knowledge and ability to use a personal computer
- Knowledge of Safety Legislation
- Must be a team player, communicate well with others, and able to interact with all people at all levels and departments
- Posses good interpersonal skills and is results orientated
- Good working knowledge of English language (both spoken and written)
38
Maintenance Supervisor Resume Examples & Samples
- Community College graduate of mechanical or electrical technology (or equivalent combination of education and experience)
- Provincial Licence as Electrician and/or Millwright
- Able to interpret Process System P&IDs
- Demonstrated excellent understanding of process control principles and their application to SDC building utilities and plant equipment
- Ability to use PLCs to interrogate, control and troubleshoot facility processes to diagnose equipment issues
- Excellent knowledge of mechanical and physical processes
- Demonstrated superior ability to identify and repair both mechanical and electrical equipment defects
- Trained and able to use chemical protective equipment (respirators, SCBA, etc.)
- WHMIS training
- Able to work at heights and in confined/enclosed spaces
- Individual should be flexible, and able to function in an unstructured environment
- Excellent interpersonal skills and proven ability to relate well in a people-oriented environment
- Computer literacy - knowledgeable/competent in MS applications (Word, Outlook, Access, Excel)
- Willing to work rotating shifts to backfill as required
- Operate plant utilities as required to supply for production processes
39
Maintenance Supervisor Resume Examples & Samples
- Provide plant support in troubleshooting / repairs and systems improvement (optimization)
- Establish and follows-up of full project implementation including timing, concept, feasibility, design, ordering, specifications, construction, and commissioning
- Plant support in testing/ repairing/ calibrating electric or electronic components
- Analyze, record and chart documentation required for maintenance records and projects
- Prepare drawings, material specifications to requisition as required by vendors or other departments
- Develop controls, drawings, and design concepts
- Deal with vendors both parts suppliers and equipment suppliers
- Oversee and implement 5S in assigned area for Maintenance
- Supervise the assembly and installation as well as assemble and installs new equipment and is able to make modifications to existing equipment as requested
- Responsible to train new Maintenance Technicians in equipment and safety as assigned
- Responsible for performance appraisal’s of Maintenance Technicians as assigned
- Must know Allen Bradley and Pilz software
- Help PM Planner set up preventative maintenance procedures on mechanical equipment for the Assembly Dept. as laid out by the manufacturer’s specifications
- Maintain maintenance Quality standards and preventative/ predictive maintenance program for the Assembly Dept. to insure compliance with QS9000 Requirements
- Order and maintain an inventory of spare parts
- Interview and hire qualified Maintenance employees for Assembly
- Hold regular meetings for Maintenance technicians and Team Leaders so they know what is expected of them
- Attend regular meeting regarding the area assigned.(Quality, QID, Weekend planning)
- Schedule overtime for weekends or holiday shut downs
- Organize all material needed so it readily availably to have on hand and have assigned to job depending
- Supervise and maintain safety standards of equipment and work area
- Ensure new parts get ordered or returned unused part back to the correct stock location
- Attend QID 2 hour meetings on the shop floor
- Update verification forms when needed
- Practice good housekeeping on the shop floor and in assembly cells
- Work together with PM Planner on implementation of SAP PM system
- Work with Technical Department on setting up training matrix for Maintenance Techs
- Adjust & repair automotive manufacturing equipment, repairs and services, and test equipment using hand tools and power tools
- Disassemble defective equipent as well as replaces defective parts, electrical, mechanical, pneumatic, etc
- Reassemble, adjust and test repaired equipment. Equipment testing includes the ability of the maintenance associate to operate the machine during non production hours, producing quality parts to ensure machine functionality
- May specialize in repairing specific manufacturing equipent, and equipment that is not specific to the manufacturing process
- Troubleshooting and modification to maintain uptime,make modifications to improve efficiency and reliability of equipment and its systems. Oversee modifications by internal and external resources for process changes, new models and expansion
- Use computerized or manual Maintenance Information Systems to document the details of equipment related issues, repairs made, Preventative and Predective Maintenance measures taken, etc
- Make necessary adjustments to parts and machinery to ensure proper production run
- Basic robotics troubleshooting on robots
- Basic electrical circuit troubleshooting
- Use computerized or manual systems to facilitate root cause analysis for failures resulting in major downtime (as defined by management). Once the root cause has been identified, put measures in place that will prevent reoccurance within the affected business unit as well as across the facility
- Optimize/upgrade or change equipment based on safety, quality, or production requirements
- Interface with all necessary IBU associates, (production supervision, etc…to ensure issues are identified and resolved. In general, communicate with the production team.)
- Supervise Assembly Maintenance Technicians on shift
40
Maintenance Supervisor Resume Examples & Samples
- Problem Solving (e.g. 8D’s, etc.)
- Managing the Employee Charter
- Programmable Logic Controls
- Robotics
- Hazardous Communication
- Bloodborne Pathogens
- Confined Space
- Pedestrian Safety
- Emergency Evacuation
- 18001 Awareness
- 10 Hour OSHA Training
- Forklift
41
Maintenance Supervisor Resume Examples & Samples
- Manage line efficiencies, key performance indicators and down time
- Monitors the production process, checks and adjusts equipment or work practices according to standard operating procedures
- Verify the readiness of the production equipment at start-up and supervise change overs
- Manage PM/PDM, RCA, and TPM programs to insure effectiveness
- Manage Spare Parts Inventory and Budget
42
Maintenance Supervisor Resume Examples & Samples
- JLL – Mobile Equipment Technicians
- Multiple Union Labor Groups
- Fully manage Vendor contracts as required
43
Maintenance Supervisor Resume Examples & Samples
- Housekeeping Budget tracking
- Housekeeping Contract Scope Change Review
- Paint Shop Industrial Cleaning Program
- Paint Shop Water Blasting / Skid Cleaning Program
- Paint Defect Analysis Program
- Paint Shop Air Filtration Program
- Body Shop Cell Cleaning Program
- Body Shop Dust Collector Filtration Program
- General Housekeeping Program
- Vendor / Contractor Personnel
- Landscaping & Grounds Program Personnel
- Vendor / Contractor Personnel Operational Support Responsibilities for the following Support Personnel Jones Lang LaSalle – Operations Managers Jones Lang LaSalle – Mobile Equipment Technicians Multiple Union Labor Groups On-Site Management Support
- Absentee / PTO Coverage
- Weekend Management Coverage Measurable Objectives
- Safety Compliance KPI Compliance
- Client Customer Satisfaction Survey
- IPMP Score & Program Compliance
- Element K Program Compliance
- Business Plan Deployment
44
Maintenance Supervisor Resume Examples & Samples
- High school diploma or equivalent. Two years of trades schooling in electrical system design, refrigeration and HVAC
- Experience - 5+ years of experience in facility/plant engineering maintenance with at least 5 years in supervision
- Special knowledge and skills - Exposure to HVAC, fluid handling/pumping, fluid filtering, mechanical systems, carpentry, welding, and electrical systems engineering and operation Knowledge of all current facility code requirements and standards
- Must be proficient in basic computer application software such as MS Office, Lotus and E-Mail etc
- The job requires regular operation of standard office equipment, and hand tools. The job also requires operating tools or equipment with a skill level that is typically acquired through trade or vocational school training
- Good interpersonal skills, ability to communicate well in both oral and written reportsThis job requires working in a professional office setting. You may be required to lift up to 20 pounds. You may be working indoors and outdoors in a range of temperatures that may vary from hot to cold. Bending, lifting, twisting and standing for long hours may be required
- The typical work environment involves potentially high risks with exposure to potentially dangerous situations that require adherence to prescribed safety policies, procedures and precautions
45
Maintenance Supervisor Body-ktp Resume Examples & Samples
- 1+ years’ experience in Microsoft Office
- Strong interpersonal skills and leadership behaviors
- Prior experience managing a unionized work force
46
Zone Maintenance Supervisor Resume Examples & Samples
- High School or equivalent and specialized/technical training; Associates Degree is preferred
- 7 years of experience
- Thorough knowledge and understanding of all aspects of zone maintenance duties and multiple trades with progressive leadership/management/supervision experience. Demonstrated ability to lead and motivate a diverse workforce
- Supervises zone maintenance staff. Screens and interview applicants and makes hiring decisions. Trains staff and counsels or disciplines as needed. Provides performance feedback and prepares documented appraisals. Determines and/or recommends unit salary administration including raises, promotions and/or reclassifications
- Conducts building and facility inspections, Identifies safety hazards and maintenance needs. Determines course of action (e.g. repairs, and/or replacement of materials, equipment, etc.) Addresses zone maintenance workload and plans or schedules staff accordingly. Determines staff needs for peak volumes and/or special projects and arranges for temporary workers. Authorizes overtime as appropriate. Ensures staff are adequately trained and cross-trained to promote continuity of operations during vacations an extended absences
- Trains and supports staff and team leader(s). Integrates the Pay for Skills program, provides forms and supplies, schedules training, and gives/receives feedback for staff training and development. Verifies components of Pay for Skills training requirements
- Monitors workflow for efficiency and timeliness, sets priorities for projects and activities. Makes adjustments as needed to meet deadlines and commitments. Schedules staff and organizes work in a logical manner to meet work-related deadlines and to ensure efficient operations
- Reviews work for quality, completions, accuracy and adherence to internal operating policies and procedures. Addresses errors and problems and provides feedback. Ensures quality workmanship, cost effectiveness, and timely service delivery
- Provides technical assistance to staff for training purposes and for problem-solving. Provides background and implements, interprets departmental policies, procedures and guidelines
- Determines costs of equipment, materials and supplies and prices accordingly. Orders materials, supplies and equipment. Liaises with vendors on issues related to products, services and delivery
- Contributes to the development of policies, procedures and internal systems which support the work of the unit. Defines needs and coordinates the development of manual and/or automated systems to facilitate workflow
- Ensures records are kept up-to-date and maintained in accordance with applicable regulations
- Plans and administers income and expense budgets. Develops projections. Track actual income and expenses and adjusts operating plans to address variances
- Develops and/or produces various operating reports (e.g., project status, work backlogs, etc.) as required
- Develops and implements security related procedures such as office opening and closing routines, recognition of duress signals and key controls. Coordinates security activities with University Public Safety Department. Promotes and maintains standards for security conscious awareness and behavior. Maintains knowledge of University’s crime prevention and suppression programs and services. Ensures dissemination of security-related information to staff
- In the event of an emergency, the employee holding this position is required to “report to duty” in accordance with the university’s Emergency Operations Plan and/or supervise the employee’s department’s emergency response and/or recovery plans
- Performs other related duties as assigned or requested. The University reserves the right to add or change duties at any time
- Requests and participates in bid walks. Oversees project management of small scale projects
47
Maintenance Supervisor Resume Examples & Samples
- Conduct performance evaluations for all assigned coordinators, technicians, assistants, and custodians
- Bench mark and monitor the maintenance department productivity
- Interpersonal
48
Maintenance Supervisor Resume Examples & Samples
- Coach Safety, Quality and Productivity to ensure objectives are met through following standardized work processes in Chicago Stamping plant
- Should have ability to multi task
- Capable of assigning work to unionized hourly workforce and holding employees accountable for following processes pertaining to daily work assignments in terms safety, quality, and throughput
- 3+ years technical work experience in a Manufacturing environment
- 1+ years of experience with PLC logic and controls
- Bachelor’s Degree in Electrical or Mechanical Engineering
- 3+ years of automotive experience
- 1+ years of prior experience managing a unionized work force
- 1+ years of CNC machining experience and Helium leak stand experience (PTO
49
Stamping Maintenance Supervisor Resume Examples & Samples
- 1+ year manufacturing supervisor experience
- 1+ year experience in Microsoft Office
- Body shop/stamping /subassembly experience preferred
50
Maintenance Supervisor Resume Examples & Samples
- Roads & Grounds Cleaning Program
- Emergency Response Clean Up Program
- Site Contracted Services Management Support Areas of responsibilities may include: Management Responsibilities for the following Support Personnel Jones Lang LaSalle & General Motors
- Weekend Management Coverage Measurable
51
Maintenance Supervisor Resume Examples & Samples
- Maintenance/Housekeeping Budget tracking
- Maintenance/Housekeeping Contract Scope Change Review
- Manage and complete Planned and Reactive Maintenance Program
- Prioritize incoming workload and tasks
- Aid in parts inventory and ordering
- Site Contracted Services Management Support Areas of responsibilities may include
52
Plant Maintenance Supervisor Resume Examples & Samples
- Create and implement regular preventative maintenance, and inspections on machines, equipment, and plant facilities to eliminate down time and ensure production goals
- Develop a competent workforce by utilizing hands-on training methods in the work area focusing on timely repair of all production machinery and equipment in the plant
- Create and implement a spare parts program
- Maintain a CMMS to organize spare parts inventory, work orders, and equipment information
- Lead the maintenance technicians by prioritizing and scheduling work and providing guidance where needed
- Manage projects involving plant related equipment such as new equipment installations and equipment overhauls
- Comply with OSHA safety rules
- Read and interpret equipment manuals, blueprints, and work orders
- Develop a collaborative relationship with all departments
- Be an integral part of the plant management team
- High School Diploma or Equivalent
- Must have 5+ years of experience performing/supervising maintenance activities in a manufacturing environment
- Must be able to work safely around industrial equipment
- Must be able to pass a pre-employment drug screen and background check
- Must possess a superb attitude, be highly motivated, and very detail oriented
- Must have prior maintenance experience
- Must have knowledge of Electrical, Mechanical, Pneumatic, and Hydraulic Systems
- Ability to follow directions and work as a team and individual
- Prefer 10+ years of experience performing/supervising maintenance activities in a manufacturing environment
- Prefer Associate's or Bachelor's degree
- Prefer experience with plastics manufacturing (shredders, conveyors, dryers, extruders, etc.)
53
Maintenance Supervisor Resume Examples & Samples
- Establish systems to ensure that preventative maintenance is 100% on-time and effectively for all manufacturing tools and equipment, including robots and other automated and semi-automated manufacturing systems
- Drive to achieve world class Equipment Availability > 90%, as well as supporting OEE >85%
- Day to day coverage of production line equipments, including rapid response on broken equipments to minimize downtime and maximize productivity
- Establish a positive work environment for non-exempt workers to be productive, and completely engaged with Tesla Mission, Core Values, and Culture
- Investigate and implement countermeasures to prevent repetitive breakdowns
- Assist with electrical and mechanical code compliance, safety, and lean manufacturing initiatives
- Maintain and help develop up-to-date maintenance and calibration procedures and schedules
- Support Lean Manufacturing and 5S initiatives
- Work with Engineering and Manufacturing to ensure maintenance instructions and schedules are always available and current
- Will support both day and swing shift manufacturing schedule (Some weekends and holiday required)
- Manage repairs/troubleshooting exactly to instructed process
- Manage small projects involving multiple departments and/or outside contractors
- Drive to reduce cost of ownership for all Equipment in Powertrain
- Provide clear report for all unscheduled down event on critical equipment
- Provide support to ensure that all equipment installation and modifications are effective
- Manage workload with positive attitude and proactively help co-workers
54
Maintenance Supervisor Resume Examples & Samples
- Maintain the reports and historical data files for TS16949
- Work as part of a team within the Maintenance Dept. To implement & upkeep TS16949 procedures,
- Liase with various departments regarding issues
- Assist with facilities activities including, sub stations, water management, overhead cranes and general plant equipment
- Deputise for the Maintenance Manager when required
- Implementation of Continuous Improvement activities
- Ensure equipment reliability is optimised by daily planning PM, corrective work and continuous improvement tasks. KPI target is 95% uptime and 95% PM completion
- Proiritise safety, breakdown, PM‘s, corrective work and continuous improvement tasks
- Communication of the daily/weekly plans and maintaining completion records. KPI Target is 85% completion to plan
- Manage the worklist of outstanding corrective work
- Maintaining departmental budgets (KPI target)
- Lead mentor and develop the Maintenance team leader group
- Lead the maintenance team through the Team Leaders
- Ensure the adequate manning is maintained (KPI target)
- Ensure a satisfactory level of time keeping and attendance
- Update the Kelio system daily/weekly
- Ensure communication within department is optimised through shift hand over meetings with T/L and techs
- Work with the Maintenance Manager on staff training, and ensure the training matrix is updates
- Understanding of the disciplinary processes and procedures and conduct 1st stage disciplinary investigations
- Ensure all HS&E is adhered to including risk assessments, accident/incident reports completed and escalated to H&S Manager
- Monitor and provide employee feedback regarding absenteeism, job performance and schedule overtime when required
- Prepare detailed reports on Downtime, concerns and R.C.A
- Support the Maintenance Manager with Capital Projects
- Review RAMS and issue Work Permits
- Any other duties deemed appropriate
- Must be able to demonstrate good timekeeping and disciplinary record
- Time served apprentice in related engineering discipline
- Minimum qualification ONC ( B-Tech ) , HNC/ HND preferred
- Good business sense, understanding of department costs
- Good understanding of a working in a Injection Moulding environment
- Knowledge of discipline routes and procedures,
- Managing within a unionised environment
- Good understanding of Health and Safety requirements within a manufacturing environment
- Proven Ability of Leadership skills , motivation and team building ,
- Control of overtime in line with company business plan
- High understanding of QS / TS / and ISO requirements
- Must possess good forms of communication skills both written & oral
- Good I.T skills and P.C literacy
- Must risk assessment skills
- Must have understanding of COSHH
- Awareness of 5s disciplines (preferred)
55
Maintenance Supervisor Resume Examples & Samples
- Planning work priorities, troubleshooting, break-downs for the shift
- Ensuring the direction received from the Maintenance Manager is followed
- Ensuring the availability, capability and development of competent technical and operational manpower
- Understanding and interpreting applicable acts and regulations as it applies to the maintenance and services departments
- Ability to facilitate the development, implementation and continuous improvement of our standard operating procedures by educating, training, monitoring, and proactively coaching the maintenance team
- Identify potential risk for the prevention of accidents, completing safety /housekeeping inspections, and resolving safety issues
- Managing outside trades/contractors performing jobs at MSS on afternoons shifts
- Ensure mutual collaboration with all MSS personnel
- 5 to 8 years experience in a leadership position at maintenance Supervisor level combined with excellent interpersonal, analytical problem solving and team building skills
56
Shaft Maintenance Supervisor Resume Examples & Samples
- 50% Organize, plan, and lead maintenance activities relating to mechanical and shaft maintenance. Manage equipment repair and PM's. Establish priorities, direct field and shop repairs and equipment servicing
- 15% Problem solving, improving work process and operating efficiencies
- 15% Safety implementation of effective safety programs and all EHS and MSHA policy and procedures
- 10% Positive two-way communication, fair and consistent administration of company policy and procedures
- 10% Compliance with all division/facility policies and procedures
- High School equivalency with 3+ years mine experience OR 2 to 4 year college degree with 1+ years mining experience
- 3+ years’ experience with Hoist and Shaft maintenance
- Strong mechanical skills in hydraulics, hoist drive systems and shaft repairs
- Cutting and welding skill knowledge, basic mechanical gearing and rigging
- Basic electrical knowledge
- Solid computer proficiency
- Ability to Weekend Shift majority of time
- Periodically attend training outside the work site
57
Maintenance Supervisor Resume Examples & Samples
- 25% Reliability Excellence Governance (Develop, Align & Implement RE Practices & Programs)
- Responsible for aligning, deploying and executing Business-wide reliability excellence vision, strategy as well as direct program administration for the White Marsh location
- Promotes a culture that builds, operates and maintains plants that are operationally sound, safe and reliable. Implements leading reliability excellence practices and aggressively raises the performance of poor departments by monitoring key performance indicators (i.e. asset health, backlog of ready work, productivity and Overall Equipment Efficiency, etc) for the White Marsh location
- Supports/implements Reliability Excellence processes for the location and ensures the reliability culture is foundational to
- 30% Operational Effectiveness/Continuous Improvement (Prevent, Maintain & Repair)
- Using established guidelines and protocols, supervises preventative maintenance and reliability activities for the White Marsh location. Interfaces and coordinates with other department personnel, facility management, contractors, community and local regulators to ensure asset health and availability
- In accordance with business/plant maintenance and reliability strategies, standards and practices provides clear instruction and direction and participates in routine ongoing maintenance activities and recordkeeping to ensure asset health and adherence to guidelines, codes, regulations, requirements and overall production quality
- Provides clear instruction and direction and participates in the execution of routine repair procedures and tasks to ensure compliance with the fundamental plant reliability strategies, standards and practices
- Monitors repairs through the SAP PPM computerized maintenance mananagement system (CMMS) to ensure work orders and requests are executed in accordance with established work flow
- Reviews and assists in analyzing maintenance/reliability maintenance metrics and performance utilizing the CMMS. Supports audit compliances, root cause analysis processes within the maintenance team, which includes tracking and reporting on established metrics for (i.e. Asset Health index; Total Maintenance Cost/RAV; Overall Equipment Effectiveness (OEE); and audits compliance)
- Partners with Business/Reliability Engineering department and more senior team members to recommend ideas and provide input for strategies on operations of assigned areas (i.e. electrical, mechanical, systems, operations, etc)
- 15% Project Planning, Contract/Vendor Management
- Manages ongoing maintenance/ reliability related projects (i.e. asset reliability/defect elimination) utilizing a general knowledge of maintenance and reliability practices and procedures
- Participates in basic project planning, cost estimation and tracking & payback justification
- Assists and provides recommendations on selection of contractors/vendors. Supports maintenance vendor issues and contract
- Maintains and applies consistent maintenance and reliability best practices (i.e. safety programs, routine safety audits, RCM
- Identifies training opportunities/needs and facilitates training sessions for maintenance personnel, focusing on skills training and development, safety practices and work standards. May provide ad-hoc technical support as needed. Serves as a source of maintenance/reliability information across departments and training others on CMMS processes and workflow
- Supports operations by identifying and reviewing failures, downtime and lost production and partners with more senior team
- 15% People/Budget Management
- Responsible for the people management in area of responsibility including recruiting, retention, development and engagement of team
- Responsible for the appropriate scheduling and delegation of activities for a team of maintenance/reliability employees and 3rd party contractors
- Establishes and manages department/area maintenance budgets. Has responsibility for a subset of cost control of repairs and maintenance and also maintenance labor and parts
- Associate Degree/Certificate
- 2+ years maintenance experience in a manufacturing or food processing environment
- 2+ years in a supervisory role
- 4 year degree or equivalent maintenance or industrial work experiance
- 6+ years maintenance experience in a manufacturing or food processing environment
58
Maintenance Supervisor Resume Examples & Samples
- 65% Supervise Maintenance Dept. employees to ensure safe, effective & efficient maintenance of equipment
- 10% Capital projects management and contractors
- 10% General purchasing of all maintenance related items
- 5% Program management
- 5% Hire, train, develop employees including reviews, tech training, EHS and PMP
- 5% Perform misc. job related duties as assigned
- 2+ years’ experience in supervising an industrial crew
59
Maintenance Supervisor Resume Examples & Samples
- 65% Supervise mechanical hourly employees to ensure effective and efficient maintenance of the equipment
- 10% Capital project management and contractors
- 5% Hire, train, and develop employees including reviews, technical training, EHS training and PMP process
- 5% Perform miscellaneous job-related duties as assigned
- 2 years experience in supervising an industrial maintenance crew
- 5 years experience working in industrial maintenance
- Flexible hours with ability to work weekends
- Highly skilled in 480 voltage and control power, PLC’s, mechanical, hydraulic and pneumatic, trouble shooting
- Computer skills in Word, Excel, Outlook and a basic understanding of spreadsheets
- Experience in building a culture of teamwork, collaboration, accountability and empowerment of employees
60
Maintenance Supervisor Resume Examples & Samples
- 30% Maintain plant equipment for high reliability and maximum productivity. Keep online maintenance records that detail all maintenance and repair of plant equipment. Plan and implement major maintenance projects as directed by the plant manager
- 25% Assist in day to day activities such as record keeping, scheduling of maintenance working hours, support of the ISO quality and environmental programs and enforcement of location, business unit and corporate policies
- 20% Fully support and assist in the maintenance of our safety program. Be familiar and assist the plant in compliance of all OSHA, Cargill EHS and location safety regulations and rules
- 15% Maintain a spare parts inventory to minimize cost and down time. Maintain a positive business relationship with suppliers of equipment, parts and service
- 5% Be a proficient operator of all plant equipment. Train operators and new employees in the operation and maintenance of equipment for best productivity and continuous improvement
- 5% Miscellaneous BU projects in a team setting
- Experience/ technical skills. Minimum of 3 years experience in one or more of the following: Mechanical, electrical, hydraulic or pneumatic equipment troubleshooting, repair and maintenance
- Experience with the operation of welding and cutting equipment
- Experience with computers, including familiarity with MS Outlook, MS Word, MS Excel, MS PowerPoint or equivalent
- Effective interpersonal communication skills, both verbal and written
- The ability to work in challenging environments such as: high noise areas, dusty, greasy, oily, hot or cold and heights up to 45 feet
- This is a full time permanent position. High impact on location for productivity, reliability, customer solutions and financial results
- Deployment of safety and environmental programs. Ensure plant equipment is maintained properly and be proficient in the operation of such equipment. Ability to train plant employees in functions of the process
- A small percentage of travel may be required
- Technical school or Bachelors degree in mechanical or electrical engineering or the equivalent
- Degree in facility operations or management
61
Maintenance Supervisor Resume Examples & Samples
- Minimum of 5+ years’ experience in working in Industrial Maintenance in Manufacturing
- Computer skills including Microsoft Office, spreadsheets and use of databases
- Good communication and problem solving skills
- Experience in building a culture of teamwork, collaboration and accountability
- Must be able to work flexible hours, multiple shifts, nights and weekends
62
Maintenance Supervisor Resume Examples & Samples
- Lead a team of Mechanics, and Electro-Mechanical Technicians to maximize productivity
- Train and coach maintenance personnel to develop skill set
- Analyze Preventative Maintenance data and modify program based on data
- Prioritize work requests based on preventive maintenance and downtime data
- Drive root cause analysis to maximize equipment availability. (though this is somewhat covered by #4)
- Drive and adhere to 5S guidelines within all maintenance areas
- Utilize SAP, EAM preventive maintenance program to maintain equipment histories, repair records, frequency needs and resource library
- Total Productive Maintenance responsibilities will include the creation of Centerline Sheets, team driven machine improvement activities, development of Clean, Inspect, Lubricate, procedures, etc
- Lead and/or support Capital Project Improvement initiatives
- Experience with Ammonia Systems
- Project Management Experience
- Background in Engineering
- Experience in the Food, Beverage, Pharmaceutical, Chemical, or Petroleum industry
- Bachelors’ degree from an accredited university, or a high school diploma and 5 years of experience in a manufacturing environment as a maintenance lead or supervisor
- 3 years of experience in a manufacturing environment as a maintenance lead or supervisor
63
Maintenance Supervisor Resume Examples & Samples
- Implement the activities of the maintenance organization in the relevant field (electronic, mechanical, etc.) including assisting with procurement of parts, equipment and tools
- Ensure immediate maintenance intervention to solve any maintenance issues in the relevant field and follow up actions necessary
- Ensure daily preventive maintenance activities are performed
- Support all lean (EMS/EPS) plan and activities affecting the relevant maintenance area
- Support the facility management for the relevant area
- Provide daily shift activities, issues and resolution, emerging issues and concerns reporting
- Communicate, coordinate and cooperate with operations, planners and engineering to maximize efficient productivity
- Maintain effective employee relations including coaching, motivation and corrective actions; ensure compliance with company policies/procedures and legal guidelines; foster a positive workplace environment
- Focus on technical development of the maintenance team to include skills, communication, and teamwork
- Ensure adherence to safety rules and standards and maintain good housekeeping
- Be available prior and after shift to ensure a timely shift transition
- Maintain continual efforts consistent with minimizing scrap, rework, and controlling costs of expendables and product
- Must have effective verbal and written communication and interpersonal skills
- Willingness to work all shifts and extended hours as required
64
Operations & Maintenance Supervisor Resume Examples & Samples
- (30%) Direct and develops associates in the daily production of finished flavors and mint oil distillation required for shipments to Wrigley factories around the world. Ensure production department KPI's for quality, safety, productivity, costs and people are achieved each period. Ensure NFI is in full compliance with all federal, state and local regulations for handling, processing and shipping food grade flavors. This role is also accountable for ensuring all NFI Quality and Food Safety standards are met, documentation and procedures are developed, maintained and performed for the activities in these departments
- (30%) Direct the on-going maintenance activities of all production equipment, auxiliary equipment and building systems to support NFI manufacturing operations while ensuring NFI is in full compliance with all federal, state and local regulatory requirements. Ensure maintenance department KPI's for quality, safety and costs are achieved each Period. This role is also accountable for ensuring all NFI Quality and Food Safety standards are met, documentation and procedures are developed, maintained and performed for maintenance activities within the factory
- (25%) Drive on going continuous improvement projects to improve efficiencies, reduce costs and reduce material waste. This includes being pillar leader and/ or coach of the Autonomous and Planned Maintenance Pillars, training direct reports on the Continuous Improvement Methodology and leading CI Teams to achieve improvements in the operation
- (15%) Perform the daily engagement, documentation and recordkeeping activities associated with this role; HACCP verification, GMP compliance documents, purchase order approvals, associate goal reviews, engagement actions, associate development and reviews
- 5 years of maintenance / engineering and CI / TPM / Lean experience in CPG manufacturing
- 7 years of maintenance / engineering and CI / TPM / Lean experience in CPG manufacturing
65
Maintenance Supervisor Resume Examples & Samples
- Provides leadership to create an environment which will maximize individual performance, productivity and self-development
- Promotes a spirit of cooperation and dedication to superior quality workmanship among all employees
- Actively pursues proper resolution of all employee concerns or complaints to create and maintain a work environment that expresses care, concern, and an atmosphere of fairness toward all employees by the company
- Looks for and acknowledges consistently superior performance by employees
- Works closely with Human Resources Department on all matters related to employee staffing, care, benefits, pay, discipline, grievances, etc
- Informs and enforces hourly employee’s knowledge and adherence to company policies concerning their employment responsibilities such as absence, tardiness, leaves and disciplinary warning procedures
- Department’s work hours, including lunch periods and breaks
- Required clothing, equipment and personal hygiene standards
- Understanding of lines of authority, proper channels of communication and procedures for expressing concerns
- The nature of work, instruction & training on the proper use of equipment on the job
- Safety and accident prevention measures in accordance with performing specific jobs
- Company quality and regulatory standards, including GMPs
- Ensures that performance of all in-operation sanitation, general housekeeping, equipment operation, cleanliness and storage procedures meet with Kraft quality specifications and FDA regulations
- Visually inspects and approves quality and quantity of workmanship in accordance with established standards, including attending daily POG review. Takes corrective action where necessary
- Complete 100% Safety Training for self and with hourly employees on a monthly basis
- Complete 100% compliance documentation with Safety Department Checklists, Monthly Department Inspections and Equipment Pre-Use Inspections
- Lead and/or participate on one KSRMP Element team
- Complete 100% of required Accident / Incident Investigations within eight (8) hours of the incident
- Ensures that Personal Protective Equipment (PPE) and GMPs are adhered to at all times
- Ensures 100% Compliance with all local, state and federal regulations (Wastewater ph, air permits requirements, storm water permit requirements, dust regulations, lockout, confined space, PPE, etc…)
- Responsible for understanding and delivering on all key Safety Deliverables including, but not limited to: Kraft Safety Events (TIR), Near Miss Reporting and follow ups, Worker’s Compensation costs, Safety Work Orders Completed, Compliance Training and Hearing Test Compliance
- Responsible for understanding and delivering on all key Quality Deliverables including, but not limited to: Consumer Complaints, Quality Manufacturing Excellence (QME) and Faulty / Right the First Time (RTFT)
- Ensures that quality is placed above production targets – action is taken immediately by the team to correct and prevent quality problems
- Arranges for sufficient working materials and supplies for daily maintenance needs. Follows up with any parts needed for job completions
- Provides department employees with information about company activities, changes, and other significant events
- Takes all appropriate actions to assure the next shift will be able to start and operate as smoothly as possible
- Leads and participates in Green Rooms while addressing the overall business key process indicators (KPIs) involving: Quality, Cost, Delivery, Safety and Moral (QCDSM)
- Checks and verifies that team members are closing out work orders when needed, and putting their time to the work orders
- Reviews and sign-off of shift performance (QCDSM) and ensures that all required administration tasks in support of the production team are carried out. Performs walkabouts to ensure safety and housekeeping standards are maintained
- Where production problems have been escalated to the team leader, decides on a course of action to resolve the problem. This may involve calling in specialist resources
- Checks that hand over procedures are followed (e.g. housekeeping, change parts etc.) and that team members are conducting a hand over to incoming team members
- Reviews quality trends to identify problems and opportunities expeditiously, and where quality problems have escalated to the team leader, decides on an appropriate course of action to resolve
- Understands and utilize POG reviews to drive product consistency
- Deliver Business Unit (shift) Productivity Target through
- B&R is below Budget expectations
- Maximizing Rework usage
- Maintenance KPI’S
- Lead at least one Improvement Project equal to or greater than $100,000
- Verifies, where problems have been addressed, that the problem has been eliminated and ensure that, where necessary, work instructions, job aids and procedures have been updated
- Leads, coaches, mentors and supports team members in using the correct problem solving techniques (5 why, quick fix, etc.) to solve situational problems
- Works with and support all manufacturing and plant supervisors, staff, business unit managers, co-leaders, and associates
- Works with support groups, such as Engineering, Quality, Maintenance, R&S/Logistics, Finance, Human Resources, R&D, Marketing and other facilities
- Works with and leads Project Teams as assigned by Managers
- Bachelor’s degree in Management, Engineering or related fields is required
- Must have a sufficiently broad background including but not limited to promoting employee and self-development, packaging maintenance and processing equipment, and manufacturing systems that are focused in the individual’s area of responsibility
- Individual must also be able to learn the company policies and procedures
- Individual must have interpersonal and team skills to function as team member and leader
66
Maintenance Supervisor Resume Examples & Samples
- Responsible for sustaining a preventative maintenance program and continuing to drive towards reliability excellence
- Identify and utilize quality contractors
- Support the installation of new equipment and provide direct support trouble shooting and repairing plant equipment and infrastructure and assure of safety compliance and training
- At least 5 years of direct maintenance experience in a chemical, coatings, paint or process manufacturing industrial environment
- Experience with lean principles
- Proven ability to solve problems to the root cause and provide necessary corrective action with associates in reaching consensus problem resolution
- Excellent oral and written communication skills with the ability to work well and collaborate with cross-functional teams
67
Maintenance Supervisor Resume Examples & Samples
- Directs maintenance personnel to ensure that all systems operate at their highest capability to meet required production schedules, quality, costs and schedule priorities
- Develops preventative maintenance procedures that are cost effective and increase the operational life of the equipment
- Assist in the development of the system and operational standards and corrective actions
- Develops, implements and reviews regularly, site-specific maintenance logs for department
- Coordinates, arranges, and supervises, or provides for the completion of corrective and preventive maintenance in accordance with company operating procedures, practices and financial considerations
- Assists workers in diagnosing malfunctions in machinery and equipment
- Assist with preparing requisitions to determine the number of spare parts to be kept in inventory
- Assist with safety training, monthly safety meetings, member of safety committee, and provides technical support for all safety projects, and supports implementation of the 9-key element process
- Evaluates long-term needs in relation to major projects and factory improvements
- Ensures that equipment and facility are maintained in a safe, operable condition and/or arrange for replacement/upgrades
- Oversee and lead the implementation of the QRMP (Quality Risk Management Process) system and operational standards as outlined in the plant accountability list in order to achieve targeted RCR
- Assist and partner with business leaders on implementation of process improvement (Six Sigma / Lean/Kraft Heinz Global Production System (KHGPS)), including leading change initiatives, planning, and facilitation
- Continuous and close coordination with the Maintenance Manager, other Maintenance Supervisor(s), other Team Members, and Human Resource
68
Maintenance Supervisor Resume Examples & Samples
- Manages employees in order to achieve or exceed the Maintenance performance indicators
- Ensures the overall management activities with the employees in his Department
- Ensures continuous communication between other members of the management team in order to perform the necessary actions or implement improvements to operation efficiency
- Leads and/or actively participates to many multidisciplinary teams: equipment efficiency, continuous improvement, equipment installation, training or others
- Keeps a close eye on maintenance spending in his area of responsibility and continuously searches for new and innovative ways to reduce costs
- University Degree in Mechanical Engineering or related field
- 2 years of management experience in a manufacturing environment
- Experienced with Continuous Improvement tools and processes (Lean manufacturing and Six Sigma)
- Strong communication skills with the ability to influence others
- Drive for results
69
Maintenance Supervisor Resume Examples & Samples
- This position required being available for consultation during all hours of Factory operation, administrative and supervisory skills and abilities, expertise in Engineering of Electrical, Electronics, Mechanical, Hydraulics, Boiler Systems, Refrigeration Systems, Waste Treatment Systems, and Building Construction
- Provide leadership for maintaining and operating all equipment related to the operation of the physical factory. Direct maintenance personnel to ensure that all systems operate at their highest capability to meet required production schedules, quality, costs and schedule priorities
- This position is responsible for overseeing and coordinating the maintenance operations on three shifts
- Must be able to interact/communicate/cooperate with all levels of employees in all functional areas of the factory as well as with suppliers and outside agencies
- Determines equipment capabilities in coordination with Company Engineering Staff for new or revised factory layouts. Improves processing methods to reduce cost and avoid loss of production as a result of equipment malfunction or failure
- Search ways to improve the operation of the factory, finding ways to reduce operating costs related to all cost centers
- Direct factory preventative maintenance program to ensure all equipment is systematically serviced. Work in cooperation with USDA inspector and all USDA guidelines. Direct maintenance organization to foresee potential problems when conducting routine maintenance
- Costs and Capital – Prepare and follow an annual overhead budget
- Strive for continual improvement to reduce costs
- Ensure all Capital Budgets stay within the confines of intended spending
- Organizational Development – Develop a long-range strategic plan to prepare the Maintenance Department personnel for change in its internal/external business environments
- Improve the department’s problem solving capabilities at all levels of the organization. Efforts will address both process and goals (achieving improvements in communication, interaction and decision making) and outcome goals (achieving improvements in performance)
- Human resource responsibilities will include departmental interviewing/evaluating/hiring prospective employees, goal setting, performance evaluation, employee relations, consistent administration of policies and procedures, training, recognition, EEO/AAP, commitment/opportunities and compliance with internal and external requirements
- Supervise a training program to train employees to technical issues and operation of all factory equipment or maintenance related areas
- Insure that effective fire protection and HAZMAT programs are established and maintained
- Reviews project instructions and blueprints to ascertain test specifications, procedures, and objectives, test equipment, nature of technical problem and possible solutions such s part redesign, substitution of material or parts, or rearrangement of parts or subassemblies
- Devises, fabricates, and assembles new or modified mechanical components or assemblies for products such as industrial equipment and machinery, power equipment, machine tools, and measuring instruments
- Sets up and conducts tests of complete units and components under operational conditions to investigate design proposals for improving equipment performance or other factories, or to obtain data for redevelopment, standardization and quality control
- Training and Safety – Provide a safe and healthful work environment for all personnel through consistent support of the company’s Heinz Safety Process. Oversee safety processes
70
Grounds & Maintenance Supervisor Resume Examples & Samples
- Clearly document job duties performed that relate to minimum qualifications, preferred qualifications, and essential job duties in the “Work Experience” section on the application. We must be able to evaluate your experience based on this information
- Clearly outline dates of employment and hours worked per week for each employment experience listed in the Work Experience section of the Application so that we can calculate full-time experience
- If an Application is considered “Incomplete”, the application will be removed from consideration for the position
71
Maintenance Supervisor Resume Examples & Samples
- 10+ year's offshore facility production and maintenance experience
- Experience with operating and maintenance of rotating equipment, including turbines, generators, and centrifugal pumps
- 5 + years in a supervisory position desirable
- Experience working on floating facility desirable
- Advanced knowledge of SAP or other computerized maintenance management systems
72
Maintenance Supervisor Mechani Resume Examples & Samples
- Provide technical expertise and leadership to the mechanical maintenance group
- Develop and support the O & M and Capital budget for mechanical maintenance
- Develop predictive/preventive maintenance as well as maintain the corrective maintenance backlog log using SAP and other software as appropriate
- Support the operations group to enhance availability, reliability, and heat rate
- Review, monitor, evaluate and recommend appropriate improvements on equipment, techniques and procedures
- Promotes and enforces safety policies and procedures
- Assist in the development of training programs for maintenance technicians
- Provides technical input for major maintenance projects and reviews new construction proposals to ensure ease of maintenance
- Develops scope, schedule and cost estimates for planned outages
- Interprets project management software
- Coordinates and supervises contract labor
- Responsible for bid specifications and evaluations of goods and services
- High School Diploma or GED Equivalent
- Minimum of seven (7) years experience in power plant maintenance/operations or a related field
- Must have experience reading and interpreting blueprints, P&ID's, schematics and system diagrams
- Must have the ability to build strong relationships, to evaluate and diagnose situations accurately, exercise good judgment, remain flexible, communicate effectively, achieve goals that promote The plant’s best interest, work effectively as a team member, and accept challenges readily in a fast paced environment
- Must have demonstrated experience to lead by example, participate in team building, and demonstrate the plant’s core values
- Must have the ability to keep abreast of technical changes and the ability to learn new disciplines
- Must be familiar with codes and regulations governing maintenance
- Must be able to troubleshoot problems and enhance the skills of his group
- Must have excellent oral and written communication skills and the ability to effectively interact with various levels within the organization, customers, and outside vendors
- Associates Degree in a related field
- Ability to work rotating shiftwork, holidays, weekends and overtime
- Possess a valid jurisdictional driver’s license
- Excellent communication skills (verbal and written) and time management skills
- Ability to read, write and speak the English language
- Ability to perform work both indoors and outdoors
- Ability to work on or around energized electrical equipment
- Ability to work in extreme temperatures ranging from very cold to very hot
- Possess good hearing and vision
- Ability to work in areas that may be noisy and dirty
- Ability to wear a respirator and other job related personal protective equipment (PPE)
- Ability to meet (on an annual basis) appropriate physical evaluations identified by NRG as prerequisites to performing certain task and training activities
- Ability to analyze and interpret data to make sound recommendations to the Senior Management
- Demonstrated decision making and leadership skills
- Effective time and resource management skills - planning, administrative and organizational skills
- Ability to handle multiple tasks and work under pressure
73
Maintenance Supervisor, Shovels Resume Examples & Samples
- Ensure that a disciplined approach to safety is present in the shift maintenance group
- Ensure the administration of the collective agreement and personnel policies occurs in a fair and consistent manner
- Hold monthly shift safety meetings with applicable employees as per procedure/agenda with review and follow up on items raised to ensure remedial action is taken
- Adhere to all permit and lockout procedures
- Investigate all incidents, follow up to prevent re-occurrence and create incident reports
- Identify and report current and potential hazards and review the same with shift members
- Set work expectations and performance levels with employees with timely and meaningful feedback
- Perform the functions within the SAP computerized maintenance system to correctly document, approve, and assign the work that is performed on shift
- Perform program maintenance work that is assigned by planning and scheduling to be performed on shift
- Five years of leadership experience in a mine maintenance environment
- Journeyman certification required (heavy equipment technician is preferred but will consider Journeyman welders and millwrights); attach your Journeyman / Red Seal ticket with your application in order to be considered
- Knowledge of the mining industry and technology with hydraulic and electric shovels, specifically CAT, Komatsu and Hitachi
- Working knowledge of computers and computerized maintenance management systems
74
Maintenance Supervisor Resume Examples & Samples
- 1) Ensures all quality standards and metrics are met, work is properly completed, and environmental standards are upheld in coordination with ESH plan
- 2) Manages assigned resources necessary to accomplish the mission
- 3) Enforces strict adherence to technical data and management procedures
- 4) Adjusts resources to meet production requirements
- 5) Manages the special certification roster
- 5) Ensures accurate daily documentation of maintenance actions
- 6) Reviews and evaluates management and production effectiveness
- 7) Initiates management actions to meet new workloads or correct reported/perceived deficiencies
- 7) Participates in the maintenance planning cycle
- 8) Ensures only qualified personnel accomplish maintenance with the appropriate equipment and tools
- 9) Ensures compliance with safety directives, appropriate occupational safety and health standards, and applicable industrial safety publications. Those occupational training requirements that require documentation will be annotated on the appropriate records
- 10) Ensures scheduled and unscheduled maintenance actions are entered and completed in the MIS
- 11) Advises the production supervision of conditions that may disrupt the orderly and controlled execution of the maintenance plan
75
Harvest Maintenance Supervisor Resume Examples & Samples
- Plan, supervise, coordinate, schedule, and assign all work requirements associated with preventative maintenance, projects, and day-to-day work orders
- Continue development and enhancement of a measurable Preventative Maintenance program
- Supervise the work of mechanics and electricians to ensure good working order of production/warehouse equipment
- Perform periodic inspections of equipment and systems to observe operating condition and need for repair or adjustment
- Supervise repairs/projects carried out by sub-contractors and ensure quality of work and adherence to deadlines through rigorous follow-ups
- Maintain HACCP program compliance and documentation, and document and maintain Standard Operating Procedures
- Minimum 3 years’ experience in leading Maintenance & Reliability OR an equivalent combination of education and experience in mechanical/electrical/refrigeration
- Available to work shift work including weekends
- Ability to work in cold environments
76
Maintenance Supervisor Resume Examples & Samples
- High school education
- Minimum 5 years of maintenance experience in an industrial environment
- Strong mechanical skills. A working knowledge of electrical equipment and systems
- Excellent written and verbal communication skills, highly motivated, goal oriented strong team player
- Physical requirements include, but are not limited to wearing respiratory equipment in accordance with the Ashland Respiratory Protection Plan
- Experience directly supervising maintenance mechanics and managing contractors
- Vocation training
- Steam Engineer Certification
- Knowledge of instrumentation and Distributed Control Systems (Delta V)
- Knowledge of a CMMS (Computerized Maintenance Management System) and/or SAP
- Greater than 10 years of industrial maintenance experience
- Experience as an instructor for employee training
77
Maintenance Supervisor Resume Examples & Samples
- Electronic, Automation, Electrical/Mechanical Engineering or similar Bachelor’s Degree
- TPM and manage maintenance indicators (MTTR, MTBF AND UPTIME)
- 3 to 5 years’ experience in a supervision position
- Strong Process oriented
- Project Management & Presentation Skills
- Problem Solving Methodologies and Statistical tools including: SPC, 8-D, A3
- Ability to direct and lead cross-functional process improvement teams
- English Language preferred
- Zero Incidents culture
- EBS Tools Integration
- Business Practices and Systems
- Program management
- Manufacturing value stream success factors and continuous improvement
78
Weekend Maintenance Supervisor Resume Examples & Samples
- Proactively implements, promotes and maintains a Zero Incident Safety Culture, through diligence in accident prevention, investigation, equipment maintenance and rule enforcement
- Promotes safe work environment and workspace organization through 5S principles
- Acts as a business partner by planning, initiating, leading, measuring and assessing continuous improvement and maintenance process improvements by applying appropriate Eaton Business System (EBS) processes, Continuous Improvement Framework (CIF) and problem solving tools such as ELS (Eaton Lean System)
- Actively participates in setting, communicating and achieving department goals and objectives and develops and maintains performance metrics as required to monitor results and uses those results as a tool to identify and initiate process improvements within own work area. Coordinates and/or participates in continuous improvement teams in own or other areas to enhance plant results
- Fully engages workforce and promotes personal accountability by identifying goals, empowering employees to drive decision making, foster innovation and continuously learn and by providing ongoing feedback on employee performance with formal evaluation provided at least annually
- Manages budget and works with Facility Maintenance Manager to prioritize resources and coordinate maintenance projects. This includes scheduling vacations, training, overtime and shutdown activities
- Partners with Production Managers to integrate maintenance planning and resources to support Flow Line Team cost savings projects and other continuous improvement activities
- Assigns design projects and tasks to appropriate personnel to support continuous improvement
- Manages capital projects for new/rebuilt production equipment to support improvement in reactive maintenance and machine capability. Evaluate new technologies for application in future equipment design
- Supports stock room system with component repairs and additions to cover new projects. Orders and maintains supplies and materials to sustain both the department and manufacturing maintenance requirements
- Minimum 3 year(s) supervisor experience in a manufacturing or operations environment
- Knowledge of Six Sigma and other problem solving tools, read/draw blueprints using AutoCAD, and computer experience in Microsoft Excel, PowerPoint, Word, Oracle and Maximo
- Previous experience as a maintenance supervisor
- Experience organizing and forming teams
- Lean/Six Sigma knowledge and experience
79
Maintenance Supervisor Resume Examples & Samples
- Implements and supports EHS (Environment, Health and Safety) policies, codes or standards and performs inspections with Corporate, contract, and regulatory officials and is committed to Eaton’s “Zero Incident Safety Culture” and “Life Saving Rules”
- Maintains the facilities, utilities, equipment and grounds to meet safety, regulatory, quality, and delivery requirements
- Develops specifications for competitive bidding, participates in the contractor selection process utilizing appropriate personnel and policies, to purchase and manage services for facilities, utilities, grounds and equipment maintenance
- Attracts, retains, motivates, and develops maintenance teammates skilled in mechanical, electrical, and electronics fields and leads the maintenance teammates as required
- Maintains facilities in emergency situations in absence of coaches or other management personnel
- Participates in the planning and implementation phase of the capital expenditure process with emphasis on safety, environmental and operational focus
- Implements and improves preventive and predictive maintenance program for the facilities, utilities, machinery and equipment
- Develops and executes spare parts strategy for machinery and facilities, purchases parts for stocking, and repair of machinery
- Maintains records of capital assets and assists with disposal and acquisition of equipment
- Engineering/Bachelor graduate
- Minimum of 3 year of supervisory experience in a manufacturing or operations environment
- Comprehensive understanding in electronics, electrical and mechanical procedures through formal study and practical experience
- Ability to guide maintenance teammates for expeditious troubleshooting and problem solving
- Comprehensive knowledge of environmental, health and safety aspects in manufacturing environment
- General knowledge and understanding of Lean Manufacturing
- Comprehensive understanding of TPM
- The ability to work as a facilitator for a team and as a member of a team
- Maintain the basic staff and the continuous upgrading of the qualifications of personnel
- Responsible for preventive and predictive maintenance of the facilities, utilities, and equipment
- Maintaining the required resources to meet customer requirements through scheduled and unscheduled maintenance University diploma in an engineering subject
80
Maintenance Supervisor Resume Examples & Samples
- Ensure the safety of all employees on the shift
- Maintain a clean and safe work environment by utilizing Lean principles
- Coordinate with Production on all scheduling of machine outages
- Enter daily work requests into eMaintenance. Prioritize, assign and track daily work orders
- Research, write and modify preventive maintenance procedures, schedules and tasks required for all plant equipment
- Follow up on and review all daily work progress
- Develop job kits for scheduled work as needed
- Create purchase requisitions; order parts or supplies when needed
- Assist with labeling, stocking and issuing parts or supplies as needed
- Coordinate any maintenance department training
- Provide input to the Plant Manager regarding the performance reviews for all Maintenance department associates
- Requires the application of average math (addition, subtraction, multiplication, and division) and reading skills
- Average computer skills. Ability to use Microsoft Office Word and Outlook
- Advanced formal education in an electrical trade, mechanical trade or other formal education as it relates to the maintenance field
- Ability to make decisions and act upon those decisions
- Requires the ability to complete paperwork accurately and timely
- Requires good hand/eye coordination and good vision
- Must be a self-starter and team oriented
- Must be conscious of all safety aspects affecting the manufacturing operations
- Demonstrated ability to lead
- Previous machine operation experience
- Previous experience driving Preventative/Predictive Maintenance programs
- 10+ years of experience maintaining equipment in a fast paced industrial setting
- 3+ years of experience leading a maintenance team
- LI-PC1
81
Maintenance Supervisor Resume Examples & Samples
- Determine and assign craftsmen for specific jobs
- Monitors productivity and progress of specific jobs
- Verify parts availability and order necessary parts for the daily maintenance schedule
- Complete key metrics to drive business initiatives in the maintenance organization
- Knowledge of Microsoft office applications
- Maintenance experience in chemical manufacturing environment
- Previous experience supervising unionized workforce
- Process knowledge of special chemical operations
- Supervision of craftspeople including administration of Code of Conduct and CBA
- Prioritize job assignments, drive continuous improvements and safety related activities
- Position to work Monday through Friday
82
Central Maintenance Supervisor Resume Examples & Samples
- Area of responsibility include the following functions
- Very good people skills
- High level of communication skills across different functional groups
- Broad chemical plant and maintenance knowledge and experience
- High school degree or GED
- 7+ years of maintenance/construction experience in chemical manufacturing environment
- Previous supervisory experience in facility and or maintenance is strongly preferred
- Welding inspection experience preferred
83
Maintenance Supervisor Resume Examples & Samples
- Associates degree or four year technical certificate in mechanical/rotating equipment repair and maintenance and five experience in chemical plant related maintenance and leadership for a crew of 15-20 fixed personnel and oversight experience for contract maintenance personnel
- MS Excel, Word, SAP, MAXIMO or related maintenance software program
- Demonstrated resiliency in completing an assignment with significant time and resource constraints
- Exercised tact and resolve in dealing with conflict, change, or emotionally tense situations
- Identified performance issues, provide constructive developmental feedback, and assist in development planning to effectively manage the growth of direct reports
- Achieved success as a leader in a union environment
- Significantly improved performance and achieve results in a manufacturing environment
- Managed in a fast-paced and high stress business environment
- Controlled costs against a fixed budget
- Direct supervision and development of hourly staff
84
Maintenance Supervisor Resume Examples & Samples
- Gemotiveerd persoon met een industrieel ingenieur of bachelor diploma (mechanica of elektromechanica) of gelijkwaardig door ervaring
- People manager met een “zero incident” ingesteldheid
- Talenkennis: Nederlands. Engels en Frans is een plus
- Software: ERP (SAP), MS Office
85
Maintenance Supervisor Resume Examples & Samples
- Everyday coaching to engage team and develop ownership for sustainable targets and achievements
- Initiate process improvements by leading the plant maintenance group to identify potential savings and assist with their implementation
- Actively participate in the development and execution of initiatives towards achieving the factory’s operating plan and objectives
- Promote, enhance, and sustain a positive labour management and relationship, including efforts to continuously improve teamwork geared towards establishing high levels of employee involvement
- Deliver effective training and performance management to the Maintenance workforce
- Coordinate with all Departments to maximize overall effectiveness and efficiency of the Maintenance operation
- Direct activities of the skilled trades’ (Millwrights and Electronic Technicians) in support of production priorities
- Recommend training and skills upgrading priorities for the skilled trades people on the shift
- Administer, coordinate and manage attendance, time, manpower schedule, vacation and overtime of direct reports on the shift
- Provide technical support to the skilled trades as necessary, and when required seek and obtain additional support from other groups within the factory (i.e. Engineering, Technical Stores, Technical Services, etc.) or outside resources
- In collaboration with the maintenance planners, manage labour scheduling of the skilled trades, prepare weekday coverage plans and communicate maintenance labour plans to people in the factory to ensure alignment with Production needs
- Work with the maintenance planner to ensure all Skilled Trades’ overtime is managed according to the skilled trade overtime equalization policy as detailed in the collective agreement
- Work with Production Team Leaders to ensure equipment downtime is coded properly on SAM, and review SAM regularly for reporting accuracy
- Must be available to work weekends on a rotating basis
- Engineering degree or Diploma in a related discipline (e.g. Mechanical or Electrical) preferred, or trade school diploma in a related area
- A minimum of 4 to 6 years relevant experience in processing/packaging operations required
- Knowledge of manufacturing principles and experience in analysis and development of methods, standards, systems, procedures, plant layout and cost control in a high speed, automated production environment
- Demonstrated problem-solving and leadership skills as well as strong interpersonal and communication skills are required
- Ability to lead and participate in a multi-functional, team-based unionized environment
- Demonstrated analytical and planning skills
- Must be able to work independently and cope with conflicting demands in short time periods
- Experience in a food processing operation preferred
86
Maintenance Supervisor Resume Examples & Samples
- Technical degree preferred and at least 5 years of maintenance supervisor experience in a manufacturing environment
- The ability to interface with maintenance employees, operation, production operators, plant engineers, production manager, senior staff
- Be well versed in plant processes, trouble-shooting and problem solving techniques, engineering standards, Process Safety Management (PSM), Management of Change and preventative maintenance programs
- Experience in maintaining budgets, CMMS systems, SAP, Microsoft office
- Experience working in a union facility
87
Maintenance Supervisor Resume Examples & Samples
- Boost team work
- Manage the activities related to the Occupational Health
- Manage a 20-25 people team
- Make the necessary changes to improve maintenance plans regarding machine performances and test analysis
- Make sure that the work plans, the specifications, the work force and the materials are recorded in the work plans and in SAP
- Support the development and the implementation of the processes and the continuous improvement of the maintenance management to enhance the reliability of the equipment
- Actively supervise the performance and the status of the equipment
- Verify if the tests are reliable
- Prepare, create, support and be in charge of the engagement of the plant’s team
- Direct the analysis process when a failure is discovered to eliminate or reduce the failures
- Encourage the communication between departments and organizations
- Participate in the different improvement processes
- Develop follow-up methods of work orders (Prevention and Correction) to meet the weekly maintenance schedule
- Develop and present the performance metrics regarding different project tasks
- Plan and organize the maintenance tasks distribution
- Manage the priorities regarding the human resources and the finances
- Work close with the rest of the departments
- Encourage the team to apply the policies of the Occupational Health
- Ensure the good management of the allocated resources
- Manage and apply the policies of time management
- Ensure the efficiency of the section and actively participate in the conflict and problem solution
- Be oriented toward the results of the section and be capable of explaining the performances
- Time management, stress and priorities
- Ensure the integration and the application of the security rules and follow up the corrective actions
- Manage disciplinary actions
- Have a structured approach and keep the good quality of the controls
- Proved leadership and people management skills
- Direct and participate in a multifunctional environment with a strong team work mindset
- Good knowledge of the administrative practices and processes
- Quality and Occupational Health & Safety oriented
- Excellent motivational skills
- Management process knowledge of equipment supplies and maintenance
- Knowledge of predictive and preventive maintenance processes
- Strategies, techniques and technologies of the preventive maintenance knowledge
- Excellent knowledge of the maintenance and reparation fundaments
- Able to adapt to a changing environment
- Technical diploma (BAC) in Manufacturing
- DEC diploma in a related field
- Green belt certified
- Bilingual English-French
- Manufacturing environment experience (7 years minimum)
- Maintenance management experience (5 years minimum)
- Work in a union environment (3 years mínimum)
88
Maintenance Supervisor Resume Examples & Samples
- Ensures Facility and Material Handling Equipment is running at maximum efficiency with minimum downtime
- Diagnoses error conditions occurring in the Distribution Center and repairs accordingly
- Ensures the planning and scheduling of all maintenance activities including but not limited to inspections, preventive maintenance, installations and repairs
- Communicates at defined intervals with specified team members (Maintenance Director, District Facility Maintenance Manager, Director of Operations, Etc.)
- Keep local and regional management apprised of escalating abnormal or critical situations and coordinates resolutions/repairs with outside professional maintenance (if required)
- Ensures the compliance with Maintenance procedures
- Manage and ensure the integrity of maintenance inventory and critical spares
- Provides assistance in the configuration, maintenance, modifications, and system upgrades of MHE control systems to include programmable logic controllers (PLC) programming
- Monitors work processes and makes suggestions for modifications in order to increase and improve productivity, efficiency and accuracy for the purpose of improving costs; implements changes as directed or needed
- Responsible for efficient operation of equipment in the Distribution Center; ensures that problems with equipment such as air and heating systems, conveyer systems and forklift equipment are addressed
- Works with equipment and software vendors on design specifications and improvements
- Manage relationships with contractors and service providers
- Monitor site expenses and control maintenance budget. Provide feedback for budget planning and preparation for expenses and capital projects
- Develops and solicits bids from vendors for maintenance, janitorial, snow removal, landscape and other contracts necessary to support all building and MHE systems
- Assists in the process of selection, training and performance management for the Distribution Center associates in the maintenance department
- Directs the workflow, motivates, trains and monitors the performance of warehouse associates involved in the maintenance functions
- Responsible for associate relations functions including directing, supervising and developing a staff of skilled trade technicians and upkeep staff (custodian)
- Supports compliance with all appropriate policies, procedures, safety rules and Drug Enforcement Administration (DEA) regulations
- Ensures the documentation of maintenance records through the CMMS/EAM System
- Excellent technical and operational knowledge of mechanical, electrical and electronic equipment and systems
- Knowledge of Building Automation System such as Tracer Summit or Delta Controls is preferred
- Proactive problem solving skills; ability to recommend and implement solutions
- Ability to read and interpret CAD layouts, illustrated parts breakdown (IPB) diagrams, and electrical circuitry diagrams and drawings
- Ability to troubleshoot complex automated systems controlled by computers, programmable logic controllers (PLCs) and microprocessors in a high-volume work environment
- Strong interpersonal and communication skills to maintain cooperative working environment
- Effective written communications, presentation skills and organizational skills
- Ability to operate independently, to multi-task, and to prioritize quickly
- Computer software experience including MS office (Excel, Word, IM), MHE software such as RSLogix, Sort Director, GSMi, IPoint, Flex Sort, etc
89
Maintenance Supervisor Resume Examples & Samples
- 35% Leading Shift Coverage
- Provide shift supervisory leadership
- Ensure expedient M&R resources are applied as required to plant and equipment “uptime”
- Work with all departments to ensure their service requirements are met
- 35% Effective Application of PdM and PM Programs
- Enhance plant operations and equipment dependability through Cargill Reliability model
- Optimize PM and PdM systems to reduce downtime
- Create and implement PM program upgrades on a continuous basis
- 20% Effective Safety Management
- Develop, implement and optimize reliability systems where none exist
- Maintain total awareness of and ensures compliance with Occupational Health & Safety Act and Company Health & Safety policies
- Identify and recommend physical, procedural and ergonomic changes to the workplace in relation to daily tasks
- 10% Leadership and Development of Staff
- Provide leadership and mentorship to maintenance team
- Provide feedback to M&R Manager and salaried team
- Qualified Tradesperson (Electrician or millwright) or Engineering Technologist
- 1 + year supervisory experience
- Strong computer/data management skills
- Knowledge of Maintenance Management systems (process and software) and Predictive Maintenance Technologies
- Able to work rotating shifts, weekends and some holidays
- Able to work around live animals, dust, and dander
- Able to work in hot and cold environments
- Must be legally entitled to work for Cargill in Canada
90
Maintenance Supervisor rd Shift Resume Examples & Samples
- At least 5 years’ manufacturing maintenance work experience
- Demonstrated work experience in industrial maintenance
- Experience with one or more predictive technologies (Ultrasound, Infrared Thermography, Vibration, MCE, Oil Analysis)
- 2 years previous maintenance frontline leadership experience
- Advanced safety knowledge to include permit procedures, hazardous chemicals, and process safety management
- Experience with Microsoft Office and CMMS software
- Certified Maintenance and Reliability Professional (CMRP)
91
Maintenance Supervisor Resume Examples & Samples
- Build a Count on me Culture. Support and implement resort management strategic initiatives and programs. Identify areas of process improvement and leverage best practices by working with appropriate departments and colleagues as necessary. (5% time)
- Knowledgeable in safety use for power tools and shop tools
- Knowledgeable use of general Engineering tools and equipment
- Knowledgeable and experience with elevators
- Knowledgeable of power, water and sewer distribution
- Working understanding and ability to read blue prints
- Knowledgeable in fire codes and fire protection
- Demonstrate analytical ability to grasp numbers and understand their impact (e.g. demonstrated ability to work under pressure)
- Create a positive work environment by maintaining the highest level of ethics and integrity consistent with applicable regulatory standards and Wyndham Vacation Ownership values
- Commands a presence of respect and humility; demonstrating the ability to motivate and readily communicate expectations and follow up
- Professional appearance and excellent communication skills in dealing with guests and corporate personnel
- Ability to keep sensitive information confidential
- PC Skills
- Microsoft Office: Word, Excel, Outlook
- Key systems
- One year of supervisory experience preferred
92
Maintenance Supervisor Resume Examples & Samples
- Audit repairs/maintenance tasks performed by maintenance team; ensuring satisfactory and timely completion of all work orders
- Ensure that grounds maintenance duties are assigned and completed. This includes, but not limited to weed eating, trimming and unloading trash cans into dumpsters
- Ensure that all common areas are maintained and in proper operating condition, including pools, public restrooms, lobby areas, front entrance, meeting rooms, fitness centers, parking lots, walkways, elevators, etc
- Communicate with owners regarding repairs requiring expense approval (e.g., replace HVAC). Consult with manager regarding necessary outside professional services; work with manager to contract services
- Responsible for keeping maintenance shops in clean, organized and safe conditions. Order supplies as needed. Safeguard all supplies, equipment and tools
- Make sure that common areas are set up for special functions
- Prepares payroll for employees in maintenance department
93
Housing Maintenance Supervisor Resume Examples & Samples
- Responsible to schedule, organize, and to carry out preventive maintenance program effectively as per Marriott SOP and manufacturer guidelines
- Organize and supervise maintenance staff working under him. Making monthly duty roaster and adjust the shift duties as per business demand
- Get physically involved in projects but at the same time ensure that routine work is carried out in a timely and cost effective manner
- Carry out instructions, work orders or assignments given out by the Housing manager/DHR
- Supervise guest complaints as well as complaints from other departments regarding breakdown or malfunctioning of equipment associated with light, sound, telephones, television, plumbing or machinery
- Maintain log readings for water treatment on boilers, chilled water, domestic water systems and the swimming pool and keeping up to date record
- Follow instructions from water Treatment Company and maintain the correct dosages of chemicals to ensure complete protection of pipework and boilers surfaces
- Keep a close track of the performance of the engineering associates and review with chief engineer
- Ensure that all the preventive maintenance, work orders and assignments are carried out in a timely and cost effective manner keeping high standard of safety for each equipment and carry out weekly safety inspections of kitchen/laundry/life safety equipment and others
- Ensure that all logs are taken and a historical record is kept. Logs should be checked for necessary action. Keep all engineering log sheets in a proper file for record purpose
- Assist engineering associates in ordering the correct materials prior to commencing the work
- Ensure that all engineering spaces are safe, kept clean and in an orderly manner at all times
- Document and keep history of all jobs completed within the housing department
- Prepare weekly/monthly work schedule to enable the housing department to function effectively and cost effectively. (review and discuss with Housing Manager/DHR)
- Assist in energy conservative program, and to control utilities consumption
- Comply with hotel and corporate SOP’s
- Take logs readings for boilers/inspection of fire control room, fire pumps, etc
- To take active roll in the TQM process
- Cross train engineering associates within the department
- Be active member of hotel emergency rescue team
- Prepare weekly walk through to check all engineering critical areas for necessary action
- Be active member of hotel emergency response team. To ensure that each and every job is done to a high standard and that all your work is done with quality in mind
- To ensure that you maintain a high level of hospitality and guest concern. Practice at all times “Empowerment” and do whatever it takes to satisfy the guest
- Your uniform should be clean at all times if you have to go to guest areas. Your uniform should be changed on a daily basis
- Hygiene is of utmost importance, please make sure that you wash before coming to work and you practice good hygiene throughout your daily routine
- Accident prevention and safety to be aware of all existing departmental job safety analysis and to strive to work in an accident free manner and to create a safe working environment for himself and for others
- As a departmental trainer, you are responsible to carry out new hire training and departmental training programme, for five and safety for hotel and staff housing
- Making monthly walk through with Housing Manager/DHR for all engineering related areas and take corrective action accordingly
- Coordinate for the maintenance work with service providers as per service agreement. Follow up all pending work. Keeping all service reports up to date
- Replace the duty of chief engineer during his absence and perform other administrative work as business demand
94
Maintenance Supervisor Resume Examples & Samples
- Review workloads and assign appropriate staff to complete the repairs, maintenance or trip and brake inspections in a timely fashion
- Monitor equipment servicing repairs, by auditing staff and completed tasks
- Ensure appropriate material is on site to expedite repairs
- You hold a post-secondary degree in a relevant field
- You are able to develop and influence others
- Your English communication skills both written and spoken are excellent
95
Armament Maintenance Supervisor Resume Examples & Samples
- Manage Armament sytem upgrades, TCTO's and introduction of new weapons systems
- Train RSAF Personnel on maintenance of armament equipment and management functions
- Schedule equipment inspections, training and maintain training records
- Maintain equipment historical records
- Advise on troubleshooting, maintenance and repair of armament release and gun equipment
- Monitor input into the maintenance data collection system
- Train RSAF to the 5 and 7 level
- 1· High School Graduate, NCO Academy, Associates Degree in Applied Sciences
- Professional / Specialty: Armament Maintenance
- Total Number of years: 10 Years in Skill Level (if required): 5
- On Equipment of Weapon System or in required Specialty: F-15 Armament System
- Advisor on maintenance and management of F-15 C/D/S gun and release equipment
- Perform maintenance management functions
- Working knowledge of the F-15 C/D/S Armament equipment
- Working knowledge of the maintenance data collection system
- Understand training concepts and techniques
- Understanding of the supply system
- Working knowledge of Microsoft Word, Excel and Access software
- Understanding of the technical order system
96
Maintenance Supervisor Resume Examples & Samples
- 4 year degree OR high school diploma or equivalent with 4+ years equivalent maintenance or industrial work experience
- 2+ years maintenance experience in manufacturing or food processing environment
- 2+ years in supervisory role
97
Maintenance Supervisor Resume Examples & Samples
- Develops recurring preventative maintenance optimization by developing efficient schedules, analyzing of processes and effective execution to include mechanical systems, HVAC controls, electrical and civil systems and other real property and non-real property systems in the RWP program as needed
- Adapts RWP program and schedules to best meet requirements of customers and performance work statement
- Works closely with maintenance personnel in validating and scheduling RWP and in understanding preventative maintenance principles and processes
- Supervises and trains technicians to provide high quality work accomplishment and outstanding customer service
- Coordinates multi shop RWP activities with other supervisors
- Interfaces with facility managers and customers to provide personalized service in support of facility RWP execution
- Ensures the most efficient performance and timely completion of all RWP events
- Assists with daily labor inputs into CMMS for accurate tracking of manpower against assigned workload
- Communicates directly with facility managers and customers on a daily basis as needed to ensure RWP is accomplished with minimal impact to customer’s mission and/or production
- Provides monthly RWP reports for facility managers and maintenance engineering as requested
- Works with Quality Assurance to ensure accurate completion of RWP checklist items in accordance with current standards and recommends changes to equipment checklists and maintenance action sheets as required to maintenance engineering
- Maintains RWP records for each system and facility
- Provides assistance to Government representatives requesting access and information regarding the recurring maintenance scheduling, execution accuracy, and completion rates
- Assists Reliability Centered Maintenance (RCM) technicians with RCM scheduling and shop coordination
- Ensures that employees are aware of and adhere to standard timekeeping procedures and that timesheets are checked daily for compliance
- Follows corporate furnished information directives, standard operating procedures, etc
98
Munitions Maintenance Supervisor Resume Examples & Samples
- Supervises assembly, maintenance storage, reconditioning and handling of munitions, explosive devices and solid propellant rockets and motors routine disposal of unserviceable munitions assembly of mechanical components of certain guided weapons, handling and delivery of munitions and guided weapons
- Plans workloads and schedules work assignments and munition inspections
- Establishes and evaluates performance standards, maintenance control and work procedures
- Provides for and controls use of equipment, space and supplies
- Analyzes reports, operation check charts and maintenance records of munitions storage, maintenance, delivery, accountability and control to determine the need for improving work methods and repair techniques
- Develops and implements organizational and functional charts to establish lines of authority and specific responsibilities
- Coordinates munitions maintenance and technical escort functions for chemical and munitions
- Able to demonstrate expertise on all munitions and guided weapons in the RSAF inventory
- Experienced at planning and scheduling required munitions maintenance activities
- Able to introduce new weapons systems and maintenance practices
- Certified Explosive Safety Expert
- Knowledgeable in explosive licensing
- Working knowledge of the supply system
99
Maintenance Supervisor Resume Examples & Samples
- Directs the activities of all maintenance personnel with the accountability of the Business Unit’s quality, cost, safety and morale. Identifies training needs and establishes technical expertise within the business unit
- With the assistance of the engineering department, assist in development and implementation of capital projects. Assumes a leadership role in identifying possible productivity improvements projects
- In conjunction with BUM assist in the development and implementation of Business Unit’s productivity projects
- Responsible for managing effective employee relations activities, GMP compliance and Diversity initiatives. Ensures compliance to governmental regulatory OSHA and safety programs and processes
- Effectively communicates with all employees, direct reports and production personnel to coordinate maintenance activities
- Responsible for directing preventive/predictive maintenance programs designed to reduce unscheduled downtime (maximize equipment availability) downtime (maximize equipment availability extend equipment life, and to optimize utilization of people and resources
- Supports and promotes future efforts to effectively introduce and implement maintenance redesign initiatives
- Coordinates with the BUM the maintenance operating budget to support business objectives. Continues to identify methods/procedures for reducing overall maintenance cost annually
- BS in Engineering, Manufacturing Technology or a related field preferred
- The successful candidate MUST have a basic knowledge of mechanical and electrical control systems as they pertain to food processing as well as knowledge of applicable OSHA and EPA regulations
- A maintenance professional with a minimum of two (2) years supervisory experience in maintenance operations, capital project management, etc
- Food, beverage, or pharmaceutical background preferred
- Strong interpersonal skills to facilitate supervising others as well as working and problem solving with others as well as excellent written and verbal communication skills
- The Maintenance Supervisor may be required to work different shifts in addition to being on call for consultation during other shifts
100
Exhibits Maintenance Supervisor Resume Examples & Samples
- Performs duties and responsibilities that are common to most supervisory positions
- Responsible for supporting special events during weekends. Supports special events requiring support from Exhibits, Fleet and Facilities Maintenance
- 4 years exhibits or attraction maintenance administration. Additional education may be substituted for experience at the rate of 2 years of education for each missing year of experience
- 6 years exhibits or attraction maintenance administration
101
Maintenance Supervisor Resume Examples & Samples
- Associates or Bachelor degree strongly preferred and advanced degree a plus
- Three plus years of facility management and automotive manufacturing, or industrial experience recommended
- Must have strong written and verbal communication
- Must have extensive knowledge on Microsoft Office (EXCEL, Word, PowerPoint, Outlook, Access)
102
Power Generation Maintenance Supervisor Resume Examples & Samples
- Minimum Acceptable Experience Level
- Language Skills:Strong, professional, oral and written English communication skills
- Citizenship:US Citizenship is not required
- Knowledge of principles and processes involved in operating and maintaining diesel engines at an overseas facility
- Computer skills, specifically in Microsoft Word and Excel
- Must successfully complete and pass the medical and dental examinations as required by PAE and our customer for deployment to Iraq. Must maintain physical and dental requirements for duration of deployment
103
Process Maintenance Supervisor Resume Examples & Samples
- Review procedures and update them as necessary
- Ensure a safe work environment is maintained through adherence to safety guidelines and policies
- Must follow safety rules and ensure compliance with GA state and federal EPA regulation and laws. Specific responsible system repairs, upkeep, and maintenance managed within regulating agencies such as OSHA
- Continuously stay current with assigned SOPs and keep an up to date training file ensuring compliance with all applicable Standatrd Operating Procedures
- Ensure all mandatory training requirements are met, including annual EHS training, GMP refresher training and any applicable training requirements
- Maintain an on-going two-way performance dialogue with Manager and meet timelines for completing all mid and year-end reviews and development plans for self and direct reports
- Demonstrate continuous progress with respect to increasing job knowledge and proficiency in technical understanding/problem solving
- Maintain a positive, professional and customer oriented attitude. Communicate any concerns related to safe work practices, hostile work environment, sexual harassment or any other type of employee misconduct directly to the supervisor, manager or human resources
- Excellent technical troubleshooting/problem solving skills are a must. Must be knowledgeable with respect to the operation and maintenance of various process systems including centrifuges, mixers, agitators, filtration, CIP, filling and packaging lines
- Possess very strong verbal and written communication skills, documentation practices (cGDPs), be self-motivated and possess strong interpersonal skills. Have a thorough knowledge of utility equipment, using blue prints, equipment manuals, specifications, standard operating procedures, and be able to use proper judgment when taking corrective actions during equipment malfunction
- Possess strong mechanical knowledge and skills on utility equipment. Have working knowledge of hazardous chemicals and their disposal, OSHA and FDA requirements. Demonstrate continuous progress with respect to increasing job knowledge and proficiency in technical understanding/problem solving
- Must have the following personal attributes: Integrity and trust, work ethic, sound judgment, intellectual honesty, pragmatism, courage and conviction
- Must have computer skills (Word, Excel, BAS, Scada systems)
- Must have passion to innovate and drive for solutions
- Must have uncompromising dedication to quality
- Must have relentless focus on rapid and disciplined action
- A Bachelors degree in Engineering or equivalent work experience with continuing education in a maintenance environment is required
104
Maintenance Supervisor Resume Examples & Samples
- Supervise, train and coach departmental employees
- Participate and instruct mechanics in the repair and reconditioning of automobiles, trucks, tractors, graders, loaders and other standard and specialized machinery and equipment
- Introduce, implement, improve and monitor reliability strategies including preventative and predictive maintenance programs for continuous progress
- Work closely with the planner, EHS and other departments to build and sustain effective working relationships
- Manage and promote safety, food safety and quality processes
- Ensure compliance with all company and country regulations
- Capital improvements and budget compliance
- Perform miscellaneous job-related duties as assigned, such as payroll-Kronos, inventory control and maintenance scheduling
- Bachelor’s Degree preferably in Mechanical/Electrical Engineering, Industrial Processes
- Experience in direct supervision in plant setting
- 3+ years maintenance experience in manufacturing or food processing environment
- Fluent in English and Dutch language
- Familiar with PdM techniques of thermography, vibration, ultrasound and mechanical integrity testing, oil analysis
- Working knowledge of Microsoft Office, Maximo and Kronos
- Mechanical aptitude
- Strong problem-solving and decision making skills
105
Maintenance Supervisor Resume Examples & Samples
- 3 years experience working in large diesel engine manufacturing
- 3 years experience working as an hourly skilled technician in support of manufacturing lines
- 1 year experience as safety champion, safety officer or safety trainer
- 2 years experience as a Team Lead and/or Supervisor
- At least 2 years of credits toward a college degree
- Knowledge of various engineering, manufacturing and/or maintenance standards and practices and various Caterpillar systems
106
Maintenance Supervisor Resume Examples & Samples
- Supervises site maintenance personnel
- Responsible for supervision of contractors
- Ensure that maintenance work is properly planned and executed including
- High school diploma or GED required. Associates or Bachelors degree preferred
- At least 4 years’ experience supervising maintenance personnel
- Experience with computerized maintenance systems, specifically SAP
- Knowledge/Experience of operation and maintenance of plant utilities (i.e. steam, compressed air, cooling towers, chillers, HVAC, etc.)
- Knowledge of OSHA regulations - particularly Process Safety Management
- Knowledge of industry process standards including ASME B31.3
- Facilities Management experience (utilities, service contractors, general facilities upkeep)
- Knowledge of ISO 9001:2008 requirements
- Knowledge of GMP standards a plus
- Experience in creating maintenance operational procedures a plus
- Must be self-motivated and be able to work independently
- Must be hands-on
- PSM experience preferred
- Experience in computerized maintenance planning (experience installing/developing/initiating a CMP process a plus. SAP experience a plus)
- Participate in HSES activities directed by management/supervision or as indicated in the HSES Annual Site Plan
107
Maintenance Supervisor Resume Examples & Samples
- High school diploma GED required
- College degree or equivalent experience in manufacturing related field preferred
- Mechanical and electrical course work providing pipefitting, machine repair, hydraulic, welding and electrical knowledge
- Two (2) to Five (5) years direct supervisory experience/training
- Strong background knowledge of operating equipment and department processes including PLC programming & panelview and equipment controls programming
- Understand principals of safety and safe work
- Must be able to read blueprints. Ladder diagrams and AutoCAD preferred
- Strong communication skills both verbal & written
- Must have good judgment in reporting errors or unusual conditions or events to Plant Management
- Must be capable of making independent decisions and judgments based on process experience and chemical knowledge
- Strong organizational skills including document management, tracking , results follow-up
- Good PC, Excel and Word software skills
- Strong understanding of maintenance and the maintenance process
- Ability to recruit, train and motivate personnel in order to balance staffing strength with profitability
108
Plant Maintenance Supervisor Resume Examples & Samples
- To ensure the Track Plant equipment is maintained to optimum standard during the night shifts
- The role will require interventions in production at Fisher Street Shaft and routine maintenance at Westbourne Park
- Supervising plant breakdown recovery, maintenance and improvements on plants during the night shift production
109
Maintenance Supervisor Resume Examples & Samples
- Provides administration and supervision of the plant maintenance function as directed
- Provides and plans technical training
- Arranges for all equipment in area to be properly maintained and upgraded as needed
- Provides daily logs including daily scheduled and nonscheduled work sheets and equipment PMs
- Accesses, inputs, and retrieves information from the computer
- While the regular working cycle of this position is usually 5 days on (Monday-Friday), this job may include working weekends (Saturday and Sunday); working hours may vary as specified by management. Incumbent must be able to work overtime on a regular basis and/or be on call as directed by management
110
Plant Maintenance Supervisor Resume Examples & Samples
- Supports development, implementation, maintenance, and ongoing improvement of the food safety system
- Arranges for maintenance of adequate level of supplies, materials and parts so that there will be no interruption in operations due to shortages
- Stays current in new technologies and applies them as applicable to the manufacturing process
- Maintain positive relations with local bargaining unit ensuring a high level of productivity (if applicable)
- Establishes and maintains an employee relations climate of trust and confidence that will discourage third party interference, or establishes and maintains an employee relations climate of trust and confidence with employees, their union stewards and representatives which will promote achievement of plant and company goals
- Establishes and maintains effective work relationships within the department, the division, the group, and the company. Includes ability to handle stress and to interact with others so as to establish and maintain a positive and productive work environment and minimize personal conflicts
- Performs those administrative activities necessary for effective management, including provision for selection and development of employees, salary administration, budget administration, employee safety, employee counseling, motivation, meeting objectives, planning, organizing, integrating and measuring the work performed within the organization
111
Maintenance Supervisor Resume Examples & Samples
- Selects, develops and coaches employees to ensure the efficient operation of their job function
- Provides recognition to employees. Assists Manager in creating employee goals to align with site strategic planning
- Conducts timely employee performance and goal Conducts shift/departmental meetings as scheduled
- Coordinates effective delegation of work assignments and training
- Ensures training is provided to staff
- Addresses issues with employees and maintains supportive documentation
- Adheres to Company policies, procedures, and applicable budget requirements
- Coordinates and ensures maintenance is completed for all production equipment, infrastructure, facilities and grounds
- Develops, maintains and institutes Total Preventive Maintenance & Predictive Maintenance programs for all equipment in partnership with the Facilities and Automation teams
- Ensures repairs for electric, pneumatic and hydronic systems are completed as needed. Ensures replacement of defective components to restore proper operation of equipment. Oversees repairs for mechanical systems. Schedules modifications to equipment to achieve desired results. Updates the maintenance work order system and assigns daily work orders
- Researches, evaluates and implements technologies and methods to improve quality, efficiency and reduce cost of facility utilities
- Maintains a clean and safe work area. Wears required Personal Protective Equipment. Performs duties in a safe manner and observes approved safety procedures
- Communicates potential hazards immediately to Manager and identifies and corrects potential unsafe conditions
- Executes assignments and assists in the maintenance of the ISO 9001 and 14001 systems
- Oversees, delegates and/or updates and reports out on department metrics and visual plant displays through the use of the Lean Manufacturing tools and processes
- Completes miscellaneous tasks as assigned in support of the Chaska campus strategic plan, and larger organizational and production goals
- Participates in Continual Improvement activities
- Bachelors degree in engineering, business management or related fields
- Minimum of five years of maintenance experience in a lean manufacturing environment with a minimum of 7 years supervisory or management experience in an engineering or maintenance department
- Excellent organizational and planning skills, communication skills and an ability to lead a multi-department team
- Advanced computer skills required; proficient using Microsoft Office suite, Allen Bradley Software platform and AutoCAD 2015
- Ability to lift 50 lbs, climb a ladder up to 15 ft. and walk and stand during entire shift
112
Die Maintenance Supervisor Resume Examples & Samples
- Bachelor's degree required, or
- Journeyman Die Maker status with a minimum of 8 years of related manufacturing experience
- Experience with die repair, construction, tryout and/or die maintenance work activities
- Ability to work any shift and work overtime as required
- Hemmer experience a plus
- Root cause analysis skills
113
Maintenance Supervisor Resume Examples & Samples
- Bachelor's degree in a technical / engineering discipline required; or Journeymen status with minimum of 5 years manufacturing experience; or Minimum of 10 years of technical/manufacturing experience
- Must possess a working knowledge of advanced technical problem solving tools
- Ability to interface with various levels of employees within all areas of the Plant from hourly represented employees to Senior Leadership as required
- Goal oriented and a self-starter and ability to lead and manage in a team based structure
- Green Belt/ Red X/ Six Sigma Training
114
Maintenance Supervisor Resume Examples & Samples
- Ensure safe execution of the Daily and Weekly Maintenance Schedule
- Directly supervise a team of craftsman, technicians, and apprentices performing maintenance duties
- Reviewing completed work for effectiveness
- Assess the performance of their direct reports and provide training opportunities
- Problem solve, delegate, prioritize and coordinate projects and tasks among several shifts
- Effectively communicate with all key players and build cooperative relationships with various functional areas
- Provide guidance and leadership to their direct reports to help advance the MBM culture
- Support the advancement of World Class Maintenance initiatives to improve equipment reliability
- 3-5 years successful experience in Maintenance Supervision in a fast paced manufacturing setting
- Strong computer skills, proficient in the use of Microsoft Office including Word, Excel, PowerPoint, and previous experience with CMMS software
- Proven maintenance experience with electrical and mechanical systems, hydraulics, and pneumatics
- Demonstrated leadership skills and experience
- Capable of communicating and expressing ideas clearly and concisely, in both written and oral formats
- Technical Diploma or Degree in an engineering or maintenance-related field preferred but not required
115
Maintenance Supervisor Resume Examples & Samples
- 1 - following all safety rules and practices
- 2 - actively participating as a member of the safety committee
- 3 - conducting safety training and performing safety observations
- 4 - leading maintenance associates, and serving as coach and counselor regarding professional development and when situations arise that affect associates' job performance
- 5 - supervising maintenance associates, including assigning work and determining work schedules
- 6 - contacting and working with vendors and subcontractors to achieve desired results
- 7 - championing preventive maintenance processes
- 8 - purchasing materials, parts, and supplies as required
- 9 - providing technical expertise regarding plant equipment and facilities
- 10 - implementing quality improvement and cost reduction ideas
- 11 - maintaining adequate inventories of spare parts
- 12 - prioritizing maintenance activities
- 13 - accurately and completely preparing and maintaining maintenance records and other paperwork
- 14 - troubleshooting and solving problems
- 15 - maintaining teamwork with other associates
- 16 - maintaining work areas to plant standards of housekeeping
- 17 - actively participating as a member of the lead team; and
- 18 - performing other duties as assigned by the plant general manager
- 0 Qualifications for maintenance supervisor are the ability to perform the duties / responsibilities of the job with or without accommodation; extensive knowledge and understanding of electrical, mechanical, pneumatic, hydraulic, steam, and interrelated systems; maintenance work experience in a manufacturing environment; an engineering degree or equivalent work experience; the ability to read, write, and speak English; the ability to learn; and the ability to follow policies and procedures, ask questions, and work effectively as a member of a team
- 1 The plant general manager evaluates maintenance supervisor qualifications
116
Maintenance Supervisor Resume Examples & Samples
- Selection, training, and supervision of maintenance department personnel with focus on developing team members for technical capabilities as well as driving cross training throughout the team to improve flexibility and coverage across various production equipment
- Assign duties and direct and follow up on the work performed by maintenance personnel
- Develop preventive maintenance program to reduce costly machine downtime
- Contract outside services for repair and maintenance of equipment and buildings
- Purchase maintenance supplies and repair parts
- Confer with technical, equipment, and supply sales representatives to obtain data to support plant operation
- Recommend and assist in the purchase of capital equipment
- Assist the Plant Manager with assigned tasks
- Approve invoice payment of supplies, repair ports, etc
- Act as contact person for governmental agencies such as DNR and OSHA
- Assist in meeting the plant Health, Safety, Environmental and Security goals. This includes participation in communicating related metrics, participating in internal and external audits and bringing continuous improvement ideas forward
117
Maintenance Supervisor Resume Examples & Samples
- Ensure the safety, health, and well-being of all maintenance personnel in the conduct of all maintenance activities
- Manage day-to-day maintenance activities interacting with the Maintenance Manager, Maintenance Planner, Maintenance Techs, Gatekeeper, Maintenance Reliability Engineer, and customers to provide the needed and expected level of service and to meet mutual individual and group goals
- Provide after-hours support for maintenance issues that cannot be resolved by the technicians called in by the Operations Supervisors
- Complete required OSHA PSM maintenance related requirements for the site
- Provide leadership of day-to-day maintenance execution, turn-around management, cost control, and associated individual contributor tasks
- Arranging for service providers and other contractors for extra ordinary maintenance during the shutdown periods
- Track and monitor site maintenance plan with all associated reporting requirements in partnership with the Maintenance Planner
- Management of outside service contractors and material vendors to ensure the best value per dollar for BASF
- Provide counsel and coaching when required to maintenance personnel to help overcome various work related issues
- Perform regular performance reviews and evaluations for all maintenance personnel
- Represent the interests of the maintenance group to management as a conduit to forward and receive information/problems/concerns
- Oversee maintenance group training in partnership with the Training Coordinator
- Oversee maintenance, repairs, and changes to non-process site systems, including the Simplex Fire Alarm System, and site security systems
- Ensure that all jurisdictional inspections are completed on time and that PA operating certificates are current for Boiler & Pressure Vessel inspections in partnership with the Maintenance and Reliability Engineer
- Hire the best personnel available when required with the goal of building the best team possible
- Recognize and encourage development of maintenance personnel to full potential
- Work within the BASF documented business management system, policies, & procedures
- Motivate and challenge to drive high performance
- Create an inclusive environment which embraces and derives value from diversity
- Role model and enable development of competencies in others needing to implement BASF strategy
- Demonstrated safety leadership of a team in a chemical or industrial environment
- Continuous improvement experience (such as RCFA, FMEA, or RCM) in a maintenance organization
- Previous experience in managing maintenance programs such as PSVs, Boiler Inspections, and Vessel Inspections
- Previous experience with the Maintenance and Purchasing portions of SAP, including the ability to share knowledge with others
- Expertise with Microsoft Office Products such as Excel, Office, Outlook, and Power Point, including the ability to share knowledge with others
- Demonstrated personnel leadership and teambuilding experience, preferably in a chemical or industrial supervisory position
- The ability to take a desired goal for the maintenance organization and develop specific relevant tasks with and for the technicians to support and achieve that goal
- The ability to develop and balance the skills of the BASF technicians with the skills available through contractors to provide complete maintenance to the site that is efficient and cost effective
- The ability to read, understand, explain and teach from technical manuals and engineering drawings such as PFDs, P&IDs, vessel/equipment design drawings, and building layouts
- Familiarity with typical site requirements in environmental, health, and safety; and understanding how they impact the maintenance organization and maintenance activities
118
Maintenance Supervisor Resume Examples & Samples
- Maintain plant facilities for the manufacture of product
- Manage maintenance costs to the overall benefit of the company
- Provide the leadership to move from a reactionary repair mode to one that performs work in an orderly and proactive manner
- Lead the effort for a zero recordable record/safety performance of the maintenance department
- Identify opportunities and implement solutions that move the manufacturing operation toward increased capacity through increased reliability of equipment and down time reduction
- Provide mechanical/electrical expertise and guidance to help the technicians assure the highest quality of repair work
- Manage the maintenance training program and monitor training progress of all technicians
- Improve communication between maintenance department and all other departments at the plant
- Work with Production Superintendent, Maintenance Planner/Scheduler and Storeroom Administrator to prioritize, scope, plan, schedule, and execute daily work
- Contribute to Manufacturing Excellence initiative by driving continuous reliability improvement opportunities at the plant through identifying, scoping, and executing small projects,
- Facilitate tracking of maintenance department activities and costs through effective documentation in, and the utilization of, the CMMS (SAP)
- Validate the following on all work orders: All work is done correctly, all completed work is of high quality, and the work area is left in a clean and safe condition
- Give final approval to close out the work order
- Plan and lead maintenance safety/training meetings as required
- Communicating department activities to the maintenance/reliability manager and other staff
- Generation of incident reports in manufacturing solutions and MOC’s as required
- Personnel responsibilities: Conduct annual performance reviews, Approval of staff vacation, time off, etc. and E-time approval, control/manage attendance
- Assure staff accountability including discipline, as appropriate
- Bachelor’s degree in technical field. Discipline in chemical, mechanical, or electrical engineering preferred
- Minimum 2+ years of supervisory experience in chemical, nuclear, or other heavy industry in leading maintenance crews, planning corrective and predictive maintenance, and prioritizing jobs
- Demonstrated knowledge and experience of chemical plant equipment (pumps, piping, heat exchangers, vessels, instrumentation, etc.) along with a background in maintenance and repair of this equipment in order to effectively lead/guide Maintenance Technicians and contractors in the execution of daily maintenance activities
- Excellent leadership and organizational skills for directing and motivating maintenance personnel and for facilitating cooperation with all other departments
- Possess strong leadership capabilities
- Proficient with Microsoft suites (Outlook, Word, Excel and PP)
- Proficient with maintenance modules of SAP preferred
119
Maintenance Supervisor Resume Examples & Samples
- College degree in engineering strongly preferred
- 3-5 years of engineering experience or supervisory experience in fast paced manufacturing environment
- Able to lead cross functional teams, strategic planning, and conflict management experience
- Highly skilled problem solver of manufacturing machinery and equipment
- Trained in process improvement (Lean, Six-Sigma, 5S, and other discipline) preferred
- Read, and analyze charts, work-orders, production schedules, and other records of reports to determine production requirements and to evaluate current maintenance repair estimates and outputs
- Experienced in developing training programs for Industrial Maintenance Mechanics highly preferred
- Develop and interpret various problem solving techniques/methods (TCC/ Trouble Cause Correction)
- Able to organize, planning, and prioritizing work and communicate and update all stake holders internal or external
- Managing the work
- Making Things Happen ThroughTeams
- Being a Strong Role Model and Leader
120
Maintenance Supervisor Resume Examples & Samples
- Handle all aspects of maintenance for the Essex community
- Monitor and direct scheduling of all maintenance personnel and vendors, and ensure staff adheres to company policies and procedures
- Track inventory for repairs and maintenance
- Responsible for turnover process, troubleshooting and repair of all mechanical systems, service requests, and reporting of potential liability concerns or safety hazards
- Assist with planning and execution of all preventative maintenance programs such as mechanical, electrical, HVAC, plumbing, fire and life-safety systems
- Minimum 4 years industry experience (100 units or more)
- Ability to directly supervise staff of up to 4 or more
- Must be proficient in all areas of apartment maintenance to include plumbing, electricity, painting, drywall, floor coverings, carpentry, locks, appliances, pools & spas, roofs and life safety equipment
- Ability to identify water intrusion issues, make repairs and/or monitor work completion by qualified vendor
- Basic computer skills, including working knowledge of Outlook, Word, and Excel. Yardi preferred
- Available for emergency call dutiesMust be able to function effectively in a customer service environment
121
Senior Maintenance Supervisor Resume Examples & Samples
- Handle all aspects of maintenance for one or more communities and/or 500 units
- Supervise maintenance associates providing training, motivation, and performance feedback
- Ensure the knowledge of, and enforcement of, company safety policies
- Responsible for operating within the property budgetary guidelines
- Minimum 5 years industry experience (100 units or more)
- Strong written/oral communication skills and business correspondence
- Must be able to meet the physical requirements of the job
- Available for emergency call duties
122
Maintenance Supervisor Resume Examples & Samples
- Supervise the area team, which includes performance management, capability development, scheduling and effectively administering the collective bargaining agreement
- Ensure predictive and preventative maintenance programs are carried out in a timely and efficient manner
- Manage site maintenance staff and all facility contracts and contractors
- Administer safety programs and ensure maintenance work is performed safely and effectively
- Identify and implement equipment modifications, refurbishment, replacements and additions by using effective management of change process
- Utilize statistical techniques for root cause analysis and problem prevention
- Administer the maintenance budget
- Ensure effective communication within the team as well as outside the department
- Perform maintenance facilitation and review of engineering design package
- Five or more years of experience in a plant environment, preferably within a proactive maintenance department (i.e. cleaning and inspection by operators, planned maintenance schedule, disciplined store room, computerized maintenance management system)
- Supervisory experience, including coaching and facilitation, with skilled trades, union and non-union employee groups
- Packaging equipment experience is preferred
- Strong computer skills with Microsoft Office suite; SAP experience is an asset
- Demonstrated ability to deliver timely and effective results while adhering to budgetary and scheduling constraints
- Demonstrated commitment to safety practices and continuous improvement
123
Site Maintenance Supervisor Resume Examples & Samples
- Degree in Engineering/ Advanced Diploma (min 3 yrs.)
- A minimum of 5 years’ experience in electrical maintenance engineering in a food or drink manufacturing environment
- Proven first line management skills is critical
- Computer Literate
- Knowledge in SAP and EISC is required
- Resource management Skills
- People management & motivational skills
- Networking/influencing /communication skills
- Proven capability in people management and Coaching skills
- Knowledge in Root Cause Problem Solving (RCPS) Research skills
124
Maintenance Supervisor Resume Examples & Samples
- Supervises all maintenance operations for assigned equipment in accordance with applicable PWS, Company policies, OSHA, DOT, ANSI, ASME and applicable military regulations
- Supervises shop foreman and mechanics to include vacation planning, discipline, conducting performance evaluations, and training
- Establishes job priorities and estimates down time
- Coordinates work flow for downed equipment waiting for parts to minimize backlog of work and cost to customer division
- Provides direct support to internal/external customers to ensure compliance, tracking efficiency, burn rates, equipment usage and maximizing cost avoidance measures
- Supervises the recovery operations of MHE, VE, CE, Heavy and Light vehicle maintenance throughout assigned area of operation
- Coordinates the proper administration, maintenance and distribution of approved publications, warranty documentation, and LDD and ECOD documentation
- Provides input to management for forecasting and monitoring of the stock levels for required service/repair parts and petroleum
- Responsible for the accurate and timely submission of all required plans and reports
- Maintains effective lines of formal and informal communication amongst all levels of management (and the customer) as required
- Coordinates collection and preparation of activity reports
- Supervise and coordinate all maintenance activities required per the preventive maintenance program
- Responsible to provide for and enforce guidelines to ensure the health, safety, and welfare of all assigned employees
- Acts as the POC for all maintenance issues in the absence of the Maintenance Manager
- Monitors team development and ensures the execution of performance evaluations in accordance with DI policy
- Conduct site visits to establish professional relationships with maintenance teams, site personnel, and the customer as needed
- Understanding of organizational maintenance and supply concepts and procedures
- Understanding of maintenance production, production control and knowledge of U.S Army maintenance support systems
- Knowledge of MHE, heavy truck and or heavy equipment
- Knowledge of equipment parts acquisition, warranty, LDD, and ECOD submissions
- Must possess knowledge of DOT, OSHA, ANSI, ASME, Military regulations standards and OEM requirements
- Knowledge of diagnostics and ability to conduct technical research
- Strong understanding of Department of Defense contracting policies and procedures
- Outstanding problem solving skills and sound judgment
- Excellent writing, communication, leadership and interpersonal skills
- Demonstrative proficiency in Microsoft applications
- Must be able to meet deployment status requirements
- Associate's degree in an associated discipline
- Two (2) years of experience in related field can be substituted for each year of the four (2) years of college
- Six (6) to eight (8) years of logistics experience in a military/tactical environment
- Prefer at least three (3) years in a maintenance supervisor environment
125
Maintenance Supervisor Resume Examples & Samples
- Responsible for maintenance issues within the hotel
- Perform daily checks around the hotel
- Conduct lift emergency release procedures as required
- Develop, implement, and direct all emergency programs
- Coordinate renovation bidding, define the cost and scope of the project, and oversee the general contractor and subcontractors to ensure quality work is performed cost effectively
- Responsible for the health and safety of the hotel
126
Area Maintenance Supervisor Resume Examples & Samples
- Manages procurement, expediting, traffic, and subcontract administration functions
- Ensures accurate and timely submission of financial, administrative, procurement, and material control requirements
- Establishes effective communications between project and home office functions to ensure accurate and timely flow of information; provides financial status reports to management
- Work is performed without appreciable direction
127
Area Maintenance Supervisor Resume Examples & Samples
- Supervise projects related to the installation, maintenance, and removal of building utility systems (i.e. electrical, plumbing, heating/ventilation/air conditioning), painting, flooring, masonry, carpentry, and furnishings; and communicate accordingly with workers/contractors involved in these tasks
- Monitor the progress of special projects and report to Director of Facilities as requested
- Schedule and coordinate all aspects of major work projects
- Participate in planning and design of maintenance work, replacements, improvements, upgrades, and major projects within facilities
- Serve as liaison between Facilities Office, building staff, students and Plant Operations, Dean of Students office, parents, student organizations, Greek organizations, Vanderbilt Police Department, Campus Planning, and Reservations & Events Office
- Report and follow-up on all maintenance concerns. Monitor work orders and submit billing information to Facilities Office
- Resolve complaints from students, parents, staff, and guests
- Evaluate facilities and develop scope of work for projects within buildings for comprehensive budget projections
- Compile reports that provide purchase recommendations for budgetary purposes
- Retain accurate records of inventory for respective areas (furniture, electronics, keys, tools, maintenance supplies, moving equipment, and other items upon request)
- Back up responsibility for another residential area
- Residence halls operate 24-7. This position requires flexibility to work weekends and evenings when necessary
- Maintain cell phone service and respond to University calls
- Respond when called to emergency situations such as flood, fire, utility failure or natural disaster
- Be familiar with fire codes, fire equipment (functions, locations, and operation), and building security
- Responsible for product sampling, product safety inspections, regular testing and inspections of products and product maintenance or maintenance scheduling
- Participate in planning student occupancy with Housing Assignments and Residential Education and summer attendees’ residency with Conference Office
- Participate in Residential Education staff selection and training
- Indirectly supervise the maintenance work crew: assign work, instruct in methods and procedures, and handle complaints and employee problems
- Directly supervise summer work crew, temporary work crews and contractors
- In conjunction with other employees, is indirectly responsible for the development, implementation, and/or control of departmental budgets; makes recommendations to assist department director
- Formulate specifications and project scope for estimating costs within respective areas
- High school graduate or GED required (substitution of experience for minimum education is not permitted)
- Five years in a related craft or maintenance field
- Associate degree or above preferred
- Experience as superintendent for construction project(s)
- Ability to use the required tools and equipment for maintenance purposes
- Requires experience with different types of technology with regard to mechanical systems
- Knowledge of Microsoft Office (Excel, Word, Outlook, Windows, and Power Point), Adobe PDF viewer, network Systems, file sharing, copiers, printers, scanners, and fax machines
- Blueprint reading experience
128
Maintenance Supervisor Resume Examples & Samples
- Supervise staff in performance of custodial duties, such as sweeping, and polishing floors, dusting equipment, furniture and fixtures, and removing trash and debris from auction grounds, etc
- Assist as necessary
- Supervise, coordinate and assist when necessary personnel engaged in performing structural repairs to building and ground maintenance activities, such as mowing, raking, removing weeds, etc
- Inspect completed work for conformance to specifications and required standards
- Inspect, test, and repair equipment, electrical systems, heating and cooling systems, etc. to ensure proper working condition
- Maintain accurate records and reports regarding the maintenance activity of the Auction, including water testing reports, etc
- Monitor inventory and initiate purchase of needed maintenance equipment and janitorial supplies
- Supervise and direct the work of maintenance employees by determining work procedures, preparing work schedules, expediting the workflow, assigning duties and examining work for accuracy and conformance to policies and procedures. Assist manager in counseling and disciplining employees as necessary
- Assist with and supervise pre-sale and pre-event set up activities
129
Maintenance Supervisor Resume Examples & Samples
- To provide team leadership, safety leadership, mentoring, coaching and support
- Implementing the weekly work schedule issued by the Maintenance Planner/Scheduler
- Manages the day-to-day maintenance function within his/her area of responsibility
- Acts as the principle contact between the Maintenance Department and Production Supervisors
130
Maintenance Supervisor Resume Examples & Samples
- 25% Development and supervision of maintenance stakeholders
- 25% Accountable for maintenance, equipment repair, and sanitation requirements. Troubleshoot causes of plant equipment problems and oversees coordination of proactive and reactive activities on a daily basis. Develops and maintains plant preventative maintenance programs. Coordinates repairs and supplies/parts purchasing
- 20% Maintain adherence to all Corporate Environmental Policies and Procedures to keep the facility in compliance with all Federal and State laws. Manage wastewater treatment system operation to ensure permit compliance. Ensure Process Safety Management program is maintained
- 15% Provide leadership in the areas of customer focus, continuous improvement, food safety, and personal safety as they relate to maintenance activities. Support a ZERO injury culture and drive continuous improvement to safety and safety programs. Ensure contractors/employees comply with all relevant Governmental and Cargill Safety Requirements
- 10% Develop and maintain energy efficient systems with demonstrated continuous energy use improvements
- High school diploma or GED equivalent required
- BS or BA in Processing, Engineering or Food Science or equivalent experience
- Or appropriate associate technical degree with 2 years of experience
- 2+ years of experience in food operation/processing and/or manufacturing environments
- Working knowledge of processing plant/equipment
- Computer literacy and eagerness to learn SAP/Maximo systems
131
Maintenance Supervisor Resume Examples & Samples
- Ensures equipment in the area assigned is in working order and that working conditions are safe at all times. Verify the readiness of the production line at start-up and supervise change overs
- Provide the proper training in Controls and Electricity to the Maintenance Technicians for the purpose of minimizing the production down time
- Identify and prioritize controls / electrical opportunities to maximize operations performance within a facility
- Plan and execute projects in a manner which minimizes downtime
- Develop and maintain electrical and controls system documentation
- Maintain and troubleshoot production equipment from various suppliers
- Quickly identify root causes of problems, as mechanical, controls or joint problems and coordinate resources necessary to address them
- Develop control software to achieve the balance between mechanical and controls changes to effectively handle all containers
- Maintain Allen Bradley hardware and software: PLCs, VFDs, HMIs, Networks and various electrical systems
- Be part of the team that supervises the electrical installation / integration of equipment and controls
- Follow Company Controls and Electrical Specifications
- Work with the Company Controls Engineering Group for the following purposes
132
Maintenance Supervisor Resume Examples & Samples
- Bachelor’s Degree in Engineering or related Technical field or a minimum of 5 years of related experiences and/or training; or equivalent combination of education and experience
- Understanding of mechanical, electrical, pneumatic, hydraulic, and utility systems including boiler systems
- Must have the knowledge of good manufacturing practices, and food processing equipment. Be safety and quality minded and have the ability to make sound decisions. Understand OSHA/FDA/USDA/EPA requirements
- Understanding of direct and overhead cost systems
- Experience using, trouble-shooting and programming Allen Bradley PLCs
- Must be able to work flexible schedule to include days, afternoons, midnights, and weekend work
133
Maintenance Supervisor Resume Examples & Samples
- Assist and partner with business leaders on implementation of process improvement (Six Sigma / Lean/Kraft Heinz Global Production System (KHGPS), including leading change initiatives, planning, and facilitation
- Bachelor’s Degree in Engineering or related Technical field is strongly preferred
- Minimum of 1-5 years of related leadership experience in a Manufacturing environment is required
- Experience implementing and maintaining TPM Systems is strongly preferred
- Understanding of mechanical, electrical, pneumatic, hydraulic, and utility systems including ammonia refrigeration and boiler systems is a plus
- Must have the knowledge of good manufacturing practices. Be safety and quality minded and have the ability to make sound decisions
- Experience using, trouble-shooting and programming Allen Bradley PLCs is a plus
134
Maintenance Supervisor Resume Examples & Samples
- Provide leadership, technical support and coaching to unionized hourly trades and peers while developing and maintaining positive employee relations
- Collaborate with Production personnel to ensure maximum uptime of production line equipment
- Plan and control expenditures in accordance with the operating budget of the department
- Assist with implementation of capital and Six Sigma projects
- Ensure that equipment and facility comply with all EHS, food safety, and regulatory requirements
- Possess a Mechanical or Industrial license
- Experience working in a unionized industrial environment
- Knowledge of industry safety, food safety, and environmental regulations and requirements
- Excellent computer skills, including Excel and strong communication skills, both written and oral
- Ability and willingness to be "hands on" to perform any maintenance task as required
- Must be legally entitled to for Cargill in Canada
135
Maintenance Supervisor Resume Examples & Samples
- Conducting safety meetings for the craftsmen and technicians at specified intervals
- Distributing and reviewing Job Safety Analysis (JSAs) at the job site and verifying that all permits are satisfied
- Reinforcing safety practices on a daily basis
- Supervising departmental safety and housekeeping practices and maintain a constant alert for hazardous conditions
- Ensuring compliance with applicable laws and regulations issued by OSHA, EPA, and other federal, state, and local regulatory agencies
- Maintaining total awareness to all plant policies, regulations, and procedures, and ensures proper adherence to them with respect to all operations
- Responding to employee injuries by investigating accident causes and recommending means to prevent accident reoccurrence
- Reinforcing quality in maintenance processes and ensure that all employees follow established guidelines
- Increasing yields by working individually or on teams to resolve problems
- Looking for continuous improvement opportunities to reduce cycle time and/or cost and improving on-time delivery
- Planning, supervising, directing and engaging in daily production operations and anticipate problems, (i.e. material shortages, equipment malfunctions, rush orders, etc.) such that loss of work hours is minimized and production and quality objectives are achieved
- Utilizing skills, work hours, materials, and work flow to achieve production
- Planning, executing, and allocating of resources for all priority work (i.e., handling the daily, firefighting)
- Collecting, auditing, and submitting completed shop papers and job history
- Associates Degree in an Electrical Technology or High School Diploma/GED with 5 Years Equivalent Electrical/Mechanical/Instrument Experience
- 3 years of maintenance experience in an industrial environment
- 2 years of maintenance leadership experience
- BS Degree in Technical / Engineering Technology
- 3 or more years of Electrical and Instrumentation maintenance leadership experience preferred
- Experience working in a union environment strongly preferred
- Proficient in s software such as SAP preferred
- Six Sigma certification preferred
- Knowledge, Skills, and Abilities in lean tools preferred
- Strong leadership skills preferred
- Demonstrated ability to work effectively with individuals at all levels of an organization
- Demonstrated ability to use influencing skills to accomplish goals and objectives
- High degree of initiative is required as well as ability to respond quickly, effectively and accurately to employee and production issues
- Ability to establish/build relationships with peers, subordinates, and internal customers
- Ability to balance multiple and changing production requirements and to make sound business decisions using facts and good judgment
- Knowledgeable in repair techniques for a broad array of mechanical applications
- Strong computer skills such as: SAP, Microsoft office: Word, Excel, Outlook
136
Maintenance Supervisor Resume Examples & Samples
- HS Diploma or GED equivalent from an accredited institution
- Minimum of 3 years of previous maintenance supervisory experience in a heavy manufacturing environment
- Minimum of 1 years of experience in a unionized work environment
- A technical college degree from an accredited institution (Associate's degree) in electrical engineering, mechanical engineering, etc. OR journeyman certification
- Experience with forging equipment and CNCs
137
Maintenance Supervisor Resume Examples & Samples
- Responsible for maintaining a safe and secure work environment. This includes correcting unsafe acts/conditions, performing monthly safety inspections, evaluating machine guarding and investigating accidents, as required
- Supervises and coordinates the employees and activities of the maintenance department to ensure safety, productivity, and housekeeping standards are met or exceeded
- Coordinates and applies preventative/productive/corrective maintenance techniques toward monitoring and reducing maintenance and repair costs. Uses Total Predictive Maintenance (TPM) and Equipment Reliability initiatives to improve uptime and lower repair costs
- Maintains machine and maintenance records
- Responsible for monitoring critical spare machine parts and maintenance supplies for equipment as needed to maintain their good working order and reliability. Maintains an orderly storeroom
- Evaluates machinery to ensure compliance with established quality and maintenance standards
- Develops a predictable/preventive maintenance program related to all equipment to insure 100% availability
- Responsible for meeting budget (labor, expenses)
- Accesses, inputs, and retrieves information from the computer including computer maintenance management systems
- Assures and maintains safe and healthful working conditions while enforcing safety rules and regulations
138
Maintenance Supervisor Resume Examples & Samples
- The successful applicant is an effective communicator
- Curious about the customer’s business and always striving to exceed their expectations
- He is able to turn strategy into objectives and actions and contribute to the overall KONE business
- Leadership experience and is capable of providing support to and inspiring and energizing his team
- Technical understanding, good IT skills and knowledge of local business practices
- Must be an Engineering Graduate preferably in the field of Electrical
- At least 2 years supervisory experience
139
Maintenance Supervisor Resume Examples & Samples
- 3+ years supervisory experience, preferably in a manufacturing environment
- This position is subject to the International Traffic in Arms Regulations (ITAR) which requires U.S. person status
- Must be able to read blueprint
- Experience with TPM, Synchronous Mfg, and Kaizen Concepts
- Must be able to communicate effectively with all levels of the organization, have good team building skills, excellent people skills; ability to handle multiple tasks, technically oriented
- Must be energetic and a self-starter, able to promote and implement change, have good PC skills, good telephone skills, strong organizational skills, and ability to promote a continuous improvement atmosphere
140
Maintenance Supervisor Resume Examples & Samples
- Supervises, plans and organizes preventative maintenance and repair of all electrical, HVAC and Material Handling Systems and
- Schedules, plans and completes all approved work requests by engineering and operating departments via the work order system
- Monitors and controls payroll and maintenance materials expense to stay within planned and key budgets
- Works with suppliers and other non-Company personnel involved with the maintenance department
- Works with engineers, supervisors and managers of the facility and remote facilities
- Member of various teams and committees involving safety, quality, energy management, recycling and emergency response
- Assists in training Associates from operating areas involving correct use of materials, handling systems and equipment
141
Maintenance Supervisor m-th Resume Examples & Samples
- Direct, coordinate, and review the schedule of construction crews, and/or multiple trades in the installation, repair and alteration of campus buildings, grounds, equipment, utilities and other facilities. Read plans and blueprints. Determine scope of work, materials needed, their availability and estimated costs, and ensure compliance with applicable standards and codes
- Conduct regular project site visits. Monitor work to ensure that all work requests meet expected quality and productivity expectations, established safety standards, and that crews follow FMC customer communication expectations and internal work order system protocols. Ensure work orders are on schedule, within budget and that all work order financial documentation is accurate and up-to-date. Routinely provide work status, cost, and schedule information and follow up as necessary with customers
- Monitor and utilize productivity reports to ensure efficient use of resources. Provide feedback to the Assistant Director for Construction
- Procure, distribute and account for equipment, tools and supplies necessary for an efficient and effective construction operation
- Experience implementing process improvement initiatives
- Experience/proficiency with a computerized maintenance management system
- Experience in the maintenance, repair and/or alterations for technically complex and sophisticated buildings in an institutional or commercial setting. Experience should include operation in a multi-trade system, personnel supervision, fiscal management, computer applications for maintenance management, database management, and technical report writing
- Experience designing a hierarchal key system for a new building incorporating levels of security as required for a diverse security environment. Working with a computerized key control system that
- Demonstrated proficiency with standard productivity software including Microsoft Office Suite or equivalent products
142
Maintenance Supervisor Resume Examples & Samples
- Massachusetts Masters Electrician License
- 6 years of supervisory or project leadership experience
- Experience with State of Massachusetts and National Building codes
- Candidate should have strong interpersonal and organizational skills and be capable of communicating with customers both orally and in writing
- Prior experience in the development of new concepts, techniques and standards as well as experience in developing solutions to complex problems
- Experience consulting with management on building maintenance and construction issues
- Good computer skills and working knowledge of Microsoft Office, Excel, Microsoft Projects, Maximo, Building Management Systems and Autocad
- BS Degree in Electrical or Mechanical Engineering or a related technical major
- AS in Electrical or Mechanical Engineering or a related technical major plus 10 years applicable professional experience
- 14+ years applicable professional experience in Electrical or Mechanical engineering or in a related field in lieu of a BS
143
Maintenance Supervisor Resume Examples & Samples
- Fully manage Vendor contracts as required Management Support
- Assist in addressing any and all issues/problems that may still be active
- Assist Maintenance, Housekeeping and Fleet Management personnel with daily operations
- On site coverage during weekend Production
- Communicate regularly with building occupants regarding status of projects. Follow up to make sure work is completed satisfactorily and on time
- Provide necessary coverage for Managers on all shifts and weekends for training and vacation coverage, or as required
- Meet regularly with Site and/or General Managers regarding outstanding issues. Add input/insight on upcoming projects and conditions
- Investigate, plan, manage, and implement projects given by the General Manager, when not backfilling
- Perform safe operating tours to ensure proper operation
- Solve building operational issues, including the supervision of outside contractors/vendors General Housekeeping
- Assist with the completion of CCA inspections
- Order HK supplies as necessary
- Assist HK manager with projects that are out of scope
- Cover HK Manager as needed
- Team Safety Tours Industrial Cleaning
- Assist in planning of Body Shop Cell cleaning
- Manufacturing process pit cleaning
- Sludge System Cleaning
- Dry-Ice Blasting
- Ultra-High Pressure Water Blasting Mechanical Systems
- HVAC/R (Heating, Ventilating, Air conditioning and Refrigeration)
144
Maintenance Supervisor Resume Examples & Samples
- Minimum 2+ years in Maintenance Management experience
- Have a strong technical aptitude
- Demonstrated capability to successfully partner with peers and senior business leaders
- Self motivated, results oriented with focus on continuous improvement
145
Maintenance Supervisor Resume Examples & Samples
- Associates Degree in a Mechanical Technology or High School Diploma/GED with 5 Years Equivalent Mechanical/Millwright Experience
- 3 or more years of maintenance leadership experience preferred
- Proficient in software such as SAP preferred
146
Maintenance Supervisor Resume Examples & Samples
- Follow Roche Values to assure people well-being by dedicating a significant part of the time to leading people
- Supervise the work of a group of employees who are engaged in the maintenance and repair of an assigned process. Plan and establish work schedules and assignments to meet uptime goals of equipment and machinery. Is also accountable for verifying, monitoring, and confirming accuracy of the direct reports attendance and punctuality in the timecard system
- Accountable of periodically carrying out Performance Management dialogs with employees under the direct supervisory scope
- Develop employees and recommend changes in the status of his/her team ensuring compliance with human resources policies and processes established in the organization, and Affirmative Action and Equal Employment Opportunity laws, ensuring an environment free from harassment
- Responsible for facilitating and promoting the Innovation and Lean Methodology initiatives by motivating employees and deploying such activities throughout the maintenance organization
- Accountable for identifying cost impact due to spare parts utilization and labor hours required for maintenance related activities
- Monitoring of Overall Equipment Efficiency (OEE) and initiating machines performance improvement through a well-established set of metrics
- Establish strategies to reduce downtime to increase machinery output by implementing RCM principles and change over reduction programs
- Must analyze opportunities trending, such as downtime analysis, parts consumption and labor incurred during Preventive, Corrective, and Predictive Maintenance activities
147
Maintenance Supervisor Resume Examples & Samples
- 2+ years of maintenance supervisory/leadership experience in a manufacturing or industrial environment
- Familiarity with Programmable Logic Controllers (PLC’s), Robotics, Electrical Circuits, Pneumatics and Hydraulics
- Ability to read electrical/hydraulic schematics, troubleshoot motor control circuits and teach robotics is preferred
- Competent in basic troubleshooting and standard repair methods
- Must be willing to work off-shift and weekend shift-HS diploma or equivalent
148
Maintenance Supervisor Resume Examples & Samples
- The associate must regularly lift and/or move and push and/or pull up to 10 pounds, frequently lift and/or move and push and/or pull up to50 pounds, and frequently position and/or reposition oneself in accommodation
- While performing the duties of this job, the associate is regularly required to stand, walk, climb stairs, use hands to finger, and handle or feel objects, tools or controls. The associate is frequently required to talk and/or hear. The associate is occasionally required to reach with hands and arms, stoop, kneel, crouch or crawl, and climb a ladder or step stool
- Occasionally required to walk, stand, stoop, climb, or balance
- Coordinated use of hands and fingers to grasp, feel objects, transfer small items from one hand to another, fine manipulation, and bilateral reach with arms. Use of close vision, depth perception and ability to adjust focus
- Essential Vision Functions: While performing the duties of this job, the associate must have the ability of close vision, peripheral vision, depth perception, and the ability to adjust focus. The associate must be able to wear protective safety glasses and/or face shields as necessary
- Professionalism: Acts in a reasonable and rational manner at all times and especially in an urgent situation. Demonstrates respect for superiors, co-workers and customers and visitors. Demonstrates honestly, integrity and maturity. Excellent Interpersonal and organizational skills
- Rigor/Self-Discipline: Self-motivated. Communicates clearly and effectively to others. Clearly understands the rationale for why processes must follow certain steps. Can identify multiple projects and prioritize them in order to meet deadlines. Highly results oriented with a demonstrated experience of balancing multiple tasks and priorities
- Teamwork: Can take exiting information and align others effectively within the company to achieve desired results. Participates and/or leads in team problem solving process. Contributes knowledge and information to assist the team and prompts others to do so. Assists in keeping the team focused and on track and resolves any interpersonal issues arising that may jeopardize team success. Commitment
- Makes a commitment to oneself and to assist others in learning new skills and processes as well as being efficient and productive while performing job duties
- Applicant must be self-motivated, detail-oriented and possess the ability to work well with others under pressure
- College degree in Industrial Technology or Maintenance and/or 5-7 years related maintenance
- Millwright or electrical licensing is a plus
- Experience: A minimum of five (5) to seven (7) years’ experience working in a capacity demonstrating the requirements of this job as listed here. Experience in the maintenance and/or operation of a process manufacturing facility or equivalent combination of education and experience will be considered in lieu of education requirement. In-depth knowledge of optical industry and ophthalmic manufacturing equipment preferred. Experience with repairs and maintenance of eyeglass fabrication equipment. Knowledge of mechanical, pneumatic, hydraulic and electrical equipment. Strong written and verbal communication skills, excellent interpersonal and organizational skills
149
Maintenance Supervisor Resume Examples & Samples
- Single point accountable for maintenance daily activities of production crews, providing their tools and materials
- Perform front line trouble shooting activities on equipment
- Direct the safety awareness program for the workforce and manage safe work performance, maintaining housekeeping and assisting the Production team in area safety analysis
- Coordinating PM and other outage activities on equipment
- Planning the daily activities of maintenance crews, providing the tools, materials and technical direction for the normal maintenance, preventative maintenance and the capital work
- Perform root cause analysis and “5-why” techniques with the goal to eliminate maintenance downtime and waste. Implement corrective actions to meet goals
- Working with Engineering on the repetitive maintenance problems to continuously improve the reliability of the equipment and facilities
- Coordinate and manage the development of work procedures and standard practices
- Drive continuous improvement activities to eliminate all waste, especially as related to maintenance downtime, safety, work practices and employee involvement
- Minimum 5 years of maintenance supervisory and/or management experience
- Associates or Bachelors Degree, preferably engineering or business
- Experience in the areas of hydraulics, robotics, PLC
- Maintenance supervisory experience in an industrial manufacturing environment
- Management of people experience
- Vaccum casting technical knowledge
150
Maintenance Supervisor Resume Examples & Samples
- Drive root cause analysis to maximize equipment availability
- Salary + Paid Vacation/Benefits
- 2nd shift (1pm start time)
- Background in Maintenance
- Experience in the Food, Beverage, Pharmaceutical, Automotive, Chemical, or Petroleum industry
151
Quality Maintenance Supervisor, APS Resume Examples & Samples
- Communication and customer satisfaction skills
- Leadership skills and experience
- Continuous improvement skills and experience
- ISO 9001:2008 Auditing / Process Improvement
- Bachelor's degree in Business Administration or related technical training, and 3 years of experience
- In lieu of formal education, at least 11 years of progressive related experience
- Must obtain and maintain local base access
152
Maintenance Supervisor / Engineer Resume Examples & Samples
- Manage the Greensboro maintenance operating costs by implementing projects and maintenance so they accomplish their stated objectives within budget and on schedule
- Develop long-term maintenance planning goals, but must also possess the flexibility for immediate troubleshooting to avoid shutdowns
- Plan, schedule and direct the preventative maintenance involving all production equipment and overseeing and scheduling contract maintenance on HVAC chillers, air compressors and all other support equipment necessary to maintain the plant
- Ensure maintenance services are in compliance with the health and environmental regulatory requirements and that all maintenance personal are in compliance with Corporate, State and Federal regulations
- Prepare, plan and coordinate capital and extraordinary expense authorizations
- Determine use of outside engineering and contracting companies the activities and training of service agencies and outside contractors providing services to the plant to assure economical and effective performance
- Manage Greensboro MRO inventory and spending by monitoring patterns and usage with the MRO clerk on a continuous basis
- Contribute to the effectiveness of maintenance by developing new plans and techniques to improve efficiency
- Provide a safe working environment in the plant through effective procedures, designs, work practices and provide for protective systems and equipment complying with government laws and codes
- Responsible for a variety of auxiliary plant services including fire alarm systems, janitorial service, tow-motor service, snow removal, and blanket maintenance contracts
- Actively participate in cost control efforts by analyzing various plant services and utilities to conserve consumption and reduce wastes
- Participates in all projects related to safety and health by assisting in problem identification and recommending solutions to these problems
- Bachelor’s Degree in an engineering or technical discipline
- At least five (5) years of supervisory maintenance experience in a manufacturing environment
- Strong attention to detail with the ability to work under pressure and be able to function effectively with all level of employees
- Excellent communication skills in dealing with outsiders, peers, superiors and subordinates
- Understanding of the principles and applications associated with manufacturing operations, maintenance and engineering
- Excellent interpersonal communication and listening ability
- Ability to work with teams and lead decision-making processes in a team environment
- Demonstrated mechanical, analytical, problem-solving, organizational and planning skills
- Demonstrated functional electrical and process controls knowledge
- Strong computer skills including the ability to prepare spreadsheets and use Microsoft Office Products (Word, Excel, Power Point and/or Access) to analyze data and trends
- Effective use and knowledge of CMMS
153
Maintenance Supervisor Resume Examples & Samples
- Communicate with owners, vendors and other department regarding work order updates, explaining company processes and procedures
- Safeguard all supplies, equipment and tools including inventory control and ordering supplies, tools and equipment
- Responsible for keeping the maintenance shop and vehicles clean, organized and in safe condition
- Accountable for the daily operation of the department when the Maintenance Manager is absent
- Perform all duties and tasks in the Maintenance department, including field work when necessary
- Be on call and respond to after hour calls when assigned
154
E&i Maintenance Supervisor Resume Examples & Samples
- 8+ yrs. equivalent electrical work experience
- 4+ yrs. supervisory/management experience in an industrial/manufacturing environment
- Proficient use of Microsoft Office with ability to learn a computerized maintenance management system
- Associates Degree in Industrial Electricity or Bachelors degree in Electrical Engineering
155
Maintenance Supervisor Resume Examples & Samples
- Test Cell equipment maintenance
- Test Cell instrumentation
- Test Cell utility maintenance
- Spare management - Identify, Procure & stock necessary spares. Identify supplier source. Commit to reduce the maintenance cost
- Preventive & Predictive maintenance – Execute, update & monitor effectiveness. Update Machine History
- SOPs - Writes practices and procedures for maintenance related activities and provides a source of expertise in areas that are necessary in completion of objectives
- Regulations, system, standard & process - Compliance i.e CPS, TPM, EOHS, ISO. Adheres to established standards, policies and practices relating to quality, cost reduction, safety, ergonomics
- Cost - Expenditures. Planning, Monitoring & Reporting
156
Maintenance Supervisor Resume Examples & Samples
- Engine assembly equipment maintenance
- Engine assembly instrumentation, control, logic, PLC
- Provides miscellaneous administrative support including reporting, manpower data, and timekeeping
157
Maintenance Supervisor Resume Examples & Samples
- Engineering graduate, electrical or mechanical engineering
- 5-10 years in plant maintenance and production management
- Maintenance management in foreign firms is a must
- Production management of feed mill or FMCG with lean manufacturing approach is advantage
- Good at leadership, strong communication skills and able to communicate with all levels in the plant
- Proficiency in Microsoft Office (word, excel, power point)
- Writing and Reading English at intermediate level is a preferable
158
Maintenance Supervisor Resume Examples & Samples
- Maintain timelines and work schedule in accordance with the preventive maintenance program
- Minimum three years of experience in the facilities management of related properties or other comparable business
- Must have extensive working knowledge of building systems to include but not limited to; HVAC, electrical, plumbing, refrigeration, roofs, building finishes, mechanical operations, energy management and Preventative Maintenance Programs
- Must have a valid Driver’s License
159
Maintenance Supervisor Resume Examples & Samples
- Prioritizes and assigns service requests to maintenance team. Monitors completion of service requests and follows up on any outstanding items. May assist in the completion of service requests as necessary. Handles all escalated general maintenance requests in a timely manner
- High school diploma, or equivalent
- Ability to meet and deal tactfully, professionally and courteously with students, staff, and general maintenance staff
160
Maintenance Supervisor Resume Examples & Samples
- A minimum of a BS Degree in Mechanical Engineering, Electrical Engineering or a related discipline plus 6 years of related experience OR an MS in a similar field plus 3 years of related experience is required
- A minimum of 3 years of comprehension of manufacturing processes and equipment is required
- Demonstrated good verbal and written skills, and proven analytical ability is required
- Excellent problem-solving skills are required
- Leadership capability is required
- Stay abreast of industry trends, best practices and new technologies
- Results and action oriented
- Ability to deliver tangible benefits to the business is preferred
- Customer and quality focused
- Technical knowledge of packaging and manufacturing equipment is preferred
- Proficiency with data collection tools (ex. oscilloscope, data logger, etc.) is preferred
- Ability to motivate, lead, guide and direct Technical Associates is preferred
- This position is based in Lancaster, PA and may require up to 10% travel both domestic and international.Engineering (Generalist)
161
Maintenance Supervisor Resume Examples & Samples
- Supervise and direct the activities of both skilled and non-skilled employees on the shift, including vehicle mechanics, maintenance mechanics, electricians, machinists and stores attendants
- Maintain current working knowledge of state and federal environmental regulations and Volvo corporate environmental requirements, including but not limited to the RCRA-Resource Conservation and Recovery Act (relating to management of hazardous waste), CAA-Clean Air Act (as it relates to maintaining equipment and processes that are regulated by the air permit), Storm Water Pollution Prevention Plan (as it relates to storm water drains and runoff to local waterways), US-DOT Department of Transportation ( as it relates to shipping waste or chemicals), and the OSHA 8-hour HAZWOPER requirements (as it relates to the communications and actions require for responding to spill emergencies). The advisor will assure that he/she and all direct reports performing related duties governed by these regulations shall receive initial and scheduled refresher training as described in the ISO-14001 EMS training matrix and perform their duties in accordance with that training
- For the Emergency Coordinator and Alternate Emergency Coordinator identified in the Contingency Plan, be prepared to perform the duties of the RCRA Emergency Coordinator during an environmental emergency
- Is responsible for all administrative duties such as vacation scheduling, training, OSHA compliance, team activities, discipline and PM program
- Works closely with the Industrial Engineering function as well as the CMMS Administrator to insure that all work is procedurally correct and documented
- Responsible for formulating technical solutions to maintenance problems. Must understand and follow all plant standards regarding facility and equipment
- Must be extremely responsive to the needs of the production process and be a partner in that process
- Communicating employee feedback on the NRV statement on the environment
- Communicating procedures and work instructions pertaining to their respective area
- Five years experience in supervision, preferably maintenance related
- Good knowledge of industrial plant systems, maintenance inventory systems, electricity, general mechanical techniques and prints
- Should have knowledge of OSHA standards
- Must be computer literate (Be able to keyboard and use typical generic and maintenance specific software)
162
Maintenance Supervisor Resume Examples & Samples
- Bachelors Degree in Mechanical or Electrical Engineering
- Willing to work 12-hour rotating shift schedule
- Ability to coordinate with other departments and managers
- Ability to work effectively and communicate across multiple levels
- Demonstrated success in measuring and improving processes to meet organization goals
- Proficiency using MS Office applications, including Word, Excel and PowerPoint
- As part of our total compensation philosophy, Guardian offers a competitive base salary, bonuses and a wide variety of benefits including health/dental/life insurance, prescription coverage, STD & optional LTD, paid vacation and holidays, 401(k) with a $1 for $1 match up to 7% and future opportunities for advancement
- For more information about Guardian, visit us at www.guardian.com
- Guardian is an Equal Opportunity Employer
163
Maintenance Supervisor Resume Examples & Samples
- Utilizes Productivity Improvement Plan process to identify areas for improvement and assists Maintenance Manager in development of a measurement system
- May review inbound and outbound S&OP reports and assists in department planning; makes adjustments based on distribution center needs
- Plans daily production goals for department
- Identifies obstacles to performance through floor observations
- Reviews daily staffing plan of department/shift with Maintenance Manager; determines proper staffing level for shift or area of responsibility based on receiving/shipping volume and departmental projects
- Establishes work schedules based on preventative maintenance requirements
- Conducts required sortation audits and analyzes results to determine appropriate system and/or personnel adjustments
- Ensures that adequate training is provided for all maintenance department employees
- In coordination with safety committee, supports safety programs to reduce employee injuries
- Partners with Maintenance Manager and Human Resources to ensure OSHA compliance; serves a back-up contact person for governmental agencies
- Maintains status reports on building and facility insurance documentation
- Assists Maintenance Manager with department budget
- Analytical skills and strong attention to detail
- Ability to read blueprints, electrical, mechanical, and voice and data communication drawings, and various diagrams
- Understanding of systems such as conveyor, sort view and graphical monitors
- Working knowledge of fire protection systems
- Comprehension of conveyor system sortation reports, fire protection and security alarm reports, capital variance reports, and OSHA logs
- Computer skills: Word, Excel, autocad systems, and programmable logic controllers
- Maintenance experience required
- Experience in an automated retail distribution center preferred
- Two years minimum supervisory experience
- Automated retail distribution center experience preferred
- Vocational skills training as a tradesperson (mechanical, electrical, welding, hydraulic, pneumatics)
164
Maintenance Supervisor Resume Examples & Samples
- Responsiveness
- Discretion
- A thorough and methodical approach
- Ability to identify problems
165
Maintenance Supervisor Resume Examples & Samples
- 50 %Supervision of crafts persons, performance management and skill enhancement process
- 25% Lead, supervise and coordinate daily proactive, reactive and modifications work type and management of formal work flow system
- 10% Responsible for development and management of budget
- 5% Complete all Environmental, Health & Safety responsibilities
- 5% Cause Analysis investigation and action tracking
- 5% Participate in Corporate and BU taskforces, as necessary, and any other duties as assigned
- Bachelor’s degree or higher OR 5+ years of maintenance experience
- 2+ years of experience utilizing maintenance/reliability strategies (TPM, RCM, etc.) and related tools/metrics
- Ability to develop and manage good working relationships with internal departments (production, sales, logistics, accounting), contractors, suppliers, inspectors and customers
- Ability to take off-hour calls and rotate on call accountability with facility staff as necessary
- Ability to apply Cargill's policies and procedures in the areas of safety, environmental, and food/feed safety
- Strong organizational, written and verbal communication skills
- Ability to speak candidly and provide constructive feedback
- Ability to make independent decisions
- Experience leading, developing, and engaging hourly work force
166
Maintenance Supervisor Resume Examples & Samples
- Manages and oversees the repair and maintenance of equipment; assigns work orders, ensuring safety and production related work orders are highest priority. Assists maintenance associates with diagnosis and repairs when necessary
- Manages preventive maintenance programs and ensures schedule is adhered to in order to minimize downtime
- Obtains and reviews contractor bids for repairs; determines appropriate contractor and hires same, ensures contractors adheres to quality, scheduling, budgetary guidelines standards
- Manages the development, implementation and administration of operational policies, programs and systems within functional area. Establishes methods and procedures for departmental work activities; identifies and resolves operational problems; and communicates expertise and approval concerning departmental activities
- Hires, orients, trains, evaluates, and develops associates. When necessary carries out disciplinary actions or recommends termination of employment
- Reviews, recommends and implements additions, modifications and improvements to facility systems
- Oversees and ensures buildings, grounds and equipment are cleaned and maintained in order to maintain machinery and physical plan. Manages and oversees facility’s waste disposal program; ensures waste is disposed of according to appropriate regulations
- Interacts with facility management to ensure maintenance needs are met. Touring facilities to ensure the conditions of the facilities are maintained
- Flexibility to work variable shifts. -Helps determine staffing needs for optimum department operations
- In conjunction with the Maintenance Manager, carries out disciplinary actions as appropriate
- Good knowledge of distribution center practices and procedures
- Analytical ability necessary to gather and interpret data, and develop, recommend, implement solutions
- Requires walking, standing, stooping, climbing stairs, bending and reaching to do the job
- Strong management leadership, communication, organization and administrative skills
167
Maintenance Supervisor Resume Examples & Samples
- 25% Reliability Excellence Governence
- Responsible for aligning, deploying and executing CCNA reliability excellence vision and strategy, as well as direct program administration at the Hazleton site
- Promote a culture at the Hazleton site that builds, operates and maintains the facility in an operationally sound, safe and reliable manner
- Implement leading reliability excellence practices and aggressively raise the performance of underperforminng departments by monitoring KPIs (safety metrics, plant yield, utility usage)
- Support the deployment and continuous improvement of Reliability Excellence processes and ensure the reliability culture is foundational to operations. Enforce common reliability processes and metrics, with focus on eliminating the root causes of becoming a reliable facility, to achieve targeted results from continuous improvement practices, and validate the importance of Reliability through key successes
- Partner with Reliability Excellence COEs to identify, deploy and leverage opportunities for continuous improvements applicable to the Hazleton site and overall BU
- 25% Operational Effectiveness, Continuous Improvement, Prevent, Maintain, Repair
- Manage the execution of preventative maintenance and reliability activities at the Hazleton site. Partner with other departments, contractors, subject matter experts, community and local regulators to ensure asset health and availability
- Supervise, monitor and review ongoing maintenance activities and records to ensure asset health and compliance to guidelines, codes, regulations and requirements
- Supervise the execution of repair procedures and tasks to ensure compliance with the Hazleton equipment maintenance strategies
- Monitor repair through the CMMS to ensure work orders and requests are executed in accordance to the established work flow
- Provide input, reviews and analyzes maintenance/ reliability metrics and performance to help drive continuous improvement
- 25% People/ Budget Management
- Responsible for the Hazleton site maintenance department personnel management including recruiting, retention, development and engagement of the team
- Responsible for scheduling and delegation of maintenance activates for the Hazleton maintenance department and third party maintenance contractors
- Establish and manage overall department budget and responsible for cost control of repairs, labor and supplies
- 15% Best Practice Applications, Training & Support
- Hazleton site Process Safety Management (PSM) leader specific to Ammonia system
- Ensure best practices are employed for utility systems (electric, water, and natural gas)
- Develop, maintain and apply consistent maintenance and reliability best practices
- Stay knowledgeable and remain responsible for understanding latest innovations, technology and trends for maintenance and reliability practices
- Identify training opportunities/ needs and facilitate training sessions for maintenance personnel, focusing on skills training and development, safety practices and work standards
- Provide ad-hoc technical support as needed
- Support operations by analyzing and developing conclusions in regards to failures, downtime and lost production, and identify opportunities to improve operator reliability and/or determines acceptable risk tolerance for assets
- Member of Hazleton site Food Safety Team
- 10% Project Planning, Contractor Management
- Manage ongoing maintenance/ reliability related projects utilizing a broad knowledge of maintenance and reliability practices and procedures
- Manage projects scope, planning, cost estimation and payback justifications
- Recommend selection of contractors and manage the relationship to ensure performance expectations are met
- Routine physical activity including standing and walking for several hours at a time, typing, climbing, and lifting approximately 55 lbs
- Technical Bachelor’s Degree or High School diploma/GED and a minimum 5 years production or maintenance experience in lieu of degree
- At least 5 years of combined experience in production supervision, maintenance or project management
- At least Minimum of 2 years maintenance experience
- Mechanical aptitude and ability to learn knowledge of hydraulics, conveyors, dust collection systems and power trains
- Demonstrated team building, leadership and conflict resolution skills
- Demonstrated ability to lead people and get results through others
168
Maintenance Supervisor Resume Examples & Samples
- Lead the Quality Cost & Delivery (QCD) Performance for designated groups
- Direct QCD initiatives: set targets, implement plans, track daily results, make appropriate adjustments in resource planning in order to attain desired results
- Drive actions for improvement: communicate with the Production and support functions to ensure a transparent information flow, collaborate to define improvement areas and precise action plans
- Manage team performance: know team problems, define areas for performance improvements with team members, drive teamwork, lead problem solving groups, lead workshops on quality improvement methods (5S, TPM, SMED, GMAO, QRCI…)
- Ensure that working conditions are fully compliant with Group HSE standards
- Associate's degree in engineering/Diploma, with a specialisation in Maintenance
- 1-3 years of industrial experience
- Team Player
169
Maintenance Supervisor Resume Examples & Samples
- Manage facility activities and support all maintenance personnel
- Maintain effective communication and coordination with all internal customers, plant management and team members; Maintain positive team member relations
- Follow the principles of the Magna Employee Charter
- Promote and practice “safety first” by immediately addressing any hazards, defective equipment or unsafe conditions
- Support Maintenance team members on all three shifts in safe, quality-minded and productive manner with a sense of urgency to attain production priorities as scheduled
- Maintain effective department communications through a prioritized work list, plant meetings, daily meetings, and weekly department meetings
- Maintain and continuously improve department organization and housekeeping standards
- Determine, achieve and improve productivity, quality, environmental, health and safety goals
- Support new program launches
- Provide motivation and a results-oriented environment
- Review all major department projects from start to finish to insure proper techniques are being used
- Report on status of departmental projects as required
- Assure that preventative maintenance is identified, executed, documented and tracked
- Interface with maintenance vendors and material suppliers to insure purchase of proper materials
- Utilize lessons-learned philosophy in continuous improvement activities
- Complete correspondence, forms and reports in Microsoft Office and other required programs
- Encourage safety and housekeeping practices and lead by example
- Promote and facilitate Open Door Process without reprisal, effective communication and Fair Treatment
- Participate in Continual Improvement activities
- Able to demonstrate understanding of how job performance affects product quality and customer satisfactions
- Able to effectively present information and respond to questions from management, team members, suppliers and customers
- Able to work flexible hours as needed
- Able to use computer software as required
- Must have a positive attitude
- Excellent equipment diagnostic skills
- Associates Degree or 5 years of experience in the maintenance field preferred
170
Maintenance Supervisor Resume Examples & Samples
- 2+ years experience in supervising an industrial maintenance crew
- 5+ years experience working in industrial maintenance
- 5+ years experience in supervising an industrial maintenance crew
- 10+ years experience working in industrial maintenance
171
Maintenance Supervisor Resume Examples & Samples
- Direct activities of the maintenance and AST professionals, supporting optimized machine availability
- Identify training needs and team development
- Manage time and attendance using Kronos payroll system
- Drive preventative maintenance and predictive maintenance functions, continuously improving machine availability
- Support TPM functions and be a primary leader for implementation
- Determine root cause, and implement corrective and preventative actions, regarding machine downtime
- Assist in machine downtime issues including troubleshooting and resource allocation
- Support manufacturing operations
- Lead and improve reliability centered maintenance
- Drive equipment safety improvements
- Implement lean and six sigma methodologies
- Schedule preventative maintenance and general maintenance work orders, ensuring high on- time attainment
- Identify and maintain MRO/critical equipment supplies
- Manage projects associated with continuous improvement on processes, machines, and plant maintenance
- Drive plant maintenance activities
- Champion company safety and overall rules
- 5 plus years of supervision experience, maintenance preferred
- Prior experience in implementation and/or sustainment of preventative and predictive maintenance systems
- Associate degree in mechanical, electrical, or related discipline
- BS degree in Mechanical or Manufacturing Engineering, a plus
- Computer skills that include word, excel, PowerPoint
- Experience with computer maintenance management systems preferred
- Mechanical abilities to be able to trouble shoot machine/equipment downtime issues
- Electrical knowledge for troubleshooting and maintaining, PLCs, servos, photo eyes, and relays
- Demonstrated communication and leadership skill
- Excellent and effective problem solving, listening, and verbal communication skills
172
Maintenance Supervisor Resume Examples & Samples
- Responsible for the safety of all employees under the supervision of this role, and those that may be impacted by the actions of the maintenance team
- Ensure safety procedures such as RA/MS, WAH, Confined space, Hot work and other work permits are adhered to
- Lead the maintenance team to ensure maximum machine availability for production
- Lead employee development initiatives within the maintenance department
- Lead continuous improvement projects in the maintenance area
- Review all SAP notifications daily
- Raise work orders on SAP
- Plan and schedule maintenance work (electrical and mechanical)
- Prepare method statements/risk assessments for planned work as required
- Plan work for and with Contractors and Supervising same on site
- Prepare spares and other items for each job
- Ensure all parts are correctly booked out of stores and the process is adhered to
- Liaise with buyer to ensure availability of critical spares
- Assist with planning and preparations for project related work
- Prepare maintenance plans, set up and periodic review PPM Basic Data in SAP
- Critic maintenance plans and overall PM processes
- Complete and review break down analysis
173
Maintenance Supervisor Resume Examples & Samples
- General Housekeeping Personnel General Housekeeping
- Restroom Sanitation
- Floor Care
- General and Medical Waste Disposal
- General Maintenance
- Medical Facility & First Aid
- Spill Response
- Cardboard and Pallet Recycling Understanding of Mechanical Systems
- HVAC/R (Heating, Ventilating, Air conditioning and Refrigeration): Indoor Air Quality ,Temperature Control
- Building Exhaust Systems
- Preventative Maintenance (Scheduled maintenance to prevent break down)
- Elevator Maintenance
- Backflow Preventers
- Natural Gas, Water, Sewer, and Electric Utility Meter Verification Understanding of Power Systems
- Normal power: Electrical Substations o Switchgear
- Emergency power systems o Uninterruptible power supply (UPS) systems: Standby generators
- Building Automation Systems
- Building Monitoring systems
- Data Centers
- Security and Locks
- Building Utility & Piping Systems
- Energy Conservation Understanding of Life/Safety Systems
- Fire Sprinkler systems
- Smoke/fire detection systems
- Fire Extinguishers
- Signage
- Evacuation Plans Understanding of Environmental Health & Safety
- Waste Removal
- OSHA, State, and Local Regulatory Compliance
- HAZMAT (Hazardous Material) Compliance
- Commodity Resource Management
- Environmental Compliance Initiatives
- ISO Compliance
- Environmental Emergency Response Fleet Management
- Perform Mobile Equipment Scheduled Preventative Maintenance
- Perform Non-scheduled Repairs
- Retain All Maintenance & Repair Documentation
- Provide and Maintain Spare & Replacement Parts Inventories
- Ensure and Monitor Equipment Uptime
- Provide Emergency Repair Services
- Inventory Control – Client Lease / Purchase Decision
174
Maintenance Supervisor Resume Examples & Samples
- Responsible for supporting weekend PM activities, project execution and manufacturing operations (assembly equipment, packaging, material handling, fixtures, and business processes)
- Supervise weekend shift maintenance Crew (Electrical Specialists, Mechanical Specialists, Refrigeration Technicians)
- Support cost improvement and capital improvement initiatives
- Establish labor standards, equipment reliability improvement, and project prioritization
- Support safety, quality, delivery, and cost improvement initiatives
- Determine root cause of problems and implement corrective & preventive actions
- Perform Lean Sigma project work, and implement Lean Manufacturing methodology throughout area of responsibility
175
Maintenance Supervisor Resume Examples & Samples
- Experience – Five or more years of experience in a facility/plant engineering maintenance capacity with at least 5 years in supervision
- Special knowledge and skills - Exposure to HVAC, fluid handling/pumping, fluid filtering, mechanical systems, carpentry, welding, and electrical systems engineering and operation
- Knowledge of all current facility code requirements and standards
- Must be proficient in basic computer application software such as Microsoft Office Suite (Word, Excel, PowerPoint, Access, Project and Outlook), Lotus, e-mail, etc
- Good interpersonal skills, ability to communicate well in both oral and written reports
176
Maintenance Supervisor Resume Examples & Samples
- 70% - Supervision of tradespeople and contractors and ensure individuals and teams are safely performing quality work and using time and materials efficiently
- 15% - Troubleshoot equipment failures through root cause analysis with the goal of improving asset reliability and integrity
- 5% - Purchase parts, rentals and equipment
- 5% - Ensure that all work is done in compliance with federal, provincial and local regulations and/or Cargill requirements
- 5% - Daily management of the CMMS related to core job function and any other duties as assigned
- Chemical, Electrical, or Mechanical Engineering degree or related equivalent
- 3 years experience in a plant production environment
- Ability to take off-hour calls and rotate on call with facility staff as needed
- Demonstrated strong safety and environmental knowledge to apply Cargill's policies and procedures
- Strong mechanical knowledge and aptitude
- Analytical and data driven
177
Maintenance Supervisor Resume Examples & Samples
- Supervises hourly personnel involved with maintenance, repair, programming and servicing of plant facilities and equipment
- Ensures training as required to maintain necessary technical skills
- Collects and records data such as requisitions, time spent, tag information, PM, and machine documents as required
- Assists Maintenance Manager II with preventative maintenance program and helps determine ways to run equipment more efficiently
- College or Technical degree (Engineering, Electronic,s or related field highly preferred)
- High school diploma and five plus years of maintenance supervisory experience may substitute for a degree
- Three or more years of technical supervisor experience required
- Knowledge of electrical, PLC, mechanical, pneumatic, hydraulic and/or electronic equipment and systems required
- Core competencies include
178
Operations & Maintenance Supervisor Resume Examples & Samples
- Manage and direct the work force to build and maintain efficient and effective work teams compliant with customer contract and BT processes
- Coordinate the planning, development, and implementation of recovery, repair, and preventive maintenance procedures to maintain system operations
- Oversee the planning, development, and use of systems to report, manage and analyze system operations, maintenance, inventory, and spare parts
- Ensure timely completion of daily availability reports, System Recovery Reports, etc
- Actively support the Safety Committee and all Health, Safety, & Environment (HSE) initiatives
- You possess at least five (5) years of relevant supervisory experience in an operations/maintenance a service-delivery role
- You demonstrate the ability to interpret financial and performance data
- Your written and verbal English communication skills are excellent
179
Maintenance Supervisor Resume Examples & Samples
- Experience using computerized maintenance management systems (CMMS)
- Experience leading projects and implementation of project activities
- Experience using Microsoft Office Software (Excel- working knowledge of pivot tables and data analysis, Word- document creation/editing and PowerPoint- presentation creation/editing)
- Knowledge of industrial electrical & mechanical systems
- Knowledge of total performance maintenance (TPM) systems/programs
- Willing to work evenings and weekends
- Maintenance experience in the corrugated packaging industry
- Supervisory experience, preferably in a union environment
- Experience working with Programmable Logic Controllers (PLC’s)
180
Maintenance Supervisor Resume Examples & Samples
- Inspect, test, and repair equipment, electrical systems, heating and cooling systems, etc. to ensure proper working condition. Equipment includes all items for the operation of Body, Detail, and Mechanic shops. Maintain perimeter fencing and structures
- Supervise staff in performance of custodial duties, such as sweeping, and polishing floors, dusting equipment, furniture and fixtures, and removing trash and debris from auction grounds, etc. Assist as necessary
- Maintain accurate records and reports regarding the maintenance activity of the Auction,
- Conduct break-fix repair as well as preventative maintenance
- Supervise and direct the work of maintenance employees by determining work procedures, preparing work schedules, expediting the workflow, assigning duties and examining work for accuracy and conformance to policies and procedures
- Assist manager in counseling and disciplining employees as necessary. Under the direction of the manager, plan, monitor and evaluate employee job performance, and assist manager in conducting performance appraisals
181
CPS Jp-maintenance Supervisor Resume Examples & Samples
- Plan and Execute Strategic Preventive Maintenance
- Review maintenance records and decide comprehensive preventive maintenance plans based on statistics
- Work with Engineering Manager to decide priorities of preventive maintenance according to the budget and organizational goals
- Manage maintenance resource and provide technical training and advice to maintenance team members as a mentor
- Direct, coordinate and provide instructions to external vendors to conduct maintenance work according to the plan
- Ensure Continuous Production Line Operation
- Work with Production Supervisors or other functional leaders to make a recovery plan in case of major breakdown of production lines
- Conduct rapid troubleshooting based on a result of failure analysis leading maintenance team members
- Support Capital Project planning and implementation
- Support next year’s capital project planning conducting technical research to create draft plans
- Support implementation of approved projects working with project management team and concerned stakeholders
- Support to develope specifications, manage on-site work and implement validations controlling external vendors
- Assign maintenance members to each task and support the total project management
- Provide facility improvement support
- Review proposed plans considering required operating expense, cost saving/avoidance and other benefits to decide priorities of the plans
- Implement the facility improvement plans communicating with requesters or assign the implementation work to maintenance team members
- Execute proper maintenance operation according to requirements
- Review and check maintenance operations to ensure adherence to local reguratory, KORE, ISO requirements
- Conducts or support internal audits and related programs under KORE
182
Maintenance Supervisor Resume Examples & Samples
- Responsible for supervision and development of maintenance personnel. Manages the day-to-day maintenance function within his/her area of responsibility
- Ensures plant support systems are well maintained and performing to Company standards as well as Local and State regulatory requirements
- Manages contractors to ensure quality work is completed safely and on time
- Coordinates plant maintenance requirements with the Planner/Scheduler to effect necessary upgrades, modifications and repairs
- Implements the weekly work order schedule by issuing work orders and preventative maintenance inspections to assigned crew leaders/technicians
- 5-years production plant experience with mechanical/electrical background necessary and 4-year degree or tech school background desired. Certified Maintenance Reliability Professional (CMRP) or equivalent is highly desired
- 3-years experience working with Boilers, Water Treatment, HVAC and Compressed Air required
- Have or able to acquire a working knowledge of personal computers in a reasonable training period (typing skills helpful)
183
Maintenance Supervisor Resume Examples & Samples
- Lead Suncor’s Journey to Zero safety initiative
- Demonstrate strong commitment to all environmental health and safety practices, policies, standards and regulations
- Coordinate day-to-day maintenance activities with the planner, supply chain management, and other relevant stakeholders
- Supervise operations and maintenance staff and activities at pipeline facilities
- Manage personnel, including work assignments, administration, training, mentorship and coaching, performance appraisals and career/skills development for staff
- Provide a high degree of technical knowledge and direction to front line trades personnel in one or all of these related trades: electrical, instrumentation, millwright, mechanic
- Coordinate the field staff and project team during commissioning and start-up of new facilities
- Supervise and coordinate routine contract service providers
- Assist in budget preparation and budget stewardship for the area of responsibility
- Ensure regulatory compliance in all operational activities
- Five or more years of related operations and/or maintenance experience in oil and gas, pulp and paper, mining or a similar industry
- Previous supervisory experience guiding complex maintenance activities, is considered an asset
- Electrical and/or Instrumentation certification as a journeyman or engineering technologist, or a degree in a related engineering discipline
- If applicable, attach your journeyman / red seal ticket with your application in order to be considered
- Proficient knowledge and skills with instrument and electrical systems, measurement, or maintenance of other related facilities and equipment
- Proficient in the use of Microsoft Office (Excel, Word, PowerPoint, Outlook) and a preference for proficiency with computerized maintenance management systems (CMMS) and SAP
- Broad knowledge of the pipeline industry, conventional oil and gas operations and processes
- Good working knowledge of the Alberta Environmental and Occupational, Health and Safety regulations
- Strong leadership skills (interpersonal communication, problem solving, decision making, strategic thinking)
184
Maintenance Supervisor Resume Examples & Samples
- Reports directly to Maintenance Superintendent
- Directly supervise unionized mechanics, welders and pipe fitters
- Provide direct report manpower as required by PM Superintendent
- Provide direct report manpower as required for ship crews
- Provide direct report manpower as needed within Maintenance Department to support other crafts/shops
- Directly support operations and oversee repair and maintenance of Vapor Emissions Control Systems including MVR, VDU, Bio-oxidizers and Scrubbers
- Other equipment and systems supported include but not limited to: mobile equipment, HVAC, compressors, boilers, steam, piping
- Obtain monthly meter readings of utilities (steam, nitrogen, electricity, natural gas)
- Provide regular safety contact with contractors and direct reports
- Ensure all tasks are performed safely
- Keep up-to-date documentation files for such items as P&IDs /other drawings, manuals, procedures of all systems and equipment for areas of responsibility
- Manage repair and maintenance records
- Manage direct reports’ attendance, overtime, vacation, timesheets, work assignments
- Coordinate all activities with Maintenance Department management, Operations, EH&S and all other affected parties
- Provide back-up to other Maintenance Supervisors
- Provide back-up to Boiler Room Operations
- Financial oversight of all areas of responsibility
- Issue Lawson requisitions for services and materials as required to perform job duties
- Provide vacation coverage for other Maintenance Supervisors
- Attend all required training
- Minimum 5 years experience in industrial facility (petroleum industry experience is preferred but will also consider process industries) in maintenance supervisory, project management, engineering positions. Management experience in unionized facility preferred
- Minimum 10 years overall relevant technical experience
- Must possess and maintain a valid drivers license and a driving record satisfactory to the company and its insurers
- Technical training and hands-on experience with emissions control systems, especially thermal oxidizers and scrubbers
- Satisfactory completion of a mandatory drug screen and background check upon job offer
- Boiler Operators License (any level)
- Experience using CMMS systems such as Maximo, MP-2, Dossier, 7i, Bench Mate or equivalent
185
Operations & Maintenance Supervisor Resume Examples & Samples
- Oversees day-to-day operations and maintenance of client’s buildings, facilities and equipment focusing on keeping all equipment in an operating and functional condition by directing a workforce consisting of technical and non-technical employees
- Direct day-to-day operations to attain established goals and objectives. Monitor performance against approved plans
- Influences budget, costs, staff and vendors by planning, scheduling, and implementing processes and procedures
- Initiates and communicates a variety of personnel actions; e.g., employment, termination, performance and salary reviews, disciplinary actions, scheduling and/or approving overtime
- Establish and maintain effective two-way communications to understand the needs and concerns of employees; communicate employee attitudes and expectations to higher management; properly manage employee personal information
- Identify and maintain accountability for company assets within assigned area and ensure employees understand their obligation to protect company assets
- Demonstrates leadership by example and shows integrity and candor in all actions
- Works proactively to identify potential project problems or opportunities, analyzes these issues using appropriate resources, and develops and implements optimum alternatives
- Clearly understands AECOM scope of work and contract requirements for the area of responsibility
- Supports or conducts formal presentations to clients and/or management
- Maintains a strict schedule in order to be successful in the assignment, yet demonstrates flexibility in the day-to-day activities and scheduling for the benefit of the customer
- Exhibits strong leadership skills, such as motivation, delegation, ownership, leading by example, well-developed organizational skills, excellent communication skills, etc
- Performs other duties as assigned by Manager
- Two years of experience in a leadership position demonstrating the ability to analyze Equipment Maintenance related problems (such as Electrical, Mechanical, HVAC, Automation and Control, etc.); then recognize and determine solutions (engineered or otherwise) for resolution. This includes but is not limited to opportunities for improved asset reliability, improved quality results, safer work conditions, lower maintenance cost, and improved work plans to increase efficiency
- General working knowledge of all facility related equipment & systems in an industrial manufacturing facility
- Experience utilizing a CMMS, preferably Maximo
186
Maintenance Supervisor Resume Examples & Samples
- The ability to produce accurate, high quality work in a time-sensitive fast paced environment
- The ability to organize, prioritize and own multiple tasks while meeting and/or exceeding deadlines
- The ability to partner with site leadership to establish priorities and deliver results
- Strong communication skills and proven success in communicating effectively with all levels
- Initiative and ability to work independently and as part of a team with a strong sense of urgency
- The ability to motivate, influence and drive good business decisions forward while working with a diverse workforce
- Experience applying problem solving skills with the ability to identify key business drivers and delve into the details
- Manage maintenance activities in meeting or exceeding environmental, safety and health objectives that support risk profile reduction
- Conduct and document daily toolbox safety meetings with crew
- Ensure mechanics adherence to safety and occupational health procedures
- Routinely audit work for safe behaviors, work quality and efficiency
- Conduct investigations as required and document findings with action items
- Actively support development of the maintenance safety committee
- Ensure mechanics receive training and development needed to support maintenance activities
- Ensure direct reports have appropriate expectations in place with line of site objectives and manages performance against them
- Support unit reliability objectives for quality, availability and production targets
- Work with reliability resources to develop reliability strategies and implement them for maintenance equipment
- Work with engineering project resources to support successful expense and capital project implementation
- Support and participate in audit activities as requested
- Manage maintenance resources to deliver low cost and high efficiency within the work control processes
- Utilize SAP to obtain information on scheduling, equipment history, spare parts, job plans and repair plans as required
- Manage crew activities to drive high schedule adherence
- Transfer craft resources after assessing the daily schedules to other supervisors as necessary to support schedule resource requirements in other areas
- Provide accurate and timely progress updates on managed work on a daily basis including contractor managed work in areas of responsibility
- Coordinate and direct activities associated with emergency work
- Monitor maintenance metrics and adjust to meet performance expectations
- Ensure accurate work order history is captured and entered into the SAP
- Manage maintenance work execution during all of the phases of pre-turnaround activities, turnaround (TA) execution, and post TA activities
- Work with TA work groups to develop resource plans for maintenance related staffing needs on turnaround events
- 3 or more years’ maintenance experience in a lead position in a manufacturing environment or equivalent military experience; or a Bachelor’s Degree in a technical field plus 2 years’ experience in a manufacturing environment
- Experience in Microsoft Office Software (Excel – sorting data, creating tables and creating graphs, Outlook – scheduling, Word – document creation/editing and PowerPoint – presentation creation/editing
- 3 or more years’ experience in maintenance supervision at a chemical or refinery plant with Process Safety Management (PSM) covered processes
- Experience with computerized maintenance management systems such as SAP, Indus and/or Maximo
- Experience with P&IDs
187
Maintenance Supervisor Resume Examples & Samples
- Lead and foster the safety culture for maintenance personnel while driving maintenance and reliability productivity improvement efforts
- Direct maintenance staff within the framework of the collective bargaining agreement
- Evaluate the job performance and developmental needs of direct reports. Provide appropriate feedback, coaching, and training to meet the needs of individuals and the maintenance needs of the site
- Evaluate effectiveness and assist in development of Predictive and Preventive maintenance plans
- Participate in Root Cause Failure Analysis and execute corrective actions for complex and/or repetitive problems
- Coordinate with others to ensure that critical equipment is identified and that spare parts are available
- Coordinate contractors as needed for mechanical, electrical and other related contracted work
- Control maintenance expenditures in a cost-effective way according to the site budget for site repairs, resources, direct labor, overtime and contractors
- Deliver on key performance metrics for the maintenance department such as equipment availability, schedule compliance, PM completion rate, percent of reactive work, etc
- The ideal candidate requires 80% mechanical and 20% electrical, skills, ability and/or experience
- Minimum 5 years of maintenance and/or supervisory experience in chemical/petrochemical, pulp/paper or closely related industry
- Candidates are PREFERRED who offer the following
- College and/or related technical courses
- Strong commitment to personnel and process safety
- Very service oriented and customer focused
- Broad based, hands on knowledge and experience with various types of mechanical equipment and repair (pumps, blowers, mechanical seals, piping, vessels, exchangers, welding, rigging, scaffold)
- Knowledgeable of 480V power distribution, feeders, and Motor Control Centers for motors, variable speed drives, lighting, grounding, etc. and instrumentation and control systems including interlocks, PLC, and DCS (Delta V preferred)
- Knowledgeable with applicable code requirements, including OSHA, PSM (Mechanical Integrity), ASTM, ISA84, NFPA70E
- Ability to work in a team environment with other engineers, technicians, operators, and contractors
- Experience of Predictive and Preventative maintenance practices such as Vibration, Ultrasound, Oil analysis, and Thermography
- Fluent in English. Good written and oral communication skills
- Advances problems toward resolution when encountering ambiguity or uncertainty
- Results oriented, puts in extra effort and work to accomplish critical or difficult tasks
- SAP preferred CMMS (Computerize Maintenance Management System) experience. Ability to utilize computerized maintenance systems for data entry/tracking to include scheduling, payroll, work orders, parts inventory, etc
188
Maintenance Supervisor Resume Examples & Samples
- Identify and report current and potential hazards and review with shift members
- Set work expectations and performance levels with employees and provide timely and meaningful feedback
- Experience working with or operating heavy haul trucks, auxiliary equipment or shovels would be an asset
- Journeyman certification (heavy equipment technician is preferred but will consider Journeyman welders and millwrights); attach your Journeyman ticket with your application in order to be considered
- Knowledge of the mining industry and technology with hydraulic and electric shovels, haul trucks and auxiliary equipment
- Understanding of how to safely and efficiently achieve maximize production
189
Senior Maintenance Supervisor Resume Examples & Samples
- Primarily being responsible for planning, execution, coordination and maintenance of site-wide facilities / utilities to ensure operational Safety, Food Safety, Quality, Reliability and Continuous Improvement
- Directing the 24/7 hour Maintenance Supervision and Execution activities while providing operational support and being responsible for supervision of technical crafts on a shift and coordination of planned or preventative maintenance, including contracted work and vendor service, with the Maintenance Supervisors
- Providing direction and guidance to crafts and their activities for assigned area/shift
- Managing unplanned downtime through proper equipment troubleshooting and preventative maintenance
- Conducting training on best practices for operating, maintaining, and troubleshooting equipment
- Using problem solving skills, AM/RM and root cause analysis to resolve and/or mitigate operational and maintenance issues
- Being responsible for compliance with all regulations including Safety and Food Safety procedures
- Managing plant projects that drive and facilitate change and communicating strategic vision to employees, motivating them to work toward common plans and objectives
- High School Diploma or GED with substantial related proven leadership, supervisory and technical experience in a manufacturing setting
- Demonstrated ability to lead and motivate others and to drive results
- Ability to prioritize and manage multiple competing requests while maintaining a culture of accountability and execution
190
Maintenance Supervisor Resume Examples & Samples
- Ensuring the direction received from the Maintenance Superintendent is followed
- Identify potential risks for the prevention of accidents, completing safety /housekeeping inspections, and resolving safety issues
- Managing outside trades/contractors performing jobs at MSS
- Track Maintenance crew/shift hours and approve them
- Provide corresponding shift/weekend canvassing as per bargain contract
- Ability to support either shifts when situation required
- Other tasks received from Maintenance Superintendent or Engineering Manager
- Perform daily inspections of the work area and document the existence of any hazards and initiate required corrective actions
- Advise employees of the existence of any potential or actual hazards to their health & safety in the workplace of which you are aware
- Communicate to employees the importance of adherence to established health & safety policies and procedures through safety talks, departmental meetings and/or work center briefings
- Communicate and enforce all company health & safety policies, practices and rules, and readily correct unsafe conditions or behaviors of which you become aware, and initiate disciplinary action when required
- Investigate workplace accidents/incidents of which you are aware and/or within the work area(s) under your responsibility, which may include but is not limited to conducting interviews with employees, investigating the incident scene, preparing incident investigation reports, and implementing corrective actions
- In the event of a critical injury, ensure the operations manager is notified immediately and a worker representative of the Joint Health & Safety Committee is notified to assist with the investigation
- Support employees impaired through injury or illness to safely return to work (Return to Work program) in conjunction with the HSE Coordinator
- Comply with legislative requirements of the Occupational Health & Safety Act and Workplace Safety & Insurance Act, including the Duties of a Supervisor and Duties of the Employer as outlined in the Occupational Health & Safety Act, s. 27 and 28 and all other applicable legal requirements
- Issue safety tickets when infractions are evident
- 3 to 5 yrs. of relevant experience in a leadership position at the Maintenance Supervisor level combined with excellent interpersonal, analytical, problem solving and team building skills
- Over 10 yrs. experience as a Journeyman: Industrial Electrician/Millwright
- Hands-on Allen-Bradley PLC Software RS Logix 500 and Control Logix5000 skills including basic programming
- Robotics (Motoman, Fanuc) and automation experience
- Proven ability in safety management, leadership, employee coaching and development
- Experience with spare parts management and purchasing (MP2 and SAP)
- Excellent technical hands-on skills accompanied with in-deep working knowledge of an industrial environment standards and regulations
- Ability to prioritize of maintenance (shift) tasks, work orders, optimum downtime windows, and necessary lead times
- Demonstrate leadership skills to encourage and influence behavior and decision making
- Ability to multitask, work under pressure and work flexible hours when required
- Ability to work flexible hours to ensure weekly OT and weekends (Saturday, Sunday and/or statutory holidays) when required, to sustain production, projects, repairs and PM’s
191
Maintenance Supervisor Resume Examples & Samples
- Prepare, coordinate and control the daily maintenance activities of the plant including mechanical, electrical, plumbing, and instrumentation maintenance and repair activities to assure high productivity quality and safety
- Supervise team to maintain and increase safety, efficiency and skills and promote a cooperative attitude with subordinates. ·
- Train others on all applicable equipment and instruments
- Assist and advise in the installation of new equipment to obtain the required reliability to operate electrical/instrumental equipment
- Assure that preventative maintenance is planned and carried out
- Participate in the execution of maintenance and capital projects such as shutdowns, plant modifications, etc. Supervise suppliers’/contractors’ day to day activities and periodically participate in vendor assessment
- Ensure that contractors comply with Cabot safety and all other site procedures
- Ensure maximum plant availability through the use of established reliability principles
- Effectively practice Performance Based Management by coaching and developing employees
- Supports efforts to implement and maintain the Responsible Care® Management System in line with the requirements of the RC14001® technical specification, as applicable to the site/region
- Knowledge and ability of Maintenance Crafts
- Knowledge of Reliability Centered Maintenance
- Reading and interpreting Blueprint and technical drawings
- Ability to gather, analyze and draw well-reasoned conclusions
- Understanding of General Manufacturing Process
- Knowledge and ability in Accident / Near Miss Investigation / Reporting procedures
- Knowledge of Environmental Awareness
192
Maintenance Supervisor Resume Examples & Samples
- 3+ years of experience in a related maintenance/supervisor role
- HVAC certification required
- Ability to provide top-notch customer service to residents
- Ability to work effectively in a very fast-paced environment
- Experience with plumbing, electrical, troubleshooting appliances, basic carpentry and painting
- Time management skills
193
Maintenance Supervisor Resume Examples & Samples
- Degree or certificate in facilities management or related field
- Demonstrated success in supervising multiple skilled trade leads and journey personnel involved in the maintenance, alteration or operation of technically complex facilities, building systems, and/or equipment
- Knowledge and practical experience with WISHA (Washington Industrial Safety and Health Act) and OSHA (Occupational Safety and Health Act) regulations
- Demonstrated success in supervising skilled trade leads and journey personnel, such as machinery mechanics, carpenters, painters, masons, maintenance mechanics, sheet metal mechanics, plumbers, and electricians involved in the maintenance, alteration, or operation of buildings, facilities, door security systems and hardware, and equipment
194
T Maintenance Supervisor Resume Examples & Samples
- Perform all duties of the job classification
- Assign and direct the productive efforts of assigned employees to ensure the timely completion of all required maintenance
- Coordinate all maintenance related actions with other effected work centers
- Authorize cannibalization actions as required
- Instruct assigned employees on proper maintenance methods and procedures as required
- Responsible for the satisfactory completion of assigned work and the preparation and maintenance of required records
- Formulate necessary reports to the Government
- Enforce foreign object damage (FOD), hazardous waste, and tool control programs
- Assist in training programs as required for employees assigned to him/her
- Ensure required quality control inspections are complied with
- Maintain appropriate records of all work accomplished
- May be required to perform simple computer input functions
- Assist as directed to ensure safety, security and preservation of Government/Company owned equipment
- May be required to perform off-site service on assigned detachments
- Comply with all established general and industrial safety rules and regulations as applicable to the contract, facilities and job assignment
195
Plant Maintenance Supervisor Resume Examples & Samples
- Bachelors Degree in engineering or related
- Expert with TPM Systems
- Experience with Inventory systems
- Minimum of seven years previous experience of direct supervision in a 24/7 manufacturing environment
- Working knowledge of preventative maintenance programs
- Experience with manufacturing facilities safety, environmental, quality, maintenance, and engineering
- Working knowledge of Microsoft Office suite
- Proven ability to improve processes and provide/carry out cost reduction initiatives
- Proven ability to establish positive employee relations
- Demonstrated ability to operate within budget parameters including usage controls
- Experience implementing and leading continuous process improvements via disciplines such as Six Sigma/Lean/Visual Factory manufacturing environment
- Previous experience in supporting safety and environmental compliance
- Experience with continuous manufacturing processes
- Union experience highly preferred
- LI-VCB
196
Maintenance Supervisor Resume Examples & Samples
- Manage operations and maintenance of all equipment in the facility
- Coordinate maintenance personnel assignments to accomplish maintenance and operations duties
- Available for after hour, weekend and holiday calls
- Collaborate with production on planning for equipment maintenance repairs/upgrades
- Assist in the development and execution of maintenance budgets
- Manage projects as assigned
- Coordinate and collaborate with all other groups (production, finance, executive staff, projects/construction, etc.)
- Assist with the negotiation and approval of contracts/agreements with vendors as requested
- Assist with the site’s environmental health and safety compliance
- Manage and support the preventative maintenance program for all equipment in the facility
- Actively participate in or lead continuous improvement teams
- Ensure spare parts are available to minimize downtime in case of equipment failure
- Identify and coordinate training for maintenance personnel to keep skill sets at an appropriate level to maintain equipment integrity
- Assist in the training of employees on safety policies (Lockout Tag out, Fall Protection, Arc Flash, Hot Work, Electrical Safe Work Practices)
- Monitor and approve equipment moves, new installations, including providing direction to contracted vendors
- Develop specifications for the purchase of equipment, services, supplies, and parts
- Supervisory tasks including, but not limited to: Administer time and attendance program, scheduling overtime, employee development, manage personnel per the union labor agreement
197
Maintenance Supervisor Resume Examples & Samples
- Grade 12, Diploma in Mechanical Engineering or N6, GCC will be advantageous
- Driver’s license, 5 years’ experience, GCC factory will be advantageous, PLC as well as knowledge of PID control
- Comfort Around Higher Management
- Drive For Results
- Functional / Technical Skill
- Process Management
- Standing Alone
198
Preservation & Maintenance Supervisor Resume Examples & Samples
- Ensure field preservation and maintenance activities are executed in a safe and effective manner in accordance with the agreed Safe System of Work
- Complete Preservation check sheets to demonstrate compliance to the preservation Strategy / Execution Plan and assure integrity of equipment
- Liaise directly with other working groups, Contractor or Subcontractor counterparts to ensure effective maintenance and preservation is completed across all required interfaces
- Monitor construction/completion of equipment and systems ensuring compliance against the approved supplier’s maintenance and preservation procedures
- Monitor equipment to ensure correct preservation activities are being implemented and recorded during all phases of the project
- Bachelor’s Degree/Diploma in Mechanical Engineering
- Strong computer skills, especially MS Office
- At least 5 years or relevant experience
- Must have EPC on-site project experience gained in the Middle East
- Experience of supervision / leadership of multi-disciplinary teams
- Experience in relevant discipline for position and understanding of how equipment can be damaged
- Can demonstrate good HSSE behaviours and understanding relating to work in the Construction and Oil & Gas industry
199
Maintenance Supervisor Resume Examples & Samples
- Supervise a team of maintenance technicians on day-to-day preventive and predictive maintenance activities
- Trouble shoot and problem solve both our processes and our equipment issues
- Participate in the execution of maintenance and capital projects such as shutdowns, plant modifications, and new equipment
- Work closely with other departments to ensure customer requirements are met
- Coach and develop employees assuring effective alignment with Cabot objectives
200
INL Maintenance Supervisor Resume Examples & Samples
- Review all maintenance records for delayed discrepancies or updates to ensure it meets the aircraft mission needs in a timely manner
- Provide daily assignments to mechanics to support daily flying schedule. Works with production and quality managers to ensure established procedures are followed
- Maintain a safe working environment and adhere to all DoS, OSHA, and company safety regulations
- Ensure AWIS / TRAX is updated correctly, work card and packs are closed
- Communicate with management on any problems within the work area
- Plan, support and attend weekly and monthly Operations scheduling meetings
- Provide daily aircraft and personnel status to senior management
- Ensure component records are updated and AOG demands are followed up
- Ensure cannibalization for component/parts are updated in AWIS / TRAX and paperwork is completed
- Ensure all aircraft/component life limited parts are maintained
- Manage critical flight safety program (heavy check / service life extension)
- Carry out supervisory responsibilities in accordance with the organization policies and applicable laws
- Position requires a U.S. Department of State Secret Clearance
- B.A./B.S. degree from a four-year college or university in a related field and/or combination of education and related experience
- Current FAA issued mechanic certificate with both Airframe and Power Plant ratings
- Minimum eight (8) years maintenance experience as an aircraft mechanic
- Knowledgeable of Army manual 95-1, DA /DOS PAM 738-750 / 571, Air Force Technical Orders and the certificate holder’s General Maintenance Manual and the Operations Specifications
- Minimum three (3) years experience on fleet types relevant to the assigned program
- Good working knowledge and understanding of applicable Federal Aviation and Department of Defense regulations
- Proficient in Microsoft Office (Access, Excel, PowerPoint) and scheduling / maintenance management software
- Experience in working with and supervising a mixed fleet of light and heavy lift rotor-wing or multi-engine turbo-prop fixed wing aircraft
- Must be capable of multitasking
- Must be able to read and communicate in English
- Spanish Language and Reading Level 2 qualified
- Ability to share knowledge with others for on-the-job training
- Teamwork - Builds alliances, partnerships & collaboration with others including those different from him/her; deals tactfully with others; assumes helps with a variety of team roles
- Strategic Planning & Decision-Making - Develops strategic short & long term plans; arranges priorities, distinguishing urgent, important and unimportant in order to meet goals & deadlines; consults & collaborates with appropriate people
- Initiative & Innovation - Generates new ideas personally & encourage team to do the same; stays up-to-date on technology & approaches to work; provides creative solutions & input when faced with challenges
- Interpersonal Relationships - Builds effective relationships with internal & external customers; ability to work independently and coordinate work with others; resolves conflicts in a professional manner
- Quality & Safety - Adheres to all safety & security policies and regulations; demonstrates quality work that is accurate, thorough & efficient
- Continuous Improvement - Examines personal & organizational processes, promotes opportunities for improvement; analyzes successes & failures to learn and improve
- Training & Development - Completes required & suggested training; shows eagerness and capacity to learn; receptive to coaching & feedback
- Integrity - Committed to passionately and consistently promoting a professional culture that is trustworthy, honest, socially responsible, and where differences are respected and valued
- Performance Management - Sets clear expectations & direction for staff; achieves team results consistently; coaches staff to improve; is a positive role model
- Expense Management - Plans budget appropriately, uses sound judgment; analyzes operation for improving expense efficiency; demonstrates knowledge of financial process & results
- Leadership - Builds commitment to team, company, mission & customer through effective & frequent communications; promotes an environment of trust; fosters a respectful, energetic & positive work culture
201
Maintenance Supervisor Resume Examples & Samples
- Plan, coordinate and direct maintenance functions on equipment, machinery, tools, and facilities while maintaining a pollution-free and safe environment
- Comply with all safety procedures as required by law and ensure departmental conformance to safe working procedures
- Responsible for the maintenance of and performs repairs and rebuilds mechanical, electrical and production equipment, including torque and air tool replacement as well as emergency repairs
- Completes assigned preventative maintenance and reactive maintenance repairs requiring, but not limited to, the following skills: Metal fabrication, Welding, Electrical and Mechanical Repairs, Hydraulic Systems, etc
- Ability to maintain machinery and equipment (i.e., pneumatic tools, conveyor systems, motors, gearboxes, etc.)
- Proven ability to support personnel in performing production equipment repairs and preventative maintenance tasks
- Ability to maintain and repair all building and ground systems, including HVAC, fire alarm, security, and CCTV Systems
- Develops and maintains a high level of proficiency in at least one of the above trades and is generally well versed in a number of trades
- Responsibility for input and use of CMMS driven tasks and record keeping
- Inspects and adjusts equipment and systems, perform specific preventative maintenance service and general maintenance functions
- Processes equipment incident reports
- Thoroughly and accurately completes reactive and preventive maintenance paperwork
- Operates and maintains mechanical and electrical systems and equipment that supply the building with heat, power, ventilation, air conditioning, and/or refrigeration, and other environmental systems in accordance with diagrams, sketches, operation manuals, and manufacturers specifications
202
Maintenance Supervisor Resume Examples & Samples
- Monitor quality, efficiency, safety and documentation of maintenance and die work performed
- Establish and maintain a computerized maintenance software for tracking work orders, maintenance history work of plant equipment/dies, and time utilization of maintenance technicians and die makers
- Monitor the use and inventories of spare parts, maintenance supplies, and equipment and initiates reordering when necessary
- Make recommendations and initiate continuous improvement maintenance actions
- Inspect work for completeness
- Perform and supervise installation, startup, and trials all new manufacturing and plant equipment and systems
- Associate's degree, Certifications and / or Journeyman's License helpful, but not required
- Maintenance experience with injection molding presses required (electrical, hydraulic and pneumatic troubleshooting)
- PLC and HMI experience required
- Prior supervisory experience in a manufacturing facility desired
- Computer skills with Maintenance Planning, Microsoft Office, etc
- Automotive industry experience helpful
- Good verbal & written communication skills
- Willing to work 2nd shift
203
Maintenance Supervisor Resume Examples & Samples
- Lead all assigned maintenance personnel and contractors in assuring all requirements of their assignments and responsibility are clearly communicated and understood. Foster an attitude of teamwork, compliance, quality, safety and productivity. Take prompt action to remediate employee performance issues while recognizing and rewarding positive results and performance
- Provide leadership and hands-on action for emergency response to process and facility issues. Notify maintenance and production process personnel as directed to assure timely communication and response
- Identify training needs and provide training opportunities. Provide hands-on on-the-job training to technicians
- Work with Reliability Engineering and Process Engineering to improve reliability and performance of production process equipment and utility equipment
- Timely review of completed work orders verifying timely and detailed documentation. Verify work is following departmental work flows
204
Maintenance Supervisor Resume Examples & Samples
- Inspects completed work for conformance to blueprints, specifications, and standards
- Analyzes and resolves work problems or assists employees in solving work problems
- Maintains production equipment in a manner that meets organization standards and ensures minimum equipment downtime. Requisitions tools, equipment, and supplies
- Must be able to work flexible hours/shifts as needed
205
Maintenance Supervisor rd Shift Resume Examples & Samples
- Prepares work schedules. Makes work assignments to subordinates
- May direct workers engaged in ground maintenance activities such as mowing lawns, trimming hedges, removing weeds, raking and disposing of leaves and refuse, and snow removal. May supervise custodial services
- Must be willing to work 3rd shift
206
Maintenance Supervisor Resume Examples & Samples
- Assist in day to day planning and organising of the workshops, ensuring manpower, materials and equipment are available to maintain schedules and maintenance programmes
- Day to day management of the workforce (mechanical & electrical), deputising for the Maintenance Engineer as required
- Contribute to and help communicate decisions, ideas and methods to the workshop team whilst working alongside them
- Quality check and audit completed works to ensure that required standards are being maintained
- In liaison with the Maintenance Engineer and Engineering Planner prioritise and allocate work to optimise the use of the workforce and resources available
- Identify any training needs of staff and deliver ‘on job’ training as appropriate
- Access and input information into the Computerised Maintenance Management System
- Authorisation and preparation of technical documents (for e.g. SOP’s)
- Issue Permit to work certificates for engineering areas
- Be fully aware of the sites Health and Safety Policy and take responsibility for its implementation. Take responsibility for the Health and Safety of the workforce and any visitors to site
- Carry out Risk Assessments and Method Statements for tasks to be carried out by workshop team
- Take a lead role in the implementation of site maintenance strategy
- To carry out other duties which are within the employee’s skills and abilities whenever reasonably instructed
- HNC or equivalent in engineering discipline
- Proven experience of working within an engineering team
- Proven experience (ideally 3 years or more) of people management
- Continuous Improvement Qualification (Yellow belt or above)
- IT ability – intermediate word and excel. Previous experience of Computerised Maintenance Management System
- Good interpersonal skills – both verbal and written
- Ability to work to tight timescales and moving deadlines
- Flexible and versatile approach to people and situations
207
Maintenance Supervisor Resume Examples & Samples
- Employee will comply with all Johnson Matthey Hazardous Waste procedures and local, State and federal regulatory requirements
- Directs operations of S&R, Fabrication and Facilities maintenance so customer needs are met. This will primarily involve managing resources to support the needs of the engineering and operation groups so they meet internal and external customer requirements
- Identify training requirements of the groups to keep up to date with industry and legislative needs
- Assist in the planning for Budgets and Capex projects
- Assist with the quotation process for customers by providing information as required to other areas of the organization
- Develop policies, procedures and work instructions as required to maintain facility efficiency
- Drive efficiency improvements through the use of standard tools e.g. 5S, CI, 6-Sigma
- Implement, maintain and enhance the TPM program to maximize the facilities utilization
- Deal with external contractors as needed – electrical, mechanical and contract services
- A BS degree in Mechanical Engineering with 3+ years of experience or 10+ years experience in a Powertrain testing facilities environment is preferred
- Welding experience preferred
- Ideally candidate is already leading or managing a group and is a good motivator/mentor
- Testing knowledge is preferred
- Candidate should need minimal supervision and should be able to identify and plan priorities without direction
- Requires broad knowledge of facility operation
- Good communication skills (written and verbal)
- Ability to interpret customer requirements based on specifications or conversations
208
Maintenance Supervisor Resume Examples & Samples
- Employee will comply with all Johnson Matthey Hazardous Waste procedures and local, state and federal regulatory requirements
- Ensures all employees comply with Johnson Matthey (JM) safety procedures and Personal Protective Equipment (PPE) requirements
- Communicate with internal customers to determine and understand their needs, timing, etc
- Ensure internal customers are kept up to date on their request status
- Execute the preventive maintenance procedures, janitorial responsibilities, repairs, and projects
- Assist department in meeting key performance indicators
- Assign jobs to employees and lend technical advice
- Execute and ensure safe work practices through training, procedures, housekeeping, and monitoring
- Assist in planning and executing shutdowns
- Ensure open communication throughout department
- Plan and schedule various maintenance, project, construction and contract work at the ECT sites
- Ensure that all parts and equipment are available for planned work
- Follows and enforces storeroom policies and procedures
- Provide program timing for all assigned projects from initial scopes to final completion
- Responsible for equipment and procedural modifications needed to create efficient maintenance techniques
- Find and act on opportunities to continuously improve and prevent equipment downtime, machine accuracy or general good practices
- Support and execute 5S initiatives within the department and organization as a whole
- Administer union contract to employees
- BS degree in Mechanical/Electrical Engineering with 2 years maintenance experience or 4 years of maintenance and supervisory experience. An equivalent combination of education and experience may be considered
- Prior manufacturing facility experience required
- Ability to work 12 hour night shift
- Hands-on mechanical and/or electrical experience preferred
- PRINCIPLES ONLY- NO RECRUITERS PLEASE
209
Maintenance Supervisor Resume Examples & Samples
- High School Diploma or GED and related maintenance work experience
- Previous supervisory experience in a manufacturing environment or related
- Strong mechanical/electrical aptitude, along with proficiency in Microsoft Office
210
Maintenance Supervisor Resume Examples & Samples
- MS-1 supervises and provides technical direction to a maintenance crew consisting of skilled and semi-skilled tradesmen in the building, mechanical, and electrical trades performing building maintenance, repairs, construction, and installation activities in multi-county residential community properties
- Reviews maintenance requests; visits the project site to confirm the scope of maintenance requested and determine information such as dimensions, materials, equipment, and labor required to complete the project
- Coordinates project work flow in accordance with designed documents and scope of work
- Enforces and schedules workforce as required per the preventive maintenance program
- Works closely with the Business Office to develop maintenance contracts
- Supervises maintenance staff in order to achieve effective coordination/scheduling of work performed, ensuring efficient use of labor and material
- Based on observation of work performance, determines training needs, and develops related training programs
- Implements and enforces safety procedures and standards for all maintenance operations
- Inspects work performed by outside contractors to ensure work is completed in accordance with project plans and specifications
- Periodically prepares standardized written performance evaluations for subordinate employees
- Inspects properties routinely and as assigned to determine maintenance needs based on findings
- Assists in the preparation of annual operating budget based on workload, equipment replacement schedule, capital improvement projects, and operational needs
- Supervises clerical activities such as standardized work order process, file management, reports, and correspondence
- Utilizing a computerized work order system, ensuring efficiency through workforce management
211
Maintenance Supervisor Resume Examples & Samples
- Responsible for day to day maintenance needs in the plant
- Supervision of mechanical and electrical maintenance staff
- Support production needs as it relates to equipment maintenance
- Manage scheduled maintenance work and breaks in work
212
Maintenance Supervisor Resume Examples & Samples
- Diagnoses malfunctions and performs vehicle repairs (e.g. adjust/test steering, electrical, cooling, lubricating, braking systems, drive trains, suspensions, power steering units, clutches, transmissions and oil, temperature, gas regulating components, adjust/test/rebuild engines etc.) and related assigned duties within qualification level, in accordance with all relevant Federal, State/Provincial and local guidelines and requirements
- Oversee (and personally comply with) the local implementation of NELLC maintenance and safety standard operating procedures in this maintenance facility, ensuring that local maintenance staff follow them, and comply with all locally applicable public authority legislation, regulation and standards
- Oversee the local use of NELLC's EAM (Enterprise Asset Management) ERP application, and maintenance facility staff to record and to track local maintenance work orders and local parts inventory. (This includes using this application personally)
- Oversee the parts inventory maintained and used in this maintenance facility
- Oversee (and participate in when appropriate) the work needed to implement preventive maintenance for the vehicles serviced by this maintenance facility
- Oversee (and participate in when appropriate) the work needed to complete “unscheduled repairs” to the vehicles services by this maintenance facility
- Represent the maintenance activity at the local level in its interaction, communication and coordination of activities with other local operations functions: driver care, route operations, and customer care
- Supervise the maintenance staff at this maintenance facility
- 5 years of fleet Supervisor experience in a Diesel Shop with Heavy/Med duty fleets
- Minimum of five years Auto / Truck or Bus mechanical repair experience
- Experience with Compliance with the local applicable DOT compliance of Med / Heavy Trucks
- Prefer ASE Certification as a Master Automotive Technician and/or a Master Truck Technician
- Must be computer proficient
- Strong experience with computerized diagnostics
- Ability to use good judgment and Decision Making skills
- Background in planning and scheduling maintenance repairs (Daily, Weekly, Monthly)
- Supervisor experience in purchasing, and budget management experience
- Must be willing to work flexible schedules
- Must pass DOT pre-employment drug screen and background check
- ASE Certification desirable but not required
213
Plant Maintenance Supervisor, Recycling Resume Examples & Samples
- Maintains all operating equipment in satisfactory condition. Schedules needed repairs to have minimum interference
- Coordinates and supervises all maintenance work and repairs, and monitors progress and quality
- Reviews technician repairs and other maintenance requests, and prepares work order documents
- Reviews all DEI’s and responds accordingly to noted equipment deficiency’s
- Performs mechanical duties as needed
- Serves as a mentor to help teach maintenance skills to entry level tech’s
- Oversees personnel including coaching, training, evaluating employee performance, and conducting disciplinary action as needed. Provides input into termination, compensation, and promotion decisions
- Monitors inventory of replacement parts and restocks as needed
- Interprets and ensures consistent application of organizational policies and safety regulations
- Creates and submits reports as necessary
- Direct supervision of full-time employees
- Education: High School Diploma or G.E.D. (accredited)
- Experience: 4 years of relevant work experience (in addition to education requirement)
- 5 – 7 years experience with hydraulics, mechanical, electrical, and pneumatic applications, and should posses welding and fabrication skills
- Maintenance and repairs skills, and supervisory experience may be required
- Must be willing to work as necessary (including weekends) to ensure the highest level of confidence of system operational availability
- Required to use motor coordination with finger dexterity (such as keyboarding, machine operation, etc) most of the work day
- Required to exert physical effort in handling objects less than 30 poundsrarely
- Required to be exposed to physical occupational risks (such as cuts, burns, exposure to toxic chemicals, etc) rarely
- Required to be exposed to physical environment which involves dirt, odors, noise, weather extremes or similar elements rarely
- Normal setting for this job is: office setting and/or plant
214
Maintenance Supervisor Resume Examples & Samples
- Must be adaptable to changing priorities, as assignments can be altered both at the Community and Regional level
- Must be well versed in all areas of Essex platforms based on your designated role (Yardi, Yieldstar, On-Site, etc.)
- Must be an energized self-starter that can complete assigned duties with some level of autonomy
- Must comply with all company policies and initiatives, bringing attention to the Floating Community Manager any discrepancies in these areas where appropriate
215
Senior Maintenance Supervisor Resume Examples & Samples
- Ensure a safe working environment and culture while complying with environmental, quality, and safety rules & programs (ISO 14001, TS16949, MIOSHA)
- Communicate and enforce safe working procedures, actively identify safety concerns and drive continuous improvement efforts of corrective actions
- Effectively lead a team of maintenance team members with responsibility for 24 hour / 7 day maintenance coverage and plant support
- Establish clear and measurable expectations of performance, monitor metrics and provide guidance to achieve the department and plant goals
- Drive maintenance engineering best practices
- Prepare maintenance improvement plans relative to capital expenditures, repairs, staffing, including facilitating knowledge with maintenance technicians
- Facilitate and implement process improvements through people deployment, productivity enhancements, benchmarking and being a model for change
- Manage projects and equipment turn-around in a safe, efficient and timely manner
- Lead maintenance improvement plans aligned with strategic business plans; accountable for delivering plant performance metrics
- Collaborate with Manufacturing Schedulers & Team Leaders as required to work on equipment
- Establish strong business relationships with other functional areas to best support mutual plant objectives
- Facilitate knowledge transfer with maintenance technicians to accelerate growth & development
- Become familiar with OSHA, State and local facility safety and regulatory requirements
- Review Preventive Maintenance schedules on a regular basis and ensure on time completion
- Provide leadership and support to maintain clean & organized work areas
- Manage, approve, and report employee time in appropriate form delivered on time every week
- Develop and maintain employee roster and shift work schedule for maintenance crew
- Liaison to contract resources to support both 24/7 coverage as well as project execution
- Oversee maintenance supplies and inventory control
- Approve and manage all interface with outside contractors performing onsite work
- 7 years engineering or maintenance experience in a manufacturing or industrial environment
- Minimum of 3 years of supervisory experience in a manufacturing or industrial environment
- Experience with safety management; including working knowledge of OSHA safety standards
- Experience with maintenance engineering concepts including: planning & scheduling, preventive & predictive maintenance, project check-out & start-ups, and mechanical integrity
- Previous PM experience in a Manufacturing Equipment Environment preferred
- Experience with mechanical & hydraulic presses preferred
- Experience implementing maintenance cost management techniques
- Demonstrated ability to be a change agent for maintenance / facility improvements
- Basic skills including alphanumeric data entry for proper use of BW PMI databases
- Efficient use of Excel (spreadsheets), and Outlook (email/calendar)
- Ability to navigate through necessary BW PMI files / folders and databases
- Ability to produce accurate, high quality work in a time sensitive fast paced environment
- Ability to organize, prioritize and multi-task while meeting and/or exceeding deadlines
- Strong communication skills and proven success in communicating effectively at all levels
- The ability to motivate, influence, problem solve, and be a change agent
- Good analysis and problem-solving skills
216
Maintenance Supervisor Resume Examples & Samples
- Minimum Seven years working experience repairing industrial processing equipment in an industrial environment or in the military is required
- Minimum two years supervision experience is preferred
- Equipment knowledge - wiring, electrical, electronic components, pipe systems and plumbing, machinery is required
- Maintenance management experience including planning, scheduling, budgeting, negotiating, parts management, vendor management and with maintenance management systems is required
- Ability to read maintenance literature printed in English required
- Prior experience with and ability to read a blueprint is required
- Basic Microsoft Office computer skills required
- Boiler knowledge preferred
217
Maintenance Supervisor Resume Examples & Samples
- HVAC experience preferred
- Prior experience and ability to perform welding activities including MIG, TIG, ARC, cutting and brazing preferred
- Ability to stand for up to 7 hours in an 8 hour shift required
- Reliability certification such as CPMM or CRMP preferred
- Ability to be on call 24 hours per day
218
Maintenance Supervisor Resume Examples & Samples
- Responsible for planning and oversight of maintenance technicians
- Analyzes operational problems and develops modifications in design to improve efficiency
- Utilizing Maintenance Management System (MP2) to create work orders and generate execute PMs
- Maintaining and continuously evaluating plant-wide Maintenance activities
- Evaluating Maintenance Technician’s skill level
- Conducting daily meetings pertaining to ongoing machine down-time and previous shifts downtime
- Supporting internal customers (manufacturing engineering, production lines, utilities, etc.)
- Supporting technical items for all Kaizen and continuous improvement activities
- Supervising junior maintenance activities
- Responsible for Daily machine down-time reporting Maintenance Sequel Server System
219
Maintenance Supervisor Resume Examples & Samples
- Maintaining the maintenance stock room, determining the materials to stock, ordering the materials, and generating purchase order requests
- Maintaining the plant equipment in a safe working condition with minimal interruption of production
- Provide leadership and support to maintenance and mold change associates
- Develop WCM and Lean initiatives for rubber manufacturing
- Provide engineering support and expert advice to WCM teams
- Providing production equipment that is safe to operate
- Purchasing and identifying spare parts for equipment including maintaining the stock room
- Develop, install, and upgrade production equipment to keep up with customer demand
220
Industrial Maintenance Supervisor Resume Examples & Samples
- Supervises maintenance activities and projects
- Responsible for the effective use of personnel, material and equipment
- Implements divisional and Corporate policies
- Coordinates input from internal/external customers to better understand customer needs and/or perceptions
- Actively identifies new areas for learning and takes advantage of learning opportunities
- Technical Bachelor degree or Skilled Trades Journeyperson’s Card
- High level of interpersonal skills to effectively lead, motivate and facilitate others in group situations
- Ability to manage people
- Knowledge of continuous improvement processes (CIP)
- Statistical process control skills
221
Industrial Maintenance Supervisor Resume Examples & Samples
- Supervises electrical / mechanical construction and maintenance projects
- Perform preventative and predictive maintenance activities per schedule
- Organize, plan and execute maintenance and process projects to include process system upgrades and new installations, design, build & debug as required
- Be the “hands-on” technical operational specialist, with both mechanical and electrical responsibilities to assure the optimization of all production equipment
- Build and maintain good working relationships with employees, union, and management
- Provide a leadership role in the implementation of major department initiatives; provide technical (mechanical, electrical, pneumatic/hydraulic) expertise to the business unit team to assist in creating and implementing the best solutions to manufacturing challenges
- Proactively pursue the vision established for the area and foster an atmosphere of teamwork and cooperation
- Responsible for diagnosis of equipment malfunctions; address all machine related issues, with co-workers and management personnel with accuracy, in a timely manner, giving updates and schedules as necessary
- Meets schedule and quality requirements
- Implements safety and good housekeeping practices; promote safe work practices and achieve objectives for ergonomics and health and safety (safety talks, job instruction training, ergonomic evaluations, safety incident reports)
- Establishes a course of action to accomplish completion of the job and/or
- Knowledge of basic math including trigonometry
- Oral and written communication skills
- High level of interpersonal skills to work effectively with others
- Knowledge of basic mechanical concepts
222
Maintenance Supervisor Resume Examples & Samples
- Executes safe work practices as the highest priority and achieves objectives for ergonomics, health/safety and housekeeping
- Ensures employees perform job responsibilities and empowers them to continuously improve their work by managing and eliminating constraints
- Motivates, trains and develops employees to effectively perform their jobs utilizing standardized methods
- Supervises construction and maintenance projects
- Responsible for diagnosis and repair of equipment malfunctions
- Establishes a course of action to accomplish completion of the job and/or project
- Provides support to execute production schedules and product requirements by utilizing Competitive Manufacturing Processes with emphasis on variation reduction
- Understands and consistently administers National and Local Agreements; participates in local labor relations activities
- Keeps abreast of current product developments and trends in areas of expertise
- Develops and implements predictive and preventive maintenance activities through the Maximo System
- Works with assigned personnel as required on current and future assembly processes
- Communicates between shifts and departments to implement best practices, resolve problems and sustain consistent performance to objectives
- Implements Lean Manufacturing Principles
- Responds to suggestions promptly in writing
- Builds and maintains good working relationships with employees, union and management
- Reduces waste by identifying and improving value-added tasks and eliminating non-value added tasks
- Controls costs and achieves productivity improvements
- Provides input to payroll and performs other administrative tasks as required
- High level of analytical ability where problems are complex
- Knowledge of mechanical and electrical concepts
- Must be willing to work any Shift
- 2+ years manufacturing experience supervising skilled trades
- Knowledge of and ability to effectively use computer software as it pertains to engineering preferred
223
Maintenance Supervisor Resume Examples & Samples
- Schedules and supervises of shipping/receiving associates
- Processes store returns and return to vendors using proper Company policies
- Conducts daily crew meeting to discuss safety, productivity and accuracy
- Supervises scheduling of inbound load appointments
- Walks warehouse daily, with Superintendent, to ensure that safety, security, sanitation and pest control codes, laws, and policies are maintained
- Ensures the most economical and efficient use of equipment and personnel to accomplish assigned work
- Develops and maintains good working relationship with all departments
- Assigned Order Selectors, Receiving, Shipping or any other Warehouse personnel
224
Maintenance Supervisor Resume Examples & Samples
- Ensure customer service, quality, and safety standards are met in an efficient and innovative manner; partner with all departments to address issues, where needed
- Be a role model leader for others; act with integrity and respect, approach responsibility with confidence and ownership, inspire superior performance, and develop a track record of success
- Manage team members coaching for growth and development; ensure department morale and engagement remains high
- Direct preventative maintenance and repairs on conveyor and material handling equipment, electrical diagnosis and repair, facility maintenance and repair, and general construction
- Monitor execution and reporting of approved preventative maintenance programs for all equipment in the distribution facility, (including yard tractor equipment)
- Maintain centralized organization of all mechanical and building drawings, equipment inventory, work order history and supplier/contractor contact listings
- Partner with facilities department to assure proper electrical, structural and mechanical issues are addressed when creating, repairing or replacing any property related to the distribution facility
- Ensure Maintenance and Operations team partner for best practices across distribution facilities
- Coordinate contractor work on-site to avoid interruption of facility operations and to remain within the constraints of DC needs and security
- Ensure Maintenance team acts as active participant in safety program development and committees
- Coach, develop and train shift Maintenance team to facilitate performance of maintenance duties; keep the distribution facility clean, safe and operational at all times
- Develop structured training programs for all Maintenance Specialists and Operations Clerks to gain working knowledge of PLC controls, forklift repairs/maintenance, Dematic put-to-light controls systems and general electrical work
- Provide training on aerial platform equipment (scissor and boom lifts)
- Bachelors’ Degree in Business Management, Logistics, Industrial Engineering, or equivalent,
- 2 years previous management experience in a warehouse/distribution/retail environment or equivalent; .com and/or “Omni-channel” retailing experience preferred
- 4 years previous maintenance experience preferred
- Bi-lingual preferred: English/Spanish
- Mechanical trade experience preferred
- Programmable Logic Controller (PLC) experience a plus
- Knowledge forklift and battery repair and maintenance, and preventative maintenance preferred
- High degree of proficiency MS Office Suite, Outlook & Internet applications
- Strong analytical, prioritizing, interpersonal, problem-solving, & planning skills
- Demonstrated collaborative skills and ability to work well within a team
- Ability to work with and influence peers and senior management
- Ability to work in a fast-paced and deadline-oriented environment
- Self-motivated with critical attention to detail, deadlines and reporting
225
Maintenance Supervisor DC Resume Examples & Samples
- Oversee the maintenance of all operating equipment, and facility systems. Enforce proper turn time of preventive maintenance schedules. Ensure timely response to critical equipment downtime issues in the distribution center
- Train/develop maintenance personnel; authenticate that skill sets meet minimum requirements of job function
- Make use of the Computer Maintenance Management System (CMMS), utilizing it to its full capability
- Interact with outside vendors relative to the coordination of all construction projects to the facility, property and equipment. Responsible for validation of quality work, and compliance of all safety standards
- Oversee the required back stock of maintenance spare parts and supplies while minimizing inventory levels through strong supplier partnerships
- Ensure contractual compliance to include: landscape, mat rental, pest control, snow removal, waste management, and fire system maintenance accounts
- Maintain an active partnership with the safety committee to ensure strong alliance regarding all safety issues on the property
- 8-10 years maintenance experience in large distribution center and/or manufacturing environment
- 2 + years of supervisory experience in a large distribution center and/or manufacturing environment
- Technically proficient in mechanical and electrical maintenance
- Ability to review and critique schematic diagrams
- Comprehensive knowledge of CMMS
- Knowledge of 5-S practices preferred
- Ability to lift up to 50 lbs
- Extensive knowledge of OSHA standards and regulations
- Awareness of state/local regulations, and code requirements
- Must have outstanding interpersonal, and communication skills (oral/written)
- Proficient P.C. skills, to include Microsoft Excel and Word
226
Maintenance Supervisor Resume Examples & Samples
- Supervise a twelve plus union maintenance team, in their daily tasks, that include electrical, pneumatic, hydraulic, mechanical and facility repairs
- Maintain and enforce safety program for the maintenance department; review safety records to uphold company policies to ensure a safe environment for all employees
- Develop maintenance personnel encouraging a team environment
- Ensure and audit 5s+1 policies in the maintenance department
- Ensuring equipment is maintained to comply with all environmental requirements
- Assist in developing and maintaining a Preventative Maintenance and Part Inventory program
- Evaluate equipment and determine what repairs are needed to improve machine uptime
- Track , monitor and audit maintenance Key Performance Indicators
- Filing purchase orders for procurement of spare and replacement parts
- Recruiting maintenance staff and evaluating their performance
227
DC Maintenance Supervisor Resume Examples & Samples
- 45% Managing Process: Ensures all operations procedures are followed effectively, and identifies and recommends needed changes to Operations Manager and/or Assistant General Manager on the standardized processes for the functional area. Evaluates and analyzes current work methods and recommends ways to eliminate inefficiences
- 25% Coaching and Developing Associates: Guides associates in daily operations, and monitors to ensure a high degree of productivity, safety, service and quality. Responsible for the training, coaching and feedback of hourly associates, and performs regular evaluations of associates through factual data and subjective observations. Uses discretion to provide coaching and counseling to associates regarding job performance, methods of performing job tasks. Resolves associate relations issues that arise in assigned functional area. Responsible for hiring, compensation, discipline and terminations of hourly associates in assigned department. Investigates operational errors to determine the cause and recommends corrective action where needed
- 15% Drives Results: Maintains inventory accuracy and control; reviews reports identifies area of improvement for key metrics inclouding productivity, accuracy, quality and expenses
- 15% Business Planning: Coordinats and monitors operations with the functional area to ensure performance production rates are consistent with business plan and pattern, reducing irregularities and damages. Reviews reports and business metrics to analyze and plan staffing needs for optimimum department operations
- 3+ years supervisory experience in a related field
228
Maintenance Supervisor Resume Examples & Samples
- Bachelor of Science degree in Electrical Engineering or Diploma
- Maintain a high level of knowledge which will enhance guest experience
- Demonstrate a service attitude that exceeds expectations
- Take appropriate action to resolve guest complaints promptly
229
Maintenance Supervisor Resume Examples & Samples
- Supervise all mechanical personnel and to assist and train as required
- Manage the manpower to ensure adherence to schedule and the meeting of deadlines
- Coordinate equipment set ups, repairs and installation to meet customers’ requirements
- Assure compliance to GMP’s, SOP’s, FDA, DEA and OSHA rules and regulations
- Interact with all customers and management to achieve objectives
- Use of CMMS system to organize, execute, document and trend all equipment related activities
- Able to balance multiple issues simultaneously in a fast pace environment
- Drive accountability for all PMs in accordance with required timeframe’s
- Utilize CMMS system to drive TPM excellence and continuous improvement initiatives
- Oversee all mechanical/maintenance and electrical inventory management in conjunction with ERP system
- Integral SME for new equipment/facility assets as needed
- Train mechanical and facility staff on ERP system and perform frequent refresher trainings
- Identify and assist in resolving mechanical/facilities/electrical related down time and support Reliable Supply mindset and culture
- Ability to troubleshoot and repair both major and minor pieces of packaging and labelling equipment using problem-solving techniques
- Ability to troubleshoot facilities/HVAC/Electrical and other infrastructure equipment using problem solving techniques
- Must be able to manage third party contractors working on site
- Working knowledge of GMP shop floor protocol and practices
- Experience in troubleshooting electrical, pneumatic, mechanical or PLCs as needed
- Knowledge to train and execute use of numerous tools and equipment in the servicing of OE/Encap/Packaging and labelling equipment
- Needs strong Lean/Six Sigma/Opex mindset and should be detail oriented and well organized
- Must be computer literate
- Must have ERP working knowledge
- Must have experience in a highly customer facing environment
- Advanced software skills: Microsoft Office (PowerPoint, Excel, and Word)
- Union supervisory experience is preferred
- Ability to be self-motivated, process oriented and customer focused
- Professional demeanor and the ability to interact with internal/external customers in a positive and professional manner at all times
- Must be a team player and willing to participate in “task teams” to accomplish projects as needed
- Ability to prioritize and multitask, pay attention to detail, work under pressure and meet tight time lines
- Must be willing to work overtime as needed
- Ability to lift 50 pounds or more
230
Engineering & Maintenance Supervisor Resume Examples & Samples
- Supervises maintenance team providing 24 hours maintenance coverage including equipment breakdown repair, preventative maintenance and associated systems, management and control of maintenance costs, management of parts, and proper utilization of CMMS
- Ensure that maintenance assignments are carried out in an efficient and safe manner. Troubleshoot plant and equipment. Supervise maintenance staff directly
- Set-up, maintain and be responsible for PM systems, inspection routines, job scheduling, staff training, identification of plant improvement plans including efficiency and yield
- Control maintenance expenditure in a cost-effective way according to the site budget for site repairs, resources, direct labor, and overtime
- Manage small to medium projects aimed at asset improvement/utilization, safety, and equipment reliability, utilizing process and project engineering skill sets
- Organize and plan maintenance work assignments appropriately and at the appropriate time
- Champion Safety objectives. Strive for zero incidents and ensure a people centered safety culture exists within the department
- Ensure compliance with Wrigley policies, GMP’s, and government regulations and policies
- Develop and/or executes effective training plans to further develop team members skills and knowledge
- Maintain open communications and share important plant information to all team members
- Identify and pursue continuous improvement opportunities to reduce manufacturing costs in the production areas
- Monitors and assists in the development of the annual capital project forecast, maintenance and repair budgets, and monitors work to ensure budgets are met
- Manages the day to day maintenance support of production, maintaining close communication with the Operational Team Leaders and Cell Leads to assure productivity of the machinery and equipment; responsible for scheduled and unscheduled maintenance overtime including scheduling shift work to resolve recurring problems
- Perform various other assignments as requested by the Maintenance Manager
- 2) 5+ years of experience in a progressive, technical leadership capacity working in a manufacturing/industrial environment
- 2) Experience in a high performance, self-managed environment, with a working knowledge and understanding of production management, cost, quality, safety, and personnel
- 3) Experience with operating within a formalized Continuous Improvement Environment (TPM, Lean Manufacturing)
- 4) Demonstrated ability to plan, organize and lead work teams
- 2) Maintenance and trouble-shooting of PLC’s, high-speed packaging equipment, electric/electronic systems
- 3) Experience with SAP
- 2) Clear ability to relate to and motivate people and effectively train
- 3) Outstanding analytical and problem-solving skills
- 4) Excellent written and oral communication skills
- 5) Competencies: Conflict Management, Priority Setting, Developing Direct Reports & Others, Problem Solving, and Decision Quality
- 6) Excellent written and oral communication skills
- 7) Proficient in MS Office and SAP
231
Maintenance Supervisor Resume Examples & Samples
- Actively lead, train, and develop maintenance personnel
- Meet and or exceed plant maintenance goals/objectives
- Plan and manage resources to meet maintenance and production plans and goals
- Manage Lean System Team training/facilitation and leadership
- Manage daily work activity conformance to quality and GMP/SQF/HAACP standards
- Maintain maintenance staffing and coverage schedules
- Actively attract, train, develop & retain effective personnel to ensure an efficient, motivated, and muti-skilled workforce
- Manage cross-functional team capability and capacity
- Ensure a safe working environment. Encourage personnel to work safely, preventing injuries and lost time
232
Maintenance Supervisor Resume Examples & Samples
- 35% Development and supervision of direct and indirect reports (coaching, Performance Management Plans (PMP's). Work with peers at location in establishing consistent personnel policies. Lead department/area in a manner that results in an engaged and safe environment. Provide leadership, organization, and communication to the department; ensure structure, training, and a team that operates as a high performance work team
- 20% Key member of the maintenance leadership team. Will develop deep technical knowledge of the department. Assist in project selection and implementation including assisting other members to accomplish the goals of the department to align with the site business plan. Will develop and implement strategies to identify, prioritize, and implement proactive maintenance and asset reliability improvement processes and projects across the facility
- 15% Support and lead the facility to use maintenance and reliability principles to improve the facility costs and productivity. Focus will be on creating a zero injury culture, food safety, environmental compliance, and reliability
- 15% Ensure that all work is done in compliance with federal, provincial and local regulations and/or Cargill requirements
- 10% Troubleshooting of equipment failures through root cause analysis with the goal of improving asset reliability and integrity
- 5% Daily management of the CMMS related to core job function and any other duties as assigned including purchasing of parts, rentals and equipment
- Bachelor’s degree OR High School diploma or GED and a minimum 3 years technical/plant production experience in lieu of degree
- Leadership: A demonstrated ability to lead people and get results through others
- Willingness/ability to work in a challenging and physical production/industrial environment
- Ability to communicate effectively both verbal and written within multiple levels; both internal and external
- Ability to take off-hour calls and rotate on call accountability with facility staff as needed
- Ability to apply Cargill's policies and procedures in the areas of safety and environmental
233
Mobile Maintenance Supervisor Resume Examples & Samples
- Plan, inspect and follow up on weekly activities for the team, in terms of corrective maintenance, preventative maintenance, modification and improvement jobs
- Ensure through inspection and follow up, that employees adhere to procedures, rules and regulation put in place
- Lead by example and encourage, adherence to Agnico Eagle’s Health and Safety Code of Conduct
- Respect the allocated budget and control cost for the department by following up with employees and maintaining awareness
- Plan, organize and facilitate the safety meetings and shop meetings, as well as following up on questions from previous meetings
- Work relations with the team (participate in recruitment, employees’ files, performance appraisals, disciplinary measures, and follow up)
- Advise, participate in and follow up on training required for each team member
- Professional diploma in heavy equipment mechanics or power mechanics or equivalent
- Red Seal or Journeyman certification
- 5 + years of experience, with 2+ years as a Supervisor
- Must have mining industry experience, mobile, surface and underground equipment
- Computer literate with Microsoft Office Suite
- JDE would be considered an asset
- Must have advance English language skills, written and spoken
234
Maintenance Supervisor Resume Examples & Samples
- Supervise both facilities and equipment in a cGMP environment with multiple sites
- Adhere to and monitor department budget and assist in the selection of capital expenditures to ensure a cost efficient
- Operation
- Maintain, monitor and recommend adequate spare parts to support operations
- Ensure staff is properly trained & competent in all the technical aspects of their positions
- Promote and maintain a safe work environment
- Support and maintain a PM program for both facilities & equipment in a multi-site environment
- Establish staffing and distribute workload so as to deliver maximum results
- Maintain two way dialog with direct reports on work and results
- Communicate company and departmental goals and objectives assuring that these are clearly understood by the shift
- Support company's long term growth and health
- Implements IQ/OQ for equipment installation
- Display and possess exceptional mechanical & electrical aptitude
- Understand PLC functionality
- Good coaching and teaching skills
- 3 years as a Maintenance Supervisor
- 1 year experience working in a cGMP environment
- BS in an Engineering discipline
- Machine building and or fabrication
235
Maintenance Supervisor, Clark Resume Examples & Samples
- Engineering degree or technical school training preferred or relevant work experience
- 5 - 10 years maintenance experience in manufacturing environment
- Good understanding or mechanical and electrical systems
- Experience predictive/preventive maintenance programs
- Strong computer application skills,
- Budget planning and managing
- Known to be an inspiring leader cascading the vision of the organization
236
Maintenance Supervisor Resume Examples & Samples
- Provide first line leadership for the plant maintenance team responsible for asset care
- Responsible for predictive and preventive maintenance, maintenance repair and installation of equipment and manufacturing operations to ensure continuous production operations
- Maintenance Planner duties to included
- 4 year degree from an accredited institution
- 3+ years maintenance experience in manufacturing environment
- Solid understanding of mechanical and electrical systems
- Experience with TPM and/or Lean initiatives
- Experience with predictive/preventive maintenance programs
- Strong computer application skills
237
Maintenance Supervisor Resume Examples & Samples
- Plans, schedules, and directs staff under the direction of the maintenance manager and external contractors in the mechanical maintenance of buildings and grounds
- Assists development of, and maintains an operating budget to ensure that such maintenance is carried out on a cost-effective basis. To ensure that such facilities remain operational, oversees the regular maintenance of heating, ventilating, air conditioning, and other facilities
- Maintains and assists in the development of new department and company standards Develops and implements short and long term goals for the department in coordination with corporate management
- Maintains and monitors department operating budget to ensure expenses are within established budgetary allocations and provides explanations for all variances
- Manage an expense budget for repairs, maintenance, overtime, and inventory for building mechanical, electrical and plumbing equipment, and automation equipment
- Trade school degree and a master level skill in a relevant trade with any applicable licensing
- 8+ years experience in a mechanical trade
- 3+ years previous supervisory/management experience in a related trade environment
238
Maintenance Supervisor Resume Examples & Samples
- Ensure that all jobs are performed safely
- Assist with personnel assignments
- Schedule work in a manner that maximizes productivity and sees that work is executed as scheduled
- Follow up on jobs to determine progress and status of the daily work
- Communicate daily job status reports to Planner/Scheduler, indicating those to be completed by the end of the shift and those expected to carry over
- Provide clarification of Work Orders or Work Request lacking sufficient information to the Planner/Scheduler
- Coordinate and complete emergency/urgent jobs in an efficient and safe manner
- Assist in coordination of plant Safety Programs
- Seek recommendations for improving work procedures and plans. Utilize employee engagement to maximize all resources
- Determine root causes of major repairs and implement the necessary corrective action to prevent recurrence
- Maintain open communications with all departments and personnel in regards to safety, job efficiency, product quality, customer service, and housekeeping
- Maintain maintenance shop and equipment (5S)
- Develop training needs for assigned craftsmen
- Ensure the assigned craftsmen understand their goals and objectives, and how they are contributing towards them
239
Industrial Maintenance Supervisor Resume Examples & Samples
- Manage the preventative maintenance program and ensure frequency compliance on all scheduled equipment checks
- Oversee all outside contractor work as required
- Participate in the budget process with the Maintenance Team Leader
- Supervise, develop and train maintenance teams conduct timely and effective performance reviews, hold regularly scheduled shift meetings to identify issues and set up action plans to resolve
- Maintain organization and sanitation of maintenance parts, tools and departmental area
- Insure all PJFS safety programs are followed in the department and participate in quarterly safety audits. Promote safety awareness through training, communications, and participation in the Plant Safety Committee
- Maintain accurate and complete departmental records for the COGZ system, vendor performance, team member files and P.O.’s
- Replace the Maintenance team leader in his/her absence when required
- Ability to effectively communicate and give direction verbally and in writing in English required
- Must have demonstrated technical skills/certification in general maintenance, HVAC/refrigeration, electrical, plumbing and hydraulics
- Must be able to read and interpret mechanical drawings, construction drawings, machine manuals, electrical blueprints/electrical schematics
- Experience with preventative maintenance programs preferred
- PeopleSoft and Kronos application experience preferred
- High school diploma or equivalent is required
- College, trade school or business management development is preferred
- Minimum two (2) years progressive supervisory experience required, preferably in industrial maintenance
240
Maintenance Supervisor Resume Examples & Samples
- Work with manufacturing superintendent for the off shift to assess priorities of priority one work orders for and assign them to off shift maintenance technicians
- Coordinate corrective work priorities for 2nd or 3rd shift maintenance activities
- Assist maintenance personnel troubleshooting equipment and make decisions that will minimize the downtime of equipment
- Assist predictive, preventative and corrective maintenance efforts required to ensure efficient, reliable and uninterrupted plant operations
- Ensure employee health and safety. Monitor and drive improvements in OSHA incident rates
- Analyze/trend maintenance issues to drive improvement with maintenance activities
- Conduct root cause analyses for major and repeated equipment issues
- Maintain quality presence in facility to minimize discrepancies and promote process compliance and accurate documentation
- Maintain communication between department management and department personnel. Maintain clear communication with the Director of Facilities Engineering and Maintenance regarding goals, projects, planning, and overall performance of the Maintenance & Facilities group for the second or third shift
- Provide the highest level of service to our internal customers, i.e. manufacturing group
- Assist with performance reviews of personnel
- Minimum High School Diploma. Associate’s or Bachelor’s Degree degree in Engineering or closely related scientific/technical discipline is strongly preferred
- Minimum 7 years of maintenance experience preferably in an FDA regulated manufacturing facility – pharmaceutical, biologics, biotech, or medical device industry
- Strong knowledge of cGMPs, FDA regulations, and industry guidelines, as well as international regulatory guidelines
- Demonstrated strong mechanical skills with sound ability to troubleshoot all manufacturing equipment
- Demonstrated leadership skills with ability to motivate, guide, train, coach and develop subordinates
- Excellent verbal and written communication. Must be able to read, write, and speak English. Spanish speaking is a plus
- Must have strong technical writing skills
- Strong interpersonal skills with ability to interact with all levels of personnel in a professional manner
- Ability to manage multiple projects simultaneously, meet deadlines, and handle an ever changing, fast paced critical work environment
- Strong organizational, analytical and problem-solving skills. Ability to analyze details and perform structured decision-making on a daily basis
- Ability to work well with others in a TEAM environment
- Good computer skills with knowledge of MS Office, particularly Outlook, Word, Excel and PowerPoint
- Ability to work at a computer and view video display terminal less than 18” away from face for extended periods - up to four (4) hours at a time
- Ability to read and review documents for extended periods - up to four (4) hours at a time
- Ability to stand or sit for extended periods - up to four (4) hours at a time
- Ability to gown and enter into an aseptic, cold (65˚F) environment
- This job description is accurate at the date of publication and may change over time. It is not intended as an exhaustive description of the job. Other duties may be assigned and qualifications required may change
241
Maintenance Supervisor Resume Examples & Samples
- Lead shift start up meeting to communicate daily/shift goal of facility and work group(s). Devise, communicate, and implement plans to obtain operational goals. Work with and motivate employees to ensure goal achievement. Provide progress or constraint updates to management
- Hire, train and supervise leads and hourly employees in the assigned work group(s)
- Provide leadership for employees through in depth training and continuous review of employee understanding of policies, procedures, and processes. Create a productive work environment through effective communication, coaching, motivating, and leading by example
- Support and aid in the development of system and process training for employees in the work group(s). Perform administrative functions to include tracking of time, attendance, and performance feedback
- Instruct and enforce location safety management plans, training, and processes
- Identify and/or solve operational issues with the account(s) by implementing continuous improvement and LEAN initiatives, to strengthen team unity, goals, productivity, and results
- Assign employees to individual tasks and ensure required tools are available
242
Maintenance Supervisor Resume Examples & Samples
- Quality assurance Administrative duties
- Ensure functional area meets all productivity goals and objectives
- Safety management and reporting
243
Maintenance Supervisor Resume Examples & Samples
- Coordinates and supervises the daily activities of non-exempt and/or hourly employees
- Decisions are guided by policies, procedures and business plan; receives guidance and oversight from manager
- Focuses on assignment of work, scheduling of work, monitoring of work as it is being done, reviewing results for timeliness, quality and cost effectiveness
- Facilities - Manages a group responsible for facilities services such as property management, asset management and general facility services
- Oversees the delivery of services that support the physical workplace; to include design engineering, space planning and general facility services
- Develops plans/strategies, third party relationships and specific programs in order to achieve business objectives
- Manages building maintenance technician(s), maintenance assistant(s), and administrative support. Equipment - Manages the work of skilled craft (e.g., electricians, plumbers, painters) workers or vendors within a plant facility. Work involves equipment, building, and facilities maintenance
- Has the ability to read drawings
- Ability to read shop math
- Has ability to use and operate equipment
- Ability to function as a team member
- Establish and maintain effective working relationship with supervisor, co-workers and customers
- Safely and efficiently performs all essential functions
244
Maintenance Supervisor Resume Examples & Samples
- Performing applicable maintenance activities
- Developing preventative maintenance programs
- Applying basic operational principles and practices
- Developing maintenance operating policies and procedures
- Developing and analyzing applicable maintenance reports
- Working with other functions and supervisors
- Investigating and resolving maintenance problems
- Ensuring compliance with department policies and procedures and applicable laws, rules, and regulations
- PC skills; Microsoft Office applications (Word, Excel, PowerPoint, Outlook); and other applicable applications
- Communicating with co-workers to provide and receive direction
245
Maintenance Supervisor Resume Examples & Samples
- Supervise and assist the maintenance team in repairing and performing PM activities on conveyors, pumps, mixers, operating motorized equipment, completion of paperwork
- Ensure the safety of all employees and that all employees are following all safety practices implemented
- Conduct daily safety training
- Adhere to safety standards regarding personal protective equipment which will include, but not limited to, wearing safety footwear, gloves, tyvek suits, eye/face shields, and a full face respirator as required
- Ensure that quality requirements are met while working in a safe manner compliant with company employment guidelines
- Conduct training and verify compliance of quality processes and procedures
- Meet demands of the production schedules by ensuring facility is properly staffed and adequate supervision is in place at all times
- Responsible for prioritizing work flow to maximize efficiency and ensure adequate quantities of consumable materials obtained
- Required to interface with customers
- Issue materials to operating groups as requested; assist requesting personnel in identifying required material though use of the computer system or order acknowledgement paper work
- Complete all required paperwork and reports, including recording material usage, production hours/labor, inventory management, etc
- Responsible for performance staffing/scheduling
- Ensure all hourly employees follow Company policies and discipline when deemed necessary
- Assist with overall development and training needs for the personnel to improve skill level, involvement, value, and morale
- Must be able to work with other departments to ensure productivity requirements are achieved
- Maintain good housekeeping of work areas
- No travel or relocation expenses considered
- Must have 1 – 3 years of supervisory experience
- Ability to apply commonsense understanding to carry out instructions furnished in written, oral, or diagram form
- Must be computer literate, with a demonstrated working knowledge of Excel and Word
- Forklift license required, or the ability to obtain one within 10 days of job acceptance/placement
- Experience operating a forklift and forklift clamps in warehouse environment is preferred
- Required to follow detailed instructions
- While performing the duties of this job, the employee is regularly required to stand, walk, stoop, squat, kneel and crouch
- The employee frequently is required to use hands to finger, handle, or feel objects, tools or controls; reach with hands and arms; talk and hear; and climb or balance
- The employee must regularly lift on a daily basis and/or move up to 75 pounds
- Specific vision abilities required by this job include close vision, distance vision, peripheral vision, depth perception, and the ability to adjust focus
- The employee must be able to wear all required PPE including, but not limited to wearing safety footwear, gloves, tyvek suits, eye/face shields, and a full face respirator (must pass a pulmonary function test, i.e. - respirator physical), as required
- While performing the duties of this job, the employee regularly works near moving mechanical parts
- The current work environment is currently not temperature controlled
246
Maintenance Supervisor Resume Examples & Samples
- Plan and implement effective procedures utilizing total productive maintenance (TPM) strategies for the production & ancillary equipment ensuring asset reliability where all equipment, machinery and systems are in an "up and running" state at all times
- Work cooperatively with the Management Team in a player/coach capacity; work with and operational customers to develop "best practices" for maintenance activities
- Utilize the maintenance systems to plan, schedule and document all maintenance activities
- Schedule and direct the daily activities of production maintenance staff to ensure completion of assigned, planned and unplanned work
- Work with Plant Leadership to continually improve systems and equipment
- Understands the internal and external customers for this position and strives to provide 100% satisfaction at all times
- Work with vendors, suppliers and contractors to establish quality standards and favorable pricing
- Oversee the maintenance of all business critical records, documents and blueprints for maintenance assets as well as all associated documentation relating to all production equipment and ancillary systems
- Adhere to maintenance budget related to the assigned areas
- Ensure all maintenance related projects and work are in compliance with standards set by Boart Longyear, OSHA and any additional governing agencies by which we manage our business
- Drive a maintenance culture that is focused on continuous improvement, positive morale and exceptional levels of customer service
- Demonstrate Boart Longyear leadership behaviors focusing on quality and results
- Provide formal and informal support and coaching to direct reports as needed to improve performance and/or generate opportunities for further growth and development
- Drive safety culture and accountability for maintenance team goals
- Maintain awareness of, and compliance with, all applicable Boart Longyear policies
- Performs other duties as assigned by management
- Perform daily work in a graphite machining environment – high content of graphite powder
247
E&i Maintenance Supervisor Resume Examples & Samples
- High school diploma or GED required. Associate’s Degree or Bachelor’s Degree in Maintenance or related field preferred
- Minimum seven years E&I experience in a tissue or paper mill required
- Prior experience in a leadership position with supervisory experience required
- Experience working in a union environment preferred
- Intermediate proficiency in Microsoft Word, Excel, Access and Outlook required
- Advanced proficiency in JDEdwards required
- Must have good E&I and troubleshooting skills
- Must be able to supervise employees
- Must possess good verbal and written communication skills
248
Maintenance Supervisor Resume Examples & Samples
- Performs preventative maintenance and maintains maintenance records as instructed
- Perform building and equipment repairs, as per work order requests
- Performs fire safety equipment tests under the guidance of the Regional Maintenance Director
- Inspects building systems as scheduled and log findings
- Coordinate maintenance services with department managers to ensure building and equipment performance without interruption
- Performs basic carpentry, drywall, flooring and painting as required to maintain favorable building appearance
- Maintains the building in good repair and in compliance with local, state and federal laws
- Follows established safety rules and Policies & Procedures of building
- Order equipment and supplies as necessary; and maintain proper records of repairs and purchases
- May be required to drive for company business with either company vehicle personal vehicle
- Maintain resident confidentiality; treat residents with kindness, dignity and respect
- Must have demonstrated HVAC repair experience
- Intermediate skillset in electric and plumbing repair highly desired
- Knowledge of water heaters, generators commercial kitchen equipment and refrigeration would be a plus but not required
- Knowledge of building codes, safety regulations and blueprint interpretation
- Completion of High School/GED education or otherwise show ability to read, write and follow oral and written directions
- Positive attitude toward the elderly
249
Maintenance Supervisor Resume Examples & Samples
- Supervising and coordinating the maintenance staff
- Performing or assigning repairs and maintenance work
- Performing or assigning carpentry, plumbing or electrical duties
- Communicating with contractors and vendors
250
Maintenance Supervisor Resume Examples & Samples
- May be hands on with a variety of power tools in repairing, refurbishing, cleaning, installing work station cubicals, or repairing any structural element (walls, floors, windows) as needed
- Must be able to read and interpret blue prints or schematics to ensure assembly or repair is accurate
- Must have working knowledge in all general maintenance components, painting, plumbing, HVAC to troubleshoot and review quality of service
- Supervise day to day functions of crew members to ensure accuracy and completeness of assigned work activities. Provides input into hiring, performance reviews and any other personnel activities under the purview of the specific Facilities Manager
- Ensures all equipment utilized is in good working condition; makes recommendations for equipment repair and maintenance
- Minimum of 3 years’ related work experience with at least one year in lead role
- Must have valid driver’s license and clean driving record
- Good interpersonal skills with the ability to work cohesively with team members and facilities management
- Knowledge of safety and security precautions and occupational hazards with a willingness to follow safety guidelines and/or precautions
- Ability to interact with all GCU personnel with friendly, positive attitude and ensure delivery of service meets expectations both individually and according to GCU standards; serve as model of behavior for all team members
- Willingness to work weekends, evenings, holidays as necessary