Manager, Continuous Improvement Resume Samples
4.9
(116 votes) for
Manager, Continuous Improvement Resume Samples
The Guide To Resume Tailoring
Guide the recruiter to the conclusion that you are the best candidate for the manager, continuous improvement job. It’s actually very simple. Tailor your resume by picking relevant responsibilities from the examples below and then add your accomplishments. This way, you can position yourself in the best way to get hired.
Craft your perfect resume by picking job responsibilities written by professional recruiters
Pick from the thousands of curated job responsibilities used by the leading companies
Tailor your resume & cover letter with wording that best fits for each job you apply
Resume Builder
Create a Resume in Minutes with Professional Resume Templates
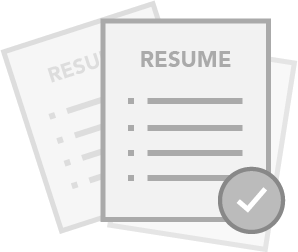
CHOOSE THE BEST TEMPLATE
- Choose from 15 Leading Templates. No need to think about design details.
USE PRE-WRITTEN BULLET POINTS
- Select from thousands of pre-written bullet points.
SAVE YOUR DOCUMENTS IN PDF FILES
- Instantly download in PDF format or share a custom link.
AG
A Gaylord
Andrew
Gaylord
784 Lawrence Plains
New York
NY
+1 (555) 370 7357
784 Lawrence Plains
New York
NY
Phone
p
+1 (555) 370 7357
Experience
Experience
Houston, TX
Manager Continuous Improvement
Houston, TX
Wiza-Farrell
Houston, TX
Manager Continuous Improvement
- Evaluates projects and directs Project Managers and Facilitators to make corrective actions as well as improvements
- Networks with other CI Managers and the Programme and Project Management Office (PPMO)
- Manage the training, development and succession planning for the direct reports
- Manage project improvement initiatives with the larger team on a day to day basis, within deadlines set during scoping
- Manage the implementation of post mortem program monitoring and track key metrics to measure success and foster continuous improvement
- Provide oversight and technical expertise during the development of new strategic manufacturing platforms and products
- Work with other members of the team to distribute workload and define project expectations
San Francisco, CA
Manager, Continuous Improvement
San Francisco, CA
Quigley-Waelchi
San Francisco, CA
Manager, Continuous Improvement
- Coaching team members in their projects using lean methodology, and facilitating project tollgate reviews
- Provide mentoring, coaching and training to support the use of continuous improvement methodologies and tools
- Using Customer Excellence methodologies, support sales and marketing leadership in their pursuit of outstanding commercial performance focused on growth
- Leading detailed process analysis using statistical tools
- Govern customer’s specific business scope, end-to-end business processes, operating work instructions, billing procedures, etc
- Display a high level of critical thinking in bringing successful resolution to high –impact, complex and /or cross-functional problems
- This position is responsible for problem solving, risk mitigation and contingency planning at a global clinical operations level
present
Chicago, IL
Senior Manager, Continuous Improvement
Chicago, IL
Powlowski, Wintheiser and Ruecker
present
Chicago, IL
Senior Manager, Continuous Improvement
present
- Manage the process that identifies and implements significant Continuous Improvement opportunities to support division and corporate objectives
- Ensure the integrity of performance systems and reports
- Lean and Six Sigma Manage lean office and implements lean principles
- Plan, lead and facilitate Kaizen and Six Sigma teams
- Complete event planning, perform pre-work, facilitate teams and support event closure and follow up
- Develop standards of performance based on process innovation and best-in-class practices Manage the preparation, development and publishing of
- Continuous Improvement materials to include detailed process documentation, process maps, and training (webinar) materials
Education
Education
Bachelor’s Degree in Field With
Bachelor’s Degree in Field With
Northern Illinois University
Bachelor’s Degree in Field With
Skills
Skills
- Excellent analytical skills with strong working knowledge of problem solving, root cause analysis, and associated solution implementation
- Strong knowledge of Color control instruments and color tolerance
- Ability to maintain favorable employee morale
- Strong interpersonal skills and ability to motivate people
- Able to work under deadlines and handle multiple and detail-oriented tasks
- Discipline and basic knowledge of related disciplines requiring conceptual and practical expertise
- Proven project management skills to ensure on-time, high-quality deliverables
- Strong leadership skills with proven ability to facilitate cross-functional teams
- Knowledge of and experience with FDA and EU PV regulations
- Leading detailed process analysis using statistical tools
15 Manager, Continuous Improvement resume templates
Read our complete resume writing guides
1
Senior Manager, Continuous Improvement Resume Examples & Samples
- The candidate must have a solid track record of holistic cost analysis and technology program management
- 8 or more years of progressive experience in cost management
- Experience in project and program management is required, including, but not limited to
- Experience with process re-engineering
- Experience working with business executives on change management
- The candidate must have proven experience in working in a matrix environment and managing multiple stakeholders, and possess leadership presence/gravitas
- High-Energy
- Understands importance of service
- Passionate about maximizing cost performance
- Willing to be creatively disruptive
- Drives best practices and application of cost diagnostics
- Engages in collaborative accumulation and prioritization
- Demonstrated tenacity
- Excellent analytical, diagnostic and problem solving skills
- Excellent verbal and written communication skills, to technical and non-technical audiences
- Strong commitment to program success metrics
- Ability to share a vision and convince others to embrace and embed in their organizations
- Strong planning, scheduling, and organization skills
- Work effectively in a team environment, and with remote teams and vendors
- Lean/Six-Sigma experience
2
Manager, Continuous Improvement Resume Examples & Samples
- As an expert in the use of the Lean tools with a comprehensive knowledge of the philosophy, utilize PDCA (Plan-Do-Check-Act) and DMAIC (Define-Measure-Analyze-Improve-Control) methodologies to successfully lead and manage completion of continuous improvement projects within a given timeframe to meet the department or facility goals in productivity, quality, efficiency, and safety
- Lead exempt and non-exempt employees assigned to CI teams in LEAN disciplines and processes to accomplish assigned stated CI projects. Responsible and accountable for CI team meeting or exceeding project goals
- Apply E3 concept (Engage, Enable, Empower) within project activities to ensure project sustainability with the work force and management teams
- Identify LEAN/CI needs of assigned departmetns including but not limited to Manufacturing, Distribution, Tech Services, Warehouse, Office, and others, and develop implementation plans with department and CI directors
- Provide monthly report out to Process Improvement Director on completed projects and assist in presentation to plant manager and other leaders as required
- Prepare and deliver Lean/CI training to employees
3
Manager Continuous Improvement Resume Examples & Samples
- As an expert in the use of the Lean tools with a comprehensive knowledge of the philosophy, utilize PDCA (Plan-Do-Check-Act) and DMAIC (Define-Measure-Analyze-Improve-Control) methodologies to successfully lead and manage completion of continuous improvement projects within a given timeframe to meet the department or facility goals in productivity, quality, efficiency, and safety. (40%)
- Lead exempt and non-exempt employees assigned to CI teams in LEAN disciplines and processes to accomplish assigned stated CI projects. Responsible and accountable for CI team meeting or exceeding project goals. (20%)
- Identify LEAN/CI needs of assigned departments including but not limited to Manufacturing, Distribution, Tech Services, Warehouse, Office, and others, and develop implementation plans with department and CI directors. (10%)
- Provide monthly report out to Process Improvement Director on completed projects and assist in presentation to plant manager and other leaders as required. (10%)
- Prepare and deliver Lean/CI training to employees. (10%)
- Demonstrated successful project management capabilities in a LEAN/CI environment, measured through KPI metrics and results
- Strong attention to detail and strong organizational skills
- Black Belt Six Sigma Certification preferred
4
Manager, Continuous Improvement Resume Examples & Samples
- To identify and execute cost reduction programs/projects for the Operations division
- Strong leadership demonstration in areas of change management and accountability
- Partner with CI Leads and facilities to identify improvement projects throughout Operations
- Monitor and Develop Operations metrics to identify opportunities for 2017 and beyond
- Coordinate major initiatives across the supply chain to insure optimum cost. This coordination will include, but not be limited to, purchasing, distribution, and manufacturing
- Able to coach and mentor Lean Six Sigma projects throughout Operations
- Ability to replicate best practices - sell the organization on the change associated with the proposals
5
Manager Continuous Improvement Resume Examples & Samples
- Ensuring the full compliance to OSHA and cGMP regulations at all times and working in concert with a cross functional team to ensure that the CI, Technology and Engineering projects meet the required standards of the internal and external customers
- Organizing, managing, developing and implementing project plans, construction projects, designs, assembly of equipment, processes, and systems to ensure timely project completion, in compliance with regulatory agency requirements, internal company standards and current industry practices
- Recruit top talent with every hiring opportunity and motivate/develop members of the department to be key leaders within the organization. Build and sustain employee engagement by creating a culture of efficient execution and an environment in which individuals and team can excel and continuously improve
- Actively influence and participate in the site leadership team and establish effective cross-functional leadership relationships and presence
- Drive implementation of CI technology and engineering projects within budgets and timelines and implement new pharmaceutical processing technologies
- Plan investments in Plant/Personnel/Equipment and oversee the departmental budget and headcount, as well as the site’s capital and expense budgets
- Develop and regularly update the strategic capital improvement plan including site master plan
- Maximize the success rate for production operations by instituting programs to minimize mechanical failure and enhance equipment performance
- Direct responsibility for capital projects, cost control, project schedules, and direct/indirect expenses
- Support procurement strategy, equipment expediting/projects and FAT/SAT/IOQ/PQ
- Construction Management in compliance with all applicable safety, regulatory and legal requirement
- Ensure that appropriate training of all personnel for equipment, process and facility safety and operations is maintained and up-to-date
- Experience in maintaining regulatory compliance thru audits, validation, change management, risk assessments, qualified drawings, corrective action plans, FMEA, and deviation support
- Utilize, promote and drive Operational Excellence, Six Sigma & Lean methodologies to all work flows with ability to run Kaizen Events
- Provide oversight and technical expertise during the development of new strategic manufacturing platforms and products
- Provide project engineering support on major investment initiatives and own the CAPEX process
- Develop budget proposals. Control charges against approved budget and monitor/report expenditures
- Manage the training, development and succession planning for the direct reports
- Substantial operational engineering experience
- Full understanding of pharmaceutical supply chain
- Relevant legal standards and compliance systems
- Knowledge of Quality Assurance (QA) and Environmental, Health & Safety (EHS) standards
- Demonstrated application of improvement methods such as LEAN & Six Sigma
- Green Belt or Black Belt Certification a plus
- Experience working to regulatory standards: FDA, Good Engineering Practice (GEP), Good Manufacturing Procedures (GMP) and Good Documentation Procedures (GDP)
- Experienced working on all aspects of capital projects, including budgeting, design, construction, validation, startup and ongoing operations
- Exceptional project management skills (including mastery of Microsoft project suite, Microsoft Project and other applicable systems
6
Manager, Continuous Improvement Resume Examples & Samples
- Manages the coordination of the activities related to the continuous improvement of global PV processes with responsibility for results, including costs, quality and effectiveness, including leadership of designated cross-functional teams tasked with development and maintenance of PV processes and conventions
- Manages updates to the safety database Data Entry Manual
- Fulfills the safety database Business Owner role, including user requirement definition based on business processes, review/approval of validation documentation and coordinating user acceptance testing, in collaboration with functional leads
- Develops and maintains the departmental business continuity plan, partnering with IT to ensure BCP is tested on a regular basis
- Manages / facilitates root cause analysis based on trends or individual deviations
- Manages / facilitates corrective/preventive actions development as a result of inspection and audit outcomes (activity is done in partnership with R&D QA)
- Participate in regulatory intelligence of GxP requirements to ensure department is current in regulatory expectations
- Knowledge of and experience with FDA and EU PV regulations
- In depth knowledge of case processing, aggregate reporting, and safety databases, including their configuration
- Skilled at interpreting business process into user requirements
- Understanding and wide application of technical principles, theories, concepts and techniques in the area of Quality Management/Quality Improvement – Six Sigma training a plus
- Strong analytical and business communication skills
- Skilled at critical thinking and decision making
- Excels at planning and organizing
- Passionate about collaboration and delivering results as a team
- Receives assignments in the form of objectives and determines how to use resources to meet schedules and goals
- BS/BA degree in related discipline and six years of related experience; or,
- MS/MA degree in related discipline and four years of related experience; or,
- Equivalent combination of education and experience in Clinical Drug Safety and Pharmacovigilance in Biotech/Pharmaceutical industry
7
Manager, Continuous Improvement Resume Examples & Samples
- Assume the lead role in the site’s TEOA process implementation – lead process improvement projects and facilitate team projects/mentor team members who are leading process improvement projects
- The TEOA Leader will be responsible for coaching the production team members in achieving the Key Performance Indicator objectives aligned with the site performance and TEOA goals
- Build strong and positive working relationships with all functional areas
- Foster the adoption of continuous improvement as a way life; creating a culture of change
- Guide the analysis of existing methods to promote effective operations through standardization, improvement, simplification, discontinuance or other methods
- Utilize Lean and Six Sigma approaches to process improvements
- Develop recommendations for business processes that ensure alignment with strategic direction; integrate business processes between multiple organizations
- Apply advanced skills to resolve complex problems not covered by existing procedures or practices independently
- Display a high level of critical thinking in bringing successful resolution to high–impact, complex and /or cross-functional problems
- Develop and utilize current and future state value stream maps to identify strategic projects and implementation plans aligned with the plant’s strategic direction
- Identification and leverage of best practices across the entire TE operation
- A history of leading change and producing documented improvements in plant costs and quality
- Experience creating a Lean or Six Sigma strategy for a manufacturing organization
- A thorough understanding and ability to use all aspects of Six Sigma as a management system: Define Measure Analyze Improve and Control (DMAIC)
- Lean Six Sigma Black Belt preferred
- Excellent communication skills both written and verbal along with coaching skills at all levels from the shop floor to top management (Strong team leader)
- Ability to develop and lead execution of strategy for transformational change & continuous improvement efforts across the site
- Ability to think strategically and execute tactically (i.e. deliver results)
- Ability to define problems, collect data, establish facts, utilize process and value stream mapping, and draw valid conclusions. Must be able to prioritize multiple tasks and manage time effectively
- Ability to effectively and efficiently lead cross functionally as well as with suppliers and customers
- Working knowledge of the manufacturing processes
- Analytically minded and data-driven. The candidate must also have a holistic overview of complex situations and deal effectively with difficult issues when they arise
- 3-5 years of professional experience with focus on production, logistics or engineering and financial knowledge. Bachelor’s Degree in Engineering or related field required
- At least 2 years of experience in leading continuous improvement activities on site level
- Experience in the automotive industry is a plus, but not a prerequisite
8
Manager, Continuous Improvement Resume Examples & Samples
- Work with Director of Global Continuous Improvement and Smithfield, RI Site Leadership Team to create a site road map for the continuous improvement program
- Collaborate with department leadership teams to develop an implementation strategy and plan for developing a continuous improvement culture and management system
- Build and drive schedules and resource requirements for the implementation of the Integrated Management System and Rapid Transformation at Smithfield, RI site for each department
- Provide coaching and mentoring at all levels of the organization in continuous improvement to execute against the site plan for continuous improvement
- Create, improve, and deploy Integrated Management System processes, systems, and tools as part of the Rapid Transformation
- Create, maintain, and deliver training to support the advancement of continuous improvement in Smithfield, RI site and other manufacturing sites as part of the continuous improvement implementation plan
- Progressive experience in manufacturing, including roles leading others and in Production, Technical or Warehouse operations preferred
- Experience working with the implementation and oversight of improvement initiatives
- Experience in root cause and/or root cause trend analysis
- Demonstrated ability to use data for creative problem solving
- Change management experience, proven success in working with people in a change program
- Behavioral flexibility - ability to explain things well in different cultures and manage relationships; it is not only CONTINUOUS IMPROVEMENT, it is the right next step to take because we value our company, etc
- Strong interpersonal skills, clear communicator, and demonstrated relationship building skills
- Talented influencer and team builder. Can form a team without official authority to do so, and motivate that team to accomplish self-directed goals
- Proficiency in, but not limited to: Microsoft Office Applications – Word, Excel, Access, PowerPoint, Outlook
- Self-Motivated with a proven record of taking the initiative
- Detail-Oriented with Excellent Oral and Written Communication Skills
- Able to work with and influence individuals throughout the organization without direct authority
- Must be able to travel up to 50% as necessary
9
Manager, Continuous Improvement Resume Examples & Samples
- Drives global, complex, cross-functional process and productivity improvement projects for Development that support the organization’s strategic objectives
- Provides tactical input on the implementation of the strategic support for process improvement initiatives for Development
- Responsible for compliance with applicable Corporate and Divisional policies and procedures
- Establishes and implements improvement methodologies and techniques to be used, governance structure, project management structure and progress reporting
- Defines a portfolio of projects to deliver high value, cross-functional productivity improvements
- Develop and assess cost, resource projections and metrics for the function
- This position is responsible for overseeing the management of projects that are cross-functional and cross-divisional, complex, have high impact and are top priority for the organization
- This role will be integral in developing the initial functional area strategy
10
Manager, Continuous Improvement Resume Examples & Samples
- Manager responsible for the facilitation, completion and implementation of process improvement initiatives that support the organizations strategic objectives
- May have direct reports and will matrix manage members participating in cross-functional process improvement initiatives to ensure projects are executed per timelines
- Supports non-complex project(s)
- Is aware of both internal and external business environments, assesses impact on the process improvement initiatives and assists in making modification as necessary
- Escalate significant issues to management and identify performance and resource gaps relative to process
- Escalate significant issues to management and identify performance and resource gaps relative to process improvement initiatives, adoption of best practices, recommends corrective actions
- Takes initiative to resolve problems and mitigate risks
- Effectively communicates project progress/ concerns and actively identifies issues that potentially impact project completion and identify potential interventions or solutions to manage the issues
- Uses process improvement methodologies and techniques, governance structure, project management structure and progress reporting to enable cross-functional teams to successfully complete a project
- This is the first level position (of 2 levels) which is responsible for the execution of cross-functional process improvement initiatives; ensuring projects are executed per timelines and support the Clinical Operation’s strategic objectives
- This position will report into a director level and may have direct reports and responsibility for matrix managing their assigned team
- This position is responsible for problem solving, risk mitigation and contingency planning at a global clinical operations level
- Assesses potential impact of non-streamlined processes on cost, compliance and re-work activities
- Bachelor’s degree (or ex-US equivalent) is required, typically in nursing or scientific field. An Associate’s degree/R.N. (or ex-US equivalent) with relevant experience is acceptable
- Must have 6+ years of Pharma-related/ clinical research related experience (and/or applicable work experience); including 2+ years (and/or applicable work experience); in clinical research demonstrating a high level of core, technical and leadership competencies through driving strategy
- Possesses good communication skills, demonstrated leadership abilities and problem solving skills
- Demonstration of successful coaching/ mentoring in a matrix environment
- Competent in application of standard business procedures (SOPs, ICH, Global Regulations, Ethics and Compliance)
11
Manager, Continuous Improvement Resume Examples & Samples
- Plans, organizes, staffs, directs and controls the day-to-day operations of the department; develops and implements policies and programs as necessary
- Develops and manages the department budget, ensures compliance and addresses variances and other budget concerns
- Managing business-wide, cross-functional projects as directed
- Coaching team members in their projects using lean methodology, and facilitating project tollgate reviews
- Facilitating project identification and completion with Champions, Process owners and project teams
- Leading detailed process analysis using statistical tools
- Performing the following internal consulting services to the satisfaction of our clients: Process mapping, Value stream mapping, process design, methods development, establishing performance standards/metrics, ROI analysis and project management
- Stimulating management thinking by tactfully challenging conventional wisdom through demonstration of the application of lean. Providing guidance and knowledge to lead the change
- Utilizing Six Sigma and Lean to lead and execute high impact process improvement projects
- Presenting data and solutions to Customers, both internal and external
- Experience in multiple supply chain functions including warehousing and distribution
- Five (5) plus years of Project Management experience
- Two (2) plus years of lean/ six sigma experience
- Experience coaching and delivering training at all levels of an organization
- Strong leadership skills with proven ability to facilitate cross-functional teams
- Excellent written and verbal communication, presentation and facilitation skills
- Proficiency with Microsoft Office applications required as well as MS Project, Minitab and Visio
- Ability to read, write and interpret information
- Ability to sit/walk/stand for up to 8 hours per day
12
Manager, Continuous Improvement Resume Examples & Samples
- Drive Lean/CI in all North America businesses
- Forges a successful relationship and partner with business leaders to assess current processes and identify process improvement opportunities both in operational and transactional environments
- Using Customer Excellence methodologies, support sales and marketing leadership in their pursuit of outstanding commercial performance focused on growth
- Determine and run Lean and Kaizen events at all facilities
- Train and develop Kaizen leaders and Lean leaders to better leverage implementation and implementation speed
- Lead/direct 6S deployment at all facilities
- Using LSS tools and activities to systematically achieve process improvements, sourcing savings and improved front end commercial performance
- Utilize Lean flow and layout to improve service operations to minimize non-value added activities and reduce repair/service Cycle Times (CT)
- Implement visual management processes into shop operations
- Delivers Key Business Metrics (KBMs) and Key Performance Indicators (KPIs) across the business
- Develop a capacity management and sharing process that encompasses all branches
- Run “Boot Camps” educational opportunities, as required
- Certification as Black Belt in Lean Six Sigma methodologies; Master Black Belt Preferred
- 10+ years of experience leading global teams and projects with at least 5 years of active LSS deployment, project and process improvement work
- Demonstrated capability of building Lean Six Sigma and Customer Excellence skills in matrix organizations
- Proven track record leading LSS projects and events using industry standard LSS tools and methodologies which achieved significant improvements to cost, quality and time
- Extensive change management experience in applying contemporary improvement tools with direct responsibility for delivering broad organizational improvements
- Positive attitude, resilient and leads by example
- Results based leadership style, managing complex projects and leveraging influencing skills across a diverse team ranging from frontline employees to senior executives
- Proven ability in strategy development, program implementation, team building, coaching and mentoring
- Strong quantitative, analytical and systemic thinking skills with ability to thoroughly synthesize information from different sources
- Functions with a high degree of autonomy while maintaining a collaborative approach
- Solid business and financial acumen
- Strong Computer skills in MS Office elements including Excel, Word, PowerPoint, Project, and Access
- Ability to travel internationally as required (approximately 50%)
13
Manager Continuous Improvement Resume Examples & Samples
- Lean Master certified and/or Six Sigma Master Belt certified
- 12+ years diverse work experience with a Bachelor’s degree in Business, Engineering or related field
- 6+ years work experience in Lean Six Sigma process application
- Trained in Lean Six Sigma Principles (5S, Waste Reduction, Error/Mistake Proofing, PDCA, Root Cause Analysis, A3 Problem Solving, Value Stream Mapping, Kaizen, Lead Time Reduction)
- Strong analytical skills and deep process orientation
- Experience in developing various process documentation (SOP, ISO, etc)
- Experience in operational performance evaluation (Efficiency/Utilization)
- Demonstrated leadership skills and experience in implementing Continuous Improvement methodologies
- Ability to influence others
14
Manager, Continuous Improvement Resume Examples & Samples
- Develop detailed work plans, schedules, project estimates, resource plans, and report out regularly on project status, issue and risks
- Participate in the development, control and revision of Standard Work Instructions (SWI) and other control documents
- Provide leadership and coaching to ensure participation and buy-in from employees in order to successfully implement process improvements resulting from Kaizen event and other CI activities
- Facilitate/lead Kaizen events and employ other lean methodologies to achieve business results
- Ensure that CI and WCPOS maturity project plans are developed and maintained, rolling up to master program plans and tracking documents
- Develop, train, and mentor non-CI team resources to write Standard Work Instructions (SWI)
- Bachelor’s degree in business, engineering or related field
- 5 – 8 years experience implementing contemporary process improvement methodologies in an Operations environment, preferably in transactional, high volume, and high mix environment
- Excellent verbal and written communication skills; Proficient in MS Office, Project, Visio, Minitab preferred
- Facilitating / Leading Kaizen Events in different business environments; Proficient with Lean and Six Sigma tools and methodology; 6S, Visual Mgmt, VSM, Kaizen, A3, SWI, FMEA, etc.; Developing Quality Management Systems and corresponding control documents including Policies, Procedures and Standard Work preferred; ISO implementation experience preferred; Developing training material and delivering Lean “Teach and Do” Modules; Implementing RCCA and Process Improvement methodology; Project Management experience
15
Manager Continuous Improvement Resume Examples & Samples
- Execute project improvement initiatives resulting in high quality deliverables completed consistently on schedule, resulting in quantifiable results/savings
- Work with other members of the team to distribute workload and define project expectations
- Manage project improvement initiatives with the larger team on a day to day basis, within deadlines set during scoping
- Continually and proactively communicate updates on project statuses and issues to CI Director, via regular communications and status reports
- Ability to further other Crewmember’s growth within their role and within the Company
- Manage the implementation of post mortem program monitoring and track key metrics to measure success and foster continuous improvement
- Assist with the identification and prioritization of opportunities where process redesign/improvement can significantly impact efficiency, compliance, quality, profitability, competitive position and customer satisfaction
- Observing real-time processes and conducting time studies in the field at BlueCities or Other Airlines (OALs)
- Need to work flexible hours and be available to respond on short-notice based on operational and/or project needs
- Recommend alternative solutions and translate complex concepts into simplified and understandable examples
- Show a passion to get the job done
- Five (5) years of professional experience with respect to continuous improvement
- Three (3) years of leadership experience managing a large team with direct reports
- Experience implementing large scale projects and tracking results
- Ability to work across all levels and influence with impact
- Ability to supervise other Crewmembers and work collectively as a team
- Strong presentation skills and experience working with and presenting to senior executives
- Available for overnight travel (30%)
- Currently in possession of a valid passport or equivalent travel in and out of the United States
- Proficient with the Microsoft Office suite especially strong in Microsoft Excel, Visio and PowerPoint
- Must be a team player and work effectively cross-departmentally
- Must be able to multi-task, manage multiple projects, prioritize deadlines, and complete assignments accurately and timely
- Project Management Professional (PMP) certified
- Airline or related industry experience
- Regular attendance and punctuality
- Potential need to work flexible hours, inclusive of weekends and irregular shifts and be available to respond on short-notice
- Must be an appropriate organizational fit for the JetBlue culture, that is, exhibit the JetBlue values of Safety, Caring, Integrity, Passion and Fun
16
Senior Manager, Continuous Improvement Resume Examples & Samples
- Manage the process that identifies and implements significant Continuous Improvement opportunities to support division and corporate objectives
- Manage the preparation and dissemination of quality management reports for use by Maintenance Operations and assist management in their interpretation and application to improve performance Act as a liaison between Maintenance Standards & Engineering team, Operations and Quality Assurance (Audit) organizations for purposes of evaluating and conducting continuous improvement projects Coordinate and manage continuous improvement programs, establishing and maintaining high quality assurance standards, procedures and controls Manage continuous improvement deployment using fundamentals of
- Lean and Six Sigma Manage lean office and implements lean principles
- Plan, lead and facilitate Kaizen and Six Sigma teams
- Develop standards of performance based on process innovation and best-in-class practices Manage the preparation, development and publishing of
- Continuous Improvement materials to include detailed process documentation, process maps, and training (webinar) materials
- Document procedures to implement process changes
- Manage the development and implementation of the operational goal setting process
17
Manager Continuous Improvement Resume Examples & Samples
- Preferable technical Master's degree or relevant experience
- Education or experience in CI and/or Six Sigma is a plus
- Mastery of Dutch and English language
- 5-10 years of experience, preferably from different areas within the company
- Understanding of the petrochemical industry, main processes, suppliers and customers
- Demonstrated ability to manage change processes successfully, monitoring complexity, diversity and risks
- Proven ability to implement strategic action plans
- Mastery of implementation, facilitation and coaching
- Proven networking abilities
- Recognised for being able to manage larger networks; for having excellent pedagogical people training, coaching and feedback skills and for creating a winning team culture
- Recognised for being communicative, dialogue engaging, inspiring, motivating and setting direction for others within a multicultural environment
- Experience in group facilitation, analytics, project management and/or in managing/delivering a CI project within a larger deployment is a plus
- Job holder must challenge “as is” and look to drive significant improvements
18
Manager, Continuous Improvement Resume Examples & Samples
- Govern customer’s specific business scope, end-to-end business processes, operating work instructions, billing procedures, etc
- Work with customer and DHL stakeholders to manage process and system change requests, conduct cost-benefit impact analysis, and implement the solution in collaboration with stakeholders
- Drive continuous improvement by analysing existing solutions to identify cost savings and service enhancements opportunities, include solution re-engineering / redesign initiatives
- Support Account Manager in developing yearly account development plan with a clear identified opportunities to grow the account regionally / globally,
- Develop Best Practices and Knowledge Management Approach. Custodian of Service & Cost Excellence Initiatives, as well as KPI performance data repository
19
Manager, Continuous Improvement Resume Examples & Samples
- Maintain End to End Value Stream Map for Coalition while driving improvements in processes, procedures, and capability
- Partner with functional leaders to define and execute business strategy to achieve goals and priorities, while deploying financial and operational objectives to help drive cost savings and efficiencies. Range of support areas include procurement, manufacturing, merchandising, quality, customer service, distribution, and product development
- Educate and coach the Lean Six-Sigma methodology throughout the organization by developing strategy and deploying Lean Six-Sigma tools / tactics including conducting special data analysis projects as requested
- Develop and implement training plans to cascade Six-Sigma to key areas within the organization. Identify and initiate efforts to achieve objectives, teaching others to accept accountability for meeting and stretching to exceed results in a timely and cost effective manner
- Use Lean Six Sigma methodology to identify and resolve complex problems to promote winning outcomes with, among, and across teams. Establish statistical process control related standards and procedures
- Understanding of P&L and balance sheets required
- Strong leadership and communication skills required
- Bi-lingual in Spanish preferred
20
Manager, Continuous Improvement Resume Examples & Samples
- Identify, quantify, and prioritize Opportunity-to-Cash continuous improvement initiatives to achieve corporate growth and profitability goals
- Lead implementation of Opportunity-to-Cash initiatives via cross-functional teams targeted toward increasing revenue, optimizing time to market, improving profitability and/or increasing customer satisfaction
- Identify and implement Opportunity-to-Cash best practices across the organization and incorporate into the Nordson Business System
- Demonstrate appropriate use of Lean Six Sigma tools to drive process improvements
- A Bachelor’s Degree in Marketing, Business, Engineering or Computer Science
- Minimum 5 years in functional role related to the Opportunity-to-Cash value stream (marketing or commercial role)
- Minimum 2 years in continuous improvement role or supporting continuous improvement initiatives
- Excellent analytical skills with strong working knowledge of problem solving, root cause analysis, and associated solution implementation
- Proven project management skills to ensure on-time, high-quality deliverables
- Ability to negotiate and influence key personnel across multiple businesses and geographies to achieve positive results through awareness, understanding, acceptance and engagement
- Experience using ERP and CRM tools and processes
- Knowledge of pricing procedures and best practices
21
Senior Manager Continuous Improvement Resume Examples & Samples
- Possess experience and knowledge of key tools, such as Kaizen, Daily Management, Problem Solving and Hoshin
- Work on strategic priorities and continuous improvement projects across the Business Group and demonstrate positive impact
- Ensure continuous improvement of Daily Management/Visual Management processes and ensure problem solving for maximum impact
- Drive problem solving culture and processes by example and through training and coaching
- Offer coaching and guidance via our Lean Deployment models in support of key Lean Deployments
- Collaborate with business and functional leaders to tailor continuous improvement activities to maximize impact
- Lead Kaizen events and ensure sustainability of improvements
- Determine knowledge and competence gaps and enable training and resource support as needed
- Share best practices as well as “off-standard” issues across key stakeholder groups
- Train and coach employees across the business
22
Manager, Continuous Improvement Resume Examples & Samples
- Working with employees at all levels of the organization to transform from a reactive to a proactive organization. Emphasize cultural change at the management level
- Discipline and basic knowledge of related disciplines requiring conceptual and practical expertise
- Functional experience in a manufacturing environment
- Effective use of technology necessary to satisfactorily perform the job
- Solve problems taking a new perspective on existing solutions; exercise judgment based on the analysis of multiple sources of information
- Explain difficult or sensitive information; work to build consensus
- Mentor, lead and direct the work of others
23
Manager, Continuous Improvement Resume Examples & Samples
- Manage and develop the company’s top strategic accounts
- Advance existing and new opportunities for all divisions of Hub Group
- Act as a communication liaison between customers and the development team
- Work closely with sales and marketing to identify new customers and develop relationships with existing customers through the strategic account management (SAM) process
- Develop and maintain a continuous stream of pipeline opportunities for business development
- Conduct meetings and planning sessions to supervise the management of customer issues
- Oversee and conduct new and existing customer solicitation
- Manage the new customer on-boarding process
- Ensure that customer reporting is being conducted across all functions
- Manage and oversee the daily activities of customer on-site representatives to ensure they are not only meeting, but exceeding both the customer’s and Hub Group’s strategic goals and maximizing their full potential
- Champion the continued development of employees through internal and external training and coaching
- Must be a self-starter with the ability to communicate and interface effectively with all levels of the Hub organization, its customers and carriers in a manner that consistently produces results
- Managerial experience is strongly preferred
- Proficiency with software programs such as MS products, Lotus Notes and AS400 is preferred
- Experience in process mapping is preferred
- Strong organizational, time management and analytical skills are required
- Experience in the transportation industry is preferred
- Possession of a Bachelor’s Degree from an accredited college or university is preferred
- Occasional travel will be required
24
Manager, Continuous Improvement Resume Examples & Samples
- Responsible for execution of an effective closed-loop quality system driven to reduce process variation
- Lead and direct LDI process for department with oversight to entire facility, including facilitation of Natural Management Team (NMT) and Natural Work Teams (NWT) meetings
- Acts as change agent to drive continuous improvement of production and service processes to improve quality and increase efficiency
- Utilizes best practices to achieve world class quality operations through leadership in continuous improvement efforts. Effectively partners with operations to improve process and package quality. Develops local strategies and tactics in alignment with the brewery and integrated supply chain strategic long range plan
- Fully versed in analytical and statistical applications that support quality such as Statistical Process Control (SPC) and Statistical Quality Control (SQC)
- Implements produce quality plans and procedures by overseeing inspection testing requirements, frequency, responsibility, and methods to assure compliance to process and product specifications
- Drive’s plant accountabilities in the areas of: tracking vendor performance, resolution and disposition of customer complaints, investigating critical quality defects on in-process and finished products, generation and analysis of quality data and reports
- Directs activities, duties, and projects of CI personnel
- Culture & communications support & improvement
- Implements practices and controls to drive an effective supplier management system
- 5 - 7 years’ experience in a managerial or leadership role with responsibility for hiring, work performance and corrective action issues
- Prior folding carton or printing experience preferred
- 3 - 5 years’ experience with SQF certification
- Proficient with Microsoft Office, Outlook, and Internet research skills
- Bachelor’s degree in a related field or equivalent combination of education and experience, advanced degree preferred
- Six Sigma Green/Black Belt certification desired
- Working knowledge of Statistical Process Control theories
- Strong knowledge of printing and converting technologies preferred
- Strong knowledge of Color control instruments and color tolerance
- Strong interpersonal skills and ability to motivate people
- Ability to maintain favorable employee morale
- Ability to work in a fast paced environment
25
Manager, Continuous Improvement Resume Examples & Samples
- Guide the coordination of business process changes, implement system solutions
- Display a high level of critical thinking in bringing successful resolution to high –impact, complex and /or cross-functional problems
- Supports the integration of processes (departments) into appropriately interconnected extended value streams
- Develop and utilize current and future state value stream maps to identify strategic projects and corresponding rolling 12-month implementation plans aligned with the company’s strategic direction
- Identification and leverage of best practices across the entire TE operation, with focus on applicable North American Transportations Solutions segment
- Lean Black Belt or Master Black Belt preferred
- Experience leading an initiative that produced documented results
- Excellent communication skills both written and verbal
- Produced verifiable breakthrough results
- A thorough understanding and ability to use all aspects of Define Measure Analyze Improve and Control (DMAIC) model
- Understand the need to improve measurement system capability as process capability improves; evaluate the use of control measurement systems
- Have knowledge of Lean enterprise concepts; ability to identify value-added elements and activities; and able to use and apply specific six Sigma Lean tools
- Bachelor of Science Degree in an engineering discipline
26
Manager, Continuous Improvement Resume Examples & Samples
- Benchmark with other world class operations and continually reapply best practice/company standards
- Establish internal lead site efforts to test new learnings and capability to deliver breakthrough results
- Stay in front of the organization from a capability standpoint to continually drive progress
- At least 5 years of prior operations experience using continuous improvement tools to deliver business results is required
- Prior success in implementing and sustaining result improvements is required
- Experience in training and leading groups is required
27
Senior Manager Continuous Improvement, DBS Resume Examples & Samples
- Significant practitioner experience in functions/areas supporting (e.g., New Product Development practioner if a DBSL supporting Innovation through improvements in New Product Development processes)
- Demonstrated proficiency applying lean principles in a variety of situations
- Hands-on and detail-oriented but also able to see the big picture
- Able to think strategically and view the business from a general management standpoint
- Very customer focused and has strong interpersonal and communications skills
- Quick study who can rapidly adapt to Danaher’s culture and gain the confidence of the Danaher organization
- High energy and able to handle conflict
- Independent worker, capable of operating in a fast-moving, ever changing environment and able to effectively deal with difficult situations
28
Manager Continuous Improvement Resume Examples & Samples
- Strong leadership ability and presence while working in a team matrix organization
- Action and hands-on orientated focus on driving improvement and solving root cause problems in CI and EHS
- Positive and upbeat personality focused on driving forward even in the face of challenges
- High ethical standards. Models and supports organization’s goals and values; adapts to changing conditions; demonstrates persistence and overcomes obstacles
- Excellent communication skills to lead and support empowered employees within a matrix structure
- Strong project and budget management skills to implement business unit plans and monitor performance to plan. Ability to prioritize, balance, and manage multiple efforts with strong results/goal orientation
- Strong analytical skills and solution-driven thinking. Able to use large amounts of data to make strategic decisions. Passion for data, analysis, trends, reporting and technology. Presents numerical data effectively
- Demonstrated lean manufacturing and improvement strategy development and implementation
- Ability to communicate effectively across mediums, audiences, and situations. Includes internal and external audiences, and higher and lower company positions. Includes training and instruction
- Expert knowledge of Excel, and strong knowledge of Word, Power Point, Project, and other applicable tools
- EH&S experience, preferably at a factory business, with knowledge of regulatory requirements
- Experience in conducting audits and implementation of EH&S managements systems
- Undergraduate degree in Engineering, technology or science related areas required or equivalent years of experience. Certified lean required and Six Sigma green-belt (or better) preferred with demonstrated project success
- 5 years of progressive materials, manufacturing and operations team leadership experience. Must have successfully led multiple Kaizen events within a manufacturing environment. Understanding and knowledge of industrial safety and environmental in a working environment. Good understanding of financial measurements and goals
29
Global Manager, Continuous Improvement Resume Examples & Samples
- Demonstrated leadership and change management skills
- Ability to cross-functionally move between departments and divisions in the Zone
- Strong Word, Excel and PowerPoint skills
30
Manager, Continuous Improvement Resume Examples & Samples
- Partners with the site leadership team to implement the BES Operating System in alignment with the goals and objectives of the site or function
- Strengthen organization competency in BES fundamentals and processes to engage and empower employees to effect positive change through continuous training, learning and application
- Build and maintain trust and credibility with employees at all levels demonstrating corporate values and principles
- Identifies and leverages best practices within the local site and BGI to support the on-going evolution of BES. Documents lessons learned and incorporate it into local sites as appropriate
- Coordinates and synchronizes site level BES goals and initiatives. Provides documentation of results and benefits achieved
- Three to five years of demonstratedsuccessful implementation / execution in continuous improvement systems and tools with achieve results
- Understand change, including how people react to it and proactively plan for the various stages of transformational and transitional change and the effect of that change
- Acknowledges the changing business environment and is comfortable to change. An ability to persuade others through communication and fact based information. Effective change agent skills to help the organization meet goals and objectives
31
Manager, Continuous Improvement Resume Examples & Samples
- Continuously drive the facility's culture toward a higher level of reducing waste and creating value. Challenge status quo methods and theories to cultivate a work environment that optimizes its operations and uses of resources
- Identify and facilitate productivity and efficiency initiatives. Develop financial justification for productivity and efficiency initiative driving toward 100% "Right the First Time"
- Facilitate teams that are focused on identifying areas of opportunity, developing strategy for improvement and measurement of results
- Provide mentoring, coaching and training to support the use of continuous improvement methodologies and tools
- Be a catalyst for team development, growth and engagement
- Leads Kaizen events to improve existing processes and strive to achieve sustainability
- Use statistical analysis in determining opportunities for improvement in Plant Operations
- Utilize Lean Manufacturing methodology to improve efficiencies and minimize waste
- Be a champion of change, systematically enhancing continuous improvement and ensuring the integrations fit within other areas of the organization
- Responsible for reporting activities such as KPI's, status of current or future initiatives and overall communications by helping others to see the what, why and how
32
Manager Continuous Improvement PL Resume Examples & Samples
- Acts as an internal consultant for location to lead, define, and develop continuous improvement activities
- Coaches and champions functions to identify and implement opportunities to improve program and process effectiveness
- Manages problem-solving efforts to improve quality and eliminate waste/cost of poor performance at the local level
- Applies analysis to improve process capability
- Conducts regular and periodic audits of the Management Operating System
- Facilitates the development of action plans to variances as identified through the audit process
- Provides technical direction/guidance to personnel as required
- Functions as facility Process Improvement champion regarding tasks, projects, and operations
- Networks and shares best practice with other locations
- Minimum four-year degree in or related operations / process improvement experience
- Six Sigma certification a plus
- Knowledge of CI / Lean / TPM tools
- The ability to communicate information and ideas in speaking so others will understand
33
Senior Manager, Continuous Improvement Resume Examples & Samples
- Bachelor’s degree in IT, Accounting, Business Management or related field required
- Proven experience with a focus on business processes from an operational or IT background, project management, shared services experience
- Green or Black Belt Six Sigma, Lean Six Sigma, Prince, PMP, or Agile qualifications
- ERP, Microsoft Project, Visio, Powerpoint, Excel, SaaS platforms
- Strong negotiation skills and the ability to make decisions in a fast paced environment
- Urgency and ownership of resolution, meeting established performance objectives and commitments
- Ability of work independently and functioning as a self-starter in a large corporate global environment
- Excellent analytical, technical and problem solving skills; results and action oriented
- Excellent verbal and written communication skills and strong listening skills
- Excellent presentation skills; ability to prepare presentations, interpret data, and provide action plans. Must be able to present and perform with an executive presence
- Effective management of confidential data
- Ability to multi-task and quickly adjust to changing priorities
- Proven relationship building skills and capable of interacting with multiple levels of the organisation including senior leaders
- Strong collaboration skills and ability to partner with key internal/external customer to drive change & continuous improvement
- Ability to understand and act on the strategic goals of the department
34
Manager Continuous Improvement Resume Examples & Samples
- Prepare reports and statistics of strategic costs; cost-out initiatives; various planned process improvements; new product introductions and various others
- Build the skills of all Functional leaders and associates through hands-on interactions and personal mentoring in lean management tools, cultural change leadership and strategy deployment
- Developing a project plan for implementing improvements and monitoring the new process to ensure it works as intended
- Diagram the flow (including inputs and outputs) of a manufacturing process then identifying opportunities for improvements
- Create and track multiple parallel projects
- Insure changes are fully integrated
- Provide feedback and insight to associates on follow-up evaluations of various improvement processes that have been implemented
- Adhere to and understand all safety regulations and protocols
- Measures and reports progress on an on-going basis of improvement procedures in process and provide benefits and results upon completion
- Ensures that the site organizational structure has been reviewed and that resources and safety are aligned for the lean transformation
- Works closely with the CI Engineer
- Familiar with engineering drawings, specifications and their interpretations
- Bachelor’s degree in Mechanical or Industrial Engineering; Quality Management; Production & Operations Management
- Five or more years with business process design in continuous improvement efforts; business management skills; process management; and manufacturing processes
- Must possess PC skills; have good verbal and written communication and interpersonal skills; have excellent organizational skills and possess knowledge of production systems and techniques. Must demonstrate excellent analytical and logic thinking skills to understand and analyze complex business processes; and demonstrate skills in the understanding of Lean principles such as Value Stream Mapping, Kaizen, Communication Tools, & Problem
35
Senior Manager, Continuous Improvement Resume Examples & Samples
- Ensure compliance with Henkel standard operating procedures and any other internal / external compliance requirements
- Ensure effective and cost efficient operating tools to support operations management
- Participate in ‘near term’ and ‘long term’ forecasting and planning to understand requirements for distribution – pick method optimization, space utilization, and overall throughput
- Analyze order behavior and model impacts for the supply chain, anticipate and mitigate risks and put in place the right resources to support the business
- Ensure correct invoicing processes with all third party vendors and implement appropriate governance
- Work with Finance and Logistics Teams to identify savings opportunities and to develop action plans to realize savings for all of Henkel’s consumer goods business units (Laundry & Home Care, Beauty, and Beauty-Professional) for North America
- Work with Purchasing to ensure ‘best value’ solutions and favorable commercial terms for the business
36
Senior Manager Continuous Improvement Resume Examples & Samples
- A Bachelors degree is required
- A minimum of 7 years’ working experience is required in Lean and Continuous Improvement
- A passion for Continuous Improvement and demonstrated track record in process understanding and improvement
- The ability to enthuse colleagues in Lean Thinking as a business necessity
- Able to work at every level of the organization, from individual contributors to senior leaders
- A leader and influencer of teams
- Business English both spoken and written is required
37
Manager, Continuous Improvement Resume Examples & Samples
- Lead site in the progressive achievement towards critical global programs such as OPD, NPI, and TPM
- Identify continuous improvement opportunities throughout the organization by routinely studying area SQDC boards, reviewing site metrics, Voice of the Customer data, etc
- Partner with process-owners to make data available for process improvements
- Coach and mentor staff specialists and process owners to complete projects by identifying and eliminating barriers
- Lead and/or support Operational Excellence projects that positively affect the business results of the site (QC Lab, equipment reliability, standards)
- Engage teams to help establish a Continuous Improvement culture and execute advanced problem-solving activities (Kaizen workshops)
- Prioritize and select projects and leverage LEAN six sigma tools to drive improvements
- Assist process-owners to champion projects through PDCA life-cycle from identification to sustain
- Model advanced problem-solving and LEAN Leader behavior and propagate that behavior at the local site level
- Manage project load via the site project governance program to ensure resources are focused on delivery of the right projects at the right time
- Assess and integrate new technologies that will create capacity, increase speed to market and enable customer growth
- Coordinate with Global and Regional Deployment Leaders regarding project status, issues and accomplishments
- Network and collaborate with other CI Leaders/Managers/Directors to share best practices
- Contribute to GB/BB candidate identification and selection, offer recruiting/promotion recommendations and conduct Performance Management for the positions directly reporting to this position
- The list below suggests the major breakdown of activities for a CI Leader. The percentages are subject to change at the discretion of the hiring manager without compromising the role’s primary focus of process improvement. The weightings may shift as much as 10% from direct problem solving to coaching/mentoring in a Manager/Director role
- 25% Opportunity ID
- 25% Project Selection and Prioritization
- 25% Problem Solving - direct
- 15% Mentoring/Coaching
- 5% Data Collection
- 5% Reporting
- 5-8 years relevant experience in the pharmaceutical, medical device, food or other FDA-regulated industry is required
- 2-3 years direct supervisory and management responsibility
- Six Sigma and LEAN certification is a plus
- Experience with cGMP (current Good Manufacturing Principles)
- Must have experience with advanced problem–solving (LEAN six sigma) and change-management methodologies consistent with establishing a culture of continuous improvement
- Demonstrated team leadership and project-management skills
- Exemplary interpersonal, verbal and written communication skills; able to communicate effectively and interact with personnel at all levels of the organization
- Demonstrated ability to lead by influence and drive results through others not under direct supervision
- Must be a results-oriented Change-Agent; a skilled facilitator adept at influence, negotiation, and conflict resolution
- Able to work under deadlines and handle multiple and detail-oriented tasks
- Experience applying LEAN and six sigma techniques in a manufacturing and business environment. (GB/BB or LEAN Master Certification desired but not mandatory)
- Experience with data collection and reporting
- Proficient in Microsoft Office Tools: Excel, Access, Word, PowerPoint, Visio and statistical analysis software (e.g. Minitab, JMP, etc.)
- Action oriented with ability to deliver timely and positive results
- Must possess excellent oral and written presentation skills
38
Senior Manager Continuous Improvement Resume Examples & Samples
- Identifies process improvement opportunities that add value and improve customer experience and PSDS Service and Repair KPIs
- Facilitate cross-functional brain storming sessions to identify potential root causes for a business opportunity
- Gathers data from various sources including SQL, manual data capture, etc… to quantify all root causes
- Analyzes data to identify which root causes are most critical to address. Data analysis includes prioritizing, Pareto Analysis and statistical analysis leveraging statistical process control tools like JMP
- Leads cross-functional teams in generating solutions to address complex problems utilizing fact-based decision Lean Six Sigma methodologies
- Leads and manages all aspects of process improvement including, but not limited to, cost/benefit analysis, process analysis, data analysis, solutioning, implementation and confirming results
- Leads implementation of solutions, communication and strategy to improve process awareness and effectiveness of long term initiative success
- Establishes strong collaborative relationships with both internal and external PSDS Service and Repair partners
- Develops and delivers presentations to communicate proposals, initiatives and progress leveraging DMAIC tollgates
- Actively participate in business process understanding and implications of initiatives. Seen as leader in the business
- Responsible for meeting and exceeding timing, goals, and budget on initiatives
- Bachelor's Degree with 5+ years work experience in a related field such as product management, process management, or operations
- Industrial Engineering degree is preferred
- Six Sigma Black Belt certification is preferred
- Minimal travel is required with this position (10%)
- Experience using Microsoft Office Suite products such as Excel, Access, Visio and Power Point
- Experience using statistical software a plus (JMP)
- Lean Six Sigma experience is a plus
39
Manager, Continuous Improvement Resume Examples & Samples
- Provide oversight for KPI’s, Metric Boards, Hr x Hr reporting for compliance and utilization of Lean Management System
- Initiate, maintain and share best practices across the organization
- Lean Operations (related) training required, preferably by nationally recognized certification body
- Minimum of 10 years of demonstrated qualified lean operational experience in a leadership role required
- Solid knowledge and demonstrated understanding of TPS and methodologies such as: Strategy Deployment, A3 development and management, Process Flow Mapping, Value Stream Mapping, 5s/Visual Management, Standard Work, Process Problem Solving and Root Cause Analysis, Quality at the source, Just in Time, Kaizen/Continuous Improvement, Abnormality Management, Project Management, Business Process Capacity planning/development, and Lean ROI
- Extensive Gemba based continuous improvement based tools/techniques
- Knowledge of and demonstrated ability to integrate safety, ergonomics and 5s requirements with lean practices in an office environment
- Proficient with Personal Computer applications (Excel, Word, Power Point, Visio, MS Project) 7.Superior and demonstrated leadership, team building, communication, presentation, interpersonal, and coaching skills and the ability to ensure accountability using Lean Management Principles
- Bachelor of Science in related business discipline. L
- Lean practitioner with experience with Toyota Motor Manufacturing or similar Industry recognized Lean Experts such as TBM
- Six Sigma training and/or experience desirable
- Lean Hospital, Financial, or other Business Process industry experience desirable
- Familiarity with the Shingo Model and aligning cultural behaviors to principles
40
Manager Continuous Improvement Resume Examples & Samples
- Handle resources of the Company to overcome challenges in progess of their projects, Generating solutions, piloting solutions and sustaining these solutions
- Involves different stakeholders in the process including process owners and senior leadership of the company
- Handle Continuous Process Improvement
- Initiate Business Excellence
- Lean and Six Sigma
- Data Analytics
- Outbound & Inbound Process