Continuous Improvement Manager Resume Samples
4.9
(126 votes) for
Continuous Improvement Manager Resume Samples
The Guide To Resume Tailoring
Guide the recruiter to the conclusion that you are the best candidate for the continuous improvement manager job. It’s actually very simple. Tailor your resume by picking relevant responsibilities from the examples below and then add your accomplishments. This way, you can position yourself in the best way to get hired.
Craft your perfect resume by picking job responsibilities written by professional recruiters
Pick from the thousands of curated job responsibilities used by the leading companies
Tailor your resume & cover letter with wording that best fits for each job you apply
Resume Builder
Create a Resume in Minutes with Professional Resume Templates
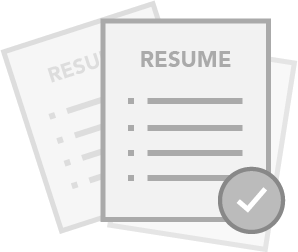
CHOOSE THE BEST TEMPLATE
- Choose from 15 Leading Templates. No need to think about design details.
USE PRE-WRITTEN BULLET POINTS
- Select from thousands of pre-written bullet points.
SAVE YOUR DOCUMENTS IN PDF FILES
- Instantly download in PDF format or share a custom link.
TK
T Kuhn
Tyshawn
Kuhn
835 Nelda Port
San Francisco
CA
+1 (555) 721 2405
835 Nelda Port
San Francisco
CA
Phone
p
+1 (555) 721 2405
Experience
Experience
Phoenix, AZ
Continuous Improvement Manager
Phoenix, AZ
Maggio LLC
Phoenix, AZ
Continuous Improvement Manager
- Manage and evaluate the Continuous Improvement staff including but not limited to performance management and employee development, etc
- Formal training in Change Management, Continuous Improvement (i.e., Lean, Six Sigma, Kaizan, Workout), Performance Management
- Manage and develop a high performing Continuous Improvement team
- Works with management to identify and establish project selection criteria with an emphasis on overall process and quality improvement
- Work closely with Operations Management, Plant Manager, and Human Resources to establish a team culture at the lines
- Work with the Site Steering Committee to develop the site continuous improvement plan (CIP) and continuous improvement strategy
- Utilize Continuous Improvement tools to eliminate waste, driving customer satisfaction, cost reduction, and improved working capital performance
Houston, TX
Quality & Continuous Improvement Manager
Houston, TX
Spinka, Wiegand and Kirlin
Houston, TX
Quality & Continuous Improvement Manager
- EHS - BU liaison on the Process Safety Center of Expertise as an extended team member. Manage the site Process Safety Management (PSM) and EPA’s Risk Management Program (RMP). Lead process hazard analysis (PHA), the management of change (MOC) system and Pre-startup Safety Review (PSSR) documentation; Develop and maintain engineering documentation for regulatory compliance. BASF Exposure Reduction Process (ERP) leadership, coordination, and implementation via a cultural change
- Drive annual Quality Evaluations, measuring compliance of our hotels & resorts to IHG’s Fire Life Safety, Design and Brand Product & Service Standards, and follow up with hotels to ensure that Management Action Plans (MAP) are executed
- Working together with hotel teams, to develop various learning systems/platforms and toolkits to better build up the Continuous Improvement capabilities of resort team thus to drive process performance with high linkage to key business objectives
- Drive continuous improvement efforts through the use of the Eaton Lean System, Eaton Quality System and ISO9001 corrective and preventative action policies to drive down our cost of non-conformance
- Provide prompted analysis and solutions to help greater resort operations team and hotel management teams understand the root causes and execute high impact solutions for Guest Satisfaction. Then together with Regional VP Operations, Regional General Managers, review and approve Action Plans to maintain and drive performance on Guest Satisfaction
- Execute performance and career development discussions
- Lead / drive a culture of continuous improvement through the use of ACE tools to implement change that strives for ACE Gold performance and supports the Chiller Operations factory transformation plan
present
Los Angeles, CA
Senior Continuous Improvement Manager
Los Angeles, CA
Schulist, Pfannerstill and Reichel
present
Los Angeles, CA
Senior Continuous Improvement Manager
present
- Outcome: Following your interview, we'll be in touch within five working days to advise you of the outcome
- Serving as member of the plant leadership team to drive improvements in safety, food safety, service, financial results, quality, and employee engagement
- Leading the plant wide cost savings program to meet annual targets. This includes identification, validation, coaching and execution of projects
- Leading the Overall Equipment Effectiveness (OEE) metric and process including maintaining measurement standards, facilitating improvement plans and strategies, training, coaching and monthly reporting
- Establishing and maintaining plant KPI’s and visual factory tools, and serving as KPLAS / downtime reporting system owner
- Continually expanding and enhancing knowledge levels of Kellogg Work Systems, lean manufacturing and industry “best in class” manufacturing cost savings projects and operations practices to develop a culture of continuous improvement
- Deploying and coaching Lean practices, 5S, Kaizen, and Kellogg Work Systems tools across all levels of the organization to deliver business results
Education
Education
Bachelor’s Degree in Engineering
Bachelor’s Degree in Engineering
East Carolina University
Bachelor’s Degree in Engineering
Skills
Skills
- Process/product knowledge, basic statistical knowledge, and organization knowledge
- Understand basic business skills and practices. Knowledge/fluency in industry quality management tools
- Possesses basic statistical knowledge and the ability to apply statistics to product and process improvement projects
- Strong attention to detail and excellent problem solving skills
- Implement and oversee the quality of deliverables and effectively manage the team and day-to-day relationships to ensure measureable exceptional performance
- Strong ability as change agent with demonstrated ability to influence change for results
- Ability to manage highly visible, complex projects to a successful end
- Prove ability to raise the performance bar – create, promote, and sustain a high performance culture that reinforces accountability
- Hands on style and solid communication ability
- Project Management skills set -Minitab Knowledge -Visio Knowledge
15 Continuous Improvement Manager resume templates
Read our complete resume writing guides
1
Continuous Improvement Manager Resume Examples & Samples
- Understanding customer (Internal or External) requirements and drive waste reduction from a customer point of view
- Respond to the customer in a timely manner as required
- Drive customer satisfaction ethos in all areas of responsibility
- Form a strong business partnership with customer contacts
- Display a "Voice of the customer" mentality
- Initiate and track corrective/preventative action plan
- Ensure all continuous improvement activities align with Holding and divisional initiative
- Facilitate continuous improvement activity and help implement global baselines in all areas of responsibility
- Provide leadership and support to ensure continuous improvement initiatives are productive
2
Continuous Improvement Manager Resume Examples & Samples
- Support LN L&P by driving key strategic projects and developing workflows in accordance with Lean, Six Sigma standards
- Plan and successfully execute continuous improvement projects to meet goals and support strategic priorities, delivering recommended improvements with supporting business rationale
- Improve customer satisfaction and reduce process variation through application of Lean Six Sigma tools and methodologies
- Lead cross functional teams that gather information to evaluate current work processes and identify improvement strategies. Process mapping, root cause analysis and benchmarking of processes
- Support the implementation of key LN L&P strategic initiatives, improving our ability to deliver on strategic priorities and improving operational effectiveness
- Serve as change agent by stimulating, communicating, and institutionalizing Lean Six Sigma methodologies and the benefits these capabilities provide
- Drive cultural changes across the business and support deployment of the Lean Six Sigma program
- Support the development and deployment of an approach and framework for building continuous improvement capabilities across LN L&P
- Facilitate rapid improvement events targeting specific improvement opportunities in the business
- Educate, coach, and mentor Green and Yellow Belts on Lean Six Sigma tools, methodology and application
- Communicate progress to Champions, Business Leaders, and Master Black Belts
- Ability to work in a complex and matrixed environment, deliver quickly and adapt to changing demands
- Excellent interpersonal and communication skills (both written and verbal)
- Ability to cultivate strong collaborative working relationships and contacts within work group, across other company functions and with external organizations. Ability to interact effectively with all levels of the organization, including senior leadership
- Ability to influence others and drive meaningful change results
- Black Belt (Certified). Demonstrated success as a Black Belt
- Strong analytic and project management experience working across functional projects. PMI or other relevant professional certification preferred
- MBA or equivalent education and experience
- Minimum 5 years of experience in implementing Lean, Six Sigma and continuous improvement initiatives
- High Level of technical skills including advanced MS Office and Visio skills
- Knowledge of information industry and technology preferred
3
Continuous Improvement Manager Resume Examples & Samples
- Drive continuous improvement culture change both internally and externally within the contact centre environment
- Drive tactical execution of key initiatives
- Act as an internal resource for the principles of lean and process excellence working closely with Disney EMEA business units to deliver GX solutions
- Provide the right metrics to measure process quality and productivity, providing meaningful feedback to the internal and external business teams
- Develop the required reporting and analytics to review and analyse customer defect data and develop and present the corresponding countermeasures
- Develop a governance for operations business teams and our contact centres in their ability to develop and execute daily, weekly, and monthly action plans to increase quality and customer experience
- Educate internal and external teams on the correlation between customer experience, productivity and process improvement
- Gain consensus to push change forward while keeping all stakeholders updated on their required inputs
- Establish a partnership with business leaders to develop and lead the continuous improvement strategy across multiple business units
- Provide leadership on continuous improvement project selection, scope, definition, and performance to ensure alignment with the GX strategy
- Collaborate and communicate with other functions on best practices, internal and external benchmarking, talent development, programs of study and knowledge sharing
- 3-5+ years’ experience in project management and facilitation of process improvement initiatives across business operations and technology
- 2+ years’ experience instructing executives, managers, and associates on Lean methodologies
- Must be willing to travel as necessary, not more than 25% of time
- Facilitation experience between internal and external GX functions
- Experience successfully deploying transactional lean, manufacturing lean, variation reduction, and six sigma methodologies
- Lean/Six Sigma Greenbelt certification minimum
- Experience communicating goals and strategies across multiple leadership levels of an organization
- Decisive, confident, positive attitude and experience with influencing others
- Ability to handle changing priorities and use good judgment when working in stressful situations
4
Continuous Improvement Manager Resume Examples & Samples
- Develop and lead implementation of strategies supporting achievement of ACE Milestones & Silver/Gold goals
- Manage / monitor progression of 9 business & support sites through the ACE 12.2 criteria
- Identify risks to ACE progression and Associate certification goals and implement mitigations
- Interface with ACE Client Manager and UTAS ACE Office
- Facilitate the annual Policy Deployment Planning process and monthly reviews for AMFMS
- Educate and train leaders and employees on ACE tools and other continuous improvement methods and processes
- Ensure ACE tools (e.g. QCPC, Relentless Root Cause Analysis) are used across the organization to reduce lead times and the cost of poor quality and improve product first pass yield and on-time delivery
- Facilitate strategic Kaizen Events, including Value Stream mapping, 3P, Cell Design, and Macro Planning
- Drive the organization to recognize and attain best in class performance and processes through benchmarking activities inside and outside of the UTC businesses. Support standard work development efforts for Quality & ACE business processes
- Facilitate goal setting, coordinating timelines, budget/staffing requirements, sharing best practices and celebrating successes
- Motivate and mentor others and lead by example through active participation
5
Continuous Improvement Manager Resume Examples & Samples
- Leads and directs the Division’s CI Program, identifies opportunities for improvement, cost reduction and avoidance; leads long and short term projects aimed at waste elimination and enhancing production efficiencies; subject matters may include plant floor and work center layout, material handling, and material selection
- Establishes current and long range objectives, plans, and policies in support of Program objectives, and directs resources to achieve objectives. Monitors performance against plan and ensures that goals are met
- Works with management to identify and establish project selection criteria with an emphasis on overall process and quality improvement
- Support Lean/CI culture by coaching, motivating and developing continuous improvement skills in all levels in the organization
- Develop and manage cross-functional teams to meet project objectives. Monitors productivity of groups and individuals, recommends changes where desirable. Provides leadership and support to team
- Creates and/or facilitates process design changes by integrating new systems and/or processes with existing ones. Provides guidance to develop a team-based organization focused on project goals and objectives
- Develops performance measurement tracking mechanisms to support project objectives
- Reviews Management reports to ensure projects achieve stated goals and support business objectives
- Maintains appropriate contact with management, supervision, and plant manufacturing to ensure that CI performance is meeting objectives. Responsible to assure that CI projects are appropriately championed to assure timely completion of CI projects
- Plan, coordinate, and direct workshops and Kaizen events
- Manage compliance to Mafact Scorecard; confuct internal and external audits as required
- Develop metrics that encourage and promote continuous improvement
- Bachelor’s degree in engineering, quality, or business
- Minimum 5 years diverse professional and managerial experience including financial/budget responsibility, management leadership, and strategic decision making/leadership in a manufacturing environment
- 3 – 5 years experience in Lean Manufacturing in an automotive manufacturing environment
- Demonstrated strong communication skills to work with internal and external contacts at all levels within the organization. Able to represent the company in a professional manner with customers and suppliers
- Strong negotiating and communication skills, both written and verbal. Must be able to work with peers in a positive, cooperative way and maintain productive relationships with key functional areas
- Demonstrated leadership and management skills in support of company management systems and philosophies. Must be able to develop and lead cohesive teams
- Demonstrated skills in using quality and statistical control tools, and the ability to teach these to others
- While performing the duties of this job, the employee is regularly required to sit with occasional walking required
- Repetitive motion involved in typing and keying affecting fingers, hands and wrists
- The noise level in the work environment is usually low
- Works mainly in office area but may spend time on shop floor
6
Continuous Improvement Manager Resume Examples & Samples
- Develops and manages cross-functional teams and Continuous Improvement project leaders to meet project objectives. Monitors productivity of groups and individuals, recommends changes where desirable. Provides leadership and support to team
- Creates and/or facilitates process design changes by integrating new systems and/or processes with existing ones. Provides guidance to Group Leaders and other project staff as needed to develop a team-based organization focused on project goals and objectives
- Develop performance measurement tracking mechanism to support project objectives. Review management reports to ensure projects achieve stated goals and support business objectives. Able to take an organization to the upper/top performers in Magna for MAFACT/WCM
- Bachelor’s degree (or equivalent). Specific degree requirements will vary based on area supported but professional and managerial experience including management leadership, and strategic decision making/leadership in a manufacturing environment lean capacity will stand out and set a candidate apart
7
Continuous Improvement Manager Resume Examples & Samples
- Lead teams within a matrix organization to ACE Pilots to drive the DRSS sites to ACE Silver/Gold performance levels, by applying the ACE Operating System
- Work with DRSS leadership to define and achieve the ACE strategic vision
- Coach, develop and manage DRSS ACE resources
- Plan, lead and facilitate Continuous Improvement events, including Value Stream Mapping, 3P, Cell Design and Macro Planning
- Drive improvement of foundational ACE principles, including 5S, VSM, TPM, RRCA, Standard Work and Process Capability
- Facilitate the annual Policy Deployment Planning process and monthly reviews for DRSS
- Ensure ACE tools are used across the organization to reduce lead times and the cost of poor quality and improve product first pass yield and on-time delivery
- Drive the organization to recognize and attain best in class performance and processes through benchmarking activities inside and outside the UTC Businesses
- Assist in the implementation of Standard Factory including coaching/guiding the DRSS Site Lean Transformation Plans, to integrate production with logistics and drive/facilitate the site leadership to execute the plan. This includes manufacturing cell design, material presentation/line feeding, takted material delivery and establishing pull systems with suppliers to minimize inventory and improve on-time delivery
8
Continuous Improvement Manager Resume Examples & Samples
- Bachelor’s Degree in Engineering required; at least five years of durable goods manufacturing management experience required. MBA with Operations focus or Master of Science-Operations preferred
- Must have thorough understanding of cycle time reduction, waste reduction, yield improvement, productivity and throughout improvement
- Hands-on experience using Operational Excellence and Continuous Improvement methods (LEAN, TPM, Six Sigma, TQM)
- Proven leadership skills to coach and lead teams to fully deliver chartered objectives and projects
9
Continuous Improvement Manager Resume Examples & Samples
- Challenges and inspires partners to achieve business results
- Coordinate and guide improvement projects and manage projects from original concept (current state) through final implementation (future state) delivering against cost, schedule and performance criteria
- Develop, document and deploy standardized processes and standard work
- Develops project plans for plant level and each improvement activity with specific timelines and follow ups to ensure improvements are sustained
- Educates, mentors and coaches team members on operations improvement and Lean manufacturing principles
- Ensures improvement activities are aligned with strategy deployment and will improve plant critical goals
- Ensures partners adhere to legal and operational compliance requirements
- Identifies and communicates key responsibilities and practices to ensure the immediate team of direct reports promotes a successful attitude, confidence in leadership, and teamwork to achieve business results
- Identify continuous improvement training and development opportunities
- Interface with all areas affected by the project which may include internal and external customers, business units, and other various departments
- Leads cross functional teams (all levels) through problem solving activities and improvement projects to eliminate waste, reduce cost, and drive operational excellence
- Prepares, communicates and educates client groups and team on changes in policies and practices within the organization
- Uses data to analyze complex problems to produce tactical and strategic decisions to improve safety, quality, and reliability
- Consumer products or food company and plant experience, either technical or production (7 years)
- Engineering: electrical, mechanical, chemical or industrial (7 years)
- Project management (7 years)
- Supervising professional and nonexempt partners, which may include project teams and contractors (7 years)
- Advanced knowledge of project management techniques directing professionals
10
Lean & Continuous Improvement Manager Resume Examples & Samples
- As an expert in the use of the Lean tools / methods with a comprehensive knowledge of Six Sigma and descriptive statistics, lead and manage the completion of continuous improvement projects within a given timeframe to meet the department or facility goals in productivity, quality, efficiency, and safety. Work closely with the Planning and Scheduling teams to implement RfS (Repetitive Flexible Supply), a globally sponsored planning methodology
- Engage and inspire the manufacturing, warehouse and maintenance employees to recognize process improvement opportunities and actively participate in the realization / validation of their suggestions utilizing the appropriate Lean /CI approach (5S, Standard work, Visual Management, Short Interval Control, etc.)
- Use your data fluency and expert level Excel skills to transform data into usable / insightful information related to work center performance, equipment capability, scrap reduction, downtime elimination and OEE (Overall Equipment Effectiveness)
- Work with cross functional teams to gain process knowledge by determining and documenting key manufacturing process parameters with regards to equipment performance and product quality
- Prepare and deliver formal/informal Lean/CI training and coaching to employees
- Provide monthly report outs to the CI Director on completed projects and assist in presentation to plant Executive Director and other leaders as required
- 5 Years of relative experience
- Regulated industry (food, pharmaceutical, cosmetics) experience (CI, production supervision, maintenance, supporting function) preferred
- Demonstrated successful lean sigma project management capabilities
- Expert level Excel skills, familiarity with SAP and Minitab
11
Continuous Improvement Manager Resume Examples & Samples
- Establish management and measurement systems to identify areas of business performance gaps
- Participate in planning and improvement to close the gaps
- Work with leadership to identify and prioritize improvement initiatives using ACE tools to generate productivity and profitability gains and reduce turn-around times and improve customer satisfaction
- Lead cross-functional teams at various facilities through Lean, CI and Six Sigma Process Improvement efforts to drive KPI improvements in quality, delivery, and cost through application of the ACE tools
- Lead the ACE Council/Guidance Management Team, support organizational development, and lead Policy Deployment and Macro Planning for site
- Provide organization development through training, teaching, coaching and mentoring of leaders and employees
- Plan and lead site through formal assessments to improve and sustain ACE Certifications
- Other activities and tasks as required
12
Continuous Improvement Manager Resume Examples & Samples
- Partner with Quality leadership to drive ACE initiatives and transformation activities while driving improvement in overall quality KPIs and value stream performance
- Develop Group Quality’s Gold Plan
- Work with group leaders to identify and prioritize improvement initiatives to achieve business results using Process Management tools (SIPOC, Control Tower, Impact/Maturity analysis, MFA, QCPC)
- Coach, facilitate and lead improvement events including Value Stream Mapping, Process certification and Root Cause Analysis
- Value stream quality metric reporting including the Quality Control Tower, Executive Committee Quality Scorecard and OMM input which include escapes, scrap, rework & repair, compliance events, supplier escape analysis, program yield and other key Quality KPI
- Work closely with MC&O, P&WC and Aftermarket organizations to understand quality performance and drive systemic improvements
13
Continuous Improvement Manager Resume Examples & Samples
- Process rationalisation –continually reviewing all processes within Customer Service to ensure they are fit-for-purpose, and are as efficient as possible to ensure reduced handling time and a more effective result for the Customer
- Create a library of processes – ensuring that we do not have any single points of failure with our processes and to make locating, reviewing and refining easy
- Reporting – giving an ability to measure success both financially and in terms of time saved for our Customers
- Knowledge – keeping all process-based knowledge fresh, current and interesting to read
- Communication – ensuring that all stakeholders are aware of current and future workload including successes gained
- Time-in-motion studies – obtaining feedback from sitting with individuals in Customer Service to enable proactive improvements in processes as well as accurate timings before and after process rationalisation takes place
- Creating a feedback-loop direct with Customer Service Consultants so that they can highlight misaligned processes as they occur
- Complaint/Customer feedback RCA – determine the root causes of negative Customer sentiment and work to eliminate these in the future
14
Lean Continuous Improvement Manager Resume Examples & Samples
- Work with cell/site/value stream leaders to identify and prioritize improvement initiatives to achieve business results using best practice Process Management tools
- Champion, develop and sustain a culture of continuous improvement (CI) and knowledge about related methodologies/ activities (Lean, Six Sigma) across all areas of the site with a strong focus on manufacturing and operations
- Establish appropriate improvement strategies based on the nature of opportunities. ( Lead time reduction = VSM/Lean, major process change = 3P)
- Strong analysis and problem-solving skills, able to identify and structure issues, run accurate (also statistical) analysis and synthesize recommendations
15
ACE / Continuous Improvement Manager Resume Examples & Samples
- Apply the ACE operating system (Lean and Quality tools) including 5S, TPM, Lean Cell Design, Standard Work, Policy Deployment, Pull systems (kanban & supermarket), Root Cause/Corrective Action, Process Capability, Design of Experiments, etc
- Provide daily direction, coaching and mentoring of an ACE Pilot with direction from the ICAMS ACE Manager
- Lead and support initiatives to help the organization meet deployment goals for ACE to achieve ACE Silver in 2017
- Drive continuous improvement using the fundamentals of lean, six sigma, and employee involvement
- Plan, lead, facilitate and champion continuous improvement events, event teams, and other project teams
- Coach leaders and employees to drive improvements in the performance of production and support processes through Process management and improving Process maturity
- Ensure ACE tools are used across the organization to reduce process lead times, improve cost of poor quality, first pass yield and on-time delivery
- Facilitate Value Stream mapping workshops and utilize various ACE tools such as MFA, 5S, TPM, Setup Reductions, Kanban, etc
- Lead and participate in benchmarking activities inside and outside of UTC businesses
- Co-chair the Cheshire ACE Council including agenda creation/publication, publication of meeting minutes, meeting facilitation and coordination of action item closure
- Support Standard Factory, Process Based Organization (PBO) and Lean Transformation efforts for the site
16
Continuous Improvement Manager Resume Examples & Samples
- Creates and/or facilitates process design changes by integrating new systems and/or processes with existing ones. Provides guidance to Grp Leaders/ Engineers and other project staff as needed to develop a team-based organization focused on project goals and objectives
- Develop performance measurement tracking mechanism to support project objectives. Review management reports to ensure projects achieve stated goals and support business objectives
- Understand your responsibility for health and safety in the workplace. Cooperate with OSHA MIOSHA inspectors. Wear the appropriate personal protective equipment. Follow all safety rules. Report unsafe conditions immediately. Report injuries, accidents, illnesses, near misses, property damage immediately. Will not remove or make ineffective any protective device such as a guard, light curtain, etc. Will not use or operate any machine or equipment that the employee is not trained to operate. Will not use or operate any machine or equipment in a manner that may endanger any employee including themselves
- Process/product knowledge, basic statistical knowledge, and organization knowledge
- Strong communication and team leadership skills with demonstrated ability to facilitate meetings
- Proven success in problem analysis and problem solving
- Project management skills to lead a team to complete a project
- Possess a detailed understanding of customer requirements
- Understand basic business skills and practices. Knowledge/fluency in industry quality management tools
17
Site Continuous Improvement Manager Resume Examples & Samples
- Develop process improvement initiatives (e.g., supplier business processes and practices) in order to benefit the ACCO Brands system and Customers by directing raw materials supply chain activities, involving external suppliers, functional peers, customer teams and/or cross-functional teams
- Review facility capability and environment (e.g. Manufacturing Equipment, technology, systems, quality, cost, efficiencies, yield) in order to recommend process improvements
- Focus on 5S and Lean Initiatives
- Implement raw materials supply chain programs (e.g., quality service Cell optimization, kaizens, process improvements with suppliers in order to improve quality and raw materials supply chain efficiencies
- Document current state processes and business systems and compare to benchmarking data and/or best practices in order to identify performance gaps
- Provide direction, leadership and coaching to members of a project team you are leading
- Bachelor's Degree or equivalent work experience of at least 5 years
- 3+ years’ experience in a Supply Chain management or Manufacturing role
- 1+ years’ experience in a project management role
- MS Excel, PowerPoint
- Continuous Improvement practical and theoretical knowledge
- Good ability to coach and lead
18
Rapid Continuous Improvement Manager Resume Examples & Samples
- Drive Culture Change – Drive fact-based decision making throughout the organization
- Duties will include project management, delivery of savings through improved processes, leadership and support of projects
- Will utilize system skills (data pull and analysis) frequently
19
Continuous Improvement Manager Resume Examples & Samples
- Having capabilty and skills to deliver projects in a professional manner
- Lead project post implementation reviews and continuous improvement
- Having the ability to be trained and train other business leaders in ECI methodology
- Have strong business accumen and process understanding
- Lead business and process reviews to challenge the status quo and lead change within the business to drive profitable growth, innovation and operational excellence
- Strong leadership and organization skills
- Open to new ideas and concepts
- Capacity and drive to work autonomously and show initiative
- High level of verbal and written communication
- Minimum 10 years of experience in a Senior Finance role with a strong understanding of business processes
- Process improvement subject matter expertise: Six Sigma Green Belt, Black Belt
- A background within the White Goods / Consumer Goods industry
20
Continuous Improvement Manager Resume Examples & Samples
- Review current state of Power Group and work collaboratively with Corporate Continuous Improvement to create/action roadmaps for all plants; prioritize most significant and challenging issues facing the business
- Align the efforts and develop the capabilities of plant Continuous Improvement leaders through coaching, teaching, and sharing of best practices; ensure that activities are consistent with and built upon Kohler’s CIM System
- Provide input for and lead by example on improvement of key strategic business goals and metrics; metrics include, but are not limited to, lead time, inventory turns, Internal and External Quality, Safety Incident Rate, Unit Productivity, etc
- Create material and provide training for Power Group associates that supports the development of Continuous Improvement competencies; work alongside plant Continuous Improvement leaders to create, maintain and improve business standards
- Guide teams via a hands on approach; partner to select projects/initiatives that will result in significant business impact; develop and provide financial and/or business justification for projects
- Provide project management expertise for cross-functional teams; drive teams toward timely and thorough completion of projects
- Bachelor’s Degree required. Engineering degree preferred
- 5+ years experience with tools and methods in a Lean, Continuous Improvement, Six Sigma environment
- Ability to teach, mentor, and coach across multiple levels of an operation
- Maintain the highest level of honesty and integrity with in Power Group and Kohler Company
- Proven ability to use systematic problem solving to solve technical challenges
- Multi-site responsibility for system deployment (Quality or CI) with proven ability to juggle multiple responsibilities
- Excellent team facilitation skills; builds teams in a collaborative work style; experience in team building and motivating others
- Strong leadership and change agent skills; able to overcome obstacles using positive facilitation, teamwork, and influence through building and maintaining relationships
- Ability to travel up to 35% of the time, both domestic and international. There might be more travel required at first
21
Continuous Improvement Manager Resume Examples & Samples
- Manage projects and implement sustainable solutions through delivering successful Lean 6 Sigma initiatives that typically cross functional areas, and utilize specific tools and techniques with a an overall Total Cost of Ownership focus. Support the Green Belts within the team to ensure timely project execution and implementation of pragmatic, sustainable solutions
- Accountable for supporting Mars Petcare annual cost savings targets
- Lead and develop a team of highly engaged and collaborative individuals by driving engagement, high performance collaboration and stretch developing initiatives
- Works with business leadership to identify, define and scope Lean 6 Sigma improvement opportunities
- Lead, coach and develop Green Belts and project team members based upon Mars Petcare’s CI/L6S standards. Give and support Green Belt training and certification
- Develops and applies necessary technical skills to deliver improvement results (such as Lean, 6 Sigma, VSM, etc.)
- Engages process/department personnel in all phases of Lean 6 Sigma improvement efforts (including Value Stream Mapping, DMAIC projects, creating Standard Work, and 6 Sigma ways of working)
- Develops strong technical network with cross functional leadership
- Serves as a technical resource to support other Lean 6 Sigma analyses, as requested
- Maintains appropriate project documentation including project charter, progress updates and final reports to ensure sustainable savings
- Captures and communicates significant learnings to enable best practice-sharing and replication
- Deep Supply Chain process knowledge
- Proven ability to lead teams and projects
- Self-motivated with excellent organization skills
- Strong attention to detail and excellent problem solving skills
- Ability to handle multiple tasks as well as prioritize work
- Strong customer focus and service orientation
- Knowledge of MS Office products used for analysis and presentation of data, specifically MS Excel and MS PowerPoint
- Demonstrated ability to be consistent, dependable and accurate in carrying out responsibilities to a successful conclusion
- Demonstrated ability to excel in a fast paced environment with changing priorities, while maintaining a constant commitment to highest level of quality
- Previous PRMS, SAP experience is a plus
- Bachelor’s Degree in Engineering, Supply Chain Management, Logistics, Business Administration or the Equivalent
- 6 Sigma Black Belt Certification
- Minimum 5 years Project Management experience
- Minimum 5 years Change Management experience
- Minimum 5 years Training/Coaching and Mentoring Experience
- Experience with Statistical Tools / Value Stream Mapping software (Minitab, eVSM, etc.)
- Functional skills in Microsoft Word, Excel, Visio and PowerPoint
- Successful completion of a drug and background test
- 5-7 years Supply Chain Management experience / Lean 6 Sigma experience
- 5-7 years Project Management experience leading cross-functional teams
22
Continuous Improvement Manager Resume Examples & Samples
- Drive behavioural change across the site, including support functions, through coaching and influencing the leadership team at the site
- Champions the implementation of IL6S performance metrics across the site ensuring that issues and problems are made visible to all leaders on the site
- Drives the IL6S master plan for the site – including the expected outcomes and milestones of the IL6S journey for each phase and drives timely reviews with ANZ / AMEA Counterparts
- Accountable for the successful linkage of the pillars across the site – ensuring all pillars are aligned to the step change in behaviours across the site
- Provides reasonable, yet stretching targets to the site leadership team and exhibits strong leadership ability through the creation of positive tension for the site
- Provides absolute clarity to the site regarding the importance of the Compelling Business Need (CBN) and the Zero Loss Journey – and ensures that all site objectives link to both
- Progressively builds their IL6S mastery across the pillars and ensures the site are continuously challenged to succeed within each phase of the journey
- Addresses the capability needs across the site in order to deliver the Compelling Business Need and phase expectations across the pillars
- Facilitation of learning events including open house events to ensure ongoing learning to other sites
- Plays a key role in the annual site contact (business plan) – through zero loss mastery and cascade to pillar 3 year objective plans
- Drives the delivery of the site conversion productivity target ensuring collaborative efforts with RD&Q and Procurement
23
Continuous Improvement Manager Resume Examples & Samples
- Enable delivery of gross productivity targets in the order of 10% cost reduction year-on-year ongoing
- Define the strategic roadmap to deliver year on year cost improvement targets
- Coach and guide the site leadership team to develop their behaviours and ways of working on the journey to becoming a High Performing Work Team so that the concept of servant leadership is clearly understood and demonstrated
- Support the business to improve existing processes and create new ones to become most effective and efficient, making best use of available resources using the CI / L6S (Lean Six Sigma) methodology. Create a continuous improvement culture that challenges the status quo
- Implement common tools and methods to drive quicker, more transparent and data based decisions by supporting the business Integrated Lean Six Sigma (IL6S) programme
- Ensure significant, sustainable business process improvement with positive financial impact
- Know the ethical and legal compliance responsibilities of the position; lead ethically and model compliant behaviour; maintain an environment where employees can speak up without fear of retaliation; ensure employees in area of responsibility understand the compliance responsibilities of their jobs and actively participate in the compliance program
- Degree level or equivalent education in finance, business or engineering
- CI Master Black Belt qualification - preferred
- Interpersonal savvy: strong interpersonal and relationship building skills as responsibility is based less on formal power but on sound professionalism
- Drive for results: can be counted on to exceed goals successfully, steadfastly pushes self and others for results
- Excellent communicator, able to spot and frame issues to enable cross-functional decision making
- Provides clear and structured methodology making things simple for others to understand and replicate
- Planning: ability to develop clear plans and demonstrate progress against them. Project management skills
- Strong analytical skills and challenge to step change site cost base in a sustainable way
- Experience of working in a High Preforming team work culture, embraces the essence of servant leadership and actively demonstrates a Learn Do Teach approach
- Proven experience in the successful application of Lean and 6 sigma techniques
- Working effectively as part of a leadership team
- Line management experience in a manufacturing environment - preferred
- Experience of working within a TPM business ideally with experience in TPM implementation
24
Site TPM / Continuous Improvement Manager Resume Examples & Samples
- Coordinate the integration and implementation of TPM/LSS/NWT systems
- Coordinate the development of the TPM master and pillar phase plan, track progress against the plans and leads issue resolution (Gap analysis, and adjustments to plan)
- Conduct quarterly TPM audits to ensure progress towards phase goals
- Participate in department reviews/activities to ensure that work is properly integrated and progress is on track
- Lead, update and maintain Integrated Business Plan (IBP)
- Lead the plant annual Zero Loss analysis workshop
- Ensure that TPM work is impacting both results and the culture change towards the vision as determined by the plant zero loss journey
- Coordinate Total employee involvement (TEI)
- Drive culture of "TPM is the work."
- Support the plant's Natural Work Team development through the TPM pillars and through mentoring of teams
- Develop an overall understanding of the different TPM pillars, and how they integrate through the master plan to deliver the improved results
- Provide technical leadership and partner with the Operations/Maintenance Department to effect improvement on production lines. Participate in development of strategies and in guidance of the operations to achieve proposed business True Efficiency (TE) objectives through loss elimination and technical capability building
- Influence and coach pillar leaders to ensure progress towards goals
- Understand and apply financial drivers and KPI to help lead cost reduction/cost control initiatives
- Engineering or related technical or business degree
- 5 years in TPM / LSS experience preferred
- Excellent facilitation, people skills and effectively communicates with all levels of the organization
- Assumes other responsibilities and performs special functions as may be assigned by the Plant Director
- Possess strong financial control skills to support plant efforts in successful cost and capital planning performance
- Self-starter with strong leadership skills with the proven ability to set a vision, manage change, develop personnel and strategically plan for continuous improvement and overall business vision
- Technical understanding of beverage manufacturing processes to effectively lead technical resources to successfully maintain production line equipment to achieve high levels of productivity
25
Bosc-continuous Improvement Manager Resume Examples & Samples
- 5+ years work experience, Being familiar with manufacturing environment is a must
- Have been trained with continuous improvement methodology, Certified Black Belt
- 1+years direct experience to LEAD continuous improvement program for specific manufacturing environment
- Experience in applying core lean and six sigma tools in manufacturing environment
- Have closed at least one BB level continuous improvement project
- Certified BB, grasp BB Level problem solving skills
- Ability to facilitate small and mid-size team
- Capability in below lean and six sigma tools
26
Senior Continuous Improvement Manager Resume Examples & Samples
- Serving as member of the plant leadership team to drive improvements in safety, food safety, service, financial results, quality, and employee engagement
- Leading the plant wide cost savings program to meet annual targets. This includes identification, validation, coaching and execution of projects
- Leading the Overall Equipment Effectiveness (OEE) metric and process including maintaining measurement standards, facilitating improvement plans and strategies, training, coaching and monthly reporting
- Establishing and maintaining plant KPI’s and visual factory tools, and serving as KPLAS / downtime reporting system owner
- Continually expanding and enhancing knowledge levels of Kellogg Work Systems, lean manufacturing and industry “best in class” manufacturing cost savings projects and operations practices to develop a culture of continuous improvement
- Deploying and coaching Lean practices, 5S, Kaizen, and Kellogg Work Systems tools across all levels of the organization to deliver business results
- Identifying process inefficiencies and leading activities using cross-functional resources to deliver business results
- Supporting team approaches to solving problems, maintaining positive and productive relations with the hourly workforce, plant management team, sister plant resources, and corporate resources
- Benchmarking and best practice sharing across the organization
- Bachelor’s degree in technical or business field with significant manufacturing experience in project management or engineering, lean and/or six sigma
- Leadership skills utilizing Kaizen and 5S principles
- Experience driving/leading Continuous Improvement efforts
- Experience coaching Green belts in project determination, processes and delivery of improvements
27
Continuous Improvement Manager Resume Examples & Samples
- Apply business process expertise, strong analytical synthesis skills, and change leadership experience to lead process improvement projects which result in insightful and actionable recommendations
- Skillfully engage and influence senior executives and key project stakeholders to surface process opportunities, solve problems, and foster quality outcomes
- Collaboratively lead solution development and implementation activities to ensure sustainability and continuous improvement
- Develop and deliver formal process improvement training for multiple audiences and customizes lean tools and techniques to U.S. Bank
- Provide business process improvement expertise, along with organizational, financial, business, strategic and project knowledge, to assess improvement opportunities and define and deliver sustainable process solutions for several workstreams
- Deliver objective advice, expertise and specialist skills with the aim of creating value, maximizing growth, and improving business performance
- Accept overall responsibility for actions of the teams and manages priorities and assigns work appropriately on multiple concurrent process projects of varying size up to and including enterprise transformation initiatives
- Lead team or multiple teams of internal and/or external resources on a project basis; leads assessment of potential new projects; analyzes opportunities at a high-level and defines approach, including appropriate SPS involvement; works with Business Line / Function leaders to shape/manage project scope; coordinates analysis of current state process and issues/gaps; defines future state process and roadmap; develops business cases, financial realization measures/metrics, and controls; formulates final recommendations and executive presentations; trains, coaches, and mentors team members; drives implementation and ensures sustainable outcomes
- Act as a change agent by emphasizing and encouraging continuous improvement; ensures that best practices and lessons learned are shared widely and applied across the organization
- Bachelor’s degree in a relevant field. Relevant business process improvement, facilitation, and project management skills
- 10 years of progressive related experience with proficiency and understanding in one or more functions, including 5 years of experience in process-related roles; 3 years in a banking environment, and a year with financial measurements and metrics
- Demonstrated skills and experience in process assessment (documenting as-is), process analysis (identifying improvement opportunities and defining future state), and project management (leading complex projects from process assessment to future state definition to solution delivery)
- Superior analytical and problem solving skills
- Advanced skills in MS Office suite (PowerPoint, Excel, Visio, and Word)
- Ability to work through others to resolve issues and manage stringent timelines for project deliverables
- Compelling executive presence
- Several years of leadership experience at a top-tier management consultancy. Training/certification in Lean Management System, Lean Six Sigma, process improvement, facilitation, and project management methodologies/tools
- Training/certification in Lean Management System, Lean Six Sigma, continuous improvement, and project management methodologies/tools
28
Continuous Improvement Manager Resume Examples & Samples
- Serve as an active member of the Van Wert Leadership Team, fulfilling leadership duties and providing input for strategy, direction & continuous improvement
- Partner with Operations and Support Functions to develop plans to identify and address current and future challenges through use of Lean & CI tools
- Lead Continuous Improvement Framework deployment (visual controls, process standardization, leader standard work, GEMBA walks, manning strategy, daily accountability, process checks and CI for everyone)
- Integrate ELSS tool deployment through tool champions and experts (Value Stream Mapping, 6S, Standard Work, TPM, Setup Reduction, Error Proofing, Pull Systems and Flow)
- Lead, plan and support successful kaizen / Rapid Improvement Events (RIE)
- Lead plant benchmarking events and integrate and share best practices
- Lead and coordinate CI planning and assessment activities including EBS Pull, Operations Assessment (OpA) and Eaton Business Excellence (EBE) assessment and improvement activities
- Lead development of Model Plant roadmap
- Ensure capability and sustainability through Lean & CI training
- Support EBS integration through detailed understanding and effective deployment of processes and tools – including obtaining training & certifications and acting as process champion as required (e.g. EBE, OpA, MESH, Lean Six Sigma)
- Conduct performance reviews to improve organizational performance
- Critical Ourputs
- Detailed continuous improvement framework deployment strategy & plans for goal attainment
- Organizational training plans
- Effective deployment of Lean tools through workforce engagement
- Achievement of Plant balanced scorecard measures
- Bachelor's degree from an accredited Institution is required
- Minimum 5 years of manufacturing experience is required
- Minimum 2 years of continuous improvement experience is required
- Minimum 5 years of leadership experience leading direct teams is required
- Must be legally authorized to work in the United States without company sponsorship on a permanent and consistent basis
- Black Belt
- Toyota production system experience and certifications
- Experience in a high mix low volume environment
29
Continuous Improvement Manager, S Molton Resume Examples & Samples
- Working closely with the leadership team on implementation of Lean strategy and all related activities at the site
- Conducting Lean System assessments and identifying need for improvements
- Providing Lean support across the organisation, eliminating wasted and increasing customer satisfaction, cost reduction and improving financial performance
- Providing training and mentoring on both methodologies
- A degree or equivalent in any engineering discipline
- Certified Lean practitioner (Black Belt desirable), trainer and mentor
- Strong management/ operational experience
- Proven experience in leading and implementing Lean in a manufacturing/ engineering corporate environment
- Strong project management and operational experience
30
Continuous Improvement Manager Resume Examples & Samples
- Works through the leadership team to lead the development and implementation of the site Lean and Six Sigma strategy, actions, and cross-functional activities
- Provides site Lean and Six Sigma training
- Conducts Eaton Lean System (ELS) assessments, and identify performance gaps
- Works through the leadership team to prioritize improvement activities and close gaps
- Utilizes Lean and Six Sigma tools to eliminate waste driving customer satisfaction, cost reduction, and improved working capital performance
- Leads the continuous improvement (Lean and Six Sigma) team
- Assists in improvement activities including training, mentoring, facilitating Kaizen events, Six Sigma projects, tool deployment, benchmarking, etc
- Provides site Lean and 6 Sigma Mentoring
- Build Continuous Improvement and Lean culture to drive change
- Minimum 3 years of lean manufacturing experience is required
- Bachelor's degree in Engineering
- Formal training/certification in Lean ( 5S, Standard work, Value Stream Mapping (VSM), Setup Reduction (SUR), Total Productive Maintenance (TPM), Lean Material Flow (LMF) and 6 Sigma
- Experience in a mixed model environment
- Operations experience
- Experience in implementing Lean in Low volume High mix type product environment
- Proficient in Power Point, Visio, Minitab ( or any Statistical software)
- Ability to manage multiple projects/activities across multiple sites
- Experienced Lean and 6 Sigma trainer and mentor
- Multiple years of related professional and Supervisory/Managerial experience
31
ACE / Continuous Improvement Manager Resume Examples & Samples
- A minimum of five years experience in the field of Continuous Improvement within a manufacturing environment, preferably
- Must demonstrate a knowledge of the applications and teaching principles and tools of Continuous Improvement
- Should have prior experience with Continuous Improvement events and projects in production and business process areas
- Possess a working knowledge of supply chain/inventory management and Kanban systems
- Must demonstrate effective communication skills across all levels, to include training, facilitating meetings and events, written reports and presentations, and project updates
- Must be able to travel, approximately 20%, domestic and international
32
Continuous Improvement Manager Resume Examples & Samples
- Demonstrated success in leading change and transformation efforts
- Organizational agility and ability to influence without authority across all levels of the organization
- Successful experience with the execution of CI programs
- Knowledge of strategy deployment and related reporting techniques and ability to integrate business and financial objectives into CI decision-making
- Strong interpersonal, verbal and written communication skills and can create effective presentation
- Strong analytical skills and statistical knowledge
- Must possess the ability to define problems, collect data, establish facts, and draw valid conclusions
- Candidate should possess basic knowledge in the manufacturing/processing of mechanical components
- Must have intermediate to advanced computer skills, and be able to operate various software programs, such as MS Word, Excel, PowerPoint, Outlook, etc. ACE Associate, ACE
- Industry recognized certification in lean, six sigma or similar discipline or equivalent experience preferred (or ACE internally)
33
Quality & Continuous Improvement Manager Resume Examples & Samples
- Provide consultancy services to Resort Operations, General Managers and Hotel Management on attaining higher levels of process quality to drive business performance and building “Great Hotels Guest Love”. These include implementing multiple platforms of learning and tracking of results, and customizing them to meet operations needs
- Provide prompted analysis and solutions to help greater resort operations team and hotel management teams understand the root causes and execute high impact solutions for Guest Satisfaction. Then together with Regional VP Operations, Regional General Managers, review and approve Action Plans to maintain and drive performance on Guest Satisfaction
- Drive annual Quality Evaluations, measuring compliance of our hotels & resorts to IHG’s Fire Life Safety, Design and Brand Product & Service Standards, and follow up with hotels to ensure that Management Action Plans (MAP) are executed
- Working together with hotel teams, to develop various learning systems/platforms and toolkits to better build up the Continuous Improvement capabilities of resort team thus to drive process performance with high linkage to key business objectives
- Maintain sustainable idea generation and adoption through Ideas Library, so that knowledge and techniques developed in a business unit can be replicated across IHG in a way that measurably improves IHG’s overall business performance
- Strong ability to impact and influence senior management teams to work better together differently, but in a systematic way
- Ability to analyse information, diagnose root causes and reach conclusions based on fact based data
- Communication and presentation skills to senior management teams
- Tertiary education or professional qualifications
- Management or consulting experience in the services industry
- Broad knowledge of General Management
34
Continuous Improvement Manager Resume Examples & Samples
- Develop and lead implementation of strategies supporting EOS and E3
- Manage / monitor progression of the site through the Enterprise Excellence Assessment (EEA) criteria
- Identify risks to EEA progression goals and implement mitigations
- Interface with the platform Continuous Improvement director and other site Continuous Improvement focal teams
- Chair the local site Guidance Management Team (GMT)
- Facilitate the annual Policy Deployment & Macro Planning process and monthly reviews
- Educate and train leaders and employees on E3 tools and other continuous improvement methods and processes
- Drive the use of the E3 tools (e.g. 5S, Standard Work, TPM, etc.) across the organization to reduce lead times and the cost of poor quality and improve product first pass yield and on-time delivery
- Facilitate strategic Kaizen Events and execute site wide leadership weeks in conjunction with platform peers
- Drive the organization to recognize and attain best in class performance and processes through benchmarking activities inside and outside of the Esterline businesses. Support standard work development efforts for both manufacturing and non-manufacturing business processes
- Manage and develop a high performing Continuous Improvement team
- Support the LEAN Transformation Teams to ensure project success
- 8+ years of relevant continuous improvement or LEAN experience
- 2+ years managing and developing a team of direct reports
- Relevant industry experience strongly preferred
- Strong knowledge and application of LEAN tools, TPM, Six Sigma methodology or other quality improvement processes
- Experience in planning and leading events/workshops, project management, team building/facilitation and event coordination
- Powerful team building skills with the ability to lead and coach multi-discipline project teams and plan schedules to achieve goals
- Strong initiative to act and ability to empower and mentor others to succeed throughout all levels of a matrixed organization
- Experience in leading culture change
- Experience with creating, modifying and delivering training to all levels of an organization
- Solid professional presentation and reporting skills in a variety of environments and with a variety of media
- Strong proficiency with the Microsoft Office suite
- Highly customer focused with the ability to develop solid relationships at all levels within a matrixed organization
- Ability to travel as needed in the US and internationally
35
Continuous Improvement Manager Resume Examples & Samples
- Work closely with our front line agents to identify process issues and work with key stakeholders to improve the agent and customer experience
- Investigate issues identified, able to present findings and recommendations of improvement and associate a benefit saving
- Manage, deliver and track process improvements through to closure and have a strong influence to deliver the high priority issues
- Develop your skills and knowledge to become a subject matter expert?
- Work closely with the training account, knowledge and communications managers, to review and sign of design of training material, knowledge content and communications to successfully deploy improvements whilst aligned to our processes and policies
- Participate and contribute in a series of workshops to help shape requirements and identify risks and issues
- Work with key stakeholders to influence the system release road map
- Play a key role on improving our front line processes to delivery business objectives, such as first time fix, contact handling time, transfers, customer satisfaction and customers leaving
- Process Mapping Experience
- Strong data analysis
- Working in a Contact Centre Environment
- I champion the customer by putting them front and centre in all things
- I can deliver value for TalkTalk by making things simpler, better and cheaper
36
Continuous Improvement Manager Resume Examples & Samples
- Facilitate management team to identify and develop annual improvement plans consistent with and in support of the strategic plan and business operating plan. Identify goals for CI events and potential quantifiable savings
- Establish, lead, and maintain a Continuous Improvement Steering Committee
- Facilitate the selection, scope, and planning of specific improvement projects
- Develop training materials and effectively deliver those materials in a team environment to ensure employees throughout the facility are trained in CI concepts and philosophy
- Facilitate CI events and teams
- Initial organization and planning
- Event logistics
- Monitor and maintain event schedules
- Follow up and audit event progress to ensure results are acheived and sustained
- Resolve implementation issues, creating and managing implementation communication processes, and ensuring consistency of implemented processes and programs throughout the facility
- Coordinate with project leaders and project Chairs to eliminate barriers. Raise awareness if/when needed
- Manage and take a lead role in promoting and improving quality processes, expectations, and results
- Responsible for motivating, coaching, and developing people in department
- Create and execute MPS objectives; meet MPS commitments and work within the guidelines of MPS
- Incorporate Milgard's vision and value into day-to-day activities and behaviors; guide and motivate others to remain committed to the Milgard philosophy
- Participate in the Leadership Development Program (LDP) for the location
- Create and execute MPS objectives, meeting MPS commitments and work within the guidelines of MPS; reflect Milgard business values and the Milgard philosophy in all business interactions
- A minimum of 4 years experience related to continuous improvement or similar project management
- A minimum of 5 years working in a manufacturing environment, with at least 2 years in a supervisory capacity
- Prior cross functional team facilitation experience preferred
- Strong background in problem solving, planning, and organization
- Ability to read, analyze, and interpret financial reports and legal documents
- Sense of urgency and self-motivation; ability to work independently
- Ability to motivate employees to achieve results
- Computer literacy with ability to learn new computer software programs
- Excellent written and oral communication skills; ability to present to senior management
- Must be results oriented with a people development affinity; proactive in attacking challenges and confident in setting and achieving stretch goals
- Must be able to teach and generate results while enhancing the Milgard work environment and supporting the Company philosophy
- Must have proven employee development and team building skills
37
Continuous Improvement Manager Resume Examples & Samples
- Overall program communications (future events, event updates, report outs)
- A minimum of 5+ years’ experience leading or driving Continuous Improvement/Lean initiatives
- Experience in a manufacturing environment, with some of those years in a leadership/supervisory role
- Proven employee development and team building skills
- College Degree preferred, but may be substituted by relevant work experience
- Proactive(!) in attacking challenges and confident in setting and achieving stretch goals
- Must be able to teach and generate results while enhancing our work environment and supporting Milgard’s philosophy of Respect, Service, and Excellence
38
Continuous Improvement Manager Resume Examples & Samples
- Champion, develop and sustain a culture of continuous improvement (CI) and knowledge about related methodologies/ activities (Lean, Six Sigma, ALPS) across all areas of the site with a strong focus on manufacturing and operations
- Deploy and sustain the ALPS capability and improvement program including a coaching support structure to drive CI initiatives and ensure sustainability of improvements
- Champion deployment of change management processes and tools to realize the business strategic objectives
- 7+ years of relevant work experience (operations, production, maintenance, logistics, (process) engineering, continuous improvement, etc.)
- Bachelor degree (degree related to technical, business, engineering, or economics fields most applicable). If higher vocational training then longer work experience is required
- Must be willing to train as an AkzoNobel continuous improvement expert as a minimum, within 12 months after assignment
- Experienced, certified Black Belt strongly preferred
39
Continuous Improvement Manager Resume Examples & Samples
- Ensure compliance in all aspects of safety with all applicable regulations (AkzoNobel and regulatory)
- Actively drive Continuous Improvement efforts in Augusta
- Actively participate in BBS program in Augusta
- Conduct 5S activities in the office area and supervise visual management in the plant
- Drive performance through KPIs and develop and improve metrics continuously
- Maintain and further develop continuous improvement program at the site
- Develop and expand local capabilities in applying continuous improvement tools and methods (Lean, Six Sigma) and promote a structured problem-solving approach
- Facilitate CI initiatives and inject passion for this activity by providing a vision and direction for the future development and performance of the site
- Give reinforcement training on selected CI topics
- Local contact for Continuous Improvement related initiatives including Lean Six Sigma
- Train and coach site management and staff in leading and implementing change and ensure sustainability of improvements
- Conduct shop-floor activity analyses, interviews, data gathering and analysis and compile into improvement opportunities and impact
- Support the site leadership and staff in improvement project idea generation, project chartering, action planning and implementation
- Coordinate and/or support Yellow/Green/Brown Belt improvement projects at the site ensure the tracking of benefits of local L6S projects and that projects are driven to completion and/or closure
- Responsible for further development, implementation of, training and coaching in, and correct execution of MOC system
- Champion the implementation of the organizational behavior aspects of the Site Transformation Plan
- Develop metrics and periodically assess organizational effectiveness
- Works in close cooperation with site management team to ensure optimized performance of the site
- Performs other duties as assigned by the Site Manager
- Bachelor’s degree with 5+ years of solid experience in a chemical plant environment in production, maintenance or logistics management; or process/production engineering
- Experience in leading change management
- Effective leadership, interpersonal skills, performance management, and people development skills
- Experience in Lean and/or Six Sigma implementations
- Experienced in identifying and tracking KPIs
- Must be willing to be trained as a CI Lead Practitioner and commit to requirements for certification
- Experience using Six Sigma Methodology
- Ability to communicate to all levels of the business (production operators to senior executives)
- Must be able to influence or persuade others that are not direct reports
- Demonstrated success working in a team oriented environment
- Advanced level computer skills (i.e. spreadsheets, Microsoft Office, SAP system) to prepare statistical reports
- Ability to creatively solve problems while maintaining a timely and cost-effective approach
- Good organizational and analytical skills
- Ability to work under pressure in a deadline-driven environment
- Ability to analyze and solve complex problems and cause and effect analysis
- Physical demands: Must be able to access all areas of site
- LI-ABN
40
Site Continuous Improvement Manager Resume Examples & Samples
- Set visual management standards and lead to implement throughout the whole site
- 10+ years of relevant work experience (operations, production, maintenance, logistics, (process) engineering, continuous improvement, etc.)
- Experience in continuous improvement methodologies such as Lean, Six Sigma, TPM
- Knows how to use the skills and knowledge of the team to design and implement solutions
- Experience with practical implementation of change programs a plus
- Extensive experience in coaching and engaging others; able to impart knowledge to others
- Strong computer skills (PowerPoint, Excel, Word, SharePoint, JMP); able to prepare various formats of documentation associated with CI programs
41
Continuous Improvement Manager Resume Examples & Samples
- Bachelor degree (degree related to technical, business, engineering, or chemistry preferred)
- Confident and experienced in coaching others
- Able to multi-task in high-pressure environments
- Excellent communication, presentation and conflict resolution skills on all organizational levels; ability to gain respect and trust through situational leadership and integrity and inspire others to follow and participate in the change process
- Good team player, knows how to build his/her own network
- Must be willing to train as an AkzoNobel lean six sigma black belt (where necessary)
- May require some travel
42
Site Continuous Improvement Manager Resume Examples & Samples
- Deploy and sustain the ALPS manufacturing program including a coaching support structure to drive CI initiatives and ensure sustainability of improvements
- Coach Advanced and Lead Practitioners and local staff/MT on site and give reinforcement training on selected topics
- · 10+ years of relevant work experience (operations, production, maintenance, logistics, (process) engineering, continuous improvement, etc.)
- · Bachelor degree (degree related to technical, business, engineering, or chemistry preferred)
- · Confident and experienced in coaching others
- · Fluent in English, both verbal and written
- · Experience in continuous improvement methodologies such as Lean, Six Sigma, TPM
- · Prior line management or team leader experience; knows how to use the skills and knowledge of the team to design and implement solutions
- · Experience with practical implementation of change programs a plus
- · Solid project and stakeholder management experience
- · Extensive experience in coaching and engaging others; able to impart knowledge to others
- · Able to multi-task in high-pressure environments
- · Excellent communication, presentation and conflict resolution skills on all organizational levels; ability to gain respect and trust through situational leadership and integrity and inspire others to follow and participate in the change process
- · Strong analysis and problem-solving skills, able to identify and structure issues, run accurate (also statistical) analyses and synthesize recommendations
- · Good team player, knows how to build his/her own network
- · Strong computer skills (PowerPoint, Excel, Word, SharePoint, JMP); able to prepare various formats of documentation associated with CI programs
- · Must be willing to train as an AkzoNobel lean six sigma black belt (where necessary)
- · May require some travel
43
Quality & Continuous Improvement Manager Resume Examples & Samples
- Manage OpEx program and Quality department, including operation of the plant lab and its staff, and a Continuous Improvement Leader
- Assess existing operational, manufacturing, lab and business capabilities across the site, including monitoring/establishing key KPIs for the site
- Mentor and coach Lean/Six Sigma candidates toward completion and certification of improvement projects
- Design procedures aimed at improving efficiencies, reducing cost and variability, eliminating waste, and improving safety standards
- Implement new processes and technologies through business improvement and Six Sigma initiatives aimed at improving the site’s manufacturing and lab capabilities. This will include delivering specific improvement projects (engineering, reliability, safety, cost control, process control, and energy reduction) across the site
- As a key and active member of the Site Leadership Team, work regularly and closely with other leaders (e.g. business, production, R&D, supply chain, engineering, etc.) across the site to institute best practices, identify areas for improvement and development, establish buy-in for operational excellence initiatives required to support the site’s strategic agenda and drive meaningful change wherever required
- Foster teamwork with subordinates, peers and superiors both internal and external to Edgar
- Bachelor’s Degree is required. A degree in an engineering discipline preferred
- 10+ years demonstrated leadership experience in a manufacturing environment
- Must have training and certification in Lean/Six Sigma
- Must have experience with quality systems. Experience with ISO9000 systems a plus
- Demonstrated ability to lead, direct and manage cross functional teams in a fast paced, results oriented environment, with technical competence and a focus on continuous improvement
- This individual should have operating experience and be comfortable interfacing across the organization, from operations to supply chain, R&D, and EHS, to drive a meaningful transformation initiative while managing multiple constituents
- A demonstrated track record of implementing & managing operational excellence initiatives and business improvement processes
- The successful candidate will have a proven track record and ability to manage multiple projects and possess a thorough understanding of world class manufacturing processes, systems and procedures that deliver results
- Financial management skills to include fixed cost control
- Experience with Operational Excellence programs and Continuous Improvement in leadership and contributing roles
- Excellent communication, negotiation, problem solving and organizational skills; including the ability to interface with internal & external customer contacts. Must be able to communicate to all levels of the organization
- Must possess a high level of initiative, and independent decision-making ability
- Establish and maintain facility environmental, safety, and health standards to minimize employee and community exposure
- Experience working in a union environment is a plus
44
Quality & Continuous Improvement Manager Resume Examples & Samples
- Continuous Improvement - Lead, coach and/or facilitate Continuous Improvement projects. Identify & select continuous improvement projects, set targets and track results. Manage and execute Lean Six Sigma training programs. Lead continuous improvement workshops and kaizen events. Provide process improvement and variation reduction expertise as required
- Quality Control Lab Leadership – Manage Quality Supervisor and laboratory technician(s) to ensure products meet customer requirements. Back up support to laboratory testing and processing as needed
- Management Systems – Ensure site compliance with ISO standards and other regulatory requirements (e.g., RCMS). Manage nonconformance system to ensure customer response in a timely manner and corrective action to eliminate issues. Management of document control, internal auditing and other good manufacturing processes according to ISO and other regulatory requirements
- OpEx – Lead development and execution of 4-year Operational Excellence plan
- EHS - BU liaison on the Process Safety Center of Expertise as an extended team member. Manage the site Process Safety Management (PSM) and EPA’s Risk Management Program (RMP). Lead process hazard analysis (PHA), the management of change (MOC) system and Pre-startup Safety Review (PSSR) documentation; Develop and maintain engineering documentation for regulatory compliance. BASF Exposure Reduction Process (ERP) leadership, coordination, and implementation via a cultural change
- Training Program Management – Manage training program requirements/content specific to site and corporate. Facilitate completion of specific unit training/content through department leaders. Coordinate with Site Support Specialist in LMS management
- BS Degree in Engineering, Chemistry or related field
- 5+ years manufacturing, process operations experience
- Experience in a minimum of two different positions in a manufacturing environment
- Demonstrated plant experience in continuous improvement, problem solving, lean principles, control plans & process control, and mechanical aptitude
- Ability to apply statistical process control and problem solving techniques
- Comfortable interacting at all levels of the organization
- Excellent individual and team facilitation skills required
- Well-developed communication and influencing skills
- Demonstrated ability to facilitate and/or lead project teams to successful implementation
- Demonstrated experience with a strong sense of entrepreneurial drive and motivation
- Continually fosters innovation and embraces change, especially in difficult environments
- Has the courage to stand behind tough decisions, even those not accepted by all
45
Continuous Improvement Manager Resume Examples & Samples
- Identify and facilitate process improvement initiatives to improve operational performance, productivity and quality
- Conduct root cause analysis using Lean Six Sigma Methodology (e.g fish bone, 5 why analysis, wastes identification, process mapping, etc)
- Carry out advanced data collection and statistical analysis when identifying problems and prioritizing solutions
- Standardize processes (whenever possible) across regions
- Recommend error-proofing techniques / processes to reduce errors and reworks in manual transactions
- Project manage identified solutions and ensure that infinitives are implemented on time
- Conduct Lean Six Sigma Overview training in the organization and mentor the individuals in delivering Lean Six Sigma projects
- Drive a culture of change and continuous improvement in the organization through training and application through projects
- Bachelor’s Degree in Business Administration, Engineering or related field
- Must have at least 6+ years’ experience in process improvement and Lean Six Sigma application
- Must have Black Belt Six Sigma Training and Certification
- Ability to work and influence others in a fast-paced environment
- Ability to work shifts as required
46
Continuous Improvement Manager Resume Examples & Samples
- Trained and/or Certified in key disciplines (i.e. Lean, Six Sigma, 5S, other
- Experience in deploying Lean or other Continuous Improvement methodologies in operations of comparable size
- Strong knowledge of Industrial Engineering
- Strong proficiency in Work Measurements
- Strong financial and analytical ability
- Broad capability building in Continuous Improvement
- Proficiency in managing business analytics to determine optimum output and results
- Proven track record of successful change management and accomplishments implementing productivity and cost reduction programs
- Strong and convincing communication skills
- Ability to work with leadership across the enterprise to bring about positive behavioral change
- Ability to work positively with front line teams to deliver on project goals
- (2) or more years of experience in coaching and leading professional teams
- At least (2) years of managerial and supervisory experience including budgeting, recruitment, and people management required
- At least (5) or more years of corporate and field continuous improvement implementation experience
47
Continuous Improvement Manager Resume Examples & Samples
- Install a continuous improvement program at the site
- Train and coach site management and staff in leading and implementing change
- Support the site leadership in improvement project idea generation, project chartering, action planning and implementation
- Lead Brown Belt improvement projects at the site for 30% of time
- Coordinate the site Brown and Green Belt improvement projects, ensure the tracking of benefits of local projects and that projects are driven to completion and/or closure
- Three-plus years in an operational role, e.g. production, maintenance, (process) engineering, and/or logistics, in a manufacturing setting
- Demonstrated ability to exercise sound judgment under pressure. Able to support and coach colleagues
- Experience in line management or team management in large projects
- Experience in change processes; lean and/or six sigma implementations or similar is beneficial
- Must be an AkzoNobel trained Brown Belt (CI Practitioner) or be willing to be trained as a Brown Belt and commit to requirements for Brown Belt certification
- Risk-friendly, able to take a decision quickly without mastering all parameters
- Able to lead workshops and working groups
- Effective communications skills, from managers to line operators
- Good problem-solving skills, able to identify and structure issues, run accurate (also statistical) analyses and synthesize recommendations
48
Rapid Continuous Improvement Manager Resume Examples & Samples
- Deliver Value – work with champions (VP/SVP level) to deliver value to the business; value will typically be measured in 12 months of cash flow improvement
- Develop Relationships – much of the Assoc. RCI Manager’s success will come from people and process; developing the right relationships and using a collaborative approach will insure overall success
- 2 years of work experience with Continuous Improvement activities
- Green Belt
- Able to demonstrate proficiency in PowerPoint and excel with experience pulling and analyzing data
- Minimum 2 years experience in facilitating and leading small group improvement projects
49
Continuous Improvement Manager Resume Examples & Samples
- Develop site TEOA deployment plans consistent with business unit /plant strategic and operational plan
- Support and mentor site based TEOA Practitioners / Kaizen Facilitators to enable them to succeed in the TEOA deployment and sustaining. Train team members, management and staff in all TEOA tools
- Identify and organize resources required to achieve successful implementation in accordance with plan
- Manage and control individual project teams and deployment plans at both site and functional levels
- Monitor progress against plans, achievement of continuous improvement and progression to higher star assessment levels
- Monitor and report site level measurements and performance to star assessment levels
- Lead the Site TEOA project teams, develop value stream maps and execute the TEOA implementation plan for the site to achieve the plant level TEOA metrics and goals while ensuring alignment to the business unit strategy
- Create, plan, lead and follow-up of the TEOA implementation plan and ensure TEOA actions are visual to stakeholders and are driven to a sustainable closure
- Facilitate TEOA Kaizen events throughout the site
- Account for predicted savings and track, validate and post to financial/operational results
- Provide leadership on lean thinking, lean processing and lean production
- Replicate examples of excellence across site and communicate this to other TEOA Practitioners within business unit
- 5-7 years of technical / operations experience with focus on production, logistics or industrial engineering and finance
- Bachelor's Degree in Engineering or related field, Master's Degree preferred
- 3-5 years of experience as Lean practitioner with demonstrated evidence of sustained, successful lean activities within specific value streams
- Previous experience in leading continuous improvement activities at value stream level essential
- Formal Mentoring, Facilitating & Coaching Training
- DMAIC Six Sigma Master Black Belt strongly preferred
- Process Improvement Management
- Previous hands-on and practical experience in using value stream mapping and implementing improvement tools with proven results in at least the following areas: 5S+1, Visual Factory, Standard Work, Quick Changeover and TPM preferred
- Have the patience, perseverance and passion to drive the TEOA culture across the plant
- Credibility and experience to work effectively and directly with the site management team
- Excellent communication, coaching and inter-personal skills at all levels from the shop floor to top management
- Strong team leader
- Analytically minded and data-driven
- The role may involve some travel to other sites within the business unit and will require overnight stays
- US citizen or perm legal resident required
50
Quality & Continuous Improvement Manager Resume Examples & Samples
- Customer First – Work with commercial team leaders to ensure ongoing conformance with changing customer requirements, proactively identifying “hot spots” and developing truly effective improvements
- Continuous Improvement - Lead, coach and/or facilitate Continuous Improvement projects. Identify & select continuous improvement projects, set targets and track results. Manage and execute Lean Six Sigma training programs. Lead continuous improvement workshops and kaizen events. Provide process improvement and variation reduction expertise as required. Coordinate OpEx plans and results with N-EDN leadership
- Quality Control Lab Oversight – Oversee the Quality Group Leader and his/her staff to ensure products meet customer requirements, using lean tools to increase lab effectiveness
- Management Systems – Ensure site compliance with ISO standards and other regulatory requirements (e.g., RCMS, PSM/RMP) together with Monaca Dispersions & Resins staff. Manage nonconformance system to ensure customer response in a timely manner and corrective action to eliminate issues
51
Lean & Continuous Improvement Manager Resume Examples & Samples
- Creation and management of Standard Work Instructions
- Utilize Continuous Improvement through Employee engagement in ideas and implementation
- Develop metrics and dashboard measures designed to include the entire plant population in both understanding of key performance indicators and necessary actions to improve KPI's
- Utilize improvement tools including A-3's, Ishikawa diagrams, Visual Management Boards, Daily Management Activities
- Work with Accounting to tie improvement activities to DI's
- Teach all ABS fundamentals to internal customers
- Review and aid in development of Hoshin plans
- Coach and support at the Center of Excellence
- Coach weekly Problem Solving Teams
- Proficient with Windows and MS Office Suite
- Ability to prepare and deliver effective presentations
- Strong facilitation and training skills to deliver Lean Manufacturing concepts, principles and practices
- Must have strong team building skills and the ability to facilitate team-based initiatives
- Excellent written and verbal communication skills, business process improvement knowledge, and ability to train others with diverse backgrounds and education levels
- Minimum 5 years of experience facilitating and managing Lean Manufacturing programs
- Strongly prefer the Bachelor’s Degree is in Mechanical Engineering or Industrial Engineering
- Experience managing 5S programs
- Lean Six Sigma Black Belt certified
- Proficiency with Minitab
52
Continuous Improvement Manager Resume Examples & Samples
- Lead, coach or provide technical expertise for Continuous Improvement/Kaizen projects
- Conduct regular Gemba Walks in key areas to identify gaps for further improvement and engage/drive a Continuous Improvement culture
- Proactively learn, develop, share best practices and customize new methods and techniques (Lean/Six Sigma, Agile, Design Thinking, Change Management) to create the Continuous Improvement program at Intarcia
- Provide coaching, training and leadership to deploy Continuous Improvement program
- Develops, maintains and monitors key performance metrics
- Act as an internal consultant/advisor to de-bottleneck and improve cumbersome/inefficient processes
- Bachelor’s degree science or business-related field
- Minimum 3 years of continuous improvement leadership applying the elements of lean/operational excellence
- Expertise in leading Lean Kaizen events in a manufacturing environment is highly desired
- Experience and track record in making rapid measurable improvements
- Strong pharmaceutical GMP manufacturing expertise
- Proven ability to communicate clearly and present key information objectively and collaborate effectively with management
- Proven leadership skills managing project teams with successful results
- Lean/Six Sigma Greenbelt or Black belt Certification highly desired
53
Continuous Improvement Manager Resume Examples & Samples
- Coordinate and prioritize resources: Own the facilitation of the local LSC (Leadership Steering Committee) to agree, prioritize, plan, coordinate and follow up on all process improvement activities. Ensure focus on best customer experience at the lowest cost. Manage the FC improvement plan
- Act as Liaison between FC and EU: Help drive leverage of cross-FC process excellence. Build and maintain close relationship with EU Process Owners and FC Process Engineers across Europe
- Develop a culture of continuous improvement and lean thinking
- Very strong analytical skill capability, being able to translate operational issues into workable solutions. Able to dive deep whilst seeing the big picture
- Degree level or higher
- Czech language skills (written and spoken) disirable
54
Continuous Improvement Manager Resume Examples & Samples
- Lead and contribute to ad hoc accounting projects set by the ASO director
- Partner with country accounting managers and their teams in Warsaw and Thane to promote, operationalize and standardise best practices in various R2R processes
- Project manage and co-ordinate the completion of annual EMEA Intangibles Impairment testing under US GAAP and report to Accounting policies team in the US
- Project manage and co-ordinate the quarterly MRC (Management Reporting Certification) reporting process across EMEA
- Represent EMEA in corporate wide accounting projects involving implementation of new accounting policies o new accounting systems
- Assist in resolving SOX and Internal audit findings relating to any of the EMEA countries and putting in place or strengthen the key controls and closing those findings
- Project managing and delivering the EY group audit for EMEA by liaising with the US, in-country controllers and EY
- Qualified ACCA accountant
- 5-10 years of post-qualification accounting experience in Big 4 accounting firms or large multinational companies
- Experience of process improvement in R2R and proven record of business partnering across matrix organisations
- Strong and clear communication in English
- 10-15% overseas travel may be required
- Strong problem solving ability and thinking outside the box
- Being able to work under pressure and deliver to multiple deadlines
- Being well organised and ability to influence people
55
Senior Continuous Improvement Manager Resume Examples & Samples
- Serve as liaison between Operations and BU Engineering for releasing stable new products from prototyping to high volume manufacturing by ensuring that critical parameters are identified and monitored as well as optimized using sound Six Sigma Methodology and SQC/SPC. (NPI/NPD – Process R/D)
- Coordinate work necessary to improve and optimize our overall Continuous Improvement results as measured by regularly scheduled audits and performing Value Stream Mapping assessing our processes, tools (RJG) and efficiency tool utilization and enhancement using sound Lean and Six Sigma Tools
- Provide technical leadership and key training for Lean Six Sigma methodology and application
- Collect and analyze data for determining an improvement strategy in this role, and provide process recommendations to achieve cost reduction targets. The ability to link cost reduction thru Lean Sigma Accounting and P/L will be required
- Lead high visibility strategic projects. Identify, prioritize and manage funnel of the highest value cost savings opportunities and coordinate the various project teams assigned to ensure proper resourcing to drive completion of projects
- Champion the elimination of process variation as key to business improvement
- Passionately drive and promote the virtue of process excellence, visibility and awareness across the business
- Act as change agent by challenging current state through demonstration of the application of the Lean Six Sigma methodologies, provide guidance and knowledge to lead and change behaviors at all levels of the organization
- Effective communicators, which is essential for the many roles they serve: trainers, coaches, and mentors. Speak to a board array of audiences (from shop floor employees to executive management)
- Business acumen and the ability to display the linkage between projects and desired business results
- Immerse in daily production and operations issues to ensure that we produce a quality product, deliver against our committed customer service goals, and optimize efficiency/productivity
- Establish a strong presence on the floor to set and communicate expectations, standards, and evaluate results so all employees understand expectations
- Facilitate a process of best practice sharing internally within the plant as well as externally with other Entegris facilities
- Management of communication process to present the status of plant improvement projects
- Travel up to 25%, as required
- Bachelor’s Degree in a relevant field of study. (Engineering or Sciences) requested
- Advanced certification(s), understanding and the hands on use of tools/software in DMAIC, Design for Six Sigma (DFSS), Lean methodologies, and/or other continuous improvement methodologies
- Experience in teaching, coaching, and mentoring Lean Six Sigma activities in a multinational company
- Track record of leading Lean Sigma Transformation in a Multinational and Multisite Environment
- Master Black Belt Certification from leading Six Sigma Company recognized by the International Society of Six Sigma Professionals highly desirable
- Manage a robust review process for project mining, selecting, scoping and prioritizing Lean & Six Sigma projects
- Knowledge of Lean Sigma accounting and the linkage Financial P/L is highly desirable
- Hands on approach, ability to see the big picture at an executive level as well as able to mentor engineers at a frontline level
- Ability to communicate and having presentation skills at all level of the organization
56
Continuous Improvement Manager Resume Examples & Samples
- Lead, define and develop CI activities for the warehouse operations to drive results
- Improve culture, ensuring that all requirements are met to improve working practices across the site
- Identify and investigate saving opportunities covering all projects & processes
- Train and educate the organisation and implement CI methodologies to include Six Sigma, 5S GB & YB training, and Kaizen
- Work across the business to lead cross functional teams in identifying, progressing and realising the return associated with all opportunities for business improvement
- Considerable emphasis on liaison with production, quality and supply chain partners
- Ensure all projects are carried out in line with Health & Safety practices
- Compile, display and analyze data in a logical format and develop solutions and prepare statistical and metrical reports
- Determine data needed to manage and sustain current process capability and drive further improvement
- Proven record of managing change and continuous improvement is essential
- High level of technical knowledge regarding CI methodologies keeping in line with the latest external developments
- Management experience in a fast moving manufacturing environment, including team management
- Experience of managing workloads and both setting and achieving KPI’s
- Good IT skills required with ability to effectively use other advanced packages
- Ability to apply principles of logical or scientific thinking to a wide range of intellectual and practical problems
- Good communication skills to make effective and persuasive presentations on controversial or complex topics
- Be willing to be ‘hands on’ in actively participating practically directly and indirectly
- Qualified and experienced in all or most of the following areas
57
Lean Continuous Improvement Manager Resume Examples & Samples
- Work with cell/site/value stream leaders to identify and prioritize improvement initiatives to achieve business results using best practice Process Management tools ( SIPOC, Control Tower, Impact/Maturity analysis, MFA, QCPC, etc. )
- Bachelor’s Degree in a related field required
- 7 years leading high impact teams
- 7 years communicating technical data to a broad audience
- 7 years managing portfolio of projects
- 7 years Manufacturing Repair Operations
- 7 years technical Background in Lean Manufacturing
- UTC ACE Ops Practitioner Certification
58
CE Capability & Continuous Improvement Manager Resume Examples & Samples
- Driving a culture of continuous improvement
- Optus Lean Six Sigma (& related CE) Program Management
- Optus LSS (& related CE) Program Logistics
- Stakeholder & Cross Functional Engagement, and Coaching & Mentoring, Training Delivery; &
- Other project initiatives include leading the planning and co-ordination of the CE Graduation and awards ceremony, the Optus LSS belt community of practice activities, including the belt community events and CE capability team, plus the planning and co-ordination of the annual charity event, an opportunity to provide basic Lean skills to a number of our charity partners
- Tertiary qualified with Lean Six Sigma Green Belt advantageous (solid CI experience will speak volumes and Green Belt training will be provided upon commencement if needed)
- Proven working experience delivering financial results leading Lean Six Sigma transactional, manufacturing and other process improvement projects to deliver customer experience outcomes
- Strong ability to coach through project completion, with strong influencing skills across all levels of the organisation
- Advanced business acumen and ability to interpret financial data, underpinned by excellent facilitation skills, including a default ability to coach on facilitation
- Expertise in process management, supported by strong communication skills and ability to adapt communication styles to specific audiences
- Project, program, change management and execution skills; &
- Strong IT literacy (including MS Project, PowerPoint, advanced MS Excel)
59
Continuous Improvement Manager Resume Examples & Samples
- Demonstrates a mindset and commitment to continuous improvement across the operation (i.e. defines improvement goals, establishes accountability through QDRC metrics, uses Lean/Six Sigma tools and techniques to continually improve processes and business results, and establishes a mindset within operations to document and control processes; promotes safety and housekeeping; uses facilitative leadership)
- Acts as a liaison across the business segment with other functional areas (e.g. Production Engineering, Development Engineering, and Manufacturing)
- Accountable for the technical aspects of problem solving, systems implementation and validation for projects and services (e.g. Technical Quality or Continuous Improvement)
- Provide leadership to direct reports (or have dotted line relationship) by leading, managing, supporting and coaching members ensuring continual development of competencies
- Develop and maintain an appropriate organization structure to support the process improvement function that is aligned with the business segment, CoE and Company alignment grids, strategies, T-MAP, etc
- Plan and manage resources to profit plan and capital plan
- Collaborate with other CI organizations across Woodward to ensure alignment of the CI, Lean/Six Sigma philosophies and methodologies and overarching best practices that is impactful and current with 'Best in Class' industry practices
- Utilizes the department to conceive and implement lean continuous improvement projects to enable the operability of the WLES process
- Stays abreast of current continuous improvement trends and methodologies
- Supports other cross functional departments with expertise and manpower to the extent possible when process improvement is required
- May be responsible fordriving effective organization containment and corrective action processes tosupport product or quality system failures
- In some locations, may bea focal point for Production Engineering and development activities including PLC Expert and WLES Expert may have direct or dotted line relationship
- Ability to act as a change agent and influence, both internal and external functional areas
- Ability to integrate and apply solutions for quality performance and continual improvement, both breakthrough and systematic throughout the organization
- Ability to lead and develop a vision and strategy for process improvement through lean/six sigma initiatives and gain active alignment support for that strategy by all organizational stakeholders
- Demonstrated ability to attract, lead, coach, motivate, and develop others
- Solid understanding of organizational structure ensuring engagement and active support of functions and members within the business system as necessary to achieve business goals
- Solid understanding of statistical concepts and methods to ensure appropriate application and analysis of data
- Understanding, supporting and leading the implementation of LEAN Manufacturing techniques (waste elimination, parts flow and pull) and Six Sigma methodologies
- Formal problem solving skills such as Taguchi, DOE, 8D, etc
- Significant understanding of lean manufacturing principles
- Strong time management and project management skills
- Ability to travel to suppliers, other locations within Woodward, and customers as required to fulfill the needs of the organization (domestic and international)
- Practical and results oriented
- 5 years of professional experience in a manufacturing environment or a branch of the military
- Demonstrated success in implementing Lean/Six Sigma concepts
- Prior leadership experience in a manufacturing environment preferred
60
Continuous Improvement Manager Resume Examples & Samples
- Masters / Bachelor degree (degree related to technical, business or economics fields most applicable)
- Experience in continuous improvement methodologies such as Lean, Lean Six Sigma, TPM
- CI Expert (Black Belt) for the large sites (Bohus, Stockvik, Alby, Columbus (GA), Jundiai), CI Lead Practitioner (Brown Belt) for the small sites (the remainder), at the latest certified according to AkzoNobel corporate standards by 31 Dec 2017
61
Continuous Improvement Manager Resume Examples & Samples
- Facile in Change Management techniques
- Change agent with demonstrated influencing experience
- Self-directed individual who can work independently
- Demonstrated knowledge of Lean manufacturing, Six Sigma, Root Cause Analysis and problem solving, flow manufacturing, Statistical Process Control
- Computer proficiency in Microsoft Office
62
Lean & Continuous Improvement Manager Resume Examples & Samples
- Work closely with Project Lotus team members to deliver an effective and on-time site implementation for Oracle
- Ensure site implementation readiness
- Maintain the site implementation project plan and communicate site project status
- Ensure risks are identified and mitigation actions are completed, escalate issues
- Facilitate the logistics, e.g., meeting schedules, site contacts, meeting room availability, clerical support, system access, training schedules etc
- Develop metrics and periodically assess implementation effectiveness
- Bachelor’s Degree years of experience leading lean initiatives in a chemical
- At least seven (7) years lean manufacturing and continuous improvement experience within chemical manufacturing
- Six Sigma and Lean Leader training
- Oracle and site implementation experience
- Strong ability to influence, obtain credibility and lead cross-functional teams
- Excellent knowledge of manufacturing business concepts, lean principles and 5S tools
- Passion for improvement
- Strong communication and presentation skills across all levels of employees
63
Continuous Improvement Manager Resume Examples & Samples
- Good knowledge of UTC ACE Operating System or equivalent Continuous Improvement methodology (i.e. Toyota Production System)
- ACE Practitioner, or working towards equivalent proficiency in ACE/CI tools
- Good demonstrated knowledge of Lean manufacturing techniques and application. Successful execution of continuous improvement events in production and business processes
- Assessment/audit background preferred
- Strong communication & presentation skills, both verbal and written
- Effectively able to train and facilitate in a classroom setting
- Good analytical and problem solving skills with a focus on results (driving to root cause)
- Knowledge of Policy Deployment and/or related reporting techniques
- Leadership skills to implement strategic ACE Vision and supervisory skills to manage ACE team members
- Due to ITAR restrictions, must be a US Citizen or Green Card Holder
- Experience and awareness of different countries/cultures
64
Continuous Improvement Manager Resume Examples & Samples
- Investigating, analysing, and documenting business processes
- Performing gap analysis to identify missing or inadequate processes or procedures
- Recommending improvements to existing processes and identifying areas for waste elimination
- Assisting in establishing and documenting highly efficient processes and procedures
- Performing base line metric collection and key performance indicators (KPI) to enable measurement of cost savings and time savings
- Providing progress reports and/or briefings on a regular basis to managers, customers, and other stakeholders
- Facilitating continuous improvement ideation sessions with Global Business Service Center teams and internal stakeholders to ensure a robust idea pipeline is in place
- Analyse the needs and expectations of the customer’s experience in order to enhance quality and drive customer satisfaction
- Monitoring, measuring, and providing feedback on process performance
- Identifying, prioritizing, and executing initiatives aimed at improving global business service center processes
- Collecting and documenting business requirements for experience enhancement processes and technologies
- Conducting product solving and root cause analysis and leading teams to create effective countermeasures and action plans to ensure sustainable results
- Supporting implementation of improvements for process efficiency, quality, and control KPIs
- Bachelor’s Degree and significant related experience
- Demonstrated ability to recognize process improvement opportunities, apply project management & quality optimization tools to drive improvements, identify & address related employee training needs
- LEAN Six Sigma certification or training
- Relevant experience with: Process Mapping, Value Stream Mapping, Problem Solving Method 8D, FMEA
- Strong collaboration skills and the ability to partner with key internal/external customers in order to drive change and continuous improvement
- Strong business acumen and leadership and decision making skills
65
Continuous Improvement Manager Resume Examples & Samples
- Contribute to the development and execution of Continuous Improvement strategy, plans, initiatives, and goals in support of the BD vision, mission, values, strategies, and plan
- Drive and sustain Continuous Improvement (CI) activities and programs such as: Kaizen Action Sheets, 5S, Lean Daily Management System, Total Productive Maintenance, and 20 Keys
- Act as a change agent by providing coaching at all levels in Continuous Improvement philosophy, culture and alignment with BD’s vision, mission, values, strategies, and plan
- Track CI metrics and drive improvement
- Provide advice, counsel and/or instructions to individual employees, teams, facilitators, area management, and appropriate personnel relating to CI activities
- Monitor and assess CI related needs and performance. Provide feedback, resources, support, training and direction as required to facilitate changes, meet needs and enhance performance
- Stay up to date, benchmark and network as required to be familiar with and be able to communicate leading edge tools related to training and CI
- Regularly provide feedback to management on status and issues regarding the success of CI
- Provide structured team, facilitator training and certification in conjunction with Human Resource personnel
- Perform additional CI duties as required
- Comply with all local, state, federal and BD safety regulations, policies and procedures including RCRA Hazardous waste regulations
- Comply with all BD quality policies, procedures and practices through consistent application of sound quality assurance principles
- Bachelor's degree required, graduate degree preferred
- Previous supervisory experience strongly recommended
- Eight to ten years experience in developing, organizing, implementing, and managing projects and assignments
- Computer skills (Excel, Word, Power Point, Minitab, SPC Software, etc.)
- Six Sigma Black Belt, Lean (Kaizen) Leader Certification required
- We consider individual involvement and accountability to be both a right and a privilege
- We accept personal responsibility for everything we do
- We treat the company’s reputation as our own and try to make wise use of our time and the company’s resources
- We expect access to the tools and information necessary to participate in any decisions that will reflect on our collective or individual reputations
66
National Quality & Continuous Improvement Manager Resume Examples & Samples
- Drive the development and successful delivery of HR Servicing process improvements to increase customer satisfaction, improve financial productivity and enhance risk mitigation
- Partner with global and local stakeholders to improve / lean-out processes that result in improved HR effectiveness and efficiency
- Facilitate continuous improvement workshops following standard methodologies like Lean/Kaizen or Six Sigma
- Partners with local and global partners to deploy and enhance HR Service Delivery Model globally
- Analyze processes and service performance related to local and global Servicing areas while cooperating with global quality professionals within HR
- Run continuous improvement process (CAPA) and transfer trend analysis results into recommendations or initiate / coordinate needed actions in cooperation with local operational management teams or global Quality team
- Apply agreed Quality Management approach (i.e. Lean, Six Sigma, Value Stream, ANSI) and execution methodology to change initiatives that benefit from this type of structure
- Use of strong cross-cultural communications and leadership, influencing and consultative skills
- Ensure that agreed local or global processes are followed and use of standards /technologies
- Become member of global Quality Management team
67
Continuous Improvement Manager Resume Examples & Samples
- A current resume (indicating your related experience)
- A Letter of Interest (preferably no more than two pages) describing how you meet the qualifications and why you are an ideal candidate for this position
- Minimum of three (3) years of knowledge and experience applying Lean principles and techniques
- Ability to impact/influence others
- Possess the drive for improvement and the ability to create new ideas to operate more efficiently
- Bachelor's Degree from a recognized accredited college and/or university whose accreditations are recognized by the U.S. Department of Education (USDE) or the Council of Higher Education Accreditation (CHEA)
- Certified Green Belt in Lean Six Sigma
68
Continuous Improvement Manager Resume Examples & Samples
- Assist in the development and deployment of Policy Deployment (PD) throughout the Organization. Effectively communicate PD through the Organization and ensure the necessary PD processes are in place to implement the Initiatives and achieve the Improvement Targets
- Assist in the development and implementation of CI strategies supporting aggressive business goals
- Help the Business Leadership plan events in line with their Macro Plans & Policy Deployment
- Know, apply and assist the application and use of Lean Principles & Tools toward developing the Organization into the Least Waste Way ( LWW )
- Drive the Organization transition to one that is supportive of and operating at the Least Waste Way
- Ensure the Esterline Enterprise Excellence principles are developed into the culture through education, demonstration and expectation
- Nurture an environment that enables real time problem identification & resolution
- Identification and removing of barriers to implementation of CI
- Monitoring progress of CI within the organization
- Hands on education, training & application of CI principles and tools
- Planning and facilitating CI events
- Providing CI training and teaching (OJT)
- Assist with the necessary follow-up actions to close out “to-do” actions after Kaizen Events
- A ‘lean guru’ with hands-on and solid enterprise experience; 6+ years hands-on track record of implementing successful lean programs with Strategy Deployment, value-stream mapping, daily accountability, 5S, visual management, lean in the office, lean sourcing, etc
- 5+ Years’ experience working in the Danaher Business System (DBS), Toyota Production System (TPS), Honeywell Operating System (HOS) or other recognized Lean business system
- TPS or Danaher Business Systems experience strongly preferred
- Formal lean training and comprehensive knowledge of Lean and continuous improvement methodologies and tools
- Project management experience in leading complex, global projects with multiple stakeholders
- Bachelor’s degree in engineering, science, operations or business
- Ability to lead and execute project independently
- MS Office, Excel, Word, PowerPoint
- Able to travel 20-25% domestic and international
- Previous exp in Teaching, Training and Instructing
- Seasoned Executive and Change Agent
- Strong & Charismatic leadership
- Excellent communication skills, interpersonal, coaching and counseling
- Detail oriented with the ability to see bigger picture and envision step-change scenarios
- High ethical standards to support a professional business code of conduct
- Superior leadership skills with proven ability to effectively facilitate effective cross-cultural business interaction
- Passion for driving business improvement and leading change in a large global environment
- Credible
- To the Lean Principles
- With Leadership
- Across the organization, demonstrating mutual trust and respect
- Change Agent
- Help create and maintain an environment that encourages and supports change while maintaining compliance and protects the business
- Bias for Action
- Execute a change strategy in line with Policy Deployment
- Emphasize creativity before capital
- Comfortable with risk taking
- An ability to do/lead guided discovery
- Ability to take initiative as problems or opportunities arise
- Have a broad skills base
- A range of successful assignments & experiences
- A good business acumen
- Employee understanding
- Recognize the value of and develop the people resource, using the support of the “HR” organization
- Strong Communications
- Effectively communicates the Esterline Strategy & Policy Deployment
- Capable of influencing and getting cooperation and action from others without having direct control
- Ability to effectively communicate, work and relate with people at all levels of the organization
- Good team player, good coaching skills and can develop other co-workers
69
Continuous Improvement Manager New Services Resume Examples & Samples
- MS in business or technical field and at least 2 years in an operational consulting or radiology administration or operations role. Other applicable prior roles may include clinical education, clinical or business analyst, modality manager, quality improvement manager, process improvement manager, or the equivalent at a healthcare provider
- Customer & Quality
- Can gain expert knowledge of product functionality at a level sufficient to train others in basic use, advanced functionality, and best practices
- Technology - familiar with the role (what data they provide), advantages, and limitations (where the data is reliable or not reliable, possible blind spots in the data) of imaging and healthcare IT systems
- Operations: recognizes key performance indicators and their relevance to a radiology department, understand how these can be measured (link to systems) and limitations in those measurements, and the (people, process, system) factors that impact those KPIs
- Organizations: fluency with typical roles and interactions within a radiology department and hospital; understand roles as linked to KPIs
- Can gain broad knowledge about Philips products and services at a level sufficient to identify what Philips offerings may address customer needs and to make the connection between customer and Philips
- Operational Experience and strong Operational Improvement Drive
- Can execute structured root cause analysis, critical thinking, and problem solving methodologies (supported by tools and procedures) and explain the process and results to stakeholders
- Ability to interpret data and trends, use of Business Intelligence type tooling, including working knowledge of statistics (understanding of terminology and significance), data visualization techniques (what visualization approach to use)
- Willingness to travel up to 25 %
70
Senior Continuous Improvement Manager New Services Resume Examples & Samples
- MS in business or technical field and at least 5 years in an operational consulting or radiology administration or operations role. Other applicable prior roles may include clinical education, clinical or business analyst, modality manager, quality improvement manager, process improvement manager, or the equivalent at a healthcare provider
- MBA and/or industry experience (in addition to in-provider experience) is preferred but not required
- Experience in direct or project/functional management of teams is preferred
- Service oriented mindset (customer focused and experienced in customer interaction) is a must
- Can execute structured root cause analysis, critical thinking, and problem solving methodologies. Can support the creation of tools and procedures to standardize these activities, and can coach others in the deployment of these processes
- Project management: able to track and manage multiple clients simultaneously, and prioritize activities based on clinical and commercial variables
- Excellent interpersonal skills and experience in stakeholder management, with sensitivity to complex organizational structures, varying cultures, and potentially conflicting goals. Comfort working with both internal and external customers
71
Continuous Improvement Manager Resume Examples & Samples
- Provides business process improvement expertise, along with organizational, financial, business, strategic and project knowledge, to assess improvement opportunities and define and deliver sustainable process solutions for several work streams
- May lead a team or multiple teams of internal and/or external resources on a project basis; leads assessment of potential new projects; analyzes opportunities at a high-level and defines approach
- Works with Business Line / Function leaders to shape/manage project scope; coordinates analysis of current state process and issues/gaps; defines future state process and roadmap; develops business cases, financial realization measures/metrics, and controls; formulates final recommendations and executive presentations; trains, coaches, and mentors team members; drives implementation and ensures sustainable outcomes
- Accepts overall responsibility for actions of the teams and manages priorities and assigns work appropriately on multiple concurrent process projects of varying size up to and including enterprise transformation initiatives
- Acts as a change agent by emphasizing and encouraging continuous improvement; ensures that best practices and lessons learned are shared widely and applied across the organization
- Relevant business process improvement, facilitation, and project management skills
- 10+ years of progressive related experience with proficiency and understanding in one or more functions, including 5 years of experience in process-related roles; 3 years in a banking environment, and a year with financial measurements and metrics
- Ability work through others to resolve issues and manage stringent timelines for project deliverables
- Compelling executive presence and effective communicator
- Several years of leadership experience at a top-tier management consultancy
- Training/certification in Lean Management System, Lean Six Sigma, process improvement, facilitation, and project management methodologies/tools
- Demonstrated ability to increase team communication, actively facilitate the implementation and acceptance of new processes/procedures, solicit feedback from the team, and gain the buy-in and support from the team’s formal and informal leaders
72
Continuous Improvement Manager Resume Examples & Samples
- Provide strategic ACE/Continuous Improvement (CI) direction for systems, projects and programs for the Landing Systems Troy Campus
- Become a resident LS expert and consultant in ACE/Enterprise Excellence operating system, Standard Work, Lean transformation and Standard Factory
- Provide support and guidance on ACE/CI Assessment process, Kaizen events and Six Sigma Projects
- Develop and mentor ACE/CI leaders, ACE/CI pilots and Tool Champions by providing guidance through ACE/CI certifications (Associate, Practitioner and Master)
- Plan, lead and facilitate Kaizen teams: complete event planning, perform pre-work and facilitate team supporting event closure. Follow-up on kaizen events and assessment plan to Macro and ACE/CI plans to prevent backsliding
- Member of Troy Operations leadership team
- Become an ACE/CI advocate in leading and implementing organizational changes throughout the Troy organization
- Complete ACE/CI initiatives that lead to improved business results (Flow and linkage changes, Kaikaku implementation, implementation of Pull system and Lean transformation)
- Plan, Lead and facilitate CI projects teams (in manufacturing, as well as, non-manufacturing/business processes)
- Utilize Macro planning and Value Stream mapping to develop future state CI plans
- Assess ACE/CI initiatives and provide input and recommendation on future activities regarding employees and leadership development
- Five (5) years varied experience, including successful implementation of CI, leading of projects, developing and mentoring leadership, leading others, training or participating in continuous improvement activities; operations, active participation in team or improvement activities
- Strong servant leadership style
- Excellent communication skills, particularly verbal skills in group settings where there may be resistance to change
- Exhibit appropriate change agent skills
- Strong interpersonal skills and ability to lead, facilitate and motivate teams; a bias for action and sense of urgency to obtain results; active listener
- Must be able to verify U.S. Person Status as defined by International Traffic in Arms Regulations (ITAR)
73
Continuous Improvement Manager Resume Examples & Samples
- Required Black Belt, and has received certification as a Lean Implementer
- Has shown initiative, the desire to drive change and is motivated to exceed expectations
- Possesses advanced computer skills (experience with spreadsheet applications would be very helpful)
74
Continuous Improvement Manager Resume Examples & Samples
- Direct plant product Continuous Improvement activities
- Responsible for overall quality operating system
- Oversee employees engaged in testing/quality lab activities
- Monitor performance of quality control systems to ensure effectiveness and efficiency
- Manage and track warranty
- Analyze quality control test results and provide feedback and interpretation to production management and staff
- Communicate quality control information to all relevant organizational departments
- Create and implement inspection and testing criteria or procedures
- Document testing procedures, methodologies or criteria
- Identify critical points in the manufacturing process and specify sampling procedures to be used at these points
- Devise processes/procedures to increase efficiency
- Previous 7 - 10 years CI experience in a manufacturing environment
- Bachelor of Science Engineering or degree related to field
- TS and ISO Audit/Certification experience
- Dependability - requires being reliable, responsible and dependable and fulfilling obligations
- Stress tolerance - requires accepting criticism and dealing calmly and effectively with high stress situations
- Ability to follow instructions carefully, requiring basic reading skills and ability to follow diagrams & pictures
- Ability to respond to changes in demand by shifting labor from one product line to another
- Ability to perform very stage of the assembly process
75
Continuous Improvement Manager Resume Examples & Samples
- Lead plant based CI team providing daily direction, mentoring, coaching and development to ensure the continued success and development of the CI team
- Manage financial roadmap, strategy development and execution to achieve short, mid and long-term business goals
- Work closely with the controlling and plant management teams, utilising the BBP system, to identify improvements to support profit planning process and reach set benchmark performance
- Ensure lead-time, from receipt of customer order to sold product, is clearly understand across the business and areas of improvement are highlighted with actions plans in place to improve lead-time performance
- Ensure Standard Work is in place for all processes within the operation
- Ensure Visual Management is deployed throughout the operation to monitor scrap performance and effectiveness of daily activity versus customer demand and efficiency goals
- Work closely with Operations team to ensure production goals are monitored and adjusted based on efficiency improvements
- Lead weekly meetings with plant leadership team to present how the CI team is driving profitability improvement
- Lead monthly meetings with senior management to present progress to meet short, mid and long-term business improvement goals
- Manage reporting of CI team progress to set deliverables
- Work closely with the Advanced Manufacturing Engineering team to ensure optimum layouts are developing and installed for new and existing product lines to meet sold efficiency and cost goals
- Ensure YFIMS auditing and improvement is high priority and sufficient action plans are in place to improve plant rating
- Must demonstrate knowledge and experience in driving change within a challenging business environment
- Information and material flow mapping experience critical to success
- Experienced practitioner of the lean tools
- Capacity planning
- Basic understanding of the profit and loss statement
- 5 years industry experience
- Degree in Operations, Engineering or Economics
76
Continuous Improvement Manager Resume Examples & Samples
- Bachelors degree in Engineering, Manufacturing Engineering, Business Administration or a related discipline required. MBA or advanced degree is highly desirable
- Five years of minimum experience in the direct implementation of Lean Manufacturing Techniques
- Demonstrated understanding and implementation of Lean Manufacturing Techniques and Six Sigma principles
- Proven ability to work in a self-directed environment
- Excellent oral, written and presentation skills, leadership and project management
77
Continuous Improvement Manager Resume Examples & Samples
- Reporting to the Operations Manager, the role will support and strengthen the Operations team (c.105 people). You will work collaboratively with your peers, the three Production Managers across this diverse Chemicals manufacturing site. Championing the implementation of Lean Manufacturing, you will drive a site step-change through process and plant standardisation in the overall pursuit of Operational Excellence. Responsible for a direct team of professional Chemists and Engineers, you will manage varied work-streams and capital projects to embed this change
- This is a practical, hands-on role (rather than theoretical) and requires an impactful, results and project-orientated continuous improvement leader. You will offer a positive, consultative approach, with the proven ability to influence, facilitate and develop others to enable you to embed the required processes, skills and behaviours in the organisation. You will be able to challenge the status quo
- You will likely be educated to BSc or MSc level as a Chemical or Process Engineer with essentially previous line management experience gained in an Operational/Production role within a manufacturing environment
- Proven knowledge of CI tools and techniques is essential including Lean, Six Sigma, 5S, TPM, with experience of other good manufacturing practices such as Root Cause Analysis and Statistical Process Control (SPC) being highly beneficial to implement the increased level of control and process automation needed on site
- 16 December 2016
78
Continuous Improvement Manager, Doncaster Resume Examples & Samples
- Leading, managing and co-ordinating the continuous improvement programme at the site
- Leading change throughout the business via identification and management of projects
- Engaging with people at all levels to yield the benefits of continuous improvements
- Developing continuous improvement strategy across all functions
- Conducting Lean System assessments, planning and managing improvements
- Providing Lean support across the organisation, eliminating waste and increasing customer satisfaction, cost reduction and improving financial performance
- Leading the continuous improvements team
- Managing simultaneous multiple projects
- A degree or equivalent in any engineering discipline or business studies
- Certified Lean and Six Sigma practitioner (Black Belt desirable), trainer and mentor
- Proficient communication and influencing skills
- Highly driven and results oriented
79
Continuous Improvement Manager Resume Examples & Samples
- Driving improvement initiatives that positively impact Client satisfaction & business profitability
- Identifying areas of improvement and facilitating improvement projects which can result in significant improvement in profitability
- Solving business problems through innovative & sustainable solutions thru Six Sigma DMAIC strategy and applicable Continuous Improvement and/or Delivery Excellence strategy and best practices
- Identifying process gaps & automation opportunities
- Project managing improvement efforts across multiple locations and maintain consistency in effort & implementation
- Interfacing with leadership/clients and identifying opportunities for value
- Driving effective Change Management for a stable & consistent delivery – Zero surprise operations
- Train, mentor and certify Six Sigma Yellow belt and Greenbelt candidates
- Good Leadership and communication skills top, bottom and across working effectively with colleagues and leaders across the organization
- Self-motivated and with a good sense of self-discipline
- Graduate of any 4 or 5 year course
- Six Sigma Black belt certified
- 6 years and above work experience in operations preferably in BPO/ Service Industry
- 1 to 2 years work experience as a Continuous Improvement or Process/ Delivery or Operational Excellence or similar function
80
Continuous Improvement Manager Resume Examples & Samples
- The Continuous Improvement Manager/ Master Black belt will manage a small team that will be focused on benchmarking and replication of best practices as well as data analytics, looking for improvement opportunities across the organization. Incumbent will be responsible for recommending, implementing and enhancing a standard framework across the organization to systematically identify, define, prioritize and follow up activities towards accomplishing the company strategic plan. This frame work includes an effective governance approach and operating model for on-going continuous improvement function towards enabling SCE reaching best in class performance
- The CI Manager/MBB support development of the 5 year strategic planning towards improving key corporate metrics (affordability, reliability, customer satisfaction and safety) by continuously monitoring link between plans and the identification of new opportunities
- Assures that strategies from high-level management are carried out through driving development and further improvement of a diverse set of operating mechanisms, including development of CI training materials at different levels of complexity. Tracks program deliverables and achievement of key milestones, highlighting risks and ensuring program metrics, savings tracker and other reports are timely and accurate. Lean Six Sigma and Project Management subject matter expert, able to train people across the organization at any CI level
- Individual will be in regular contact with executive management across the OU’s providing information and getting buy-in in setting strategic direction on corporate goals i.e. affordability, reliability, customer satisfaction and safety. With day to day interaction at a managers and supervisor level
- On occasion, this position will lead projects/ activities of significant impact for the organization that are complex in nature and require a significant amount of effort
- Bachelor’s or Master's Degree in Business Administration, Engineering or a related discipline
- Five years implementing CI practices through applying Lean and Six Sigma methods within the service industry or environment (i.e. utilities, financial, call centers, others)
- Five years of experience within the Service industry in a functional role within the organization
- Experience leading Kaizen events as well as DMAIC projects within the service industry
- Five or more years of experience managing/supervising/leading a group, unit, or teams
- At least 2 years performing data analytics with tangible results on process improvements
- Possess understanding of both theory and practical application of continuous improvement principles and tools
- Demonstrated history of implementing sustained improvements in operations, support departments and with suppliers using Lean (Toyota Production System) and similar continuous improvement programs on a large scale
- Formal training on Project Management (e.g. PMBOK or similar)
- Strong interpersonal, change management and conflict resolution skills
- Lean Six Sigma (or similar) certification at a Master Black Belt level from a recognized company or institution
- Experience leading at least 20+ Kaizen events as well as 5+ DMAIC projects within the service industry
- Leadership implementing/deploying CI programs
- Use of complex data to identify opportunities and offer solutions; Exposure to Advanced Data Analytics
- 3 years of experience and project manager using a formal methodology such as PMBOK
- Strong oral and written communication skills with the ability to clearly communicate data, context, and implications to business stakeholders
- Utilities industry experience
- Project Management PMP certification
- Formal Data analytics training/certification
81
Continuous Improvement Manager Resume Examples & Samples
- Assists with the deployment of Continuous Improvement strategies site wide
- Own and manage area Continuous Improvement Processes and Projects
- Define and deploys area CI tools and techniques
- Train and coach plant leadership and personnel on the use of continual improvement concepts
- Collaborate and build strong interpersonal relationships with the area leadership and team members
- Leads cross functional teams to drive projects from conception to realization
- Lead advancements in Safety, Quality, Cost, Productivity, Delivery and Employee Engagement
- Consult, coach, develop and train leadership and team members to excel in Continual Improvement concepts
- Help to establish, improve and manage Key Performance Indicators (KPI’s) with area leadership and team members
- Demonstrates flexibility in managing special projects as directed by leadership
82
Continuous Improvement Manager Resume Examples & Samples
- 3-5 years leading high impact teams
- 3-5 years managing portfolio of projects
- 5 years operations experience
- 5 years technical background in lean manufacturing
- Master’s degree a plus
- Extensive experience in operations
- Demonstrated proficiency with advanced ACE tools
- Demonstrated proficiency with MS Office products
83
Quality & Continuous Improvement Manager Resume Examples & Samples
- Develop closed-loop quality system driven to reduce process variation and ensure plant compliance
- Act as change agent to drive continuous improvement of production and service processes to improve quality and increase efficiency, which includes root cause analysis and problem solving
- 3-5 years’ experience in quality, or equivalent.EDUCATION / KNOWLEDGE
- Bachelor’s degree in Business, or related field preferred or
- 3-5 years’ experience in quality, or equivalent experience
- Prior management or supervisory experience preferred
- Proficient with Microsoft Office, Outlook, and internet research skills
- Experience in implementation of technical testing in production environments
- General knowledge of printing and converting technologies preferred
- Experience with Minitab software and SAP is a plus
- Visual Color Detection, the ability to match or detect differences between colors, including shades of colors
84
Continuous Improvement Manager Resume Examples & Samples
- Managing CI Projects as assigned, typically within a local region or business unit
- Performing gap analysis to identify deficiencies in business processes and programs, and recommending adjustments to programs and/or processes
- Linking process deficiencies directly to bottom line impact
- Leads cross-functional project teams formed to implement change and drive continuous improvement
- Drives mixed model value stream implementation projects with a focus on continuous improvement of safety, quality, cost, and delivery
- Use appropriate problem solving tools to provide rapid improvement with sustainable results
- Ensures adherence to standard processes for data collection, documentation and reporting
- Plans budget and manages costs related to operational excellence initiatives
- Directly supervises, trains and mentors full-time CI assigned resources
- Building project plan to CI projects, including resources, timeline, critical paths, etc
- Managing diverse CI strategies for transactional and/or manufacturing operations
- Participating in operational continuous improvement reviews with Local and/or Regional Management
- Minimum 10 years experience in operations required
- Experience in a Continuous Improvement function
- Black Belt or Master Black Belt certification required
- Must have thorough understanding of cycle time reduction, waste reduction, yield improvement, productivity and throughput improvement
- Proficient with Microsoft Applications: Word, Excel, Outlook, and PowerPoint
- Be a self-starter with excellent organizational skills in planning and organizing to handle multiple tasks concurrently
- Advanced problem solving capabilities, attention to detail and numerical aptitude
85
Continuous Improvement Manager Resume Examples & Samples
- Utilize Lean Manufacturing tools and methodology to reduce waste, streamline processes, and improve quality process controls
- Utilize organizational and financial metrics to drive project selection and priority
- Maintain and continually improve manufacturing processes in terms of quality, safety, cost, delivery and communication
- Employ a working knowledge of standard-work to ensure every work activity is properly defined, displayed (point-of-use) & accurately followed
- Create and maintain process documentation as applicable
- Champion facility layouts and drive necessary modifications to drive efficiency and productivity improvements
- Develop CAD layouts for new or modified processes
- Provides hands-on technical support / trouble shooting to solve problems to root cause
- Lead multi-functional work teams to complete projects and desired process changes
- Lead, coach and mentor LSS Green Belt projects by using lean tools
- Act as a change agent by facilitating Kaizen events
- BS in Industrial Engineering or equivalent
- A minimum of five (5) years of relevant experience in an operations or manufacturing enviornment
- Six Sigma Black Belt Certification is strongly preferred (ASQ or equivalent)
- Three to five years of demonstrated project management excellence (includes experience in leading cross-functional teams) and ability to work in a matrix organization
- Must possess a good knowledge of process flow and development as related to manufacturing systems
- High proficiency in key methodologies and associated Lean, Six Sigma and Project Management tools
- Ability to manage highly visible, complex projects to a successful end
- Ability to devise new approaches to problems encountered
- Solid computer skills with CAD, MS Office and other analysis tools and software programs
- Outstanding analytical and statistical technical skills
- Leadership skills to champion, motivate and influence change in a continuous improvement environment are essential
- Ability to work under tight deadlines and handle multiple/detail oriented tasks
- Able to drive action in a timely manner
86
Continuous Improvement Manager Resume Examples & Samples
- Acts as a safety leader and puts safety first in all responsibilities. Works in conjunction with the EHS Manager to establish and maintain all policies and programs to assure a safe working environment
- Facilitate deployment and integrate the philosophy of WCOM into the culture of the Plant
- Identify the highest value cost savings projects and coordinate the various project teams assigned to ensure proper resourcing to drive completion of projects
- As a member of the plant leadership team, also involved in daily production and operations issues to insure that we produce a quality product, deliver against our committed customer service goals, and optimize efficiency/productivity
- Be recognized as a leader and problem solver at the site by providing leadership and expertise that will solve problems and improve performance
- Motivate, coach and instill good management skills in engineers, shift supervisors, and hourly employees. Establish a strong presence on the floor to set and communicate expectations, standards, and evaluate results so all employees understand expectations
- Initiate and lead employee training to further instill the continuous improvement skill set in the organization. Develop new processes and programs as need and where gaps exist
- Led major projects as necessary to improve plant results
- Be able to extract useful data from a variety of systems to facilitate identification of improvement opportunities
- Coordinates the work necessary to improve our overall Continuous Improvement results as measured by regularly scheduled audits
- Assist in generating reporting tools and progress reporting for assigned business areas
- Facilitate a process of best practice sharing internally within the plant as well as externally with peers and other facilities
- Lead project selection process and drive policy deployment so that all employees have a clear understanding of goals and objectives for a successful year
- Bachelors Degree is required. Prefer a major in a technical background such as engineering or industrial technology
- 5 years of operations management experience is preferred
- Intermediate to advanced computer skills including Word, Excel, PowerPoint and Outlook, SAP
- Ability to drive change and overcome obstacles
- Demonstrate and foster Bemis Core Values and actively contributes to a high performance culture
- Demonstrated ability to absorb new technologies and management techniques
- Utilize an approachable and participative style in motivating people to achieve higher standards and performance levels
- Experience implementing lean principles or other continuous improvement methodologies preferred
87
Continuous Improvement Manager Resume Examples & Samples
- Support the process that identifies and implements significant Continuous Improvement opportunities to support division and corporate objectives
- Support the preparation and dissemination of quality management reports for use by Maintenance Operations and assist management in their interpretation and application to improve performance
- Act as a liaison between Maintenance Standards & Engineering team, Operations and Quality Assurance (Audit) organizations for purposes of evaluating and conducting labor productivity and technology improvement projects
- Support continuous improvement programs, establishing and maintaining high quality assurance standards, procedures and controls Support continuous improvement deployment using fundamentals of Lean and Six Sigma
- Support lean office and implements lean principles Plan, lead and facilitate Kaizen and Six Sigma teams
- Complete event planning, perform pre-work, facilitate teams and support event closure and follow up
- Develop standards of performance based on process innovation and best-in-class practices Supports the preparation, development and publishing of Continuous Improvement materials to include detailed process documentation, process maps, and training (webinar) materials
- Provide guidance and technical knowledge on process and continuous improvement projects
- Educate, coach, mentor and qualify Lean / Six Sigma specialists
- Track continuous improvement status, cost savings, training, certification and events by project or account Review and report on performance against operational objectives and project success factors
- Support the development and implementation of the operational goal setting process
- Ensure the integrity of performance systems and reports
88
Continuous Improvement Manager Resume Examples & Samples
- Translates strategies into tactics representing multiple disciplines within a department area or covering more than one department
- Typically 2nd level people manager
- Provides management and leadership to managers, supervisors and/or exempt staff
- Integrates functions in a multi-discipline work environment
- Develops departmental plans, including business, production and/or organizational priorities
- Decisions are guided by resource availability and functional objectives
- Manages subordinate managers
- Holds subordinates accountable for budgets, schedules, performance standards
- Determines organizational structures with top management approval
- May be responsible for the activities at a manufacturing facility or multiple operating facilities
- Establishes and integrates organization operational objectives, assignments
- Designs, manages and executes policies to deliver business strategy
- Errors in decisions, recommendations result in failure to achieve major organization goals
- Minimum of 5 years experience as a first level operating manager
- Minimum of 2 years LEAN experience
89
Continuous Improvement Manager Resume Examples & Samples
- Will be an operations/supply chain/business Site Lean Leader with strong analytical skills and exceptional communication skills
- Ideally, the candidate will have significant industry experience in a leadership role with broad expertise
- A key requirement will be for the candidate to know “what great looks like” (as opposed to merely ‘good’) in various areas of operations
- The successful candidate will have a track record of leading and personally implementing significant change by engaging all stakeholders in a team-oriented process
- Experience with large and small companies will be a plus
- Ability to create “leverage success”: the successful candidate will apply his/her learning wherever most applicable across the site using “leveraged success” to increase value
- Able to conduct: Kaizen events, 5-S training/audits, standard work events, visual control training, leaders standard work training
- Ability to effectively implement visual management techniques
- Bachelors with a minimum of 2 years of relevant experience or equivalent combination of education and successful prior experience in a CI Manager role
- Minimum 3 years of Lean Management experience with additional experience in project management a plus
- Minimum 2 years of experience leading continuous improvement activities, utilizing recognized lean manufacturing techniques
- Bachelor’s Degree in Engineering preferred or commensurate experience
- Proficient experience with Kaizen and Lean events
- Previous experience in project coordination/management in a manufacturing environment
- Experience with a production/operating system similar to the Toyota Production System
- Understanding of Lean Principles such as 5S, pull, flow, takt, JIT, Kanban
- Experience utilizing value stream mapping to document and clarify the “current state” of processes. Design associated “future state” maps with wastes eliminated and lead times reduced as guides to maximize efficiencies
- Experience with Mistake-proofing or Poke-yoke
- Knowledge of TPM (Total Productive Maintenance)
- SMED or Equivalent Quick Changeover
- MDI (manage for daily improvement)
- Experience in prior Lean transformations
- Formal problem solving techniques such as 8D or 5-Why
- Microsoft Outlook, Word, Excel, PowerPoint, Access, Visio
90
Continuous Improvement Manager Resume Examples & Samples
- Identify, manage, and execute Lean Six Sigma Projects using the DMAIC methodology
- Drive multiple continuous improvement programs to enhance business KPIs and overall customer experience
- Collect and analyze data and identify solutions based on root cause analysis and create business cases to present to key stakeholders and solutions
- Interface and collaborate with other areas of operations, including merchant services, editorial, scheduling, and others. Filter and identify critical process changes and updates between departments
- Serve as a primary thought leader on CI strategy
- Support the head of customer experience in preparing for leadership meetings, team huddles, and problem solving on major projects and issues
- Create process maps and help standardize process and workflow
- Create reports and use data to drive decisions throughout CS
91
Continuous Improvement Manager Resume Examples & Samples
- 8+ years of experience in manufacturing area is required
- Black belt Six Sigma or ACE/Lean Practitioner desired
- Experience with SAP or other ERP system is desired
- Knowledge of Planning and supply chain management a plus
- Strong demonstrated leadership and team management experience
- Strong demonstrated aerospace / aerospace aftermarket knowledge
- Strong demonstrated communication and presentation skills
- Strong demonstrated MS Excel skills with the ability to perform complex analyses and data mining
- Applied statistics capability desired
- Demonstration of job specific competencies including Business Acumen, Negotiating Skills, Operations Experience, Drive for Results, Interpersonal Savvy & Strategic Agility
92
Continuous Improvement Manager Resume Examples & Samples
- Drive the development and implementation of Continuous Improvement projects consistent with and in support of the strategic plan and business operating plan
- Documents and works with Site Controller to validate achieved site LSS Savings
- Assist in designing new procedures and methods for operational processes
- By utilizing projects charters with deliverables, will work with site leaders to identify, modify, and sustain desired changes including reducing waste and improving inefficiencies
- "Identify opportunities for continuous improvement via idea generation and prioritize improvement opportunities with the management team
- Lead projects and initiatives from idea generation to strategic execution. Provide strategic insight and evaluation of the organizations progression
- Participate in developing and influencing strategy, planning, and execution depending on project or initiative needs
- Lead goal setting, assignment of projects, review of progress, approval, and feedback for direct report(s)
- KPI goal setting with the site via semi-annual Business Assessment, reporting and leading site reporting for KPI’s. Monthly updates on LSS resource, engagement, activities, etc
- Mentor employees to realize benefits from all continuous improvement initiatives and act as a change agent to the site/organization
- Act as a mentor for the Continuous Improvement leadership, supervisory staff and front line personnel
- Own the Lean Maturity assessments and improvement initiatives for the site. Partner with Site Leaders on strategy and deployment objectives
- Be a change agent: challenge organizational leaders to drive continuous improvements; remove organizational barriers to continuous improvement processes
- Develop, implement and monitor site Lean training initiatives. Aid in the development of the AWS C.I. Strategy
- BS/BA Degree or Equivalent
- 8+ years of successful leadership in executing continuous improvement/Lean/six sigma efforts and enabling efficiency, effectiveness and tangible financial benefit
- Lean or Six Sigma certification or practical experience leading C.I. Efforts
- Experience guiding team progress for continuous improvement projects/programs
- Experience designing, implementing and leading continuous improvement projects/programs
- Ability to coach / mentor / inspire direct reports
- Demonstrated experience with ensuring effective Change Management development and execution; Comfortable with ambiguity
- The ideal candidate will have the ability and willingness to transition into an operations/technical/reliability leadership position within 36 months
93
Lean & Continuous Improvement Manager Resume Examples & Samples
- As site APLS leader, site CI committee leader, site management team member and BU APLS network member, lead site APLS system setupand implementation to ensure compliance with corporate standard
- Develop site Value Stream Map (VSM) and transformation plan, drive year by year improvement
- Lead or Coordinate the progress of ALPS primary process implementation and site improvement projects
- Responsible to report key monthly KPI performance in EMP system
- Responsible for operational data and performance verification
- Drive site OEE improvement by using systematic approach, like SMED, SOS, process constrain study, etc
- Lead site level ALPS plan, procedure development, system setup and implementation
- Share practice within ALPS and CI network
- Conduct ALPS internal or peer audit as required
- Key role to develop site staff’s capability in terms of Lean and CI
- As member of regional key manufacturing process network, play key role in site major manufacturing process trouble shooting and gradual rate improvement
- About 2 years experience of production supervision, process engineering or engineering design
- Good command of both oral and written English
- Competent in MS office, Min-tab
- Good communication and interpersonal skill
94
Continuous Improvement Manager HUB Pakistan Resume Examples & Samples
- Support in Build up an effective CI culture in the plant. Delivers clear understanding of continuous improvement process requirements (behaviours and culture) & necessary to deliver productivity and improve safety, quality, and service
- Work with Plant Manager to define and scope improvement opportunities. Drives behavioural change across the plant, through influencing employees through empowered CI teams in implementing C I and productivity projects
- Support in achieving the plant conversion productivity target (6% Conversion Productivity) and identifying productivity opportunities to close potential gaps. Supporting start ups of NPDs, Capex projects and learning curves during projects
- Initiates and supports training programs by using existing tools from the continuous improvement toolbox (Six sigma, QCDSSM, 5S +1, FMEA, SMED - Changeover, etc) to ensure all employees understand the concept of continuous improvement
- Encourage, summarize and prioritise ideas and prepare effective implementation plan and tracking the benefits and recognize idea owners on the basis of CI reward policy
- Track Key Performance Indicators which clearly measure plant performance as a basis for improvements. Build up effective system for measuring& control of KPIs in the plant. Build up communication tools for KPIs (Waterfall System) tracking understandable for whole plant levels.(Periodically effective communication to the manufacturing team )
- Excellent support to manufacturing KPIs (QCDSM) to achieve best results. Coordinate with TPM owners to get clear understanding about the Efficiency loss drivers and plan corrective/preventive action to improve the scenario
- Support excellent Customer service level via performing deep capacity analysis & back up solutions preparation. Support delivery of other functional goals (safety, quality) - performing safety scans & behavior observation
- Perform work in compliance with the requirements of IMS (Integrated Management System) and valid work procedures and instructions. Follows rules for work safety, security, environment and food safety according to legal, KFB and KFI requirements
- Coordinate and supervise internal trainings (production/M&R) though training matrix with support of Team Leaders and HR personnel
- 6+ years manufacturing experience
95
Continuous Improvement Manager Resume Examples & Samples
- Develop strategic plan for the plant to drive a learning culture and implement lean tools and processes, including gap analysis to current state
- Lead Continuous Improvement Internal Audits. Develop implementation plans with Business Team and Operational Leaders post audit (Tactical Plans)
- Conduct lean tool and process training as necessary. Plan and deploy training to support the plant’s goals and objectives in lean manufacturing and to develop the depth of lean skills for the tool champions
- Lead the Plant Continuous Improvement Council that consists of plant leaders. Council monitors progress to the strategic plan and redirects activities and resources as needed to improve safety and quality, drive cost out of the business, and improve the lean culture and tool usage
- Lead Kaizen events (Rapid Improvement Events) and train Kaizen team leaders to facilitate events. Coordinate and drive a structured closure process on follow-up activities
- Interact with customer service managers and sales managers to facilitate cost out improvement opportunities or VA/VE events with our customers
- Responsible for the implementation and deployment of actions to ensure compliance with ISO 14001,OHSAS 18001, OSHA regulations, and all Federal, State, and Local laws as they apply to their areas of responsibility
- Support the sharing of best practices as result of internal and external benchmarking activities
- Manage the Six Sigma program for the plant and mentors six sigma project champions
- Minimum 3 years of experience supporting Lean and/or Continuous Improvement initiatives in a manufacturing environment
- Management experience
- Experience leading Continuous Improvement initiatives
- Requires strong manufacturing process understanding, organizational, planning, and communication skills
- Possess a clear understanding of Six Sigma Methodology
- Actively increasing knowledge in Lean Manufacturing principles and deployment of them in both manufacturing and office settings
- Knowledge of computers and related software for word processing, spread sheets, databases and project management
- Knowledge of behavioral science, including the ability to build a team, motivate, counsel, and constructively deal with people at all levels
- Working knowledge of: ISO 14001, SPC, Root Cause Analyze, PFMEA; Capability Studies, etc
- Problem-Solving concepts/tools and understands the importance of the change control process
96
Continuous Improvement Manager Resume Examples & Samples
- Improves processes, eliminates wastes, and optimizes workflow in the plant
- Facilitate CI events and teams. Creates and audits processes and standard to ensure sustained improvements
- A minimum of 3-5 years of manufacturing experience in a Continuous Improvement/Lean or Quality capacity
- Bachelor’s degree required; Engineering preferred
- Knowledge of Lean manufacturing principles; Kaizen principles and/or ISO certification
- Prior cross functional team facilitation experience, proven to manage change, develop personnel, and strategically plan for continuous improvement
97
Continuous Improvement Manager Resume Examples & Samples
- Deploy DMOS (Division Management Operating Structure) with all functional groups within a Division
- Complete Discovery process (business and operational analysis to identify opportunities) with all functional departments (Operations, Logistics, Sales and SG&A) within a Division
- Conduct Discovery in their own Division and support Discoveries in other Divisions if/as needed
- Drive additional savings beyond Discovery process by teaching and coaching, and ensuring there is a process of reviewing employee improvement ideas. This also involves assisting in driving project implementation through PIT's (Performance Improvement Teams), Division Steering Teams, and "Just Do It" initiatives
- Facilitate teams in maintaining an opportunity pipeline
- Support the Glide Path process (a total value stream review) with time bound actions, owners and due dates that ensure sustained performance improvement
- Tangibly demonstrate their value in culture change, balanced performance improvement, cost improvement and sustainable efforts
- Complete regular MOS / DMOS (Management Operating Structure) audits and serve as the site expert on the MOS / DMOS
- Give and receive timely, honest, data driven feedback with all members of the Regional / Division and Subdivision teams to influence tangible savings and drive culture change
- Support multiple facilities and spend time supporting DMOS in Division locations. Time spent in these locations will be determined jointly with regional CI support
- Bachelor's degree required (Dean Foods internal knowledge may be considered in lieu of this requirement)
- 5 - 8 years of demonstrated experience leading and facilitating continuous improvement initiatives in a manufacturing or logistics environment; CPG industry preferred
- Proven proficiency in Lean problem solving, root cause and waste reducing tools, processes and concepts (e.g. center-lining, visual replenishment, visual management, performance improvement teams, SMED, statistical analysis, pull systems, problem solving, fixed sequence scheduling)
- Experience leading and following Safety/Security and Sanitation/Quality Policies and Procedures, and reporting and following through on any deficiencies
- Internal candidates are able to demonstrate understanding of MOS
- Demonstrated ability to work well with individuals and groups at all levels of the organization
- Skilled in organization, prioritization, and attention to detail
- Position will support multiple plants within the Great Lakes Central Division; must be willing to travel 80% of the time
- Ideal candidate will be based in the following locations: Huntington, IN, O'Fallon, IL, Franklin Park, IL, Louisville, KY, Livonia, MI or Grand Rapids, MI. No relocation assistance is available, therefore local candidates will be considered first and foremost
98
Continuous Improvement Manager, Quality Resume Examples & Samples
- Green belt/black belt certification is an advantage
- Advanced knowledge in Lean and 6-Sigma
- Good knowledge of GMP for biological products
- Excellent team builder / team player
- Proven Planning & Organizational skills
- Leads improvement initiatives for the Belgium QA organization in line with the overall Quality strategy and Quality plan as well as the business imperatives
- Supports improvement projects or initiatives to ensure alignment and compliance as appropriate
- Leads and coordinates strategic performance management (Objectives Setting and Review, Project Management Office of Quality, Total Quality Culture transformation initiatives) to monitor delivery and alignment of local plans
- Leads Quality innovation to generate compliant, practical, sustainable and creative alternatives in line with the overall strategy
- Act as a secretary for the Belgian Quality Leadership Team and committe
99
Continuous Improvement Manager Resume Examples & Samples
- Participate in the SLT to establish the roadmap for HmeX enablers that support the site specific priorities in line with CBNs
- Owner of HMEX and follow up on the deployment of the tools and concepts
- Challenge to standardize on best practices and ensure consistency in approach
- Ensure benefits of the Enablers prioritized and implemented
- 7 or more years of experience in manufacturing environment; with prior experience in a leadership role preferred
- Strong knowledge of business and technical tools and practices related to Manufacturing Excellence, Lean Manufacturing, TPM or other continuous improvement tools
- Practical experience and proven results driving continuous improvement principles and achieving targets
100
Continuous Improvement Manager Resume Examples & Samples
- Provide management, expertise, collation and guidance on all Continuous Improvement projects and activities
- To manage the Continuous Improvement projects for all designated operations in order to provide broader business benefit and a centralised focus
- Assist with Continuous Improvement proposals, coordinate and monitor progress
- Utilise Value Stream Mapping and coordinate with Operations/Contracts Managers to establish process Improvements
- Liaise with the site General Manager(s) to identify and achieve pre-determined target savings for the site through Value Stream Mapping and other activities
- Capture and co-ordinate all current Continuous Improvement projects and establish a reporting method for these projects
101
Continuous Improvement Manager Resume Examples & Samples
- Creates a strategic plan and road map to meet facility goals to improve inventory, productivity, scrap/defect etc
- Supports creating and implementing regional and local Lean and Six Sigma strategies and tactics in manufacturing facilities primarily as well as supporting functions
- Works within the infrastructure of Gates Lean and Six Sigma practitioners by training and coaching site associates in Lean Six Sigma methodology
- Leads plant/DC employees to diagnose and evaluate performance (safety, quality, service delivery, cost) challenges through root cause problem solving initiatives
- Develop and implement plant/DC solutions based on Lean and Six Sigma transformation philosophies, concepts, principles, tools, and techniques
- Assist in the design of work standards, quality control charts and systems and other elements of operational excellence to aid plant/DC improvement
- Help establish meaningful plant/DC metrics which monitor performance at a level sufficient to illustrate the true root cause of problems
- Other tasks or duties as assigned
- Create standards and transfer best practices throughout Gates facilities
- Assist in the design of work standards, quality control charts and systems, and other elements of superior manufacturing practice to aid plant improvement
- Degree in engineering or operations management
- At least 8 years of specific management experience and progressive responsibility in operations and/or supply chain
- Experience as operations manager, plant manager, or a leadership position for continuous improvement is desirable
- Experience driving a change management initiative
- Demonstrated ability to lead teams and implement projects through continuous improvement initiatives, such as Lean or Six Sigma
- Certification desirable (e.g. Lean, Six Sigma) with hands-on application - engaging floor practitioner
- Significant experience in implementing Lean systems at the plant level (e.g..Quick Change Over, Total Productive Maintenance, 5S, Kaizen events, level scheduling, KanBan systems, and Value Stream Mapping)
- Experience as a Six Sigma and Lean trainer
- Ability to build credibility and trust within the organization
- Demonstrate an understanding of the broader organization, and how this role fits into the strategic plan and overall direction of Gates
- Create alignment so employees understand the strategy and how their contribution further organizational success
- Reinforce the business plan and strategy by building a disciplined, consistent approach with measurements of success
- Bring focus, purpose, and agility to motivate others to adapt quickly to changing business needs
- Take the initiative to look for and take advantage of opportunities and take independent actions and calculated risks
- Work with internal and external stakeholders in a variety of formal presentation settings
- Demonstrate organization skills
- Demonstrate ability to drive and report metrics
- Master Black Belt or Lean Master highly desired
- Must be proficient with the use of Microsoft Office Suite (Outlook, Word, Excel, PowerPoint)
102
Continuous Improvement Manager Resume Examples & Samples
- Minimum 5 years of continuous improvement management experience with core competencies in the area of Lean/Six Sigma
- Strong and demonstrated track record of significant achievements in leading and executing Lean/Sigma programs in a global manufacturing organization
- Degree/Post Graduate Degree in Engineering or equivalent discipline
- Master Black Belt/Black Belt certified by independent certification body
- Strong ability as change agent with demonstrated ability to influence change for results
- Possesses strong technical competencies in engineering, business and continuous improvement processes in a high volume manufacturing environment
103
Continuous Improvement Manager Resume Examples & Samples
- 5+ years of experience in contact centre / outsourcing space
- 3+ years of experience with CRM voice or non-voice business (chat & email)
- 2+ years of experience in people management
- Managed at least 3 improvement project – CSAT/Resolution/Cost/AHT etc
- Preferred - Experience within technical & customer care domain
- Effective communication with account leadership
- Ability to identify improvement opportunities
- Six Sigma / LEAN knowledge or certification
- Flexibility to work in shifts and sites
- Knowledge of MS Excel & PowerPoint
104
Continuous Improvement Manager Barcelona Resume Examples & Samples
- Help drive the implementation of Lean Standard Work. Create a common understanding of the Lean Standard Work principles. Support and manage the FC implementation Agenda. Contribute to and facilitate Kaizen activities. Train and support all levels and act as multiplier on lean, standard work and Kaizen/PDCA methods
- Standardize processes: Actively share best practices and ensure ongoing communication with EU Process Owners to avoid duplicate efforts
- Highly motivated, customer-obsessed, flexible to deal with constantly changing demands to drive improvements on behalf of Amazon customers in a fast-paced production environment
- Experience in an Industrial Engineering, Business Process Engineering, Quality, Operations or Logistics role
- Project Portfolio Management experience. Demonstrate a strong track record of team leadership within a large-scale, rapid and process-driven environment
- Excellent communication skills (written and verbal). Active networker. Shop-floor affinity
- In-depth knowledge of Lean Six Sigma and its practical usage to solve problems and optimize processes
- Wide range of method skills and practical experience, especially on continuous improvement and change management
- Didactic skills and experience
105
Continuous Improvement Manager Resume Examples & Samples
- To support the deployment and implementation of GKN Lean Enterprise
- Provide coaching and expertise on lean tool application to solve problems
- Facilitate site-wide continuous improvement activities (production and business process) and support Continuous Improvement Leaders (CIL’s) in their activities; ensuring commonality of approach
- Liaise with corporate function to install best practice
- Work with the Site Steering Committee to develop the site continuous improvement plan (CIP) and continuous improvement strategy
- Lead site Continuous Improvement leaders, including task prioritization, coaching, training and development, and supporting their interaction with management
- Plan and oversee layouts of equipment, people, and processes to create flow; conduct time studies and work with engineering teams to develop standard work processes
- Identify cost saving projects and track predicted savings
- Maintain the facility suggestion system and ensure that actions are tracked and closed in a timely manner
- 3-5 years Leadership Experience – Technical and managing direct reports
- Trained in Lean tools and techniques
- Analytical Skills/Formal Problem Solving
- PC Skills-Office/PPT/Excel
- Value Stream Mapping ability
- Demonstrated portfolio with quantifiable results
- 4 yr degree required
- Six Sigma Blackbelt trained
- Engineering Experience – prefer Industrial Engineer
- Lean Launch Experience
- Startup Experience
- Autocad Experience
106
Continuous Improvement Manager Resume Examples & Samples
- Act entrepreneurially on matters related to CI; lead, guide, and energize the business
- Plan, lead & execute actions aligned to strategic objectives
- Take the CI process to new heights (e.g. lead-time reductions , single piece flow)
- Improve safety, quality, productivity, and delivery in all departments
- Collaborate with leadership to ensure employees are engaged during the Lean journey, providing leadership to plant lean steering committee
- Develop & carry out Lean training for all employees
- Align CI activity to business strategies
- Deploy the lean strategy, monitor results and report progress
- Work with HR to measure the effectiveness of cultural change
- Regulate and alter workflow schedules according to established manufacturing sequences and lead times to expedite production operations
- Recommend methods for improving utilization of personnel, material, and utilities
- Plan and establish sequence of operations to fabricate and assemble parts or products and to promote efficient utilization
- Develop manufacturing methods, labor utilization standards, and cost analysis systems to promote efficient staff and facility utilization
- Review production schedules, engineering specifications, orders, and related information to obtain knowledge of manufacturing methods, procedures, and activities
- Confer with vendors, staff, and management personnel regarding purchases, procedures, product specifications, manufacturing capabilities, and project status
- Apply statistical methods and perform mathematical calculations to determine manufacturing processes, staff requirements, and production standards
- Analysis, recommendation, and implementation of enhancements to exiting work methods flows and processes to increase throughput
- Responsible for keeping abreast of developments in the field through contracts with professional societies, educational centers, journals, periodicals, etc
- Is responsible for the quality and safety of own work and compliance of all company procedures and policies
107
Continuous Improvement Manager Resume Examples & Samples
- A minimum of 10+ years of manufacturing or similar experience
- Bachelor's degree in Engineering preferred
- Experience in facilitating Kaizen workshops with demonstrated high impact results
- Previous program/project management with project results
- Lean Six Sigma knowledge preferred
108
Continuous Improvement Manager Resume Examples & Samples
- The incumbent will provide leadership and support to optimize, standardize and deploy ELSS strategy, principles and practices across the sub-regional sites in APAC. Lead and/or facilitate ELSS (Eaton Lean Six Sigma) projects, EBS (Eaton Business System) activities, EBS-PULL, OpA, and deploy ELSS through tactical activities and facilitation of kaizen events in major sites. Develop ELSS deployment procedures and policies, sharing of best practices across the APAC region
- Support development of site ELSS knowledge, coach and grow site talent on Continuous Improvement (CI). Determine and share CI best practices
- Drive improvement in site processes and achieve targets on cost saving and other business metrics
- Support key business segment’s cost effectiveness projects and actions, product cost reduction initiatives and ensure achievement of business benefits determined in each project
- Lead, facilitate or support site Needle Mover projects, RIE events, Business Process Improvement (BPI) projects, including non-Cost-out CI projects
- Follow-up the development and improvement of process and system to enhance and sustain process reliability
- Support OpA, EBEA (Eaton Business Excellence), and other EBS initiatives and activities as assigned
- Analyze and improve manufacturing and business processes using lean methods and tools, real-time problem solving techniques and other statistical and quality improvement tools
- Initiate operating principles that focus on process standardization, visual factory, flow focus, accountability of tier meetings, etc
- Mentor and support candidates of Lean Development Training and Lean Certification throughout the certification processPrepare and conduct ELSS related training for sites and develop on-site ELSS knowledge and talent
109
Continuous Improvement Manager Resume Examples & Samples
- Lead the execution of the Business Improvement (BI) plan for a manufacturing unit, ensuring that cross functional teams are engaged to focus on the specific priority areas and have the appropriate tools and/or necessary support to utilize them effectively
- Deliver training, up to yellow belt, as specified by Manufacturing Unit training plan to build capability across all functions
- Provide coaching and hands on support for the use of foundation elements of the business improvement toolkit to build practical experience and ongoing capability
- Engage key stakeholders to sponsor BI activity and act to embed a continuous improvement culture
- Selection of tools, from the UK tool kit based on nature of the problem and the business need, to make businesses improvements and promote the development of the manufacturing unit
- Draw on divisional best practice and benchmarking to inform manufacturing unit application of tools and solutions
- Review and analyze scorecard performance for the Manufacturing Unit teams to ensure data integrity, generate insight and action improvement plans which develop current performance
- Lead and direct the Manufacturing Unit BI team to ensure that people are kept safe, engaged, focused, developed and delivering their potential
- Identify resource requirements and work with Senior Leaders to build appropriate teams to deliver agreed programs of work
- Six Sigma Black Belt or degreed Engineer (Mechanical, Industrial, Process, Chemical, or similar) with attainment of Black Belt in one year. Expected progression to Master Black Belt
- Bachelor’s Degree is required for this position. The degree may be in engineering, business, food science or other related fields
- 5 - 7 years of related experience in manufacturing required - food industry preferred
- Possess keen team leadership, problem analysis, problem solving, and process improvement skills
- Must have the ability to operate relatively independent and should be comfortable in doing so
- Be proficient in Microsoft Office Suite and possess experience in data analysis programs
- Ability to analyze and utilize data to drive continuous improvement
- The ability to solve practical problems and deal with a variety of variables in situations where there is limited standardization
- Knowledge and experience with Lean processes and problem solving tools
- Have the ability to interpret a variety of instructions which may be in written, oral, diagram, presentation or schedule form
110
Continuous Improvement Manager Resume Examples & Samples
- Manages the OPEX CI activity
- Takes charge of process improvement, standardization, simplification
- Enhances collaboration from process perspective between functions and departments
- Monitors BCO
- Monitors Automation
- Manages New customer implementation
- Analyses and evaluates existing processes or sub processes operating systems within the context of business requirements
- Proposes changes or enhancements to help achieve the business goals among other things via analytics delivery
- Has accountability for robust process governance methodologies in the Organization
- Manages relations with relevant business stakeholders
- Leads, coaches & drives analytics excellence in team
111
Continuous Improvement Manager Resume Examples & Samples
- Evolve A&B Process Systems into a “Relentless Continuous Improvement” culture
- Working with employees at all levels of the organization to go from being “Firefighters” to “Improver/Growers”. Emphasize cultural change at the management level
- Knowing, understanding, and supporting Visual Management System methodology and execution
- Leadership and Management
112
Continuous Improvement Manager Resume Examples & Samples
- Promote and provide technical and organizational leadership in teams, based on a culture of improvement, ensuring the sustainability of practices and methodologies in the supply chain
- Detect and deploy programs and improvement projects, that challenge the status quo of the operation area, interacting directly with all areas involved
- To coordinate and encourage the generation of continuous improvement and productivity projects, contributing with at least 50% of the total productivity of the areas in charge
- To develop, share and implement best practices between the different plants operation processes in Mexico
- Manage and lead the effective implementation of improvement tools in cross-functional teams
- Manage the effective implementation of operation improvement tools
- Fulfill and ensure that, the team meets the standards (OHSAS 18000) and security policy
- Ensure compliance with the security measures applicable to the task
- Fulfill and ensure that the team meets the standards (ISO 9001, FSCC 22000 "Food Safety System Certification" and "Quality, Cost, Moral, Sustainability QCMS) and quality policy
- Degree in Engineering, Master's degree in Manufacturing, Administration, Quality, and/or Productivity
- Verifiable degree in continuous improvement techniques: Courses and diplomas in Continuous Improvement, Lean Manufacturing, Six Sigma
- Applicable courses according to the training matrix
- Organizational process improvement through tools and/or analysis methodologies (lean manufacturing, Six sigma, Changeover, work methods, etc.)
- (Desirable) Black Belt training at a recognized institution (ASQ American Society of Quality or University) for example
- Administration of personnel, coordination and management of high performance teams, at different organizational levels, as leader and facilitator of projects and strategies
- Project management and financial impact assessment
- Negotiation and Effective Influence
- Development of efficient teams
- Skills to solve complex and ambiguous situations
- English: 80% advanced. Must write, read and speak English with medium to high knowledge in technicalities od the business
- Management project knowledge
113
Continuous Improvement Manager Resume Examples & Samples
- Continuous Development of the productivity decks
- Generate cost reduction opportunities and implement process improvement to reduce manufacturing costs
- Participate in the QRMP yearly audit and assist in the development of procedures and corrective actions
- Assist with the implementation of the QRMP (Quality Risk Management Process) system and operational standards as outlined in the plant accountability list in order to achieve targeted RCR
- Share and implement best practice initiatives across Supply Chain
- Develop and maintain performance (KPI) visuals
- Develop a waste analysis for all lines
- Manage and evaluate the Continuous Improvement staff including but not limited to performance management and employee development, etc
- Partner with business leaders on implementation of process improvement (Six Sigma / Lean)
114
Continuous Improvement Manager Resume Examples & Samples
- Develop, maintain, and roll out Continues improvement training modules. Develop standard work structure for week long kaizen evets. Examples: Standard Work For Flow, Transactional Process Improvement, ingle minute exchange of dies (SMED), Value Stream Mapping, Production Preparation Process (3P), Process Control, and Materials management
- Oversees the implementation and consistent application of Lean techniques and continually evaluates areas for improvement; Annual assessment, Future factory Vision, continuous improvement road maps, key performance indicators (KPI) metrics, and site maturity
- Develops an infrastructure to support continuous improvement and quality initiatives including the establishment tracking and reporting on site progress to Continuous Improvement Roadmaps and site maturity matrix
- Employs Lean Manufacturing methodology and analytics into organizational operations in order to accomplish business objectives
- Serves as a dynamic change agent and directly leads select business improvement projects
- Executes a strategy that drives cultural change within manufacturing operations aligned with the overall business strategy: to identify areas of continuous improvement, eliminate waste, decrease cost, promote uniformity of policies, and track progress
- Drives Executive Management to develop and measure Key Performance Indicators (KPI) on a monthly, quarterly, and annual basis
- Develops strategic operational plans in collaboration with Executive Management
- Coach and Mentor leaders around the organization on continuous improvement fundamentals
- Responsible for the development and codification of standard Lean Manufacturing methods and training materials
- Oversees the execution of the overall Continuous Improvement efforts across API. Tracks performance of improvement initiatives against plans against roadmaps
- Analyzes and measures the effectiveness of existing business processes and develop sustainable, repeatable and quantifiable business process improvements
- Proactively recognizes, plans and acts on the need for innovation and improvement
- Produce and present monthly reports on progress of ABS and IC development
- Assembles multiple teams as needed to support tactical efforts
115
Continuous Improvement Manager Resume Examples & Samples
- Drives tangible and measurable improvements of key processes through the leadership, training and mentoring of a team
- Assist teams in developing a Lean Roadmap to use in the deployment of strategic objectives
- Coach and mentor RBS Engineers and leaders in the use of various tools, concepts and practices around RBS
- Directly supports a site in achieving strategic deployment objectives by conducting on-site workshops, kaizen events, assessments and providing guidance through the lean transformation process
- Develop and upgrade RBS materials
- Identifies and shares best practices across
- Work with the Plant Manager and other functional leaders as a “thought leader” to define current state situation, assess gaps in process, capabilities, & talent, while assisting in the development of the future state in line with strategic plans
- Delivers and sustains measurable results
- Sets high expectations for sustained excellence
- Self-starter: action oriented / "can do" attitude / resourceful
- Ability to coach, mentor and develop associates
- Matching 401(k) contribution
- Discretionary Personal Reimbursement Account
116
Continuous Improvement Manager Resume Examples & Samples
- Leads and drives lean transformation and change initiatives to create and sustain a world-class visual manufacturing operations site for instantaneous recognition of waste in all areas
- Implements STERIS Business System (based on Toyota Production System - TPS) continuous improvement activities in all major lean disciplines and in alignment with strategic initiatives and objectives
- Facilitates and/or conducts lean training programs, Kaizen events, and other lean initiatives. Assesses, coaches, and provides constructive feedback to teams to strengthen lean competencies within the company
- Serves as a change facilitator, develops and collaborates with business lean champions, and influences site leadership in the transformation to and/or in support of a continuous improvement culture
- Develops and manages multiple processes, long and short-term, sustainable, lean-related visual action plans as well as key projects implemented
- Monitors existing and new manufacturing and administrative processes for improvement opportunities in safety, quality, delivery, and cost through lean problem solving methodology
- Tracks, measures, and reports progress on improvements using standard, established Key Performance Indicators
- Assists in the preparation of budgets, schedules, and other financial reports particularly regarding the impact of and sustainment of lean improvements, waste reduction, ROI, and as indicated by lean accounting principles
- Maintain professional and technical knowledge through world class lean operations benchmarking
- Organize and facilitate business Lean Steering Committee
- Oversee SQDC, 5S, Hr x Hr boards for compliance to standards
- Initiate, maintain and share site developed “best practices”
- Bachelor degree required, preferably in Engineering, Manufacturing, or related discipline
- Lean manufacturing (related) training required, preferably from Shingijutsu or nationally recognized certification body (SME/AME/ASQ/Shingo)
- Minimum of 10 years of demonstrated qualified lean manufacturing experience in a leadership role required
- Solid knowledge and demonstrated understanding of Toyota Productions System and methodologies such as: A3 Development and Management, Process Flow Mapping, Value Stream Mapping, 5S/Visual Factory, TPM, QCO-SMED, Standard Work, Process Problem Solving and root cause analysis (PDCA), Quality at the Source, Just In Time, Kaizen/Continuous Improvement, abnormality management, Hoshin Kanri – SD- X Matrix, project management, cellular and model line development
- Extensive use of Gemba based continuous improvement tools/techniques
- Knowledge of and demonstrated ability to integrate safety, ergonomics and 5S requirements with lean manufacturing and other business practices
- Proficiency with personal computer applications, required (Excel, Word, Visio, MS Project and Power Point)
- Superior and demonstrated leadership, team building, communication, presentation, interpersonal, and coaching skills and the ability to ensure accountability
- Demonstrated ability to work effectively in a fast paced and changing environment with multiple priorities while driving results
- Ability to interpret manufacturing schematics and blueprints and interface effectively in technical situations
- Ability to mentor and facilitate lean culture change in an environment with varying acceptance
- Knowledge of assembly line balancing and Toyota Kata highly preferred
- Incumbent must exercise independent and group problem solving skills to meet the objectives set forth by the senior business leader and Director of Lean Enterprise along with opportunities captured by lean events and activities
117
Continuous Improvement Manager Resume Examples & Samples
- Manage the Fulfilment Centre improvement plan to focus on best customer experience at the lowest cost
- Contribute to and facilitate Kaizen activities
- Help drive the implementation of Lean Standard Work
- Train and support all levels in Kaizen activities
- Disseminate Lean Standard Work principles across teams
- Support and manage the Fulfilment Centre implementation Agenda
- Take ownership for the LSC (Leadership Steering Committee)
- Coordinate and prioritise LSC process improvement activities and resources
- Standardize processes and actively share best practice with EU Process Owners to avoid duplication
- Liaise between FC and EU to drive leverage of cross-FC process excellence
- Maintain strong relationships with EU Process Owners and FC Process Engineers
- Project Portfolio Management experience
- A strong record of team leadership in large-scale, rapid, process-driven environments
- Very strong analytical capabilities
- The ability to translate operational issues into workable solutions
- In-depth knowledge of Lean Six Sigma and its practical usage
- Wide knowledge of change management and continuous improvement methodologies
- Demonstrable training and dissemination skills and experience
118
Continuous Improvement Manager Resume Examples & Samples
- 6+ years of related experience in either Materials, Operations, Quality or similar role in a plant environment
- Hands-on experience using LEAN, TPM, Six Sigma, and TQM
- Black Belt or Master Black Belt certification
119
Continuous Improvement Manager Resume Examples & Samples
- Support the Company''s mission, vision and values in performance of daily activities
- Provide key input into the development of the Plant''s strategic business plan and identify and track key measurable to support plant business plan goals
- Develop and drive the development of departmental strategic goals and identify and track key measurable to support the department goals
- Guides the design, development and implementation of cost reduction plans to improve competitiveness and operational excellence
- Guides the design, development and implementation of process improvement initiatives and activities throughout the plant to improve competitiveness and operational excellence
- Review and measure manufacturing methods, technology application and workflow processes and apply lean/continuous improvement application skills
- Responsible for working with the leadership team to plan, execute, monitor and continuously improve plant and corporate objectives
- Provide support and guidance to all departments in the application of lean/continuous improvement manufacturing techniques
- Monitor the effectiveness of the Tower Automotive Production System, anticipate problems, implement corrective action and develop adjustments to the system
- Guides the design, development, implementation and monitoring of verification methods to ensure team members are gaining knowledge from the training and that the continuous improvement activities are sustainable long term
- Track, monitor and implement required improvement activities related to business plan, goals, issues, etc
- Assist with plant activities to achieve customer cost reductions goals
- Provide active leadership role in meeting / exceeding customer expectations in all related areas
- Utilize teamwork to develop plant synergy
- Drive plant activities towards achieving customer awards and Quality registrations (ex. TS 16949, ISO 14001, Pentastar, etc.)
- Interface with customers and suppliers as appropriate
- Responsible for following all internal and OSHA required procedures in performing daily activities and hold direct reports accountable for enforcement
- Provide leadership essential to maintaining safety as a fundamental priority in plant based activities
- Responsible for ensuring the entire team has the necessary training, tools and materials to properly perform their roles safely and efficiently
- Maintain high standards of housekeeping throughout the plant
- Provides direct leadership and supervises continuous improvement staff in the plant
- Bachelor''s Degree in business related field, prefer manufacturing, engineering or quality, Master''s Degree preferred
- Minimum six (6) or more years experience in a manufacturing environment with experience in a metals environment preferred, or a combination of degree and experience
- Possess knowledge of plant department functions and corresponding roles and interactions to facilitate overall plant synergy
- Vision and ability to translate progressive operating techniques into applications and results
- Specialized knowledge and the ability to train and mentor others in formal problem solving techniques such as Kaizen, value stream mapping, JIT synchronous, SMED quick die change, etc
- Demonstrated experience in applying lean manufacturing concepts
- Experience in quality and environmental measurables such as TS 16949 and ISO 14001
120
Continuous Improvement Manager Resume Examples & Samples
- Be an agent of change and lead the TPS improvement efforts for the plant ensuring achievement of targets and goals
- Be the key plant contact with platform, enterprise and contract resources to drive TPS program development and implementation. Provide status updates as required
- Serve as a key plant contact for Research and Development activities
- Partner with Operations, Maintenance, Safety, and Quality leadership to create a Zero Loss environment at the plant
- Conduct and update periodic opportunity assessments, providing guidance to plant leadership on top areas of opportunity within the facility
- Conduct line capability and/or loss studies for assigned areas
- Facilitate training to assigned teams for key problem solving and focused improvement methodology tools
- Train and coach plant personnel in continuous improvement processes and problem solving tools to improve results
- Provide project management support to assigned strategic initiatives
- Oversee the line performance tracking data and utilization
- Diagnose and evaluate performance challenges in the areas of quality, productivity, and waste and drive improvement activities
- Support plant leadership in annual operating and capital plan development
- B.S. degree at minimum, preferably in Industrial Engineering, Business or Finance
- Previous TPM or Lean Implementation Leadership experience required
- 5-7 years previous experience in manufacturing and/or engineering, preferably within food or consumer packaged goods industry
- Exposure to multiple Supply Chain and other business disciplines (purchasing, manufacturing, logistics, R&D, etc.) in previous positions or project work preferred
- Strong understanding of manufacturing unit operations
- Exposure to productivity/continuous improvement methodology in previous positions
- Strong statistics, data modeling/analysis skills
- Understanding of plant cost structure and Supply Chain COGS. Able to interpret and build product costs, analyze trends and complete project valuations (using discounted cash-flow techniques)
- Excellent communication skills - both formal and informal. Ability to communicate within all levels of the organization
- Strong computer competency required
- 5+ years in a continuous improvement manufacturing role and relevant degree or equivalent experience
121
Continuous Improvement Manager Resume Examples & Samples
- Provide leadership and direction to cross-functional manufacturing teams empowered to execute projects for continuous improvement
- Coach, lead and mentor key plant functions, including Quality, Operations, Maintenance, Finance, Production Planning, Regulatory and Transportation
- Map process flow, suggest changes to reduce process steps and times and build SOP's as well as working hand in hand with Quality and Safety to deliver a high quality standard
- Develop standard operating procedures, specification documents, protocols, training programs, trouble-shooting guides and other documents to establish, improve and sustain operational and maintenance processes
- Create project timelines, measure effectiveness of progress, maintain project timeline while meeting key milestones and measuring overall success
- Deliver breakthrough levels of improvement in process capability and cost effectiveness
- Benchmark against best in class tools & methods and share best practices within the business
- Coach, lead and mentor Senior factory leadership in establishing and maintaining a culture of continuous improvement throughout the entire site
- Build key competencies and capabilities throughout the site to include Problem Solving, Standard Routines, Measures Development and Operational Reviews
- 4-5 year Bachelors of Science Degree in Engineering preferred
- Strong coaching skills and ability to influence with integrity
- Very Process-oriented individual with strong experience in documentation, process standardization, creating Work Instructions, SOP’s, etc
- Experience with DOE’s and SPC would be a big plus
- Extremely strong knowledge of formal continuous improvement programs and the ability to implement CI theory such as 6-Sigma and Lean (TPS)
- Other helpful knowledge and skills would include 5-S, Fishbone Diagrams, Process/Value-stream mapping, TPM
- 2-3 years’ experience in process, packaging or discreet manufacturing industries; food related preferred
- Ability to thrive in a fast paced, aggressive, results oriented culture
- Superior team building and communication skills to work with all levels of the organization
- Exceptional people skills, oral and written communication skills
- High level of competency in obtaining information and data, analyzing spreadsheets and business software, and applying and presenting data to drive improvements.EEO/AA/M/F/Veteran/Disabled
122
Vnc-area Continuous Improvement Manager Resume Examples & Samples
- Actively build on the 16 weeks OPEX deployment and keep the implemented tools, techniques and behaviors alive in the Area
- Support, train and coach the entire Area in OPEX tools and techniques where needed
- Support the Area/country management (and the various teams in the Area) in continuously improving the Area performance at all identified levels and metrics
- Share identified and implemented improvements with other Area
- Implement identified improvement ideas from other Area
- Implement & test suggested improvements / changes to the standard processes as defined by the global process owners
- Introduce end-to-end process mindset into the Area (by understanding how the Area is performing into the entire Damco network; how the Area impacts other Area and CO’s performance)
- Ensure that changes / updates / improvements to the initial training material are effectively cascaded through the entire Area
- 1 OPEX /CI Ambassador and coach
- Sustainability and expansion of OPEX in the Area depends very much on keeping alive what has been deployed in the 16 weeks deployment. This role is instrumental in this. Continuously the organization has to be challenged and coached to keep OPEX and Continuous improvement alive
- The CI manager is the Ambassador who defends at all levels and in all situations OPEX and the CI mindset
- Case needed the Area CI manager will also be the project manager of local improvement projects, however this will only happen occasionally; in principle, the local teams manage the identified improvement projects supported by the Area CI manager
- 2 Area management support
- Challenge Area management in their CI thinking and drive
- Help the Area management to identify improvement initiatives that drive the overall improvement of the Area
- Teach and coach lean leadership to the Area management
- 3 Support and training
- Provide CI / OPEX training and support at all levels in the Area where needed
- Ensure that at all levels in the Area the OPEX/CI competencies are assessed and improved where needed in collaboration with the respective management (teams)
123
Continuous Improvement Manager Resume Examples & Samples
- A truly international working environment in a modern working location with lots of challenging improvement opportunities
- Value and team-based leadership focused on creating synergy by cooperation and functional coordination
- An open and engaging working environment and speak up culture
- Opportunities for personal and professional growth in a dynamic environment
- Work-life balance
- Competitive compensation packages
- To have direct responsibility for the study of existing processes within the Port, developing Operations Procedures and identifying methods and products by which these operations could be improved or streamlined in order to provide maximum cost effective benefits to the Port
- To organize training for new potential CI professionals and mentor project owners to ensure effective process improvement pipeline and performance culture
- To maintain an audit and oversight program to monitor processes within the Port are carried out in accordance with laid out procedures
- To give recommendations on operations process improvement to Operations
- To create a pipeline of improvement projects ensuring that these projects are classified and prioritized for implementation
- To ensure that documentation on operating processes and improvements are constantly mapped and updated
- To agree and ensure completion of a predetermined number of improvement activities and their minimum values set as KPI every year with the Port management team
- To assist the Management team in meeting and maintaining the Port KPIs
- To ensure that proper management control systems are in place to ensure that focus is maintained on process improvement on a constant and ongoing basis
- To ensure that best practices are shared throughout the group network through the use of portfolio and global functions
- Master’s degree in Business Administration or equivalent
- Good knowledge and work experience with process excellence frameworks (Lean 6 sigma green belt, black belt preferably)
- In-depth, comprehensive understanding of port business processes would be considered as advantage
- Ability to work under pressure, anticipate potential problems and diagnoses, evaluate and resolve problems as they happen in order to meet process performance objectives and deadlines
- English – fluent verbal, written communications and report writing skills; Georgian and/or Russian will be a plus
- Excellent interpersonal, mentoring and change management skills
- Effective negotiation and conflict resolution skills, as well as excellent managerial skills, including planning, organizing, and directing work, proven problem solving skills
- Strong analytical skills, including the ability to extract, compile and analyze data
- Strong interpersonal skills and business savvy
124
Rapid Continuous Improvement Manager Resume Examples & Samples
- Engineering Degree from an accredited university required
- Project Management Certification is preferred/experience is required
- Six Sigma Black Belt Certification – if you do have this you will be expected to acquire this certification during your first year
- Ability to provide strong leadership and guidance to your team
- Ability to foster an inclusive environment within your team and between departments
- Previous leadership experience within a manufacturing environment
- Previous CAD experience and the ability to read and interpret prints and drawings including G, D, & T
- Ability to model our mission statement and Who We Are including our Beliefs, Values, and Vision
- A positive attitude that encourage teamwork and collaboration
125
Continuous Improvement Manager Resume Examples & Samples
- Provide input and leadership to define Continuous Improvement and Safety Initiatives throughout facilities
- Lead continuous improvement projects through the project life cycle to include activities such as process assessments, project planning, collaboration with stakeholders and process users, process observation and baseline metrics collection, team facilitation, and follow-up to ensure sustained results
- Assist in the continued embedment of our Customer First Culture by working with production supervisors and team members to develop their understanding of our Customer First model and their impact to the Customer
- Develop and utilize tools and techniques to extract, quantify, interpret, analyze, summarize, and visually display and present data
- Effectively communicate project expectations to team members, including delegation of responsibilities to appropriate team
- Conduct Six Sigma, Lean projects, leading teams to address business process problems and design new processes to achieve results
- Coach site managers to establish performance measurement systems and goals aligned with organizational objectives
- Conduct Kaizen Leader Training and mentor Kaizen leaders
126
Quality & Continuous Improvement Manager Resume Examples & Samples
- Manage / improve the maturity of the Quality Management System, Corrective Action Process and Continuous Improvement across the Charlotte Operation
- Provide Quality Management and Continuous Improvement (ACE) expertise and communication to align team members, other departments and leadership around organizational strategy, values, goals and objectives
- Support strategic initiatives to drive reduction within customer, supplier, and operations quality metrics
- Lead / drive investigations and corrective action for customer related failures, and facilitate customer quality & reliability interactions
- Support and ensure timely response to customer inquiries to improve customer satisfaction
- Collaborate with design, marketing, supply chain, and manufacturing organizations to ensure new and changed product are designed for manufacturing and reliability
- Lead the manufacturing quality team on passport deliverables for all new programs
- Direct quality projects, investigations and corrective actions by establishing strategy and providing leadership and organization necessary for success
- Prepare for and present quality reports to upper management and customers
- Establish firm expectations for the team and help manage multiple projects simultaneously
- Develop, coach, mentor and manage staff. Establish goals and develop measurable metrics to gauge achievement against goals
- Accountable for budget, staffing, and/or business/operational results
- Support strategic initiatives to enhance supplier performance surveillance and drive process controls and improvement
- Drive UTC Continuous Improvement (ACE) initiatives (i.e. six sigma, lean transformation, etc), while assuring successful annual recertification
- Lead / drive a culture of continuous improvement through the use of ACE tools to implement change that strives for ACE Gold performance and supports the Chiller Operations factory transformation plan
- Prepare and host Regulatory Inspections and complete all audit responses timely to sustain certifications
- At least 8 years of experience in Quality, Manufacturing, and/or Engineering with at least 3 years of supervisory experience
- Demonstrated ability to interface with all levels of leadership, suppliers, and external customers, responding in a professional manner
- Experience with ISO9001
- Experience with ASME code a plus
- Ability to assess complex situations, articulate options and identify important actions
- Problem solver who not only identifies issues but leads efforts to resolve them
- Experience leading, communicating, and influencing a cross-functional Management team
- Strong and thorough quality knowledge, including
127
PC&L Continuous Improvement Manager Resume Examples & Samples
- Lead & manage the PC&L Improvement Coordinators network
- Master's degree in engineering or Supply Chain management
- Experience in PC&L management in plants
- Knowledge of PC&L FCP’s and Tools
- International mind set, overseas experience
- Commitment to the highest ethical standards and willingness to adhere to Faurecia's Code of Ethics and Code of Management
128
Continuous Improvement Manager Resume Examples & Samples
- Improve site performance
- Drive and manage the improvement portfolio
- Lead and support the ALPS deployment on site
- Champion, develop and sustain a culture of continuous improvement (CI) and knowledge about related
- Champions deployment of change management processes and tools to realize the business strategic objectives
- Run own improvement projects delivering value to the organization
- Network within the AkzoNobel CI community and share insights, problems and opportunities to promote improved
- Relevant work experience (operations, production, maintenance, logistics, (process) engineering,
- Strong analysis and problem-solving skills, able to identify and structure issues, run accurate (also statistical) analyses
129
Continuous Improvement Manager Login to Save This Vacancy Resume Examples & Samples
- Take lead responsibility for all Continuous improvement for the Group and be a driving force for change
- Work with key stakeholders to identify and deliver areas for improvement and prioritise those that provide the best benefit for the Group. Establish a close link with the IT team in particular to identify current and future processes to ensure we adopt value improvement on all projects (both financial and non financial)
- Efficiencies will be identified and set as targets for the Continuous Improvement Manager and the relevant champions to deliver against throughout the year with the CI Manager accountable for the overall delivery
- Work closely with the nominated Business Champions to ensure projects and processes are successful across all functions with impacts understood across all functions
- Be the lead on process mapping all processes end to end to identify opportunities where deep-dive workshops are required
- Be able to translate operational issues into workable solutions and engage the operational team throughout so “change in not done to them”
- Responsible for the preparation of senior manager reports and presentations defining opportunities, costs and benefits
- Develop a culture of continuous improvement and “lean” thinking and where possible standardise processes and procedures. Suitable governance framework to be developed so we are able to refer to current processes easily and adapt to change as the people, processes and technology evolve
- Significant experience (5-10 years) of implementing lean/ continuous improvement within a complex organisation
- Keen advocator of change (where change is appropriate) and consultative approach with strong communication skills to demonstrate benefits of process improvements
- Strong influencing skills and experience in dealing with multiple stakeholders to deal with any cross functional barriers
- Commercial grasp and the desire to succeed with a proven track record of driving improved profitability
- Strong communication skills both written and verbal with the ability to work both independently and collaboratively
- Energy and passion for innovating processes proactively to deliver improvement strategies and results
- Be comfortable with ambiguity but be able to distil it into structured outcomes
130
Continuous Improvement Manager Resume Examples & Samples
- Facilitates internal Continuous Improvement and Six-Sigma activities
- Primarily responsible for the implementation of the Shiloh Production System
- Gathers information to evaluate current work processes in order to determine the flow of work, time requirements, costs and duration
- Drives methods improvement for worker efficiency and reducing waste through deployment of lean tools, especially value stream mapping. This includes materials and utilities such as restructuring job duties, reorganizing work flow, relocating work stations and equipment, and cost justification of new equipment as necessary
- Drives cost control and reduction programs with his/her general knowledge and special skills while assisting the management team through deployment
- Use project management and lean methodology to lead and guide related plant projects and deliver process and financial results within a specific time frame. conducts progress reviews with Plant Managers, Directors - Operations, and Executive Management
- Develops and coordinates programs to recognize and reward groups or individuals for suggestions and actions related to process improvement
- Facilitates employee teams to build cohesiveness and improve the overall results
- Train employees, as needed, in all aspects of lean manufacturing, team effectiveness and continuous improvement
- Identifies and communicates best practices with and between other Shiloh facilities while implementing best practices from other facilities
131
Continuous Improvement Manager Resume Examples & Samples
- Manage the improvement initiatives that drive cost, quality, and productivity improvements
- Analyze data using Tableau & SQL
- Work with groups cross-functionally to develop and implement solutions across the organization
- Improve our cost, quality, and productivity positions
- Demonstrate strong analytical comprehension
- Ability to identify problems, map problems, develop solutions, and own the solutions through implementation
- Demonstrate sound ability to communicate across the organization about problems and solutions
- Process flow mapping ability using Microsoft Visio
- Bachelor’s degree in Operations Management or related business field
- 2-3 years’ business and analytics experience
- Tableau Experience
132
Global Senior Continuous Improvement Manager Resume Examples & Samples
- Bachelor Degree in engineering required, masters preferred
- Minimum of 8 years of progressive experience in engineering, testing, laboratory, equipment or manufacturing environment
- Understanding of Automotive and Industrial customer expectations and quality systems (TS-16949)
- Understanding of lab best practices for Operation and Safety
- Experience with product and process development (APQP)
- ASQ CRE, CQM or CQE desirable with hands-on application
- Experience driving change management initiatives
- Demonstrated ability to lead teams and implement projects through continuous improvement initiatives, such as Lean, Six Sigma, 5S, Kaizen projects
- Knowledge of ISO 9001 and TS16949 QMS standards
- Ability to interact with various levels of the organization
- Ability to influence leaders, their impact behavior, and thinking
- Prove ability to raise the performance bar – create, promote, and sustain a high performance culture that reinforces accountability
- Orchestrate and prioritize multiple activities at once to accomplish Company goals
- Prove ability to lead teams remotely
- Have Mechanical engineering knowledge
- Understanding and ability to apply concepts of testing and measurements
- Practical knowledge of mechanical products, mechanisms and systems for power transmission and/or fluid power applications
- Experience in supervising indirect people and managing multiple projects and/or teams
- Strong proficiency with Microsoft Suite and other ERP systems, such as Oracle and other programs used within the engineering profession
- Experience in partnering with business leaders on developing and driving global initiatives
- High Level interpersonal and leadership skills; must be able to influence and coach across multiple teams/levels within the company and locations; including establishing global partnerships
- Change management leadership capability
- DFSS and statistics knowledge
133
Continuous Improvement Manager Resume Examples & Samples
- Bachelor’s Degree in Engineering or Business
- Minimum of 5 years of Engineering, Quality and/or Operations experience
- Familiarity with Industrial Solutions products and services
- Experienced leading process improvements / RCAs / 8D
- Strong analytical and quantitative skills; familiar with statistics and Six Sigma quality concepts
- Change agent with strong credibility and influencing skills
- Impatient to deliver
- Experience & passion for process development, change management and influencing
- Greenbelt / Blackbelt Certification and/or a proven education or work history in leading and implementing projects
- Experience implementing and influencing
- Clear understanding of the basic roles, functions, and products / services / repairs within Industrial Solutions
- Self-motivated and possess demonstrated ability to motivate others to achieve results
- Committed to process improvement
- Customer-focused in defining and establishing priorities
134
Self-assessment & Continuous Improvement Manager Resume Examples & Samples
- Background in various safety management/functional area programs such as Conduct of Operations, Maintenance, Radiation Protection, Emergency Management, Quality Assurance or Training and Procedures is strongly desired
- Experience performing or leading performance of readiness reviews or independent verification reviews of safety basis implementation is strongly desired
- Specialized training or certifications related to quality management, conduct of assessments or safety programs is preferred
- WIPP related experience is preferred
135
Continuous Improvement Manager Resume Examples & Samples
- Lead the development and implementation of the site Continuous Improvement Program; define actions and coordinate cross-functional activities. Also, provide Lean and Six Sigma support across the organization to drive short- and long- term business improvements
- Lead the development of action plans based on plant-wide VSM, in conjunction with Front Line Leaders and value stream owners
- Lead multi-tool Kaizen events to successfully improve processes and establish follow-up action items based on opportunities identified
- Assist in facilitating site Continuous Improvement tools training
- Lead and support Eaton Lean Six Sigma (ELSS) Self-Assessment, and identify performance gaps. Works with the Leadership Team to prioritize improvement activities and to close gaps
- Utilize Continuous Improvement tools to eliminate waste, driving customer satisfaction, cost reduction, and improved working capital performance
- Demonstrate ability to perform and/or facilitate development of current and future state Value Stream Maps, and to drive resulting implementation plans
- Manage multiple projects, lead teams, and track progress to meet objectives. Identify and coordinate Kaizen events leading to improvements in on-time delivery metrics, while reducing costs and inventory
- Facilitate activities to drive a culture change toward the Continuous Improvement journey using the Plan – Do – Check – Act approach and the ADKAR methodology
- Schedule and coordinate regular Continuous Improvement Team meetings to communicate improvement status and schedule of events
- Support and participate in the Gemba Walk process by developing the schedule and tracking actions for advancement. Track and communicate progress of Beaver Continuous improvement deployment through the division and region, and interact with other plant Leaders to share best practices
- Possess a working knowledge of relevant ISO 14001 and 9001 standards, as well as Eaton’s Global Management System for the Environment, Safety, Security and Health (MESH) and Eaton’s Quality System (EQS)
- Support plant quality initiatives including developing A3s, Process Failure Mode and Effects Analysis (PFMEA), Control Plans, Method Sheets and Problem Solving efforts
- Collect and analyze product and process performance data, using applicable Six Sigma and Lean Manufacturing approaches, in order to identify sources of variation, and implement robust solutions to product design and manufacturing process challenges relating to both electronic & thermal-magnetic circuit breakers
- Establish part processing and implement processing and assembly of products to ensure the highest quality at the optimum production rate at the most economical cost
- This position is in an Operational and Excellence Department that supports a $100M+ business consisting of new and legacy circuit breakers and related products manufactured at the Beaver Plant
- Bachelor’s degree in Engineering or Business from an accredited institution required
- Minimum of 3 years of experience in manufacturing or operations is required
- Minimum of 1 year of experience in Lean, Six Sigma, or Continuous Improvement required
- Knowledge of LEAN manufacturing tools and manufacturing processes is required
- Demonstrated knowledge and training in process work instructions, standardized work, operator balance charts, and error proofing
- Experience with basic quality tools, such as capability studies and gages R&R´s
- Experience conducting multidisciplinary teams and ability to be self-motivated, drive for results, and operate in a complex manufacturing environment
- Strong communication skills and ability to communicate to internal/external customers in a clear, concise, and organized manner
- ASQ CQE Certification
- Green Belt/Black Belt (Six Sigma) Certification
- Bachelor’s degree in Mechanical, Electrical, Electronic, or Manufacturing Engineering
136
Senior Continuous Improvement Manager Resume Examples & Samples
- Continuous review of customer’s business requirements by identifying improvement projects and assess its value (e.g. by creating business cases)
- Re-engineering of existing services in order to save costs, improve process times or to adjust to
- University degree or similar level of education in transport business
- At least 8 years working experience in the logistics industry
- Creativity and solution driven thinking beyond limiting boundaries
- Understanding of Project Management discipline and solutions
- Structured process analysis and process documentation skills
- Strong affinity with required customer quality standards
- Language requirements: English
137
Continuous Improvement Manager Resume Examples & Samples
- Assess the current CI culture and define and implement the required aspects to build or improve it
- Define the Annual Operating Plan (AOP) ensuring alignment with the local and global strategy
- Act as the Champion for the AOP, measuring performance and working with the Senior Management Team to ensure results
- Quantify and drive improvements which then are captured in a project pipeline that is aligned with senior management as part of the annual planning process (AOP)
- Drive the implementation of a CI governance structure, including the required tools and training across functional departments, ensuring a sustainable terminal improvement roadmap
- Implement and manage the Process Performance System (e.g. Operational Dashboards) and other elements of the business KPI’s
- Establish a structure for the development and mentoring of CI Project Leaders (Black Belts and Green Belts), Kaizen Facilitators, and Project Sponsors
- Act as owner of the Business Process Manual and its subparts (Work Instructions, etc) via APM Terminals standard platform(s)
- Lead projects with higher complexity regarding analysis and/or change management
- Leverage the required skills and mindset by
- At least 3-5 years of experience in a Continuous Improvement role
- Proven experience with change management, cross-functional projects, conducting LSS training as well as Lean (Kaizen) events and mentoring CI resources
- Preferably experience with terminal operations and/or the transportation/shipping industry
138
Continuous Improvement Manager Resume Examples & Samples
- Lead teams within all operations areas in order to achieve manufacturing and process improvement goals. Specific key responsibilities include
- Provide effective change management and leadership in implementing the company’s Lean Enterprise strategy
- Current state identification
- Improvement opportunity Identification
- Future state development (6 month, 12 month, 18 month strategy)
- Implementation roadmap ownership
- Mentor and train individuals/teams on Lean Enterprise Implementation and serve as a subject matter expert and resource
- Program Manage annual cost reduction plans
- Facilitate improvement events and train/coach/mentor other team members in facilitation
- Establish budgets supporting Lean Enterprise activities, track performance vs. budget, and analyze/evaluate options to maximize value-added results
- Provide leadership to others and serve as a technical subject expert and resource
139
Quality & Continuous Improvement Manager Resume Examples & Samples
- Bachelor’s Degree with minimum 3-5 years of work experience in progressively more responsible position
- No degree: 5-8 years minimum experience in Quality Management, Engineering Management, Production Management, and/or Project Management in a manufacturing environment (preferred)
- Must be a certified Six Sigma Green Belt or attain certification through GPI as part of selection for this position within 2 years
- Demonstrated ability to prioritize, plan, track, execute and document multiple projects simultaneously
- Demonstrated ability to conceptualize, develop, and implement document control systems
- Demonstrated proficiency in Microsoft Office or similar word processing, SAP, MINITAB, SHAREPOINT, spreadsheet and communications software
- Demonstrated proficiency in Statistical Process Control (SPC) and ability to analyze data to make calculated corrections to reduce waste, increase productivity, and increase quality performance
- The candidate must demonstrate good verbal and written communication skills
- The candidate must exhibit ability and a desire to make reasoned decisions on actions to be taken, based upon his/her knowledge and experience, with less than complete information on the current situation
- The candidate must take a strong position on well reasoned convictions, be uncompromising in the quest for quality of output whether it is a product, a service or an activity and above all act at all times in accordance with corporate principles
- The candidate must be action oriented and rise to meet challenges quickly, sometimes with a minimum of planning
140
Continuous Improvement Manager Resume Examples & Samples
- Formulate projects and objectives based on the needs of the operating group
- Prepare project plans and schedules, including requirements, tasks, work assignments, resources, and the inclusion of project milestones and review points and reporting thereof
- Select staff for the project team, as indicated by project skills requirements
- Coordinate the project staff during project performance and participate directly in project performance as required
- Incorporate Lean Six Sigma principles to gain efficiencies and provide assistance to project staff based on those principles
- Report to senior management on project progress, problems, and the need for changes
- Ensure that all work and documentation meet the standards of the department and the project
- Fulfill project reporting requirements
- Assign personnel to various projects and direct activities to gain desired results
- To perform this job successfully, an individual must be able to perform each essential duty satisfactorily
- Master s Degree (MBA) or eight years related experience and/or training or equivalent combination of education and experience
- Lean Six Sigma Black Belt required
141
Continuous Improvement Manager Resume Examples & Samples
- Follow Akzonobel HSE Responsibility Liability Statement including policy, rules, and standard. Comply with regulation requirement
- Organize and work out safety production rules, procedure and emergency response instruction related with own department
- Organize and participate safety production education and training, recording related activities; ensure employees be familiar with relevant procedures and work instructions. have the enough safety production knowledge and skill to work with and cope with emergency situation
- Supervise and enforce the action on main hazardous source applications
- Organize and participate emergency response drill
- Inspect the status of safety production related issue, find hazardous situation and take action to eliminate the risk
- Stop and correct break rules command, work at risk, work against procedure; report incident, near miss and at risk situation to safety personal or site director timely. Comply with Akzonobel life save rules and golden principle
- Take action on site improvement plan and finish the actions on time
- Bachelor degree (degree related to technical, business or economics fields most applicable). If higher vocational training then longer work experience is required
142
Continuous Improvement Manager Resume Examples & Samples
- Identify and facilitate process improvement projects, training/ workshops to drive cultural change
- Conduct root cause analysis to determine metrics, troubleshoot manufacturing/ business and assembly issues, material flow, project plans, production capacity, facility design and create process documentation
- Carry out advanced data collection and analysis for process mapping, develop budgets and cost analysis to determine project feasibility
- Develop and conduct compliance audits, program evaluations and reviews to drive results with the fortitude to ensure change is permanent
- Lead assigned projects and identify self-initiated projects based on opportunities discovered during audits
- Advanced knowledge of Microsoft word, excel and ERP applications
- Ability to read Schematics
- Training in CAD preferred
- Minimum of 4 years’ experience
- Exceptional communication skills, both verbal and written, problem solving and analytical skills
- Training in Lean manufacturing principles and Kaizen facilitation
- Strong leadership skills, experience working in a unionized environment, ability to learn and apply new concepts and overcome obstacles with change
- Previous exposure to a high volume job shop environment
- Ability to work with and influence others in a fast paced environment, ability to work shifts as required
- Bachelor's degree from an accredited University
143
Continuous Improvement Manager Resume Examples & Samples
- Maintain a culture of excellence in execution, continuous improvement, and communication within medical polymer production work areas. Take an outside looking in perspective and define quality from the customers’ perspective who buy our medical polymers
- Provide leadership regarding project prioritization, process validations, and continuous improvement activities. Act as a SME and leverage understanding of Industry leading best practices and connect with key stakeholders in order to gain support of continuous improvement initiatives
- Manage and drive improvement quality standards, resolve technical related issues and improve manufacturing procedures, processes, monitoring and measurement activities
- Continuously review and drive operation improvements with regards to production set up and layout of equipment and general work areas
- Continue to develop, implement, train and monitor effectiveness of process systems and procedures to ensure compliance to GMP and all other applicable agency regulations
- Execution of validation protocols as instructed for cleaning processes, equipment qualification and processes/products. Coordinate and monitor inspection activities
- Drive compliant behavior within the Quality Management System for Medical polymer products including audit support, evaluation of non-conformities, support of investigations, and execution of Corrective Actions / Preventive Actions (CAPA). End-to-end ownership across the entire CAPA cycle from non-compliance to investigations to Corrective/Preventative
- Employ strong process disciplines by creating repeatable processes within the production areas
- Ensure adequacy and compliance of dedicated, environmentally, climate controlled areas that manufacture medical polymers; ensure clean work areas that are free of contaminants (includes airborne) and spills. Oversee safety, cleanliness and organization of department
- Bachelor’s degree (Operations Management, Engineering or other technical discipline)
- Minimum of 5-10 years of experience in manufacturing or related operations is required with of direct supervision of employees required preferably in a medical device environment
- Experience within a Good Manufacturing Practices and/or ISO regulated manufacturing environment is required; ISO9001 or as an engineer in a medical device or pharmaceutical industry preferred. Working knowledge of Quality Systems Regulation (QSR) requirements and associated risk assessment for medical devices preferred
- Experience with environmentally, and climate controlled environment is preferred
- Experience with CAPA process and implementation
- Demonstrated strong project management skills is preferred. The ability to lead and facilitate project improvements is preferred
- Advanced understanding and working knowledge of Six Sigma/Process Excellence Tools is required. Six Sigma Training and/or Certification are preferred
144
Continuous Improvement Manager Resume Examples & Samples
- Lead lean manufacturing initiatives to achieve operational excellence and enhance the overall effectiveness of manufacturing operations
- Drive the change management necessary to implement effective lean manufacturing operations
- Accurately determines which project management methodologies and process improvement strategies are best suited to achieve objectives
- Effectively uses those tools to increase the likelihood of success
- Support continuous improvement activity throughout the organization
- Tracks and manages post-project implementation performance monitoring: including control plan audits, savings verifications, and reporting
- Coaching and training plant/operations managers and coworkers on principles of lean manufacturing and problem-solving
- Maintain a high energy level and positive attitude to support continuous improvement
- Follow-up with plant/operations managers to ensure successful implementation
- Provide leadership to others through example and sharing of knowledge/skill
- Bachelor’s Degree in a engineering, supply chain, operations or related field
- 5 - 10 years of working knowledge and practical experience in manufacturing environment
- Working knowledge of and ability to apply lean and six-sigma principals and other similar problem solving tools
145
Continuous Improvement Manager Resume Examples & Samples
- Bachelor’s degree required from an accredited institution
- Minimum 1 year of lean manufacturing experience
- Must be authorized to work in the United States without company sponsorship now or in the future
- Master’s degree from an accredited institution
- Bachelor's Degree in Engineering from an accredited institution
146
Continuous Improvement Manager Resume Examples & Samples
- Drive cost saving projects from start to finish
- Develop metrics and set up tool to measure operational performance as part of the overall launch program
- Review and analyze customer defect data and develop corresponding action plans to reduce defects
- Develop and execute action plans that increase quality, inventory accuracy and service
- Use lean techniques to root cause process deviations and develop countermeasures for these deviations
- Work closely with support staff to secure resources for projects and provide support for other initiatives as needed
- Travel to sites to evaluate and ensure compliance of improvement initiatives
- A completed Bachelor’s Degree in Engineering, Mathematics, Operations/Supply Chain, Computer Science, or other technical field from an accredited university
- 3+ years Operations Management experience, including continuous improvement experience
- Background in manufacturing, production or distribution environment
- Knowledge of Six Sigma tools and Lean techniques required
- Proficient with MS Excel and SQL
- Willingness to travel as necessary, up to 40%
- MBA / Master's Degree in Engineering or Supply Chain
- Lean Six Sigma Black Belt
- Ideally have a Logistics and/or Retail background
147
Continuous Improvement Manager Resume Examples & Samples
- The CI Manager will be responsible for leading the CI improvement process at aggregate operations. He/she will work with local managers to identify production, QC and commercial process best practices and then bring awareness of these best practices to other operations
- The CI Manager will become proficient in the technical aspects of production, QC and sales processes, as well as the general management aspects of the business. He/she will help to identify new product opportunities, develop benchmarking studies, coordinate peer based site reviews and facilitate improvement discussions with the Plant and Area Management. He/she will follow up on improvement opportunities and provide assistance to local management to make tangible progress in realizing improvement goals
- The Continuous Improvement Managers will become a conduit for transferring best practices across the organization, and deliver training modules in conjunction with the HeidelbergCement Aggregate Academy, including best practice calls
- In addition, the CI Manager will have North American (NAM) functional responsibility to lead improvements of a specialist topic. This high profile position will require regular travel within the Region/NAM and a commitment to work with multiple levels of management
- Bachelor’s degree in Mining Engineering or related field, or at least 8 years of experience in the aggregate or allied industry; or an equivalent combination of both, plus at least 4 years in a direct mine/quarry management role
- Highly organized with excellent communication and project management skills, and the strong desire to work alongside and support our line management with all aspects of Continuous Improvement
- Self-motivated and high energy with the ability to plan and lead multiple projects that require interfaces with multiple stakeholders and differing levels of management
- Ability to coach, motivate and train peers without direct lines of authority
- Ability to understand the operational, technical, commercial and financial aspects of the business and how they relate to each other, including product costing and investment evaluations
- Experience in optimizing processes in sand and gravel, and quarrying operations. Ability to diagnose and optimize production steps for blasting, loading & hauling, crushing & screening, lead-out, maintenance, extraction and site management. Ability to relate above processes to site geology and commercial markets
- Ability to apply technical recommendations in a pragmatic, hand on way in the actual operating environment
- Comfort leading or applying in change management processes
- Highly driven with determination to lead our North American operations to a best in class performance
- Ability to think outside the box and to identify best practices and transfer this knowledge across the organization
- Knowledge of Aggflow and AggQC software and proficiency in Microsoft Office
- Willingness to travel within Western Canada and Washington State
148
Continuous Improvement Manager Resume Examples & Samples
- Continue our implementation and champion lean-manufacturing techniques: Including visual management, practical problem solving, process control, abnormality management and Standard Work (including time observation)
- Work with production management to support daily operations, as required, attend to issues in the day to day processes to assure that the operation goes on, problems are contained, but also solved once and for all
- Operational Start up management for major capital projects, partnering with project engineers and production teams
- Analyse results to identify then deliver on improvement opportunities
- Ensure employees have the information required to make decisions
- Lead and deliver daily operational improvement
- Interface between production and Innovation teams for New Product Development to create new, efficient, manufacturing processes
- Provide back-up coverage to production leaders
- Ability to influence and inspire
- Evidence of practical problem solving
- A Bachelor Degree in Engineering (Mechanical, Industrial, or related discipline)
- Project Management experience to include: planning, scheduling, status reports, and activities in a speaking/group environment
- Working knowledge and appreciation of lean manufacturing and continuous improvement
- Ability to deal with multiple priorities and opportunities, in a fast paced environment
- 2 years Continuous Improvement experience or a solid Experience working with Microsoft Office Software (Word, Excel, and PowerPoint)
149
Area Continuous Improvement Manager Resume Examples & Samples
- Must be able to work with abstract and complex concepts as well as communicate them in an easy to understand way
- Advanced communication skills to work in a team environment and lead through influence
- Administer budget and allocate spending
- Administer flow and distribution of supplies and materials
- Extensive coaching and training of peers
- The position will typically be responsible for lean implementation
- Implementation planning, coaching and facilitation skills
- Will work with broad ranges of employees ranging in level from frontline employees to senior leadership
150
Continuous Improvement Manager Resume Examples & Samples
- Facilitate/Coordinate/Participate on departmental team projects aimed at generating Lean/CI techniques, cost reductions, and process performance improvements
- Conduct Kaizen events in pilot areas and other specific plant functions
- Maintain Lean/CI implementation schedules for assigned projects, progress updates as required, and most importantly, provide documentation that demonstrates the direct link between Lean/CI implementation and direct process improvement and Plant Operations
- Provide Lean/CI training and coaching at all levels of the Plant
- Assists Business Unit Managers and individual Lean/Continuous Improvement Initiatives
- Participate on and lead teams aimed at the resolution of quality issues and concerns
- Support production control, material control, material planning departments in improvement projects relating to scheduling inventory management and raw material flow and tracking
- Coordinate prototype and pilot runs to address design and process feasibility concerns from a departmental aspect
- Interface with plant engineering on projects addressing staffing, manpower, time and capacity issues
- Generate, provide and participate in department specific training issues
- Conduct weekly cost saving meeting designed to reduce costs
- Conduct weekly “attack scrap” meetings designed to identify and reduce scrap
- Assist in monitoring department equipment (OEE) and interface with Maintenance department to identify maintenance, repair, PM needs and TPM
- Manages Lean Technician job tasks, attendance tracking and coaching
- Participates in training as required
- Ensures Housekeeping and Health & Safety Standard are maintained
- Complies with policies and procedures pertaining to facility or divisional adopted standards such as TS 16949 and ISO 14001
- Utilizes the concepts of continuous improvement and cost reduction in the execution of the job function
- Acceptable attendance
- Four-year degree from an accredited college or university in mechanical engineering, industrial engineering or related field
- Minimum three years’ experience in a lean manufacturing environment with a record of proven accomplishments
- Candidate must have experience in identifying areas of improvement, planning for and leading Kaizen events
- Experience in SPC, SMED, design of experiments, KANBAN, and 6-Sigma implementation is a plus
- Experience in a high volume automotive manufacturing environment
- Experience working with all levels of management
- Interpersonal Skills – Must have strong oral and written communication skills
- Problem solving – Must have strong analytical skills. Must have strong self-initiation and decision making skills
- Physical / Mental / Visual Abilities – duties of the job require periods of standing, sitting, use of hands and fingers. No special physical demands are required to perform the work
- Proficient in computer skills (MS office, AutoCAD, etc)
151
Continuous Improvement Manager Resume Examples & Samples
- Collaborate with Site Leadership to develop & communicate site vision ensuring continuous improvement projects and project funnels are in place to support that vision
- Ownership of site Lean Sigma communications including vision, project completions, employee suggestions process, reward & recognition, etc
- Ownership of communication of Lean Sigma program to customers including project examples and results that benefit our customers
- Lead efforts to create a sustainable continuous improvement culture at the site
- Propagate the use of best practices at site and support the implementation of best practices at other sites. Active participation in Best Practice Sharing across site and region
- Ensure site alignment to Regional & Corporate Strategy
- Lead the training/mentoring of Lean Sigma methodologies for site continuous improvement efforts
152
Continuous Improvement Manager Resume Examples & Samples
- Coach and role model the use and application of the Mars Quality Principle and the Mars Global Quality Standards
- Coach and role model the application of Mars safety standards in order to safeguard our associates and the assets we use
- Responsible in part for identification, delivery and tracking of the Site ‘Do it Best’ targets. This includes the provision of quality analytics to aid decision making
- Responsible in part for identifying and assessing business continuity risk associated with all Site operations
- Responsible to complete the submissions of all continuous improvement small minor projects liaising with key cross functional stakeholders to gain alignment on the proposal
- Responsible for partnering with other Business functions to develop and continuously improve the overall supply chain productivity and achieve customer leadership
- Responsible for deployment of key business process and toolkits on site that improve productivity and increase standardization
- Support marketing and R&D in new product introduction and innovation management
- Support the Plant Manager in co-creating the site master plan
- Support the Plant Manager in the development and delivery of the Site Operating Plan
- Support the Site Teams in the identification and delivery of the Do it Best MCC Improvement Plan
- Responsible for development and deployment of lean strategy within Manufacturing on Site
- Lead the site in review of global benchmarking data to improve performance. Responsible for the deployment of LEAN and TPM across the site
- Responsible for inspiring and engaging Site Manufacturing Associates in the Site CI Strategy
- Support the Food Safety Management team to drive continuous improvement down the relevant site based HACCP Teams
- Lead, coach, develop and mentor the Supply CI team. Ensure succession planning, engagement and the creation of a high value adding team
- Liaise with CI / LEAN / TPM in regional and global programs, so that information to the business remains contemporary and relevant, and peer contacts, relationships and networks are maintained
- Investigate, respond and ensure implementation of corrective actions for all major customer complaint investigations (Domestic & Affiliate markets)
- Provide regular SOG updates on Supply CI / Usage performance (lead and lag indicators), challenges, opportunities and progress on standards implementation and CAPA’s
- Define, develop and recommend a Bathurst Supply CI Strategy in consultation with the Bathurst Plant Manager
- Ensure that the appropriate CI systems are implemented, available & operating effectively throughout the Bathurst site
- Be the Supply CI / LEAN / TPM advocate and proactively challenge new and existing practices, products and processes to ensure compliance and continued improvement
- Responsible for the implementation and delivery of the Bathurst CI / LEAN / TPM Supply strategy through regular internal auditing, identification of gaps/ opportunities and the implementation of close out actions
- Tertiary Qualification
- Experience in Lean principles and tools and their application
- Previous experience managing multi-functional teams
- Experience across Supply manufacturing
- Excellent organisational and project management skills
- Ability to review processes, recommend improvements, build buy in and execute with excellence
153
Continuous Improvement Manager Resume Examples & Samples
- Leads and manages high level, cross-functional teams through improvement events using a knowledge transfer model
- Ensures implementation runs smoothly and that gains are sustained through Lean management system coaching
- Advises leadership in regards to annual strategy deployment cycle including the development and deployment of A3s and the check/adjust process
- Coaches management through the identification of value streams, creates, and delivers the vision for pull-based workflows through those value streams
- Serves as general subject matter expert for projects & project teams. Supports, guides, and coaches the process owners in TPS elements
- Teaches Lean Six Sigma concepts for every cycle of the Leadership development including the CI practitioner certification program
- Ensures existing processes maintain a high level of performance while continuously reviewing and refine those processes to make additional improvements
- Co-leads and coaches the implementation of Hoshin Kanri at the organizational level with linkage through value stream
- Co-leads the development of the Lean training program and curriculum development for the entire organization as part of the leadership development
154
Senior Continuous Improvement Manager Resume Examples & Samples
- Lead effort to implement best practices, ensuring adherence to the principles of lean manufacturing
- Assist and mentor direct reports & plant management and CI teams with planning and facilitation of strategic plans, kaizen workshops, and other lean activities
- Follow-up with operations ensuring successful implementation of Future State plans
- Implement training/On-Boarding programs in conjunction with HR Leadership
- Analyzes, develops and recommends design approaches necessary to meet production requirements for new or improved products and/or processes
- Determine from part drawings and related engineering data the operation necessary for the fabrication and assembly of product
- Create routings for the purpose of managing the flow of material throughout the manufacturing process & process mapping
- Analyze existing operating methods and initiate and develop new method to improve economy and quality
- Highly developed problem solving and project management skills
- Demonstrated facilitation and coaching skills
- Demonstrated capability to learn product lines and manufacturing processes
- Demonstrated ability to use information technology including Microsoft Excel, Power Point, and Word
- Working knowledge of AutoCad or InventorPro software
- Negotiation and selling skills to support change management
- Bachelor’s degree in Business, Operations Management, Industrial Engineering, or other comparable engineering degree
- 5 years of successful experience with implementing lean manufacturing
- Six Sigma Black Belt certification preferred
155
Quality & Continuous Improvement Manager Resume Examples & Samples
- Perform initial quality survey and ongoing supplier quality assessments (QSA) at suppliers and quarterly business reviews at suppliers
- Conduct production part approvals, validations and first article inspections of Supplied parts
- Work with ANZ engineering team to perform DFMEA’s and pFMEA’s to ensure clear specifications are communicated to suppliers
- Work with supply chain to identify cost out opportunities through supplier resourcing or production improvements at suppliers
- Analyze warranty returns and perform failure analysis. Use this information to initiate corrective actions, as well as cost recovery,
- Ensure ISO9001 certification is maintained and assist with ISO14001 and MESH deployment
- To annually schedule and perform internal audits on all processes and functions with Eaton ANZ
- To train, coach and mentor internal auditors
- Drive continuous improvement efforts through the use of the Eaton Lean System, Eaton Quality System and ISO9001 corrective and preventative action policies to drive down our cost of non-conformance
- Implementation and development of Continuous improvement programs
- Bachelor’ degree in Science or Engineering (Electrical preferred)
- Experience with process continuous improvement tools such as Lean and Six Sigma
- Experience of internal & external quality auditing
- Knowledge of ISO9001 and implementation
- Ability to analyse and interpret drawings and validate components against these
- Good communication skills, ability to clearly communicate to employees, suppliers & customers
- Proficient knowledge of Excel, Word, Powerpoint. AutoCad and Visio knowledge advantageous
156
Continuous Improvement Manager Resume Examples & Samples
- Network within the AkzoNobel CI community and share insights, problems and opportunities to promote improved performance and problem-solving across the company as well as encourage others to do the same
- Manage multiple departments of the site in different maturity of CI journey and develop an understanding of strategic business needs in order to anticipate the requests for support and leverage learning between SMU and BA Advisors
- Deliver effective coaching and mentoring service to site leadership team and personnel, facilitate CI workshops and trainings as requested
- Develop 5S standards and lead to promote 5S in production, warehousing, office and utility areas with sustainable approach
- Not less than ten years industry experience, not less than 5 years manager experience
- Lean & six sigma Black belt certification
- System tools of CI
- Be good at operation system
157
Quality & Continuous Improvement Manager Resume Examples & Samples
- Indonesian citizen
- At least 2 years of experience in hotel operation, or an equivalent combination of education
- Must have prior managerial experience in managing a large team
- Good understanding of English
- Strong inter-personal skills with excellent ability to manage quality improvement program
- Excellent communication skills, both written and spoken
- Detailed and meticulous, with expectation towards quality delivery
158
Continuous Improvement Manager Resume Examples & Samples
- Leads multiple continuous improvement projects to deliver breakthrough improvement in key processes using Lean, Six Sigma and other process improvement methodologies
- Leads targeted projects and cross-functional project teams to ensure goals, timelines, planned benefits and completion dates are delivered
- Develops multiple Green Belts (part time Six Sigma Project Leaders) in targeted functional areas. Provides one-on-one project review & mentoring in application of Lean and Six Sigma methodology and tools
- Identifies and implements continuous improvement best practices. Leverages tools and techniques of continuous improvement that rely on statistical, data driven decision making
- Drives culture change to instill focus on fact-based management practices, the use of Lean/Six Sigma and other problem solving methodologies
- Continuously improves company’s organizational capabilities to achieve process quality as part of project execution, including an awareness of the need to “do it right the first time”
- Recognizes and addresses organizational barriers to ensure future success of ongoing improvement programs. Supports continuous improvement programs, establishing and maintaining high quality assurance standards, procedures and controls
- Leads efforts to implement process control and management (process mapping, documentation, metrics, monitoring and management systems and process ownership). Documents procedures to implement process changes
- Ensures senior leaders are apprised of the status of all Projects and Programs
- Works with Business Leadership to identify and prioritize process improvement opportunities
- Bachelor's Degree with at least seven years’ experience in continuous improvement and quality
- Must be Lean/Six Sigma Certified Black Belt and have experience in planning and executing Lean and Six Sigma projects (DMAIC)
- At least four years’ experience as a Black Belt leading cross-functional teams managing multiple projects under time and cost savings constraints
- Ability to collect, analyze and interpret both qualitative and quantitative data. Demonstrate excellent analytical, root cause analysis, problem solving, and decision-making skills
- Process improvement tools and methodologies such as process mapping, value added analysis, data analysis and root cause analysis
- Enjoy working in a collaborative team environment
- Excellent verbal and written communication/presentation skills
- Ability to communicate and work at all levels of the organization
- Experience with e-commerce/IT enterprise systems, call center, and distribution/fulfillment
- Proactive and self-directed
- Exhibits strong leadership skills and desires to take higher responsibility positions in the future
159
Continuous Improvement Manager Resume Examples & Samples
- Must be familiar with plant safety rules and guidelines
- Be a “leader of change”. Must have a positive attitude, work well with all levels of the organization, and have initiative in identify areas of opportunity and improve company operations
- Will be responsible for managing and leading continuous improvement projects
- Work closely with Operations Management, Plant Manager, and Human Resources to establish a team culture at the lines
- Conduct root cause analysis to determine metrics, troubleshoot manufacturing/ business challenges and create and maintain process documentation
- Implement cost savings improvement projects
- Manage a portfolio of lean projects directed at reducing waste and improving quality and cost
- Implement corporate/plant CI systems
- Train and lead cross-functional continuous improvement teams; focusing on measurable quality, service and cost improvements
- Implements a formal lean / six sigma program that focuses on reducing process and product variation. Implements such tools as: SPC, Process Capability, Pareto analysis, Fishbone, SMED, DOE, 5S, KPI, SMED, VSM and Kaizen events
- Assist in setting annual operational OEE targets and help drive improvements to achieve attainment and adherence goals
- Perform other duties and assume additional responsibilities as assigned
- Exceptional communication skills, both verbal and written, and ability to work in a matrix organization
- Demonstrated ability to lead kaizen improvement events
- Demonstrated ability to lead cross-functional teams to implement cost savings programs across plant
- Strong analytical skills using tools such as statistics, downtime tracking, mechanical history, project planning to identify opportunity areas
- Creative in problem solving and innovative approaches to resolve complex problems
- Proficiency in Minitab, CAD and Visio, Microsoft Office skills such as PowerPoint, Project, Excel, Word,
- Ability to quickly come up to speed on complex production processes and work with others identifies opportunity areas via data
- Ability to teach/coach Lean /6 Sigma concepts throughout the plant
- BS in Engineering; Master’s degree preferred
- Past experience in leading kaizen workshops in the areas of 5S, standard work, visual management, daily management, SMED and OEE gap closure
- 6 Sigma certification preferred
- Maintenance/manufacturing/engineering/QA/QS experience preferred
- Has worked in a lean manufacturing environment
- Hands on style and solid communication ability
- Ability to work with minimal direct supervision, in a fast-paced, dynamic environment
160
Continuous Improvement Manager Resume Examples & Samples
- Serve as not only coach and mentor, but as a leader in project delivery and accountability, trainer and developer of material. It will be important to be comfortable with sharing best practices across categories. Responsible for training not only those within the confines of the project, but leadership teams, and others across multiple business unit
- Should be comfortable with advanced statistical topics from understanding tolerancing to quantitative research that will help them take the lead on understanding and assessing how the customer requirements were defined. Should be willing to learn and use conjoint analysis techniques, how to apply the Kano module and be ready to help the project team prepare necessary inputs for the QFD
- As problems arise on the project team they should be a go to person to mentor project team members on appropriate tools and techniques to solve variation issues from components of variation studies to designs of experiments
- Mentor, coach and train black belts within the product categories following through on the impact of training based on the evidence of project completion
- Create deployment strategies and work with the leadership teams to define competency needed and the skill level of the categories roles to meet basic and advanced quality skills
- In conjunction with manufacturing quality and engineering personnel, develop new tests in the manufacturing environment to reflect experimental results or explore theoretical improvement options
161
Continuous Improvement Manager Resume Examples & Samples
- Trains Leadership, Frontline Leaders, Engineers, and Operators in use of Lean Tools
- Coordinates Lean events with Frontline Leaders, Engineers, Staff, and operators, with a focus on improving knowledge and Continuous Improvement culture leading to continually improving High 5 metric performance
- Leveraging the Eaton CIF process is an essential element of improving CI culture. CIF includes process standardization, visual controls, leader standard work, manning strategy, process checks, daily accountability, and GEMBA walks
- Responsible for coordinating cost savings process, and capturing and submitting saving related to labor/productivity. This includes conducting deck building events leveraging division and engineering resources as appropriate
- Plans and coordinates Kaizen Events for the improvement of processes, while ensuring safety requirements are adhered to
- Champions Lean assessments within the plant, coordinating Champions and owners for each Lean tool. Actively participate in assessments outside the plant
- Coordinates OpA activities, including self assessments in the time frame required and ensures identified opportunities are prioritized and worked on
- Works with other Eaton facilities to benchmark or be benchmarked in areas of lean manufacturing, 5S+, and other continuous improvement activities
- Provides assistance to production personnel in implementing improvement ideas and other resources they may need
- Follows all environmental health and safety procedures and practices to assure a safe work environment. Identifies and corrects unsafe conditions or practices to assure a safe work environment for all employees
- Record any measurable statistics which your position impacts such as production expenses, maintenance expenses, sales volumes, payroll costs, capital expenditures, research budgets, cost of purchases, value of inventories controlled, employees supervised (direct and indirect)
- Implements Lean tools to provide production support in the areas of increased production, scrap reduction, cost reduction, 5S improvements, and assessment preparation
- Minimum 3 years of Manufacturing Experience
- Must be legally authorized to work in the US without company sponsorship
- No relocation benefit is being offered for this position; candidates must reside within 50 miles of the facility in order to remain in consideration
- 5 years of Manufacturing Experience
- Prior experience leading CI/Lean initiatives
- Greenbelt or Black Belt Certification
- Experience with Value Stream Mapping
- Prior Leadership experience
- Strong interpersonal, communication and leadership skills are required
- Demonstrated working knowledge in Statistical Process Control (SPC), Design of Experiments (DOE), Lean Manufacturing, Process FMEAs, exposure to APQP requirements is preferred
- Requires good organizational skills
- Six Sigma Certification (green/Black belt) preferred or be able to be certified within 12 months in role
- Must be self-motivated and require little supervision for the successful completion of projects
- Must have excellent facilitation skills, project management skills, and drive for results
- Must be willing to provide any required production support, work off-shifts and travel periodically
- Frequent communication with all levels and support of cross-functional teams
162
Quality & Continuous Improvement Manager Resume Examples & Samples
- University Engineering Degree (Bachelor of Applied Science) or degree in other related engineering discipline
- Minimum 5 years of quality engineering, engineering or manufacturing in manufacturing environments, with applied knowledge of Lean & Six Sigma methodologies
- Demonstrated leadership skills and managing teams
- Exceptional oral and written communication skills required for procedure writing and communication when dealing with all levels of the organization
- Rockwell Automation will only employ those who are legally authorized to work in Canada for this position
- Certification in LEAN, Six SIGMA Black Belt, CQM, AQE is desired
- Preference given to candidates with a PEO P.Eng. license, and designations in American Society for Quality (ASQ) and/or Certified Quality Engineer (CQE)
- Candidates with working experience in Engineered-to-Order (ETO) Electrical/Electronics systems manufacturing; working in environments with formal quality management (ISO9001) & production systems preferred
163
Continuous Improvement Manager Resume Examples & Samples
- Driving sustainable continuous improvement/performance improvement across manufacturing
- Appropriate implementation of CI, Lean and Good Manufacturing Practice techniques
- Reducing wastage through the application of process mapping and waste elimination techniques based on robust data/information
- Implementing and maintaining a robust performance measurement system to measure performance
- Create and maintain a framework that the site can use to drive operational improvements in conjunction with Group functions. Create and drive a pipeline of Improvement Projects and Opportunities
- Working within a network of improvement champions to operate in a similar fashion, self support and share best practice
- Set up and maintain a governance system for monitoring progress of continuous improvement projects. Reporting programme delivery and KPI’s
- Measuring the financial and other benefits achieved. Drive use of the Manufacturing Information Systems for performance tracking
- Maintain knowledge and seek best practice understanding from other sites and other external sources
- Identify opportunities requiring capital investment and work with the site teams to create a business case
- Create a framework for robust NPD, process and product development
- Help prioritise and coordinate the capital plans across the sites
- Experienced CI professional within a Manufacturing/Supply Chain environment
- Proven experience in the implementation of Continuous Improvement/Lean techniques and team development across all Supply Chain areas
- Black Belt in a Lean Manufacturing aspect – ie Lean 6 Sigma
- Technical expert with ability to facilitate, coach and mentor at all levels of the organisation in CI/Lean Manufacturing techniques including TPM, autonomous maintenance, problem solving, process mapping (VSM), Lean development ( DMAIC), Process and Product improvement via process capability (Cpk) development, statistical process improvement (to 6 Sigma std), Facilitator of EEM processes, RCA/FMEA/TPM, SPC, 5Y’s, SIC, AM, APQP……….)
- Must be credible to Site Director/customer peer group
- Facilitation/Influencing skills essential
- Ability to analyse, and interpret data including financial information, process and product information
- Computer literate using CI tools ie Word, Excel, Planning (Projects), Powerpoint, MiniTab and business systems
- Some flexibility to work across a number of sites\locations
- High volume FMCG and continuous process experience, ideally food. Likely to have a manufacturing/operational/engineering background
- Ability to work under pressure on multiple fronts
164
Continuous Improvement Manager Resume Examples & Samples
- Bachelor’s degree: Industrial, Electrical, Chemical, Mechanical Engineering or Finance
- Minimum of 5 years of proven Continuous Improvement experience in a Manufacturing environment
- Project management, Data analysis and continuous improvement methodologies -Training or exposure to statistical analysis
- Solid interpersonal skills – communication, influencing, selling ideas
- Must be a self-starter and able to work individually or in a team
- Demonstrated success in multiple projects and realized expense savings/process improvements from Six Sigma projects
- Knowledge/understanding of Continuous Improvement, Six Sigma or Lean methodology and tools
- Proficient in Microsoft Office Excel, Word and PowerPoint
- Able to travel independently and in accordance with Company guidelines
- Food / Feed manufacturing -Six Sigma / Lean Certification Black Belt or Master Black Belt highly desired
- Project Management skills set -Minitab Knowledge -Visio Knowledge
165
Continuous Improvement Manager Resume Examples & Samples
- Plans, designs and modifies current and future designs for facility and equipment layouts to ensure the efficiency, safety, and proper working of all manufacturing systems
- Researches ways to reduce production costs, develops production goals, and creates schedules and plans for individual tasks within the Continuous Improvement Manager scope
- Monitors process changes after implementation and offers additional recommendations for improvement as required
- Provides management with operations and engineering information by collecting, analyzing, and summarizing data and trends
- Identifies priorities in the Operational department such as efficiency, cost savings, energy conservation, and safety and estimates relevance, time, and cost on all Operational objectives in order to create processes that will take these priorities into account
- Provides maintenance, support, and troubleshooting for any problems which may arise within the Continuous Improvement scope
- Studies operating targets, modes of operation, and unit limitations in order to anticipate any operational problems which may arise
- Follows and enforces standards in compliance with legal regulations to maintain a safe and healthy work environment for all employees
- Completes any ad hoc tasks as assigned by management
166
Continuous Improvement Manager Resume Examples & Samples
- Lead Focused Improvement by driving Margin Enhancement (ME) initiatives and elimination of losses / defects.Work collaboratively with all departments and divisions to identify ME and cost savings opportunities
- Develop mature project management infrastructure
- Develop plan for broad training to support CI mindsets
- Provide rapid response when and where needed
- Train and drive Technical Mastery by delivering CI Methodology training and ensure the organization applies CI skills and tools to solve problems in a timely manner
- Lead and Influence the Plant Leadership Team (PLT) in the use of CI to deliver Performance; ensure the PLT shows visible support of CI and rewards success and guide the PLT on staffing for performance
- Lead Performance Management by developing and training Plant Resources on a cadence of accountability and set goals.Lead the development and implementation of performance KPIs such as OEE, Uptime, Throughput and Yield, loss identification and elimination, and ensure lag and lead measures are in full compliance
- Champions continuous improvement teams across all sites
- Plays key role in capital project conceptualization, development and implementation.Plant Point-of-Contact for Corporate Improvement and Capital Projects by knowing the technical details of the new projects to provide Plant perspective and requirements to the Project Team.Examples include, scope requirements, testing required, training requirements, start-up planning and execution
- Deliver Project Start-ups and the transition to ongoing Operations by supporting Engineering/Project Team in the Testing and Commissioning phases (equipment & materials focus).Own and manage the Qualification phase (people focus) then transition the project to on-going operations in the Verification phase (methods & sustain focus)
- This job description reflects management’s assignment of essential functions; it does not prescribe or restrict the tasks that may be assigned
- 5 years experience preferred
- Track record of successfully using continuous improvement methodologies/tools such as Lean, Six Sigma, TPM
- Must be a proactive team player
- Will have continuous contact with employees at all levels of the organization as well as external customers in the business and technical field
- Must be confident and well-spoken to be able to present technical concepts and ideas
- Must be able to write and interpret complex documents in a clear and concise manner
- Must exhibit a willingness to operate with a great degree of flexibility resulting from ever changing market conditions
- Build alignment
167
Senior Quality & Continuous Improvement Manager Resume Examples & Samples
- Provide leadership in all aspects of quality assurance and continuous improvement to include but not limited to quality compliance requirements, quality control, and quality engineering problem solving through utilization of comprehensive root-cause analysis techniques
- Support VP of Quality in the management of Quality Assurance and Continuous Improvement department
- Work closely with all functional leaders and extended leadership team to support the reduction of each functions cost of quality loses
- Analyze production and service limitations and standards, and recommend revisions of specifications when indicated
- Formulate or help formulate Quality Assurance and continuous improvement policies, plans and procedures
- Assist Marketing in quality related technical discussions with customers
- Ensure proper analysis techniques are used in development of new and revised designs
- Work with Program Managers to create and maintain project schedules directly related to quality requirements
- Support the identification of new technologies to enhance products and reduce costs
- Maintain department budget that is aligned with strategic business goals
- Support life cycle phase reviews to achieve program timelines
- Oversee staffing, training, supervision and workload distribution of engineers and or technicians
- Interpret and enforce policy, conduct performance evaluations, and manage employee relations while meeting engineering schedules, customer needs and quality standards in a timely fashion
- Monitor performance and work with other members of the Quality and Continuous Improvement Department to create sustainable solutions that meet customer expectations
- Ensure proper root-cause corrective actions are applied to identify issues
- Support or lead employee training efforts when deficiencies are identified during root cause problem solving
- Provide technical input on quality and contractual related issues to internal and external customers
- Interface with quality regulating organizations
- Assist with the implementation of quality standards and regulatory requirements
- Maintain audit schedules and ensure audits are completed in a timely manner
- Administer direct supervisory responsibilities for personnel including selection, hiring, training, performance evaluations, promotional recommendations and schedules
- Oversee Quality and Continuous Improvement Representatives on Integrated Product Teams
- Actively promote and enforce adherence to S|H|E rules and procedures
- Identify and effect change to reduce risks of harm and minimize waste and resources used
- Communicate to employees, visitors and customers that health and safety and a concern for the environment are values for Cobham
- Promote and facilitate incident and near miss reporting
- Experience in DFSS and/or APQP processes
- Aerospace industry experience
- Military or commercial aviation or aircraft modification experience
- Experience in inspection techniques/methods/equipment
- Knowledge of, or ability to operate measuring and gauging equipment
- FAA interface experience
- DCMA interface experience
- ISO 9000 training and experience
- AS9100 training and experience
- NADCAP experience
- ASQ Certified Quality Manager
- Statistical Process Control (SPC) knowledge and experience
- Auditing experience
- Ability to read and interpret technical, contractual and regulatory documents
- Ability to make independent judgments regarding technical issues
- Ability to handle multiple changing priorities in a fast paced environment
- Strong team building and team work capabilities
168
Continuous Improvement Manager Resume Examples & Samples
- Use Six Sigma experience, expertise and understanding of the company’s strategy to influence executive leadership in the selection of Six Sigma projects aligned with strategic goals
- Operate at a cross-functional level, leading and executing Six Sigma, DMAIC, DFSS and/or Lean projects
- Create project plans collaborating with process owners, champions, sponsors and team members focusing on the customer
- Work closely with process owners, project champions, and senior leadership team to provide leadership and direction on the implementation of large change / value improvement projects
- Lead Kaizen events, value stream mapping sessions and activities to track and influence project objectives
- Use Six Sigma tools and techniques, such as control charts, histograms, Pareto charts and root cause analysis to analyze data
- Implement control plans to ensure that gains are sustained on a long-term basis
- Develop and operationalize dashboards and key metrics to regularly track operational performance
- Define specific initiatives aimed at improving services and processes, based on the results of service reviews and process evaluations
- Promote Six Sigma to obtain critical support and resources and ensure that improvement projects are implemented and adequately funded
- Educate business leaders on Six Sigma concepts and how to apply them to their operations and enable organizations to become more self-sufficient and self-sustaining in process improvement endeavors
- Cultivate talent by mentoring, coaching and training team members in Six Sigma concepts and methodology
- Lead, motivate and inspire a Six Sigma vision in an organization newly introduced to the framework and methodology
- Manage and direct the activities of up to two direct reports
- Bachelor’s Degree in Business Administration or related field required / Master’s Degree in Business Administration preferred
- Completed Black Belt Training & Certification required
- 10+ years of experience in leading and managing Six Sigma, DMAIC, DFSS and/or Lean process improvement projects
- Extensive experience in business environments training team members, coaching other personnel and completing other problem solving projects leveraging Black Belt & Lean Manufacturing toolbox
- Demonstrate expertise in driving and producing measurable productivity gains
- Possess advanced quantitative and analytical skills, as well as the ability to understand the big picture and the varied needs of different stakeholders
- Proficient with statistical and process management software, such as Minitab, and flow charting software or process mapping software
169
Continuous Improvement Manager Resume Examples & Samples
- Lead Damco GSC site towards achieving improvement targets, ensuring sustainability of implemented tools, techniques and behaviours in the Damco GSC site
- Drive execution of tactical improvement plans/ideas (TIPs) and realization of benefits
- Coach priority projects identified during OPEX implementation
- Support, train and coach teams on OPEX tools and techniques as needed
- Engage with Damco global CI community to share improvements, techniques and best practices
- Implement improvements identified in other GSC sites/CSOs
- Support Damco site management in improving key metrics such as quality, lean maturity, client and employee engagement, and overall process efficiency (OPE)
- Support OPEX rollout in other GSC sites
- Participate in OPEX rollout as an OPEX navigator for other Damco GSC sites
- Own one of the five OPEX lenses during an OPEX wave
- Coach at least two teams during OPEX wave through diagnostics, design and implementation phases
170
Continuous Improvement Manager Resume Examples & Samples
- Ensure teams have the needed resources, access to sponsors, and help from outside the team
- Diagnose problems and lead teams to the development of non-reversible solutions
- Through execution of lean initiatives drive performance excellence and embrace the role of a
- Excellent communication skills - written and oral; active listener; skilled at group
171
Senior Continuous Improvement Manager Resume Examples & Samples
- Execute deployments by using the available systems and by collaborate with the business units on a frequent basis
- Prioritize deployment outcome and define lean strategies for effective implementation
- Collaborate with and influence stakeholders to gain support for effective implementation
- Lead lean initiatives by example. Coach, train and develop the Continuous Improvement Managers and the site managers and co-workers on the lean principles and tools to use
- Implement mechanisms to monitor progress and evaluate roll out for their effectiveness and quality
- Ensures all project outcomes and deliverables are implemented on time, on budget, and within scope
- Track and manage post-project implementation performance including control plan audits, savings verifications, and reporting
- Drive continuous improvement activity throughout the organization
- Provide leadership to the organization through sharing of knowledge/skill and best practices
- Maintain a high-energy level and positive attitude to support continuous improvement
- Bachelor’s Degree in engineering, supply chain, operations or related field
- 10+ years of working knowledge and practical experience in a manufacturing environment
- 5+ years of working experience with CI implementation
- Master Black Belt / Black Belt certification preferred
- Demonstrated evidence of successfully leading direct reports, dotted line field reports and a proven track record in influencing front line employees, peers and Senior Leaders
- Demonstrated ability to drive and manage the change process
- Comfort with facilitating teams/groups and working with all levels in the organization
- Proficient in operating Windows and associated Microsoft Office applications, including: MS Word, Excel, PowerPoint, etc
172
Continuous Improvement Manager Resume Examples & Samples
- Normally requires a minimum of 7 years directly related project management experience
- Bachelor’s degree or an equivalent field of study
- Certified Black Belt with expertise in Lean methodologies required, Master Black Belt preferred
- Experience in a health care services (supply chain distribution or services) environment highly preferred
- Typically requires a minimum of ten (10) years of directly related and progressively responsible experience; previous experience in major process improvement and change
- Demonstrated strong leadership, interpersonal & organization skills and change agent abilities
- Strong project management skills with demonstrated track records in quality and operational improvements, ability to prioritize workload, meet deadlines, and perform multiple tasks simultaneously
- Structures approaches to resolving complex problems. Has good judgment as to most effective approach to use. Initiates needed changes in direction
- Expertise in Microsoft Office suite such as Project, Excel, Word, Visio, Access and PowerPoint
- Robust presentation skills; ability to present and discuss strategies and complex information in a manner that establishes rapport, persuades others, and gain understanding
- Ability to manage duties in a fast paced work environment
- Strong analytical skills with the ability to identify key issues and creatively overcome internal challenges or obstacles
- Expertise in using statistical software, specifically Minitab, with process improvement initiatives to analyze data, to produce reports/graphs, and monitor quality
- Influence, negotiate and resolve conflicts to reach consensus and common goals by applying a hands-on style of management and collaborating strongly with peers
- Ability to communicate effectively, both orally and in writing including the ability to communicate within cross-functional/organizational teams
- Positive, team-oriented attitude and approach to getting work done
- Ability to lead dynamically and energize multidiscipline work teams
173
Continuous Improvement Manager Resume Examples & Samples
- Liaise with diverse teams across the Business, IT, Networks resources as well as System Integrators (SI) in their execution of process changes, balancing business needs to achieve business case objectives
- Understand the OB customer and staff needs and vendor capabilities and to manage and recommend workable solutions to the business, co-ordinating business decision making where required in a timely manner
- Liaise with Business subject matter experts, Network & IT resources for the implementation
- Act as Sponsor on new capabilities and requirements into the business and business case process
- Communicate improving process capability to internal and external contact points; and
- Work with the OB Change Manager (who will be more focused on change impacts) to ensure consistent messaging is conveyed
- Tertiary qualified in an Engineering or techncial Business discipline (Post Grad in Business/Marketing advantageous)
- Several years of experience with in depth knowledge of ICT & Telco products, processes and systems
- Significantexperience with the NetCracker implementationand past history with ServiceNow experience
- Proven track record in Operations Management with strong financial & analytical skills
- Proven track record in process improvement with LEAN Six Sigma Green or Black Belthighly desirable
- Project/program management experience & relevant PMO related accreditations (eg. Agile)
- Excellent communication, negotiation, analytical and interpersonal expertise
- Decisive, focussed, strategic, tacticaland tenacious in your approach; and
- Advanced IT literacy and a knack for catering your language, style and behaviours to suit audiences at all levels
174
Continuous Improvement Manager Global Resume Examples & Samples
- Manages and provides technical leadership to the PBU CI Managers and Professionals. Provides training and development; along with input into and supports delivery of performance reviews and development plans
- Coordinate BBP Benchmark Events, Best Practices Sharing and basic Standardization regarding Process Improvements across the plants and represents as needed in the Best Practices Sharing Committees
- Directs the progress of the assigned plants in JCMS Implementation and acts as the Principle Champion for BT&S for assigned principle. This will include coaching, 2nd party assessments, acceleration events and other roles and responsibilities as defined. Achieves and maintain certification and helps to certify SME’s
- Accountable for Continuous Improvement goals and performance
- Supports and facilitates the Operations Leadership Team in improving the performance of the plants by utilizing continuous improvement methods and projects. Provides technical leadership to the teams and annual CI Roadmaps. Lead and be a Train the Trainer for Annual Hoshin style events
- Support the training programs for Operational Excellence and Leadership Staff within the BPU’s. Identifies Training needs, assist with training and coaching to successful certification. Help to identify High Potential candidates within the CI Organization
- Commits to CI plans and goals for BT&S; assist with identification of CI Savings, BBP Gap Closure, Project Tracking and Resource Utilization; manages specific research and provides analyses as requested; reports Key Process Figures to Operations and Global CI Functions and Delivers CI updates for/ at Global Management Review meetings
- Drives resolution of business process deficiencies using statistical, BBP Gap and financial justification
- Develops self through continued training, use of skills and involvement with internal & external CI organizations
- Promotes safe working conditions & practices during plant visits, initiates corrective actions or process improvements as needed
- Extensive Travel is required (75-80%)
- Six Sigma Master Black Belt
- Lean Facilitator
175
Continuous Improvement Manager Resume Examples & Samples
- Develop plant CI Implementation Strategy Manages CI resources to deliver year over year cost savings Facilitates kaizen events Implements cost savings improvement projects Implements 5S, SMED and Standard Work projects Implement corporate/plant CI systems
- Demonstrated ability to lead kaizen improvement events. Demonstrated ability to complete cost savings projects. Strong interpersonal and communication skills and ability to work in a matrix organization. Ability to lead cross-functional teams to implement cost savings programs across plant. Strong analytical skills using tools such as statistics, downtime tracking, mechanical history, project planning to identify opportunity areas. Creative in problem solving and innovative approaches to resolve complex problems. Microsoft Office skills such as PowerPoint, Project, Excel and Word. Ability to quickly come up to speed on complex production processes and work with others to identify opportunities areas via data. Ability to teach/coach CI concepts throughout the plant
- Has worked in a lean manufacturing environment. Solid systems understanding and ability to identify improvements needed. Hands on style and solid communication ability. Able to effectively interface within all levels of the organization. Ability to work with minimal direct supervision, in a fast-paced, dynamic environment
- 5+ years of lean experience in a complex manufacturing environment. Past experience in leading kaizen workshops in the areas of 5S, standard work, visual management, daily management, SMED and OEE gap closure. 6 Sigma certification preferred. Food manufacturing experience preferred Maintenance/manufacturing/engineering/QA/QS experience preferred
176
Continuous Improvement Manager Resume Examples & Samples
- A bachelor degree is mandatory, master/diploma preferred
- At least one year experience in logistics or production environments
- Practical Lean Management / Continuous Improvement experience - experience in training teams, leading Kaizen and lean projects and delivering results through implementation of changes
- First experience in Change Management
- Excellent communication skills (written and verbal) in English and German
- Able to motivate, lead, speak to and listen to Associates as well as to the Senior Management
- Lean or Kaizen Certificate
177
Continuous Improvement Manager Resume Examples & Samples
- Participate in planning and improvement activities to close the gaps
- Work with leadership to identify and prioritize improvement initiatives using ACE
- Lead cross-functional teams through Lean, Continuous and Process Improvement efforts to drive KPI (Key Process Indicators) in quality, delivery, and cost through the application of ACE tools
- Lead the ACE Council/Guidance Management Team, support organizational development, monitor yearly KPI, and set goals for the site
- Lead a team of 4 hourly direct reports to drive ACE within the organization
- Organizational agility and ability to influence leadership and employees across all levels of the organization
- Must have intermediate to advanced computer skills, and be able to operate various software programs, such as MS Word, Excel, PowerPoint, Outlook, etc
- Industry recognized certification in lean, six sigma or similar discipline or equivalent experience
- Once in the role, UTC ACE Associate certification must be achieved
178
Continuous Improvement Manager Resume Examples & Samples
- BSME and MBA
- 10 years of professional experience, with a minimum of 5 years managing people
- Must have technical knowledge of CI methodologies and be able to demonstrate problem solving, planning and project management skills
- Previous experience in extrusion, thermoset, and/or injection molding technologies
- Knowledge of robotic design and application
- Must be able to excel in a team environment. They must demonstrate excellent interpersonal skills and be able to effectively communicate with and build strong working relationships with individuals and teams at all levels of the organization
179
Continuous Improvement Manager Resume Examples & Samples
- Lead, develop, and support Plant Continuous Improvement Leaders (CILs) during certification training and with daily job responsibilities
- Partner with plant teams to eliminate waste, reduce process variation, and reduce operation costs through the application of Continuous Improvement tools
- Partner with the appropriate teams to gain agreement on value-added focal areas for the plants
- Assist in recruiting and training Green and Black Belt learners; support them in project selection, execution and sustainment
- Facilitate best practice sharing from Lean Six Sigma projects. Serve as liaison between plants and the Best Practice committee. Encourage plants to submit ideas for Best Practices
- Work with plants to support and monitor the Total Process Control (TPC) Master Schedule. Work with non-TPC plants to support and develop glide paths and actions plans, and monitor reliability metrics
- Provide engineering project Vertical Start-Up (VSU) guidance related to Continuous Improvement and goal achievement
- Provide leadership and direction for Kroger DownTime (KDT)
- Direct improvements and standards as defined in appropriate documentation. Ensure proper application of software. Encourage and support integration of new features
- Provide feedback and recognition at all levels of the plant and General Office
- Drive changeover time reduction to improve productivity
- Work with internal and external consultants to drive implementation of the Continuous Improvement efforts
- Bachelor's Degree in Engineering, LEAN Manufacturing, or related field
- 5+ years of experience in plant engineering or LEAN Manufacturing
- Certified Six Sigma Black Belt or Master Black Belt
- Able to import raw data, utilize templates & tools, and develop the appropriate action plans
- Demonstrated competence in materials/training methods
- Able to read and understand complex materials & impart it to others
- Manufacturing operational background and/or experience
180
Continuous Improvement Manager Resume Examples & Samples
- In depth knowledge and practical experience of DMAIC methodologies
- Managing 3rd party supplier relationships
- Building a strong internal network of colleagues at all levels in commercial and operational teams
- Issue Resolution/Process Improvement - ability to build trusted relationships
- Negotiation and conflict resolution
- Ability to deal with conflicting priorities
181
Continuous Improvement Manager Resume Examples & Samples
- Develop and maintain Continuous Improvement programs including Total Preventive
- Bachelor’s degree in business, engineering, or related field; 8 years of lean manufacturing
- 5 years manufacturing experience with 3 years in manufacturing processes and/or training
- 3 years lean manufacturing systems and continuous improvement experience
- Six Sigma Green Belt Certification or comparable problem solving certification
- Demonstrated successful ability to build positive partnerships and work collaboratively with
- Demonstrated successful ability to organize and prioritize work to ensure timely deadlines
- Excellent interpersonal and communication skills with the ability to interact with all levels of
- Six Sigma Black Belt Certification or comparable problem solving certification
- Knowledge of Management Systems including health and safety, environmental, quality and
182
Continuous Improvement Manager Resume Examples & Samples
- Volume, Revenue, OC
- Develop efficient distribution networks to support RTM
- Manage and control all logistics costs (ensure product availability at the right time, in the right quantity at lowest possible cost)
- Establish and track KPI’s (CFR, CTS, OTD, OSC, Inventory Accuracy, Product Damage, Warehouse Waste, Warehouse Capacity, Picking Accuracy)
- Forecasting & Replenishment
- Ensure resource availability to fulfill the expected customer orders and execution of replenishment plans
- Communicate logistics capabilities and limitations to CS & PS
- Constantly track and monitor inventory movements (RDC)
- Product Change Management
- Provide technical inputs (storage, handling, distribution) on PCM projects
- Provide relevant input during evaluation phase for product performance
- Warehousing, Transportation & Co-packing
- Cultivates relations with 3PL to ensure that our needs, objectives and standards are met
- Responsible for managing the physical flow of products through the effective use of labor and available systems
- Challenges the cost basis and establishes productivity studies
- Accountable for warehousing and transportation capacities at all time to ensure highest CFR at lowest possible cost
- Ensures compliance to QPE and related product traceability processes
- Assesses current distribution network effectiveness and redesign as needed to meet business requirements
- Ensure compliance to logistics procurement process (bidding) to ensure the selection of the best 3PL at the lowest cost
- Develop and manage co-packing operations
- Develop process for product destruction (warehouse waste and trade returns)
- Maintain a knowledge base of alternate 3PLs within the marketplace for contingency planning (naturally disasters, labour issues, etc.)
- Manage warehousing and transportation capabilities based on planned volume, product attributes, and apply the proper GWP requirements
- Order & Customer Supply Management
- Assists in managing Customer expectations by providing Customer Service with detailed information about inventories, co-packing data and delivery status
- Responsible for timely delivery to Customers
- Establish and agree with Customer delivery requirements
- Develop prioritization criteria for stock reservation and picking
- Assist in developing appropriate KPI’s for distributor score-carding and selection (focusing on warehousing and transportation)
- Work with Distributors to implement GWP
- Ensure distribution capabilities to support short and long term RTM strategies
- Maintain Knowledge of distributors’ warehousing and transportation capabilities to support volume growth
- Customer Service Finance
- Deliver the orders completely so that no payment delay excuse from order quantity mismatching
- Effectively share goals and objectives across the organization
- Select and develop people through effective competency development, new hire acclimation, coaching, and advancement planning
- Ensure the appropriate organization structure is in place to ensure work force optimization
- Accurately assess people and effectively communicate strengths and opportunities
- Actively participate in the development and delivery of effective training
- Ensure that the team acts with the highest degree of integrity and equally complies 100% to the corporate policies on compliance
- Ensure that each team member gets the appropriate training and coaching
183
CS Senior Continuous Improvement Manager Resume Examples & Samples
- Provide Strategic vision for the ACES program by identifying and prioritizing where and how we adapt and invest
- Act as an internal resource for the principles of lean and process excellence working closely with corporate partners on network solutions
- Drive the creation of Standard Work quality initiatives specific to the needs of the business teams and regions to meet and exceed Business Plans
- Review and analyze customer defect data with development of corresponding countermeasures
- Gain consensus to push change forward while keeping variation between sites to a minimum
- Establish a partnership with senior business leaders to develop and lead the continuous improvement strategy across multiple global sites
- Collaborate and communicate with other global ACES leaders on best practices, internal and external benchmarking, talent development, programs of study and knowledge sharing
- 7+ years’ experience in project management and facilitation of process improvement initiatives across business operations and technology
- 5+ years’ experience instructing executives, managers, and associates on Lean methodologies
- Facilitation experience at all levels of the organization and to audiences of all sizes
- 10+ years of leadership experience in project management
- Applied knowledge of measurement, statistics and program evaluation
- Demonstrated working knowledge of LEAN/Six Sigma principles, rules, systems and tools with experience supporting improvement activity and workshops through consulting, coaching, training and facilitation as required in a highly customer centric environment
184
Continuous Improvement Manager Resume Examples & Samples
- Minimum of 5 years working experience working in manufacturing or other related industry
- Knowledge of CI / Lean / TPM tools required
- Knowledge of principles and methods for process improvement
- Excellent multi-tasking, organization, and time-management skills
185
Continuous Improvement Manager Resume Examples & Samples
- Responsible for the successful delivery, adoption and support of Continuous Improvement Initiatives in line with the BUK Automation Strategy and Customer Journey Framework
- Provide leadership and support for a team of Continuous Improvement Analysts in order to deliver initiatives in line with Barclays UK Truly Connected Finance strategy
- To initiate, formulate and present recommendations, based on analysis, in order to influence the decisions of Senior Stakeholders across Barclays UK
- Interacts and communicates with a wide variety and sometimes complex, stakeholder groups in an efficient and effective manner
- Collaborative working across all channels in BUK to include (and not limited to) technology, CI and frontline colleagues to ensure successful and consistent delivery of change with minimal training
- A recognised Project Management or Business Analysis Foundation level qualification is preferred but not essential
- Experienced in Project Management or Business Analysis
- Skilled in the use of documentation and presentation software tools e.g.: MSWord and PowerPoint
- Skilled in the use of Operational modelling tools e.g.: Blueworks or Visio for the production of business operational designs
- Have a good level of understanding and knowledge of Barclays technology systems
186
Continuous Improvement Manager Resume Examples & Samples
- Act as advisor to both manufacturing and engineering teams regarding regulations that affect the design, construction and installation of plant facilities equipment as it relates to continuous improvement
- Champion lean manufacturing principles by continuously improving standards assuring principles are adhered to throughout Knoll. Expanding on principle knowledge by utilizing appropriate documentation and visual aids (i.e., standardized work, combination tables, Kanban tickets, hejunka tags, etc.)
- Assist and coordinate product launches with both Product and Manufacturing Engineering, Quality and Production teams to assure process capability. Also, responsible for assuring generic equipment design and optimum work balance is in place prior to program launches
- Assure the integrity of manufacturing process by developing checks, controls and method triggers that eliminate process deviations
- Member of both Leadership and Manufacturing teams assisting with ongoing development, communication and implementation of programs and policies. Fostering team cohesiveness related to team direction, annual planning, budgets, policy changes etc
- Identify and address any areas of non-cohesiveness, working with team leadership to resolve all issues effecting goals
- Must be a strategic thinker with the ability to identify waste and understand and thrive in data driven environment
- Must be results oriented, customer focused, have high energy, self-motivated and analytical
- 10+plus years continuous improvement experience
- Advanced Six Sigma knowledge and ability to train and lead others in its implementation (minimum Green Belt certification)
- Leadership in Health and Safety preferred
- Ability to train and motivate others
- Strong PC skills Excel, PowerPoint, Word, Minitab and Microsoft Project
- Ability to understand and take into account the entire business process from order entry through customer delivery installation
- Kaizen
- Value Stream Mapping
- Poke-yoke
- Demand Flow Technology
187
Continuous Improvement Manager Resume Examples & Samples
- Manage Quality and Continuous Improvement
- Coach and train direct reports and plant leaders in lean manufacturing and problem-solving principles
- Develop and write sequence of operations as well as time estimates for each operation specification
- Assists in maintaining bills of material for all machine components and parts
- Champion MasterBrand Production System strategy and provide hands-on support and any necessary training during implementation
- Coordinates prototype drawings for products or processes with necessary support personnel
- Responsible for the maintenance, distribution and accuracy of all production and post production engineering drawings
- Coordinate the implementation of engineering change order requests for all related departments
- Provide technical support with corporate IT for hardware & other IT coordination
- Exceptional leadership, and both verbal and written communication skills
- Demonstrated ability to deliver training to large groups
- Experience with change management principles and demonstrated ability to drive and manage the change process
- Minimum of 5 years experience in various manufacturing/operations roles, including supervision
188
Quality & Continuous Improvement Manager Resume Examples & Samples
- Ability to type 45 WPM
- Good communications and writing skills
- Tasks and Project Management
- Diploma in Hospitality
- 1 years of hospitality experience, or an equivalent combination of education and experience
189
Continuous Improvement Manager Resume Examples & Samples
- Key function for OPEX savings (average 1Mio€ p.a.)
- Key for CI&Technology, CI function
- Lead of Six Sigma and Lean Projects
- Discover Six Sigma Projects and saving opportunities
- Coordination/ development / project support of Black Belts and Green Belts
- Training of new Black Belts and Green Beltss
- Implementation of Catalent Production System – Six Sigma
190
Continuous Improvement Manager Resume Examples & Samples
- Deliver cost productivity improvements by managing project deck focused on cost productivity, sourcing and VA/VE
- Accountable for managing projects that will deliver savings, determined annually
- Lead, facilitate and execute projects using Six Sigma and lean principles and processes to deliver results
- Responsible for deploying Six Sigma and lean principles and processes across the site
- Works directly with the Operations leadership to facilitate setting priorities, developing goals and designing objectives related to Six Sigma and lean
- Tie Six Sigma projects and lean transformational plans to the site’s operating goals and objectives
- Train and coach process owners in the use of lean and statistical tools, approaches and techniques to create process management and measurement systems and develop an operational excellence mindset at the department level
- Support lean cultural change
- Interface with manufacturing personnel to improve existing processes, increase safety and solve any ergonomic concerns
- Provide technical support to shop floor in the areas of equipment, layout, tools, fixtures and machines to ensure low-cost and high-quality products
- Implement the manufacture of new products or product lines with the emphasis on integrating the most efficient process and repeatable design
- Develop proposals to incorporate new technology where appropriate
- Prepare capital expenditure requests, frequent interaction with outside suppliers and agencies, including regulatory personnel
- Minimum 3 years of prior manufacturing experience
- Must be authorized to work in the United States without company sponsorship
191
Continuous Improvement Manager Resume Examples & Samples
- Deliver defined projects for Area Operations functional excellence activities
- Coordinate and review all Operations functional excellence activities in Area
- Drive Area implementation of best practices from fragmentation to scalable knowledge
- Develop change management strategies and plan with particular emphasis on a process oriented approach
- Sustain CI deployment and maturity in CSO’s
- Area coordination of continuous improvement
- Coach Area Leadership Team on CI sustainability and Lean behaviors
192
Continuous Improvement Manager Resume Examples & Samples
- Champions a culture of inclusion and accountability by leveraging employees at all levels of the organization in the development and troubleshooting of quality manufacturing processes
- Develops the Bethel plant’s long term strategic plan for Continuous Improvement. Sets short and long term objectives to achieve strategic plan. Communicates organization’s vision of effectively in verbal, written, and presentation form
- Leads production and functional teams in the monitoring and improvement of processes to ensure the highest quality product by utilizing EQS, ELSS, and other Eaton and industry best practices
- Facilitates improvement activities including training, mentoring, facilitating Kaizen events, Six Sigma projects, tool deployment, benchmarking, etc
- Conducts or supports various internal and external assessments (e.g. ELSS, OpA, MESH, AS9100, Production Rate Readiness). Works across functions to prioritize improvement activities and close identified gaps
- Facilitates the annual organizational objective planning process using EBS Pull methodology
- Minimum 3 years of manufacturing experience utilizing Continuous Improvement methodologies
- This position requires use of information or access to hardware which is subject to the International Traffic in Arms Regulation (ITAR). All applicants must be U.S. persons within the meaning of ITAR. ITAR defines a U.S. person as a U.S. Citizen, U.S. Permanent Resident (i.e. ‘Green Card Holder’), Political Asylee, or Refugee
- Minimum 5 years of manufacturing experience utilizing Continuous Improvement methodologies
- Experience leading Continuous Improvement/Lean initiatives
- Six sigma certification
193
Continuous Improvement Manager Resume Examples & Samples
- An Engineering degree in a relevant field or similar
- At least 5-7 years of experience in Manufacturing Management
- LEAN Black Belt certification a preferred plus
- The drive to challenge change
- Experience in Management of a team and projects
- Communicator, team player and a true leader
194
Continuous Improvement Manager Resume Examples & Samples
- CI Manager is a practitioner, coach, teacher, trainer and consultant supporting the Site Steering Committee and Employee Involvement teams
- CI Manager works to involve everyone in the pursuit of sustained beneficial change
- Lean Enterprise training workshops
- Identifies and drives continuous improvement opportunities from concept to completion
- Implements train-the-trainer approach and rapid, sustained implementation through learn-by-doing methods
- Facilitates improvement implementation through
- Engineering / manufacturing experience and conversant with the tools and processes necessary for the implementation of lean practices. May include, but not limited to Practical Problem Solving, Kaizen, 5s, Toyota Production System, Six Sigma
- A track record of personal involvement in continuous improvement initiatives
- Experience in operating with a company that has already adopted the lean philosophy, preferably extending into office areas
- Project management, and proficiency in oral and written communication
- Change management, acting as a role model in coaching and championing change
- Interacts effectively at all levels of the organisation to “get things done”
- Fosters open communication, values learning and builds employee effectiveness
- Trains others and promotes facilitation and leadership skills
- Computer literate, including Microsoft Office and Business system awareness (preferably SAP)
- Knowledge of operational and functional best practice
- Quick to learn with excellent analytical, diagnostic organisational and planning skills
- Able to work exceptionally well in team environments and build teams
- Envisions the future
- Demonstrates Customer focus
- Health and safety awareness
- Able to take measured risks
- Self-reliance and a drive to succeed and motivate others
- Discipline, focus and ability to see beyond temporary set-backs
- Able to listen, challenge and communicate
- Drives for excellence, aligned to business results
195
Continuous Improvement Manager Resume Examples & Samples
- Bachelor degree is required; Preferably in Mechanical or Electrical Engineering or related discipline
- Production supervision experience preferred
- Black Belt Certification Required
196
Continuous Improvement Manager Resume Examples & Samples
- Bachelor’s degree in Business, Engineering or related
- Minimum 7+ years of relevant experience; demonstrated leadership and management experience with an understanding of the dynamics of interpersonal relationships
- Experience creating and executing Continuous Improvement activities that drive organizational results and change
- Formal training in Change Management, Continuous Improvement (i.e., Lean, Six Sigma, Kaizan, Workout), Performance Management
- Microsoft MS Office Suite, Minitab and familiarity with plant operations software (i.e., PI, OIS and MOIS) and statistical analysis software
- Very strong communication, interpersonal, and influencing skills (without authority), with ability to use fact-based and well-thought-out arguments to challenge all levels or change behavior/techniques as required
- Ability to hold performance dialogues and identify root-causes of problems with all levels of the organizations. Drives to actionable outcomes and follows up on results
- Proficiency in training, communication, presentations skills and development of materials
- Employment is subject to successfully completing Mosaic's pre-employment checks including criminal, drug and alcohol testing
197
Continuous Improvement Manager Resume Examples & Samples
- As an expert in the use of the Lean tools with a comprehensive knowledge of the philosophy, utilize PDCA (Plan-Do-Check-Act) and DMAIC (Define-Measure-Analyze-Improve-Control) methodologies to successfully lead and manage completion of continuous improvement projects within a given timeframe to meet the department or facility goals in productivity, quality, efficiency, and safety (40%)
- Lead exempt and non-exempt employees assigned to CI teams in LEAN disciplines and processes to accomplish assigned stated CI projects. Responsible and accountable for CI team meeting or exceeding project goals (20%)
- Apply E3 concept (Engage, Enable, Empower) within project activities to ensure project sustainability with the work force and management teams. (10%)
- Identify LEAN/CI needs of assigned departmetns including but not limited to Manufacturing, Distribution, Tech Services, Warehouse, Office, and others, and develop implementation plans with department and CI directors. (10%)
- Provide monthly report out to Process Improvement Director on completed projects and assist in presentation to plant manager and other leaders as required (10%)
- Minimum of five (5) years related experience
- LEAN certification/Six Sigma training or comparable required
- Professional communication skills and proven leadership capabilities
198
Continuous Improvement Manager, Montreal QC Resume Examples & Samples
- Develop continuous improvement – lean manufacturing and Six Sigma methodologies in the day to day operations
- Facilitate process improvement teams and provide counsel and assistance to the project team leaders with respect to facilitation techniques, quality systems, continual improvement, people development and safety improvement
- Assist in the facilitation of Manufacturing Fundamentals and other, similar, key programs
- Lead workshops resulting in tangible key performance indicator improvements
- Contribute to strategic planning at the plant level
- Ensure through audits that tools are appropriately and effectively used
- Develop and maintain the site’s annual 12-months rolling lean implementation plan based on the strategic plan
- Develop, manage, and report progress of the lean deployment plan with site management (based on current and future state Value Stream Maps, site performance improvement targets, and Group / Business standards, policies and best practices)
- Ensure Lean and Six Sigma principles are appropriately taken into consideration at all stages of the process improvement project
- Understand all environmental policies and significant environmental impact of job activities
- Understand all safety policies and significant safety impact of job activities
- Assist leadership in the planning, development, coordination, support, and execution of high impact (immediate and long term) improvement plans for effective and sustainable cost saving initiatives while making sure lean manufacturing and Six Sigma initiatives are aligned with customer focused metrics
- Serve as a business change agent leading process improvement initiatives, process redesign activities/projects which will enable the organization to reach the next level of world class operations by implementing continuous improvement-lean manufacturing practices throughout the plant
- Work with local financial representative to validate project justification and success when necessary
- Minimum three years of project facilitation experience
- Lean deployment experience preferred
- Six Sigma Green Belt certification required and Black Belt preferred
- Clear practical and hands-on orientation
- Strategic thinker, with clear vision and direction of change management
- Strong facilitation and interpersonal communication
- Proven ability to coach, mentor, and energize team members
- Deployment of a lean culture: organization, policy deployment, management routines, management control, behavior and visual management
- A demonstrated understanding of Lean principles such as Value Stream Mapping, Just-In-Time, Demand Flow, Single Piece Flow, Continuous Improvement Process, Kaizen, SPC, Six Sigma and Communication Tools, and Statistical Problem Solving
- Thorough understanding of lean tools such as standardized work, 5S, SMED, TPM, Kanban, MIFA, Error Proofing etc
- Thorough understanding of the DMAIC methodology Analytical skills including key statistical methods commonly used in Six Sigma
199
Continuous Improvement Manager Resume Examples & Samples
- Work with various stakeholders to identify and prioritize Continuous Improvement initiatives
- Responsible for Continuous Improvement governance, including ongoing stakeholder management
- Project manage Continuous Improvement initiatives and ensure that that planned benefits are realized and that projects are implemented on time and within budget
- Contributes to CI ideas identification, assessment and execution
- Drives productivity discussion journey setting up priorities, tools and initiatives
- Help drive a culture of change and continuous improvement through providing with CI standards, tools, methodologies and best practices
- Help drive CI training Programme conducting trainings/workshops/ideation events for different groups of employees
- Help drive CI communication plan execution
- Bachelor’s degree in Finance or Business Management
- Total years of experience 5+
- 3+ years’ experience in developing and executing in Transformation / Process Improvement Projects
- Experienced in Finance/Procurement/HR Operations
- Wide range of method skills and practical experience, especially on continuous improvement, project management and change management (e.g. Lean Six sigma, Process mapping, Problem Solving etc.)
- Ability to develop CI training materials and to lead CI training workshops independently
- Strong analytical skills, being able to translate operational issues into workable solutions, able to dive deep whilst seeing the big picture
- Developed consultative communication skills
- Microsoft Office Advanced user (especially MS Excel and MS PowerPoint)
200
Continuous Improvement Manager Resume Examples & Samples
- Supporting the management of all service delivery in accordance with regulatory and statutory obligations, championing and ensuring compliance with all Health and Safety, security and environmental standards and policies
- Developing strong relationships with the Employer and key stakeholders to optimise continuous improvement opportunities across the contract, focusing particularly on the customer and project objectives
- Leading and driving continuous improvement and operational excellence activity across the contract with a forward looking approach
- Engaging the wider team, the Employer and all stakeholders and leading the identification, development and implementation of improvement and innovation initiatives which improve our service offering to the Employer and the Estate Users
- Interpreting the findings and feedback gathered from a variety of sources into clear, concise and logical conclusions and recommendations which will assist the management team in identifying areas for business and service development
- Documenting activities, benefits and successes and measuring improvements across the spectrum from customer service to financial improvement
- Keeping abreast of industry thinking and techniques and reflecting this in the technology, processes, products and services offered to contract and the Employer
- Contributing to the development of continuous improvement and innovative skills across the contract
- Analysing and considering ideas for improvement in sphere of responsibility and across the contract in general
- Promoting sound waste management practices across the estate
- Championing and ensuring compliance behaviours and positive attitudes with regards to all Health and Safety, security and environmental standards and policies
- Developing and maintaining good working relationships with key stakeholders
- As a member of the management team acting as a role model for continuous improvement activity and processes ensuring they are followed to clarify objectives, actively managing performance and developing skills
- Creating an environment in which teams and individuals can perform at their best, improving performance and realise their full potential
- Encouraging and developing teams to innovate and improve their performance and delivery
- Complying with the Company’s Equality and Diversity and other people policies
- Understanding the contract deliverables and identifying ways in which to maximise performance and delivery
- Contributing to change processes with the intent of contract and service improvement
- Understanding the impacts and benefits continuous improvement initiatives can have on the contract and service delivery
- Managing budgets relating to continuous improvement initiatives and opportunities
- Contributing to the achievement of sustainability objectives through personal behaviour and adapting working practices where required
- Demonstrable track record in continuous improvement and operational excellence
- Flexibility to travel extensively between sites
201
Continuous Improvement Manager Resume Examples & Samples
- B.S.in Engineering or related technical discipline
- 3+ years process improvement experience using Lean methodologies
- Must be a US Person and able to hold a US Government Secret Clearance
- Trained in Lean tools and techniques including value stream mapping
- Strong Change Management skills
- Demonstrated portfolio of lean improvements with quantifiable results
- Strong written, verbal and presentation communication skills are required to include the ability to effectively interact and persuade all levels of Management and Staff
- Experience working on projects in which there are often "blurred" lines of responsibility
- Experience and or knowledge of how to effectively work in a matrixed organization
- Advanced skills in MS Office
- Demonstrated Experience with change management and stakeholder management
202
Continuous Improvement Manager Resume Examples & Samples
- An ability to train and motivate others
- The ability to attain results through the facilitation of teams and individuals
- A customer focused approach to improvement
- Strong PC skills Excel, Powerpoint, Word, Minitab, Microsoft Project, etc
- The ability to understand and take into account the entire business process from order entry through customer delivery and installation
- High initiative
- Safety-first attitude
- Data-driven
- Ability to “see the waste” in an organization
- Significant experience in a high paced manufacturing environment implementing rapid and continuous improvements with a high rate of success
- 5 – 7 years’ relevant experience
- A working knowledge of lean tools and principles
- Value stream mapping
- Poka-yoke
- Ideally advanced six sigma knowledge and the ability to train and lead others in its implementation (minimum Green Belt certification)
203
Continuous Improvement Manager Resume Examples & Samples
- Develop and execute CI strategies and activities for specific customers/sites. Challenges include meeting expectations in delivering results, considering alternative courses of actions, making timely decisions and developing greater communication skills
- Develop and maintain effective partner relationship with major customers, dealers and Cat region (SPM) in order to achieve the CI objectives and targets
- Establish high-level relationships with business decision makers and identify business needs and problems. Provide input to customer’s operation and systems
- Achieving alignment of various parties at Caterpillar, dealers and key end-user personnel
- Providing a clear vision for success and drive high levels of CI execution to achieve our commitments through your deep subject matter expertise in equipment management, production optimization, safety, sustainability
- Partnering with dealer personnel to direct the day-to-day activity related to contractual commitments at each site
- Successfully delivering on all areas of contractual commitments by utilizing a complete understanding of Caterpillar and Dealer Capability
- Working with Caterpillar Product Groups and other internal Business Units to completely understand the technical and operational capabilities of our equipment, technology, and services
- Creating innovate new value-added capabilities to improve site operations and equipment maintenance
- Initiate and manage job studies to develop production data and M&R Projects. Assess the need and suitability of analysis & application tools like FPC (Fleet Production software) & SAT
- Must have the ability to work with people from many different backgrounds and cultures, internally and externally, with the appropriate influence and ability to resolve differences
- Good human relations skills are required to develop a collaborative/cooperative work relationship with others inside and outside the business unit
- Must have the ability to work and set priorities for self and for the work team without day-to-day direct supervision
- Enhancing use of Caterpillar systems and developing leadership abilities
- The position manages the completion of its own work assignments and coordinates work with others. To plan, monitor and control all aspects of the project
- A bachelor’s degree or international equivalent
- Extensive job related experience
- Prior experience in field assignments
- Knowledge of Caterpillar products, policies, and procedures
- Knowledge of 6 sigma and project management tools
- Demonstrated ability to work independently, communicate effectively with others in the work group, dealer personnel and customers
- Demonstrated deep subject matter expertise and experience in the management of equipment (operation & Maintenance)
204
ABS & Continuous Improvement Manager Resume Examples & Samples
- Work with location leadership to drive continuous improvement activities and waste elimination: Identify, propose & implement new productivity improvements
- Facilitate successful kaizen and rapid improvement process events with both internal and external consultants, customers and suppliers, with a major emphasis on locally focused improvement. Provide the support all follow-through required to sustain the improvements established during the events
- Coordinate and deliver team-based and ABS training to support enhanced organizational performance through imparting a thorough knowledge of team and ABS concepts, principles, and practices
- Facilitate, review and aid locations in developing Hoshin plans
- Act as internal consultant and catalyst to assist individuals and teams in the application of ABS principles and techniques to improve operations. May provide external consulting services to other company or supplier operations
- Coach and support leadership at all levels in meeting business improvement metrics through the application of ABS methods and techniques. Establish reporting methods to track progress and communication processes to inform the organization of results and opportunities
- Facilitate consistent, uniform approaches for visual controls and productivity measurements to be utilized throughout product teams and the factory
- Assist team leaders in team skill and knowledge development to support meeting management goals, project management, improvements, results measurements, problem solving, and related team skills
- Provide overall guidance and consultation focusing on the perfection of ABS techniques. Identify opportunities for improvements, continually evaluate results, and sustain performance gains
- Ensure that all work activities are performed in accordance with established safety and environmental standards
- Maintain full compliance with Company policies and procedures and conducts all activities in accordance with the Arconic Guide to Business Conduct
- Demonstrate a knowledge of, and commitment to, ABS manufacturing principles and techniques
- Bachelor’s degree from an accredited institution in Engineering, or Business
- Minimum of 3 years’ experience in manufacturing work environment
- This position requires use of information or access to or use of information which is subject to the International Traffic in Arms Regulations (ITAR). All applicants must be U.S. persons within the meaning of ITAR. ITAR defines a U.S. person as a U.S. Citizen, U.S. Permanent Resident (i.e. Green Card Holder), Political Asylee, or Refugee
- Highly structured and formal education and training in ABS or Lean Manufacturing preferred. A technical degree is preferred
- 8 years of manufacturing experience preferred
- Arconic ABS certification Level 2 or completion within 18 months of role
- Thorough knowledge of lean manufacturing and rapid improvement techniques
205
Continuous Improvement Manager Resume Examples & Samples
- 2-5 years’ experience in the application of lean tools and principles
- Six Sigma Black Belt preferred
- Able to drive and lead change
- Ability to teach, coach and mentor lean tools
- Financial acumen desired
- Requires outstanding interpersonal skills and ability to work cooperatively with all employees and managers
- Functional knowledge of business processes, manufacturing and transactional
- Experience in proposing and implementation of time study/labor management initiatives
- Ability to demonstrate results using problem solving skills. Working knowledge of design tools such as Design of Experiments (DOE) and Failure Mode and Effects Analysis (FMEA)
- Experience in managing projects from proposal through implementation and evaluation; Formal Project Management Certification/Degree preferred
206
Continuous Improvement Manager Resume Examples & Samples
- May supervise a team of up to 10 indirect reports and 3 direct reports
- Complexity: High. Requires the successful execution of business plans by leading through influence instead of direct authority. Coaching skills and lean tools will be utilized daily
- Other: Cross functional responsibility for ensuring improvement activities are undertaken with a lean approach considering the process integration and technical issues that may be impacted
- Two hundred fifty thousand dollars annual budgetary responsibility (approximate)
- Serve as a Lean Coach/ Mentor
- Responsible for the lean and soft skill development of plant CI resources
- Coordinate improvement activities across multiple manufacturing sites and business offices
- Manage Centralized CI Office business support services
- Responsibility for training curriculum and content development
- Assist in strategic planning for development of Centralized CI Office
- Assist in planning and executing annual cross-company CI Summit
- Actively participate in your own development opportunity identification and propose activities and events for skill improvement
- Bachelor’s degree required; an engineering degree is preferred
- Minimum 8 years’ experience implementing lean tools in manufacturing or office environments
- Increasing levels of responsibility over the course of their career
- Demonstrated ability to lead a team, document improvement results, and effectively communicate those results
- Lean/Six-sigma certifications are a plus, but not required
- Coaching certification is a plus, but not required
- Must be willing and able to travel a minimum of 25-30% of work time
- In lieu of a cover letter, please submit documentation of a Kaizen event that you have led. It should include a business case for the event, photos of before/after changes, a summary of the activities, and the final impact on the business
207
Continuous Improvement Manager Resume Examples & Samples
- Bachelor’s degree in Business, or related field preferred
- 3-5 years experience in quality, or equivalent experience
- HACCP and SQF certification
- Six Sigma experience a plus
- Ability to lead and direct others
- Proficient with MicroSoft Office, Outlook ,and internet research skills
- Minimal Travel required
208
Continuous Improvement Manager Resume Examples & Samples
- Deploy the appropriate People / Safety / Quality / Cost / Delivery / Productivity metrics and management routines at all levels of the organization
- Act as a change agent (leader) to instill a Problem Solving and Continuous Improvement culture on site and in related areas of the company
- Support site management in its strategic planning process and its implementation by taking ownership of relevant projects, that are a subset of the core responsibilities, and by taking a leading role in other programs; e.g. Manufacturing Fundamentals
- Contribute to the Continuous Improvement network development. Ensure 2-way communication throughout the continuous improvement organization. This includes communicating project status and coordinating activities between the Regional Continuous Improvement leader and other Continuous Improvement leaders. Also, this includes capturing project lessons learned and submitting activity reports
- Promote the use of metrics and data to drive project focus
- Bachelor’s degree (Business or Engineering preferred)
- Strong analytical and problem solving skills; knowledge and ability to train on methodologies at all levels of the organization
- Thorough understanding of lean tools such as standardized work, 5S, SMED, TPM, Kanban, MIFA, Error Proofing and etc